Like so many of my stories, this one begins as so “One day I was in my shop and ran across and old rusty tool that was still functional”. Let’s start with a bit of backstory.
My grandfather immigrated from Quebec along with his brother to the Boston area to improve their lot in life. They’d grown up on a farm near Compton, Quebec, and somewhere along the line had picked up the skills necessary to service heavy machinery. He’d tell my dad stories of working on various machines who then relayed some of them to me.
My grandfather had a family, including by dad of course, somewhere near Rockport and eventually bought a farm in Derry, NH, sometime in the late 1930s or early 1940s where he raised dairy cattle, grew hay and what not. Along the way he amassed quite a few tools that then passed on to my dad.
One of these tools was a rusty 18″ pipe wrench that I recall my dad using on a number of occasions and when my dad passed away, I got the tools, including this old wrench.
So, I’m in my shop moving stuff and uncover this big 18″ pipe wrench that I then took a lot closer look at. Interestingly enough, it was made by Ridgid.
Ridgid and the 18″ Pipe Wrench
For years I thought Ridgid was a made-up Home Depot house brand. Actually, it was founded in 1923 in North Ridgeville, Ohio, and moved to Elyria, Ohio, in 1943. What got them started was the invention of the modern pipe wrench. In 1966 it was bought by Emerson Electric and today it sells a lot of different tools including hand tools they make, power tools by Techtronic Industries of Hong Kong and Wet Dry vacs made by Emerson.
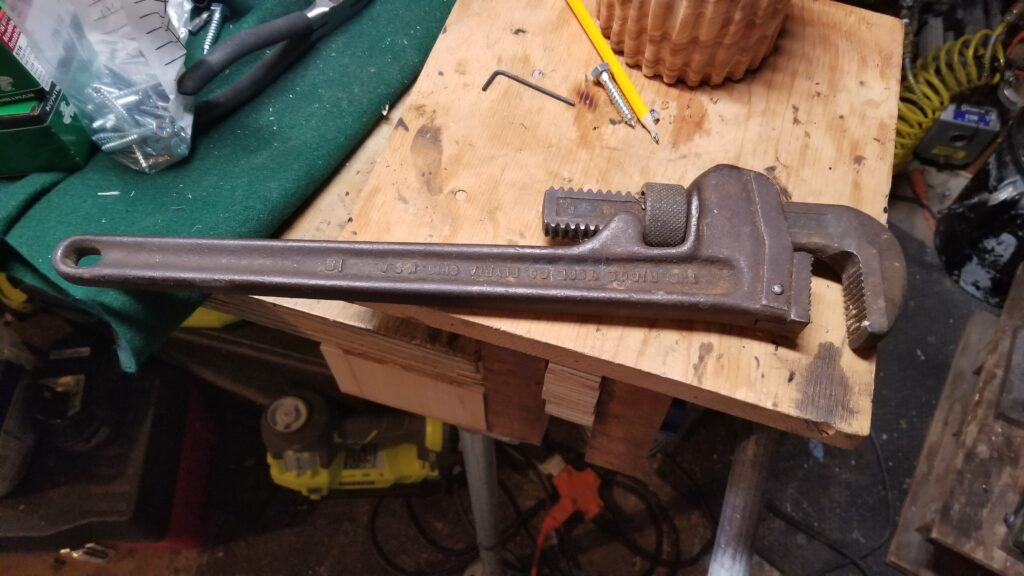
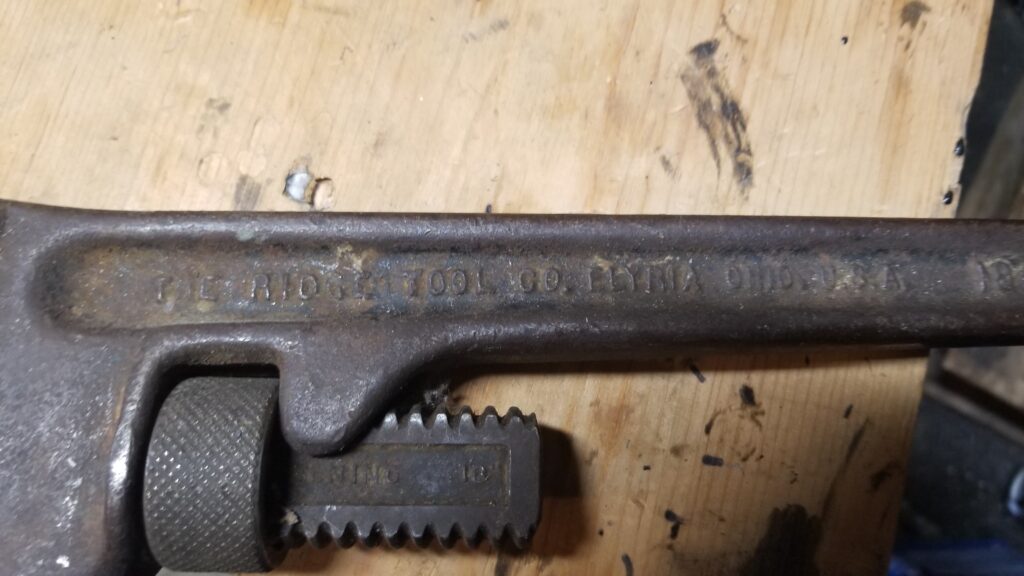
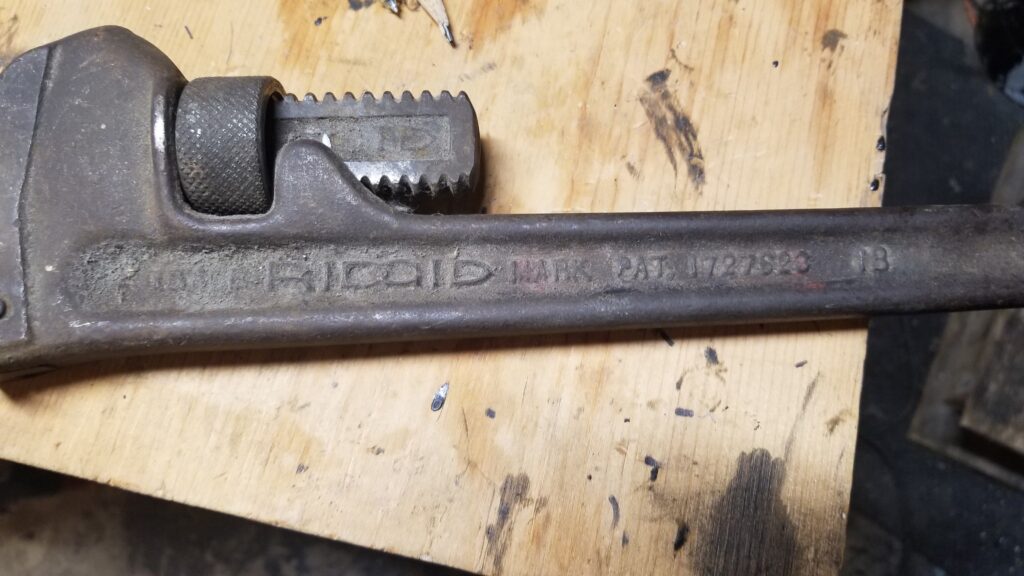
Now if you read the caption of the photo above, the 1727623 patent was in 1929 and 2051755 filed in 1936. That patent was actually split into two and an additional patent 2076830 was filed in 1937. I’m going to go out on a limb and bet that wrench was made somewhere between 1929 and 1937. The compression spring in the wrench is a leaf design and not conical so that does put it prior to 1937 patent.
In reading, guys report the markings as not being very reliable and company records incomplete so the above is really a best guess but it does basically align with when my grandfather would have been buying tools.
So I had a decision to make – leave it alone and let it rust or clean it and apply paint. Well, it’s not like these wrenches are rare collector pieces and this was a tool I would use going forward – seriously, other than being rusty it was good as new.
Removing the Rust
I considered three options – abrasive, electrolytic or acid. The rust was actually pretty light and I opted to go with acid – notably a combination of apple cider and phosphoric acid.
The first step was to spray down the wrench with brake cleaner liberally to get rid of oils. Next, I put a wire brush in my hand drill and removed all of the loose rust and dirt from the wrench body, nut and jaw.
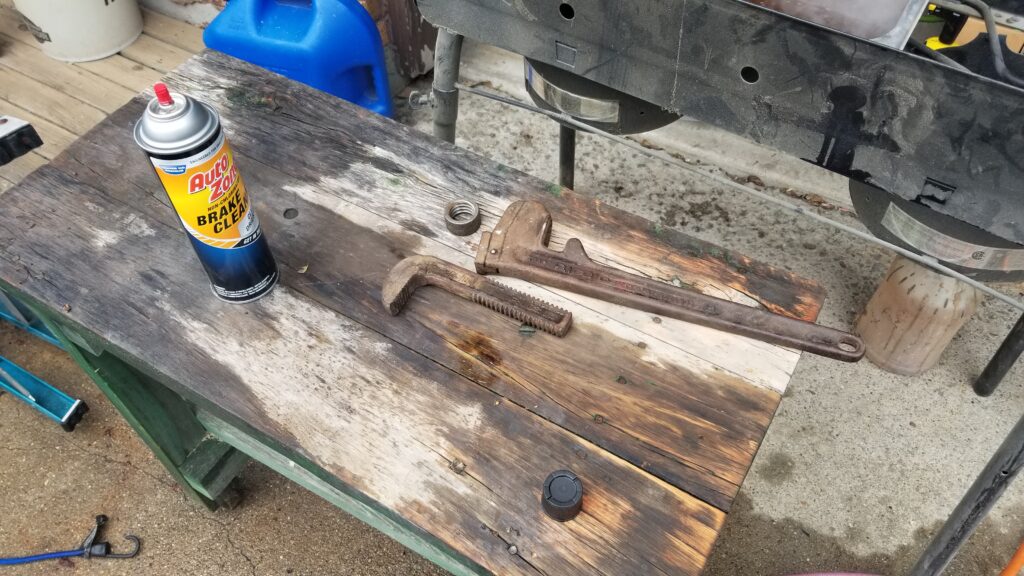
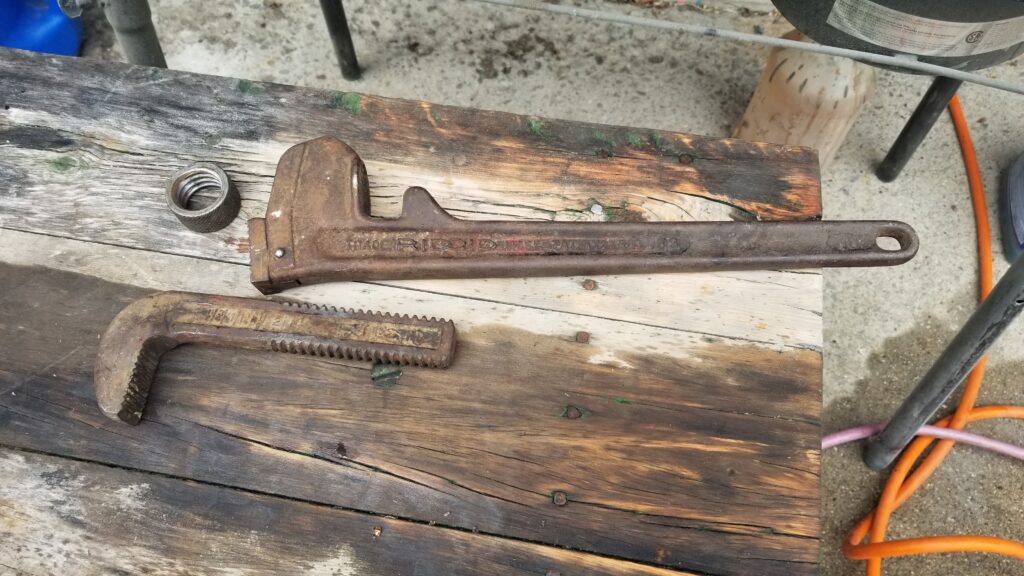
The acid bath was a gallon of grocery store bought apple cider vinegar plus about a quart of Prep-N-Etch phosphoric acid. Apple cider alone would do the job but I was re-using apple cider and I wanted to make sure there was enough acid to do the job.
Now a trick to really get things done is to heat up the apple cider bath and get it warm – you don’t need to boil it. I don’t bother with a thermometer for this – just hot to the touch. The reason why is that heating up a solution speeds up the chemical reaction. If it’s cooler then it just takes longer and if it is boiling off then you are losing liquid needlessly.
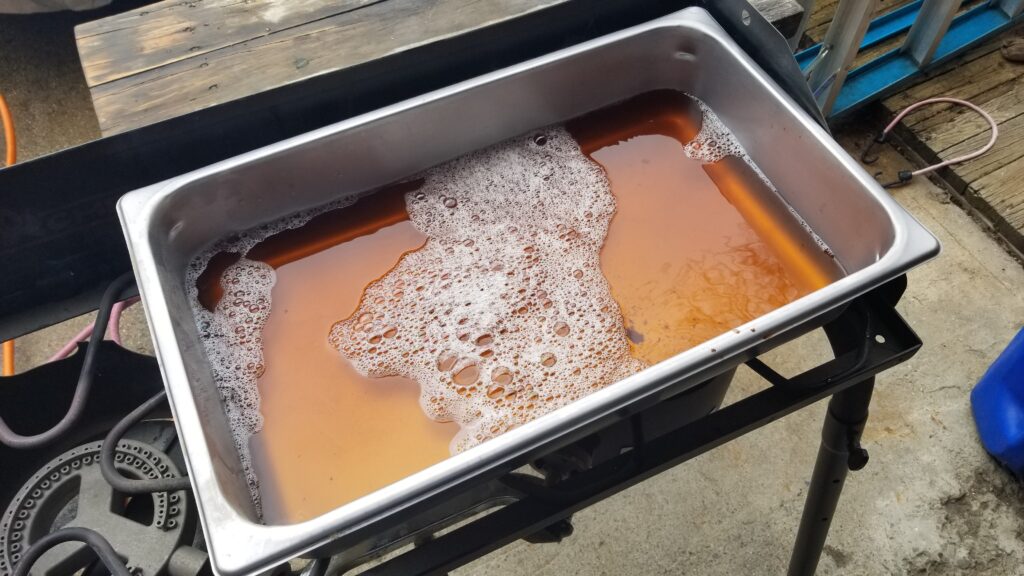
Please remember something – do this in a well ventilated area or outdoors or the condensation will cause exposed steel to rust. It’s a very weak acid solution and while the vapors aren’t something you should be breathing, I would be more worried about causing rust if I were you.
Before I put the wrench parts in the warm/hot acid bath, I really hosed them down with brake cleaner one more time while wearing nitrile gloves. The reason for the gloves was mainly to keep oils from my skin from contaminating the otherwise clean surface. Oil will block the acid. The hot bath will remove some oil but it is contaminated at that point and must be discarded.
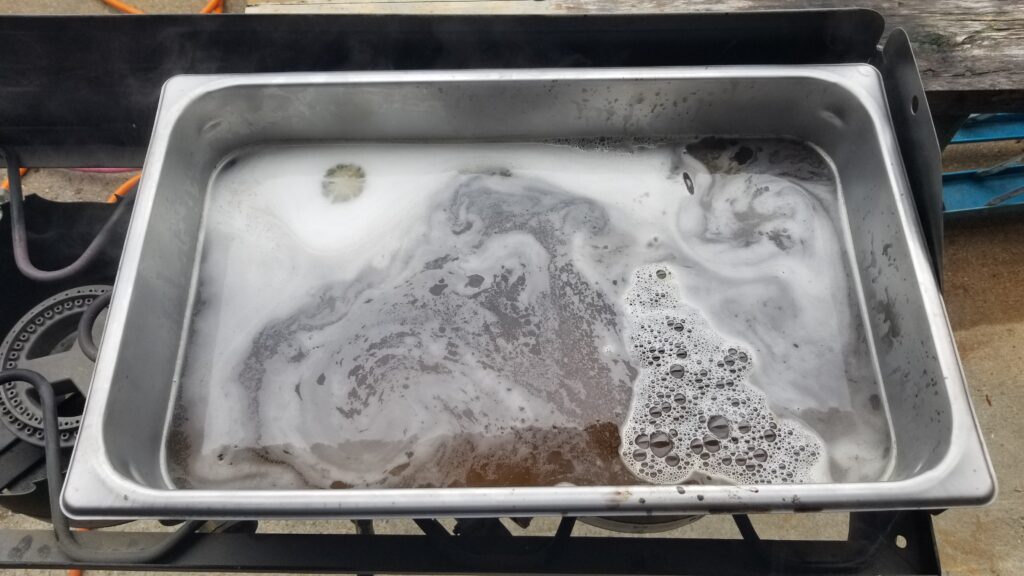
I checked it every few minutes and when all the rust was gone, I pulled it out, hosed it down liberally with water and then used WD40 to displace the water and reduce the odds of rusting. This is what WD40 was meant to do – water displacement formula 40.
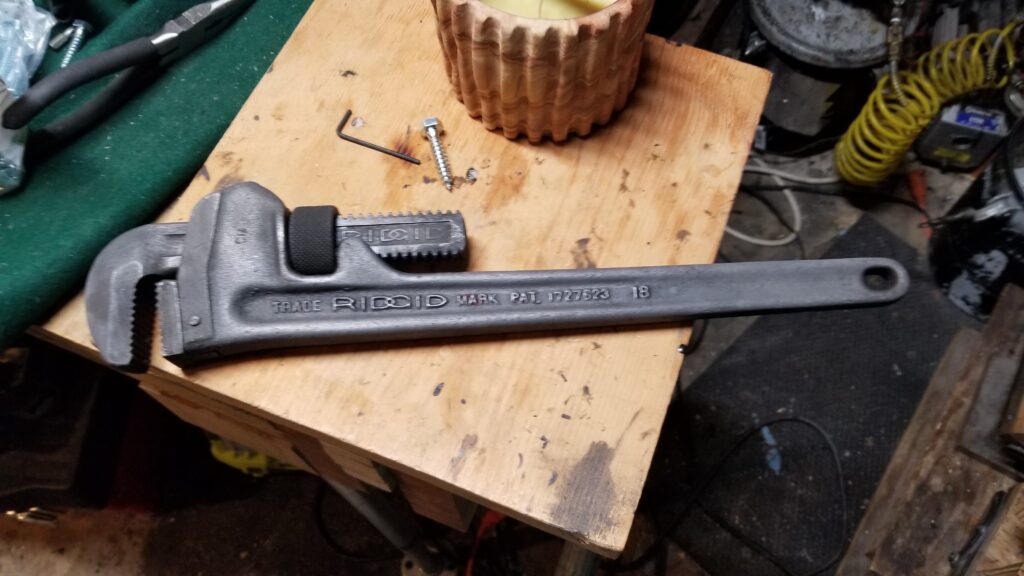
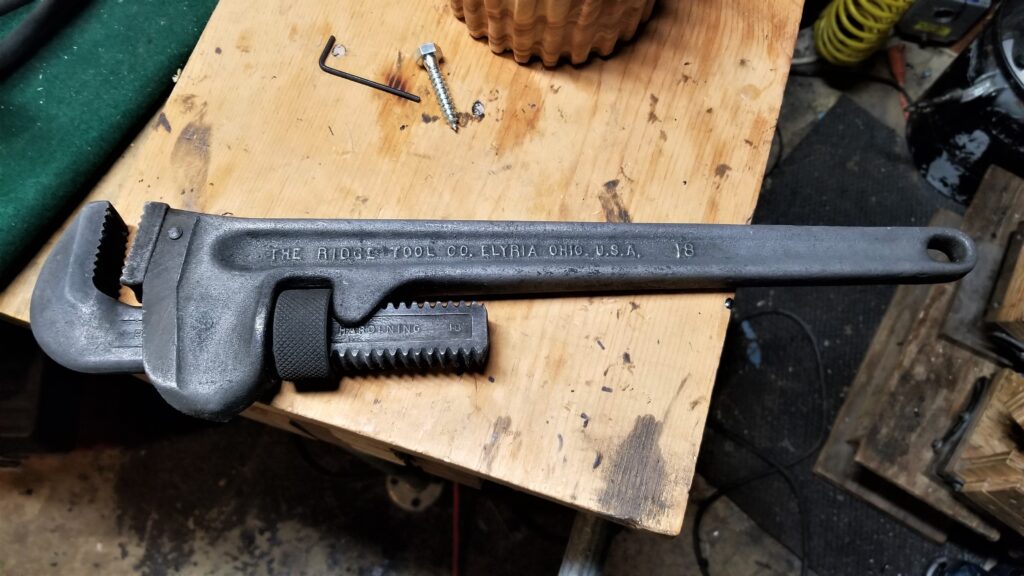
At this point it was getting dark and I decided to wait until the next day to point the wrench but here’s what it looked like at that point. The next post will be about painting the wrench and the end result.
By the way, I’ve written on using apple cider to remove rust from tools as well as formal manganese parkerizing before this so you can click on one of the links to learn more.
If you find this post useful, please share the link on Facebook, with your friends, etc. Your support is much appreciated and if you have any feedback, please email me at in**@*********ps.com. Please note that for links to other websites, I may be paid via an affiliate program such as Avantlink, Impact, Amazon and eBay.