When any projectile weapon is made, there are machining operations, dust and lubricants. Now a lot of this is down in the bore of your new purchase. This is true of any arm – including air guns of all types and firearms. If you shoot your weapon without cleaning it, you do risk hurting the barrel or maybe even a jam. Think of it this way – all that crud has to go somewhere. It may go out the end of the barrel or it may get pressed into the walls of the barrel affecting accuracy going forward.
So, clean the barrel. Now, I’m going to focus on airguns going forward as there are some peculiarities to consider.
#1 – The steel used in air rifles and air pistols is relatively soft – way softer than that found in a firearm. You must take care not to nick the crown of the muzzle and create a burr that will affect accuracy. I would recommend aluminum or carbon fiber cleaning rods and not steel. Look out for the pull through cords as many (not all) have a wire brush as part of the unit. There are flexible wire units that allow you to pull the patch in from the breach and out the muzzle end. Personally, I swear by carbon fiber rods and mainly use Tipton brand rods now. I have 4-5 of them now for different calibers and lengths of barrels.
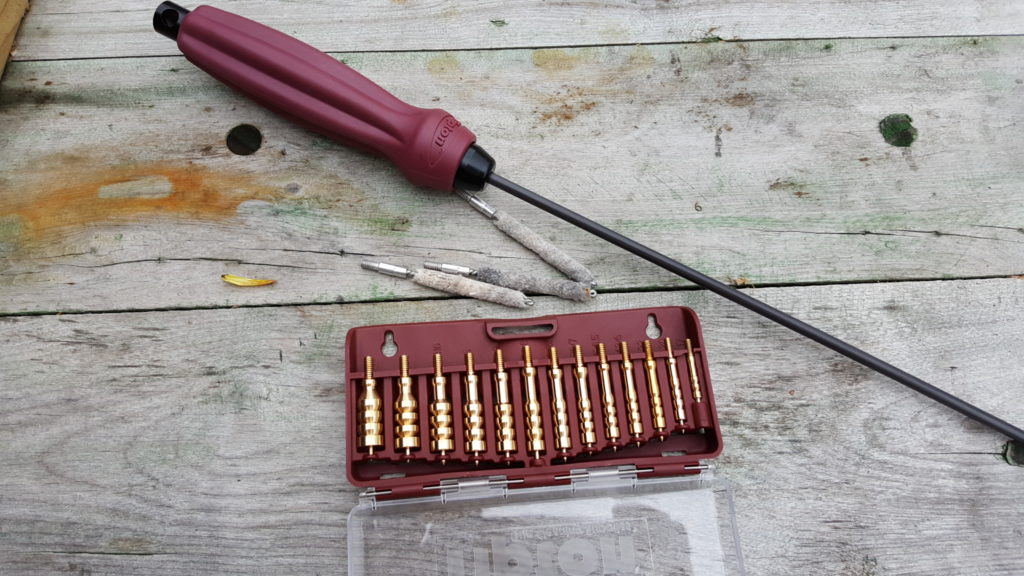
#2 – Because of the soft steel, do not use any form of wire brushes as they may hurt the rifling and accuracy going forward. I just use a simple mop for the given caliber that screws into the end of your cleaning rod. Tip – make sure the thread of your tip(s) match the size of your cleaning rod – for example, that if the rod is 8-32 (size 8 with 32 threads per inch) then the tips should be the same. I have the following jag set from Tipton. These impale a patch and allow you to push it down the bore while scrubbing the sides.
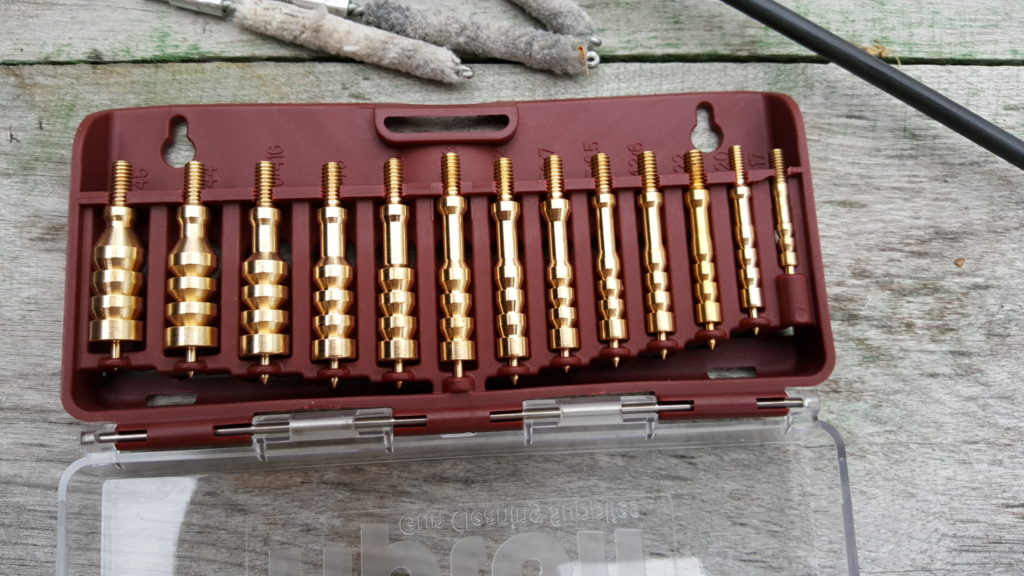
#3 – Look out for strong solvents. I’d recommend something light such as WD40, CLP or any modern synthetic transmission fluid. If you didn’t know it, automatic transmission fluid (ATF) is a great cleaner and lubricant for airguns and it lubricates the O-Rings. Regardless of what you use. Run dry patches after to remove any extra lubricant. By the way, WD40 can help with cleaning but it will not prevent rust.
The following is an example of a clean and dirty mop after going through my brand new Hatsan Gladius and note you would see this from just about any brand and I’m not saying anything bad about Hatsan. My Gladius is fantastic. To do the initial cleaning, I used WD40 with the mop and then ran patch after patch after patch until it was relatively clean. You can decide where you want to stop or you may spend the rest of your life running patches down a barrel.
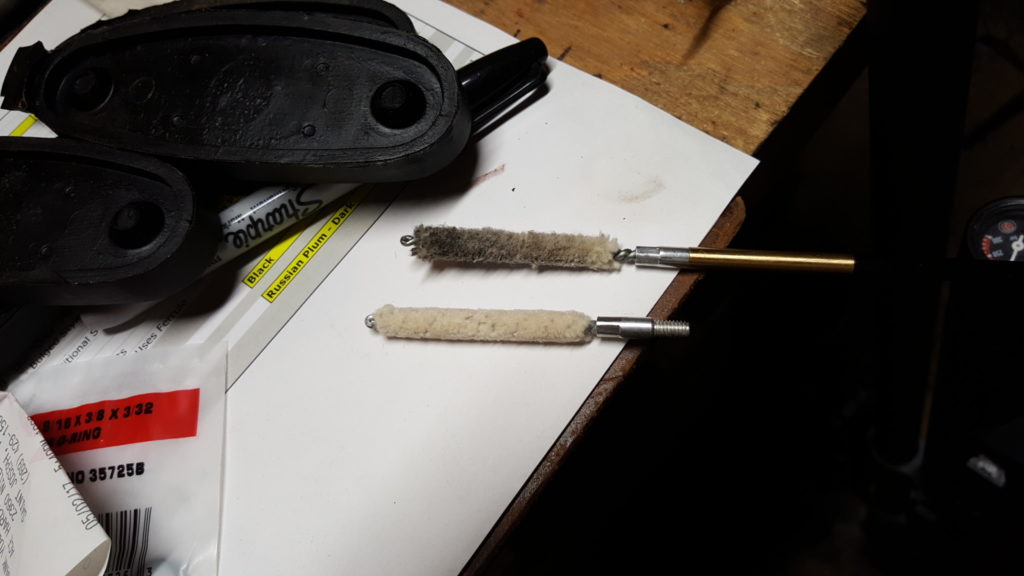
#4 – This is a bit of a general comment, but be aware of where all the junk is going when cleaning. For example, don’t use a cleaning and was all the crud down into your action. Unlike a firearm, it can be nearly impossible to clean from the breach end so you have to clean from the muzzle. Thus, be sparing with the cleaner and inspect the breach end to see if you need to clean the weapon further. My advice would be to go light on the cleaner and just make how ever many passes are needed with the mop and/or patches until the bore is shiny.
#5 – I recommend using a decent gun vise to hold what you are working on to free up your hands. I sure have cleaned a lot of rifles and pistols over the years sitting on the floor and still do from time to time but the Tipton “Best Gun Vise” has worked well for me.
So with that, you are done. Guys ask how often should they clean and the answer is surprisingly little – you may choose to do it on a regular preventive basis or when you notice accuracy tapering off. One thing I had told to me that I took as gospel and will pass on – beware of the harsh cleaners that have ammonia as it will attack/harm aluminum parts in airguns and airguns tend to use a lot of aluminum.
This last comment has to do with lubrication vs. cleaning. Note, if you are ever lubricating the main spring, areas around the piston or other high pressure areas, you must what is recommended and it is probably some form of silicone based lubricant vs. petroleum. Be sure to read up on what is recommended for your application before doing anything in those areas.
In reading the above it sounds like a Tipton commercial but it wasn’t planned – the listed items are what I actually use. I was not paid to write this. I’ve bought all my Tipton stuff over the years from Amazon and Midway depending on pricing and availability.
At any rate, I hope these tips help you with your next project.
If you find this post useful, please share the link on Facebook, with your friends, etc. Your support is much appreciated and if you have any feedback, please email me at in**@*********ps.com. Please note that for links to other websites, I may be paid via an affiliate program such as Avantlink, Impact, Amazon and eBay.
Like this:
Like Loading...