Hi folks – back in 2020, I wrote about buying a Mophorn 3 ton pneumatic/air- pillow jack to work on our vehicles. Actually, I bought it in 2019 and it’s still going strong. This past Fall, I decided to get a second air bag jack but decided to get one with a higher lift capacity to better jack up my 2021 Ram 2500.
To give some background, I wanted an air-pillow/air-bag lift for speed and to save my shoulders that could no longer handle pumping a hydraulic jack arm over and over to lift a vehicle. I have an air-over-hydraulic bottle jack but it is tall and slow. The air bag jacks use compressed air to inflate a rubber cylinder that then lifts the vehicle – like what you see in air-ride or air-lift suspensions on trucks. They are called by a variety of names as you can see in this post: pneumatic jacks, air bag jacks, air pllow jacks, pillow lift jacks. Air-over-hydraulic is a different creature – air is used to actuate the hydraulic pump vs. you hand pumping to move the hydraulic pump up.
Always Use Jack Stands
Once the vehicle is in the air, I always put jack stands all the way around to support it. This is always a good idea regardless of jack type you use and the air bag jacks are no different.
Vevor 11,023 Pound Jack
I did some of my usual digging on Amazon and tool sights and decided to get a Vevor 11,000 pound air jack. I bought it in September 2022 and started using it right away because it’s really speeds things up to be able to lift both ends of a vehicle without repositioning the jacks.
There was one thing in their product page on Amazon that confused me until I realized it was a metric term. They say it can lift 11,023 pounds / 5 tons. Well, being used to American measures, 5 tons if 10,000 pounds soI wondered if this was some kind of hype. The issue is that they mean 5 metric tons. A metric ton is 1,000 KG or 2,204.6 so 5 metric tons is 11,023 pounds.
Their stated operating air pressure range is 5-10 kg/cm^2. That comes out to 71.1 to 142.2 PSI. The airline for my driveway tools is at 100 PSI – most of my tools are 90 PSI. My guess is that given their operating range, the jack can’t lift its rated maximum capacity. I can tell you that it has no problem lifting the front or rear of either my 6.7L Hemi 2021 Ram 2500 or full size 2016 Ford Transit F150 van and that’s really what I wanted. The photo at the top of the blog is the Vevor with my Ram 2500 up in the air.
The lifting height is about 15.75″ and the minimum height is 5.3″. The minimum matters a lot when you are trying to get it under some vehicles. One trick I have found is to stand on the air bag to get the air out and then close the exhaust valve to make it thin enough to slide under some cars.
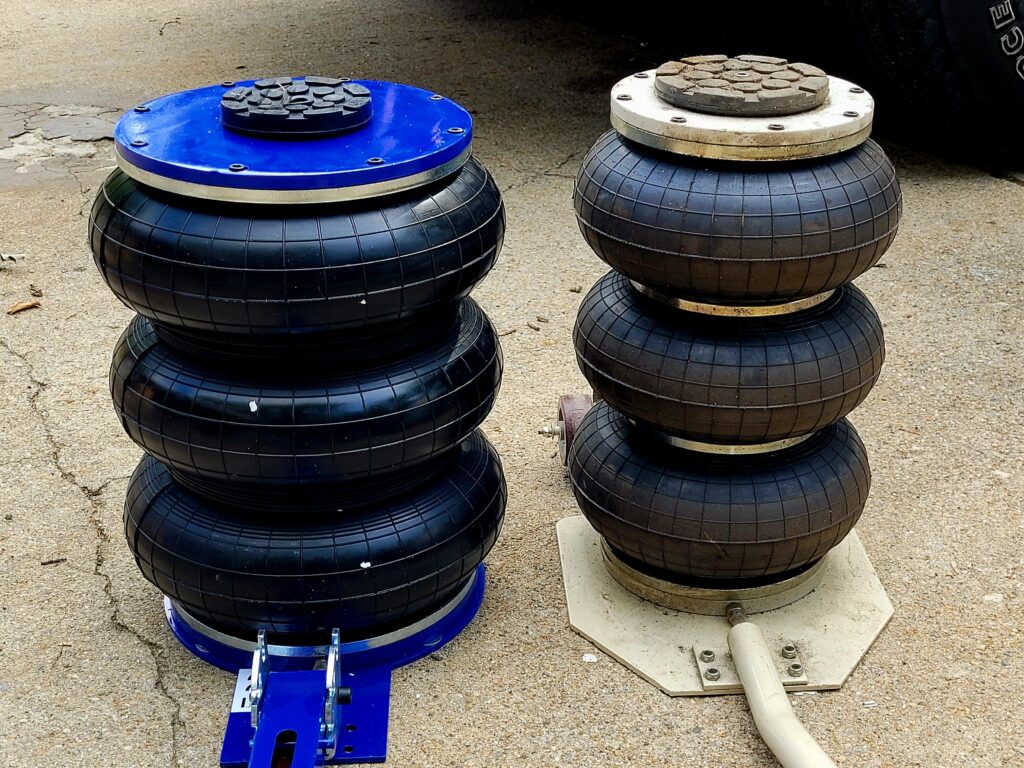
One of the nice perks is that the handle has three positions so you can slide it in flat under a vehicle or at an angle if so you choose. My Mophorn jack’s handle is in a fixed position so that limits how far it can slide under some vehicles but it’s also more sturdy since it can’t move.
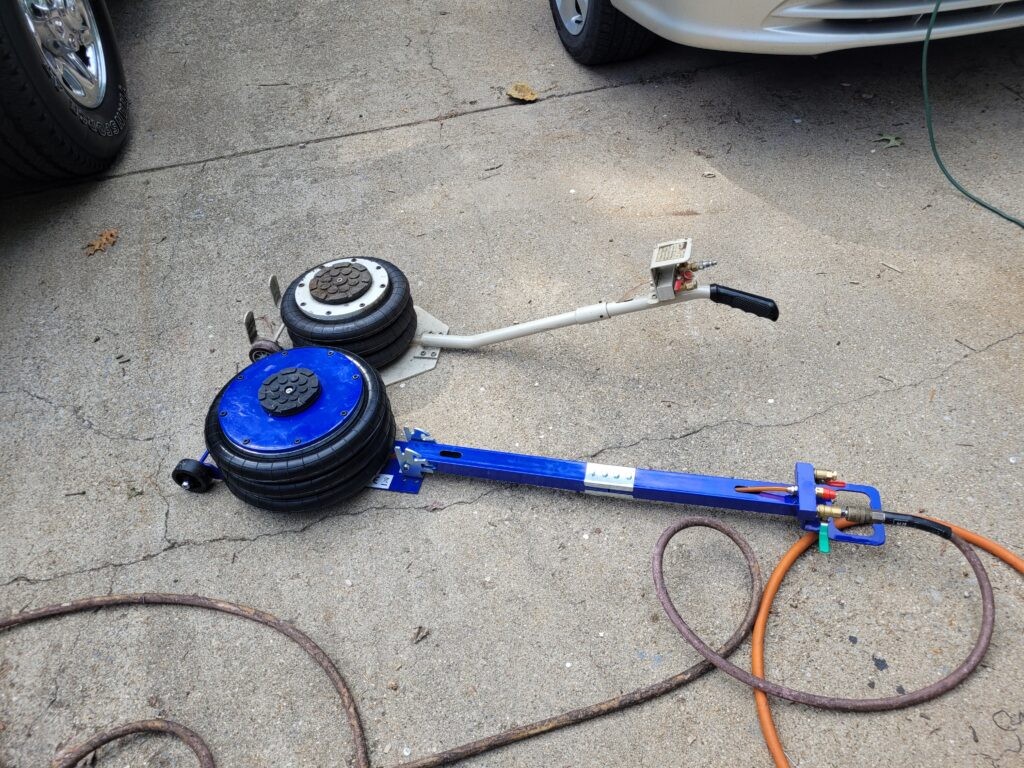
With the Mophorn jack, the screws securing the botton of the bag to the plate started to come loose and the unit was leaking air. With the Vevor, they are in solid and really did not want to back off – I was going to add medium Loc-Tite but since they were in so firmly, I decided to leave them alone. They may even have a thread locker applied already – I’m not sure. I think out of all of the screws there were only one or two I could torque down further.
Summary
All in all, the Vevor air bag lift seems like a solid unit. I’ve not had any problems at all. I sometimes wish the handle wouldn’t move so easily but its ability to fold flat to the ground makes up for that.
I’d recommend the Vevor11,000 pound unit off Amazon [click here to go there]. The Mophorn is always an option also – I’m still happy with that as well.
Last comment – Vevor has a ton of models with different configurations and lifting capacities – click here to open the Amazon listings in a new tab.
2/10/24 Update: Still using both – no problems. I don’t see the Mophorn unit any longer but this CXRCY 6600 pound lift unit looks identical. Chinese brand names come and go but this may be the same factory.
If you find this post useful, please share the link on Facebook, with your friends, etc. Your support is much appreciated and if you have any feedback, please email me at in**@*********ps.com. Please note that for links to other websites, we are only paid if there is an affiliate program such as Avantlink, Impact, Amazon and eBay and only if you purchase something. If you’d like to directly donate to help fund our continued report, please visit our donations page.