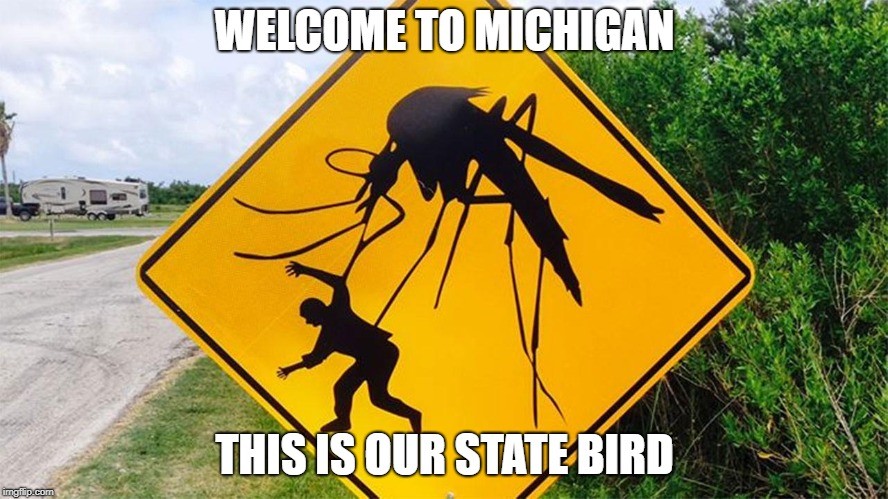
Our home is in a former swampy area that was drained in the 1980s and a subdivision built. In short, you dig down and can hit water fairly soon – usually within 10 feet. At any rate, we’ve had a very wet spring and summer and had standing water in our lawn until late-June and the mosquitoes have been the worst I ever recall in the 20 years we’ve been here. We could not stay out at night or we’d get attacked unless we hosed ourselves down with Deep Woods Off. In short, something needed to be done.
This hedgerow is right by my garage and ensured the mosquitoes had a perfect base to attack me from and rings our property:
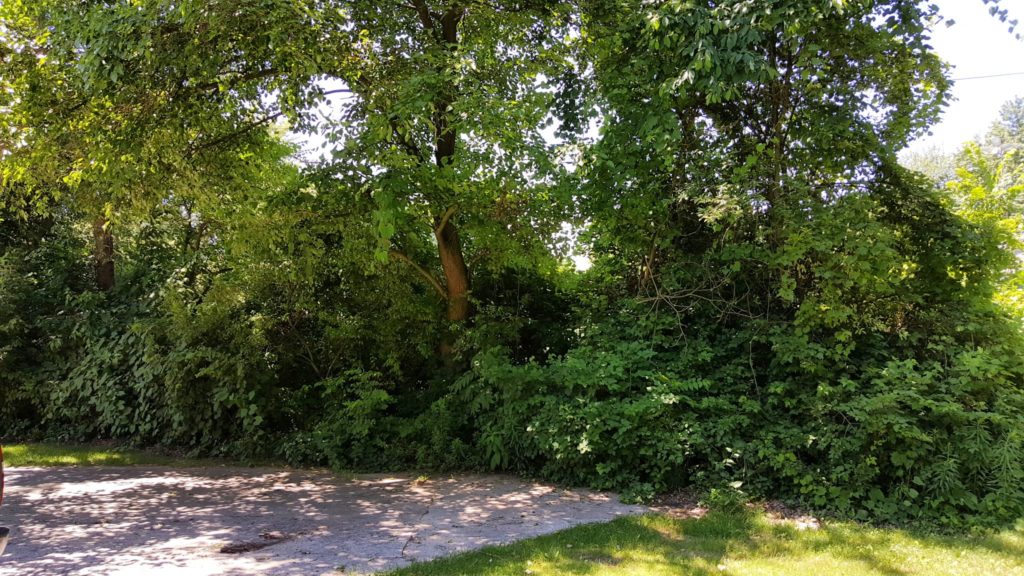
When I was at Ace Hardware, I saw Off! brand’s Backyard Pretreat that was supposed to kill mosquitoes and leave a residue to repel them. I thought they would know what to do given their experience – as it turns out, this product is a rip off.
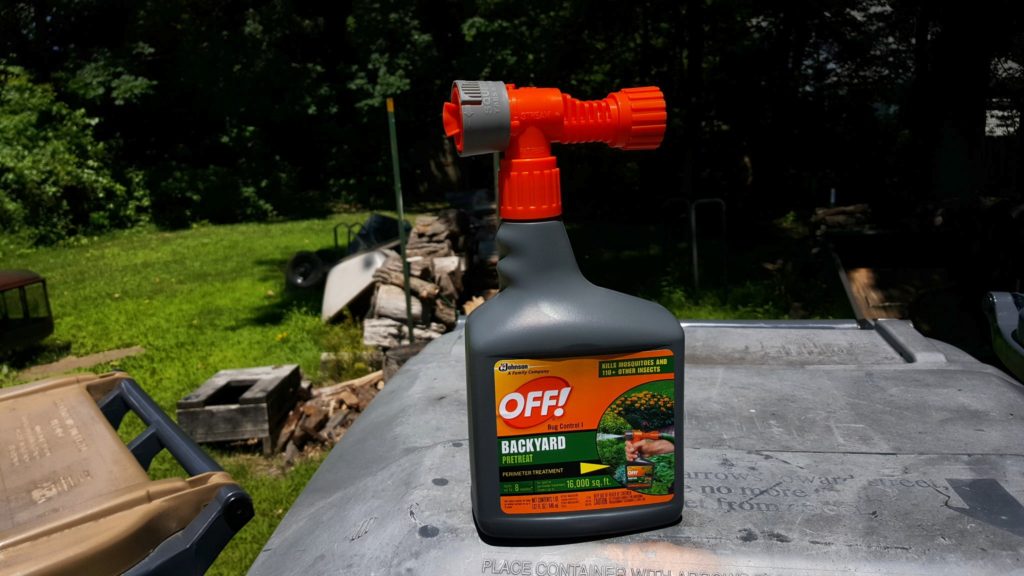
I’m sad to report that after three jugs of this stuff and my getting bit over and over while applying it, I can’t say it did anything at all even several days later. I really had high hopes – I dragged a long hose all over the place spraying stuff down over and over with no noticeable improvement.
On Facebook, I posted my woes with Mosquito control and a friend, Allan, suggested Talstar P Pro and a Ryobi cordless electric sprayer to help with evenly spraying a ton of solution. I had never heard of Talstar so I did a search and it is very well regarded. Allan told me they live on a wooded ravine and he’s been using it for 10 years to control mosquitoes and it worked exceptionally well for him.
Talstar P Professional
Every once in a while on Amazon, you see a review score that is mind blowing. FMC’s Talstar P Professional 96 oz has 2,263 customer reviews and a combined score of 4.6 out of 5 stars. That is one heck of a score and is only possible if something works really, really well.
5/21/2023 You will no longer find it on Amazon – you need the liquid Talstar and I tend to find eBay the best source to buy it. Click here for a current list on eBay.
So, based on what I read and Allan’s recommendation, I ordered the 96oz bottle. I then read up on the Ryobi sprayer. It gets good reviews, uses the 18volt Ryobi batteries (it comes with one battery and a charger) and it has a three year warranty. I ordered it off the Home Depot website [Click here] as they had free next day home delivery and since I had to wait for the Talstar, I figured it would save me a trip.
Note: You can use any pressurized sprayer you want – I have 1.5 acres and knew I would be applying gallons and gallons of it. My shoulders and elbows hurt enough as it is and I didn’t want to incur the repetitive stress.
The sprayer arrived the next day and the Talstar the day after. While I was waiting, I went to the FMC website to read up on Talstar to make sure I understood how to apply it plus I peppered Allan with his experience.
I would recommend you go to the website [click here] as they have recommendations on best practices for mosquito management and Talstar P Pro is actually interesting from a chemical perspective.
The active ingredient is Bifenthrin, which is similar to the chemical extracted from Chrysanthemums to kill insects. Here are two links so you can read more at the National Pesticide Information Center.the user guide for the Talstar P.
Ryobi Model P2830A One+ 18-Volt Lithiu-Ion Cordless 2 Gallon Chemical Sprayer
Here are photos of the sprayer. I charged the battery and screwed in all the fittings. They are all lose so be sure to do that. I didn’t have any loose plastic in the tank but I did rinse it out just to be safe.
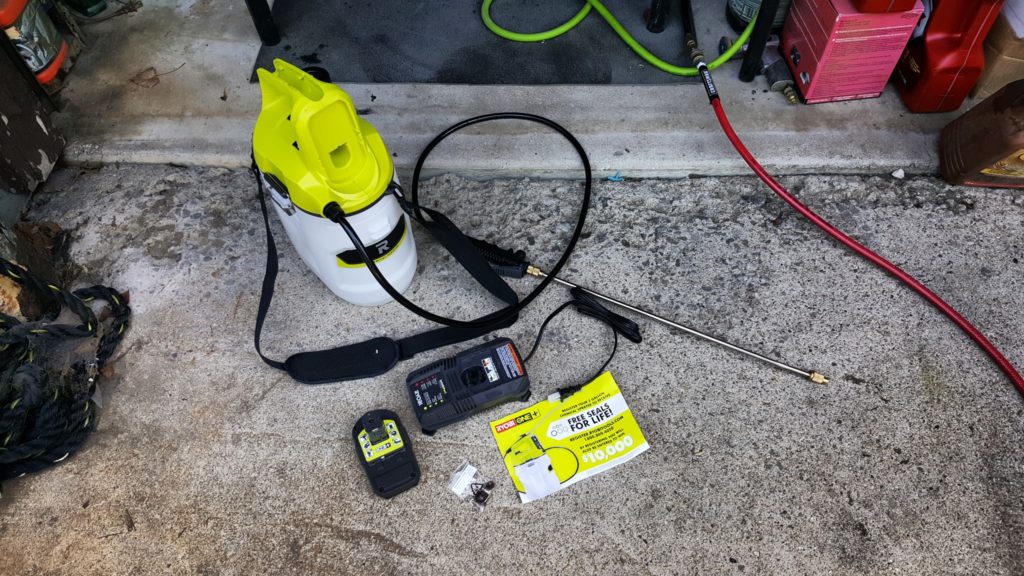
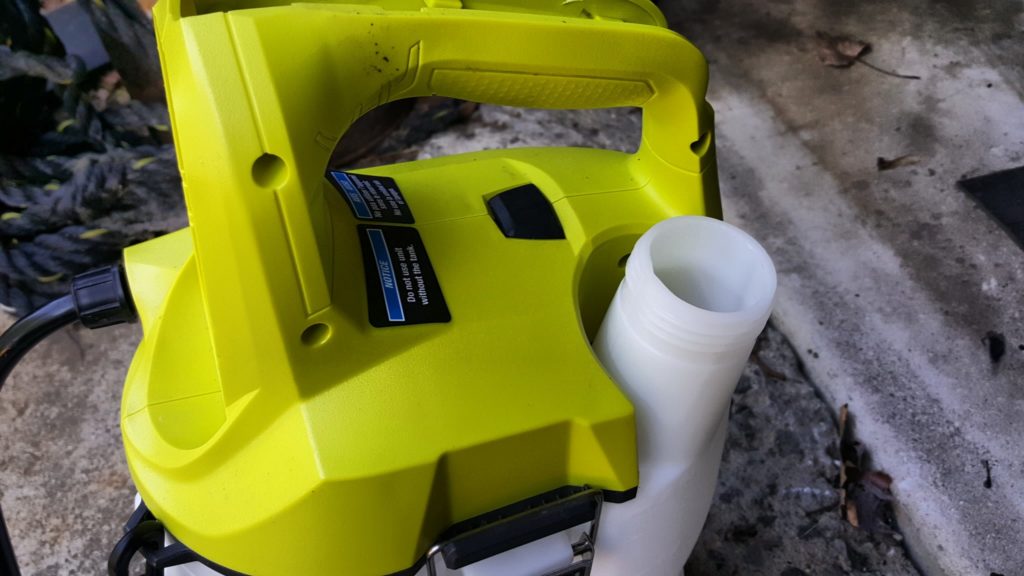
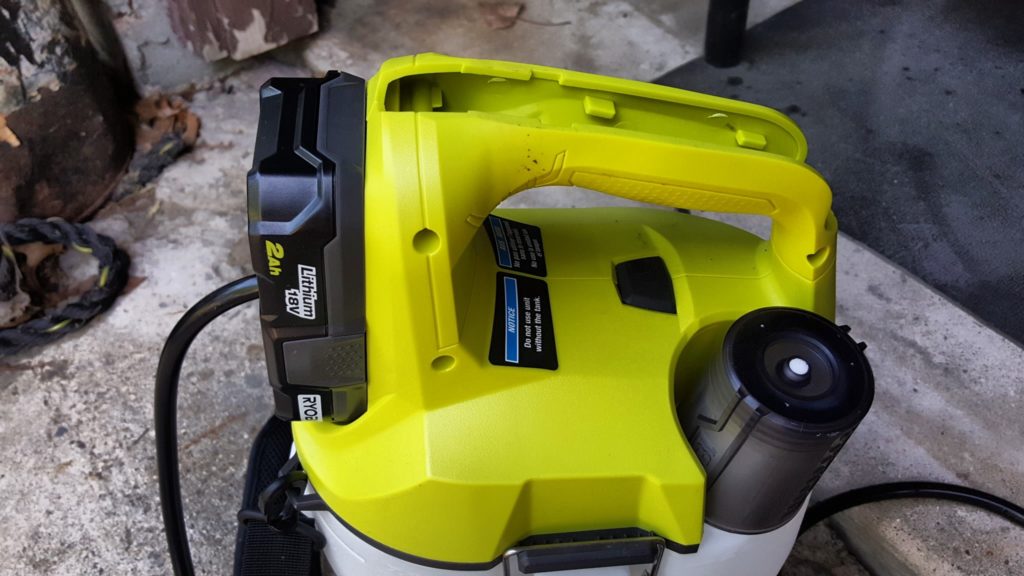
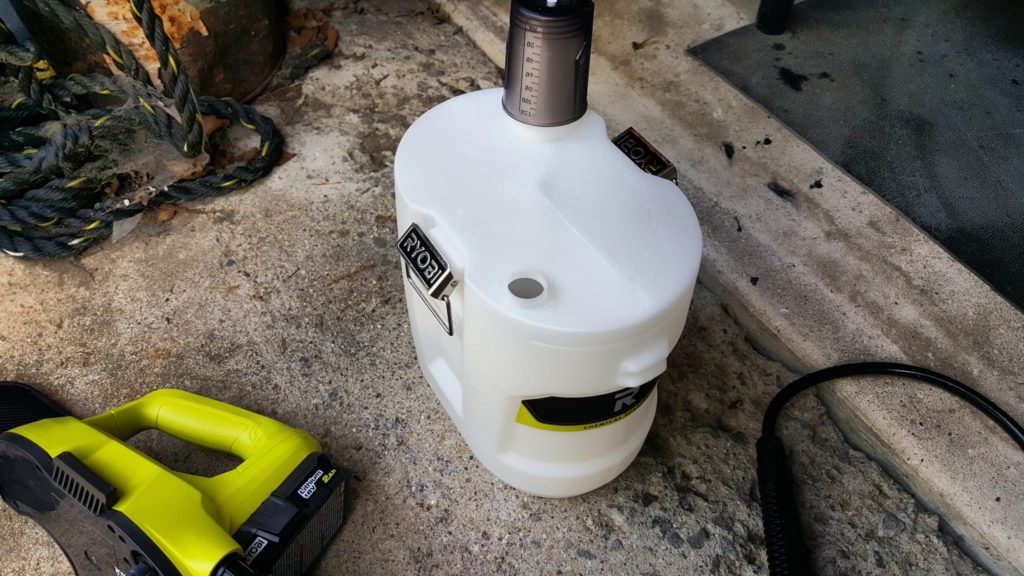
Application
After reading the user guide, I planned to use one ounce of Talstar to one gallon of water to ensure I had residue to continue killing mosquitoes. Since it was a two gallon tank, I increased it just a bit to 2.5 ounces per two gallon tank. Note, a real nice perk is that the tank lid is a measuring cup! I would use it, rinse it out and pour the mix into the tank before filling it with water.
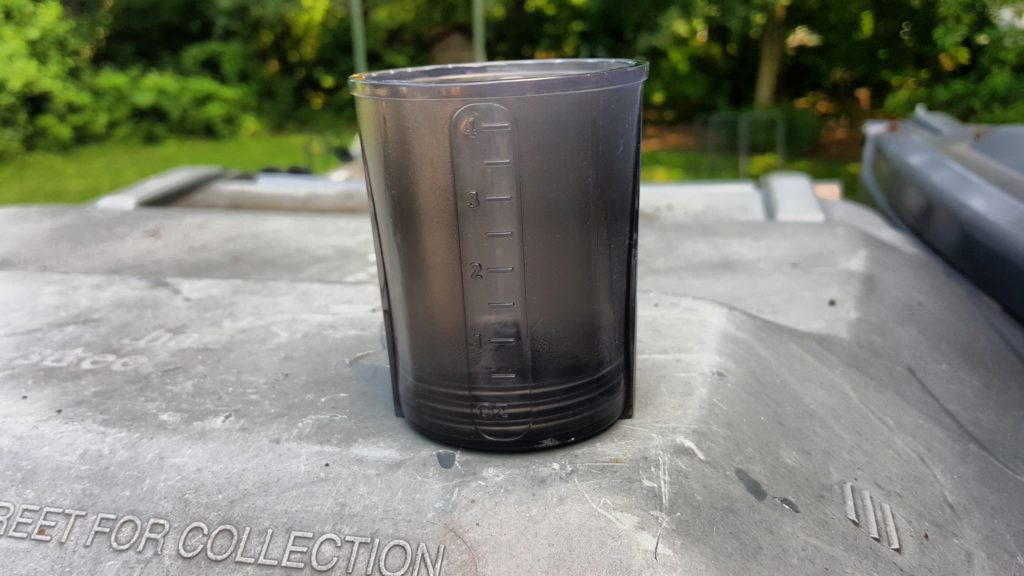
While doing the work, I wore Nitrile gloves just to avoid contact plus I was constantly adjusting the sprayer tip from coarse mist to a stream to try and reach back over brush, through leaves, etc.
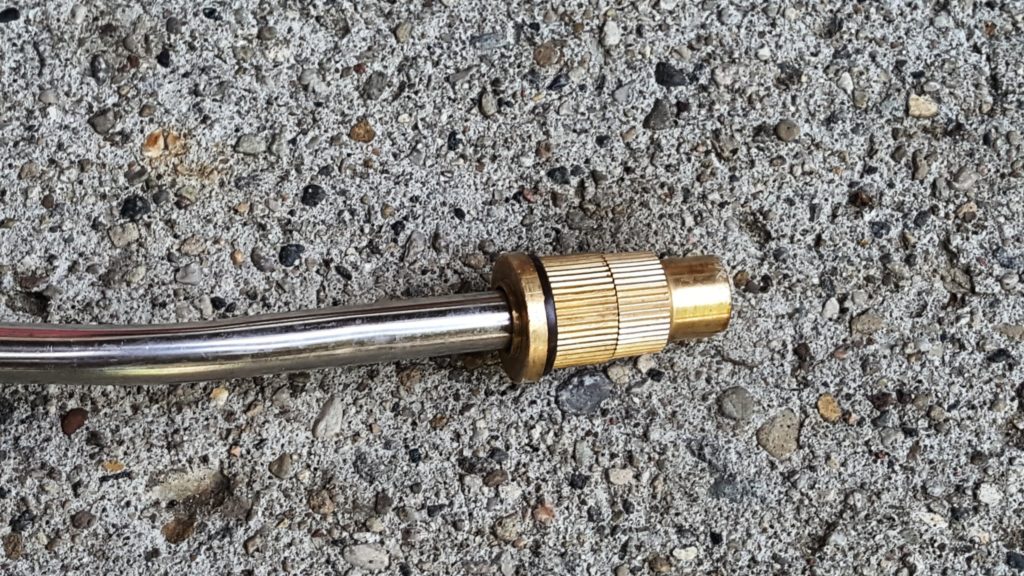
FMC recommends spraying at night or in the evening when mosquitoes are active. I was busy the first night so I did it the following morning at 7am. I mixed up two gallons and started spraying around the house, pool, garden and so forth. I hosed down the bushes, the walls of the house and under the eaves. I also sprayed the hedge – first using a coarse spray on all the brush, leaves and ground. I found adjusting the tip to a stream was handy to penetrate the brush and also reach further back. I’d just come back to the hose and what not and mix another two gallons of spray (2 gallons water and 2.5oz of Talstar) and kept spraying.
It took me aboput 30-45 minutes and 8 gallons, or four complete tanks, to do most of our yard. I skipped probably a half acre of grass starting about 100-150 feet from our house but I did all of the hedge row, bushes, etc. I was pleasantly surprised that the 2.0Ah battery was able to do the whole yard. When I finished the first batch, I did plug the battery in and let it charge.
That night I still saw mosquitoes, but fewer of them, and applied a second dose around 7:30-8pm. Same procedure – 8 gallons focusing around the house, all the bushes, etc.
Results
The next morning – no mosquitoes. Whoa!!! I did not see one single mosquito all day. That night I worked on cars without being attacked! I did so again yesterday and just had breakfast with my wife in her garden — something that would have been next to impossible.
I’d say the spray got a good number of them but when they landed in the residue, that got rid of a ton as well. In other words, you might see a bit of a delay from dose to noticeable reduction.
In four weeks, I am going to do it again. Even my wife, who always groans at me and my tinkering, was impressed and told me to make sure I apply another dose before the first one wears off!
It’s really not that expensive in the long run. The bottle holds 96oz. I use 10oz per 8 gallons (4 batches x 2.5oz/batch). If I apply it twice per application, that means I’ll use 20oz per time, which means I’ll get just over 4 complete applications (so about four months of protection). At $35/bottle, that’s about $9/time plus however you want to account for the sprayer. For me, it’s worth it. My wife really reacts to mosquito bites plus we can enjoy being outside again and I can go back to working outside without getting attacked.
I’d highly, highly recommend you skip the ripoff gimmicks and temporary fixes. Spend the money and get Talstar Pro and a spray bottle (if you don’t have one). It made a world of difference for us and wanted to spread the word that this stuff really works.
May 21, 2023 Talstar is no longer on Amazon but there are tons of sellers on eBay – click here to open eBay and see the latest Talstar P Pro liquid listings..
If you find this post useful, please share the link on Facebook, with your friends, etc. Your support is much appreciated and if you have any feedback, please email me at in**@*********ps.com. Please note that for links to other websites, we are only paid if there is an affiliate program such as Avantlink, Impact, Amazon and eBay and only if you purchase something.