I bought a new 2021 Ram 2500 in September of 2021. It was my first heavy gasser with a 6.4L Hemi and a piece of advice a lot of guys gave me was to make sure I rotated the tires with every oil change. It sounded reasonable – it’s heavy truck and the tires need to be rotated so they will wear evenly. If you don’t do this your handling may suffer such as picking up a wobble or you may wear the tires such that they must be replaced prematurely. Ok, I was totally on board with concept but then started thinking about how heavy they probably were – I sure knew they weren’t going to be light.
Factoid: FCA (Fiat Chrysler Automotive – who owns Dodge now – and FCA is now part of Stellantis – for those keeping track of who owns who) reports the LT275/70R18E Firestone Transforce AT tires as weighing 50.7 pounds. The 16×8 steel chrome clad wheel comes in at 45.2 pounds. Add them together and you get 95.9 pounds not including any wheel weights, TPMS, etc. So you might as well say that each weighs 96 pounds. Yeah, that’s quite a bit for me. |
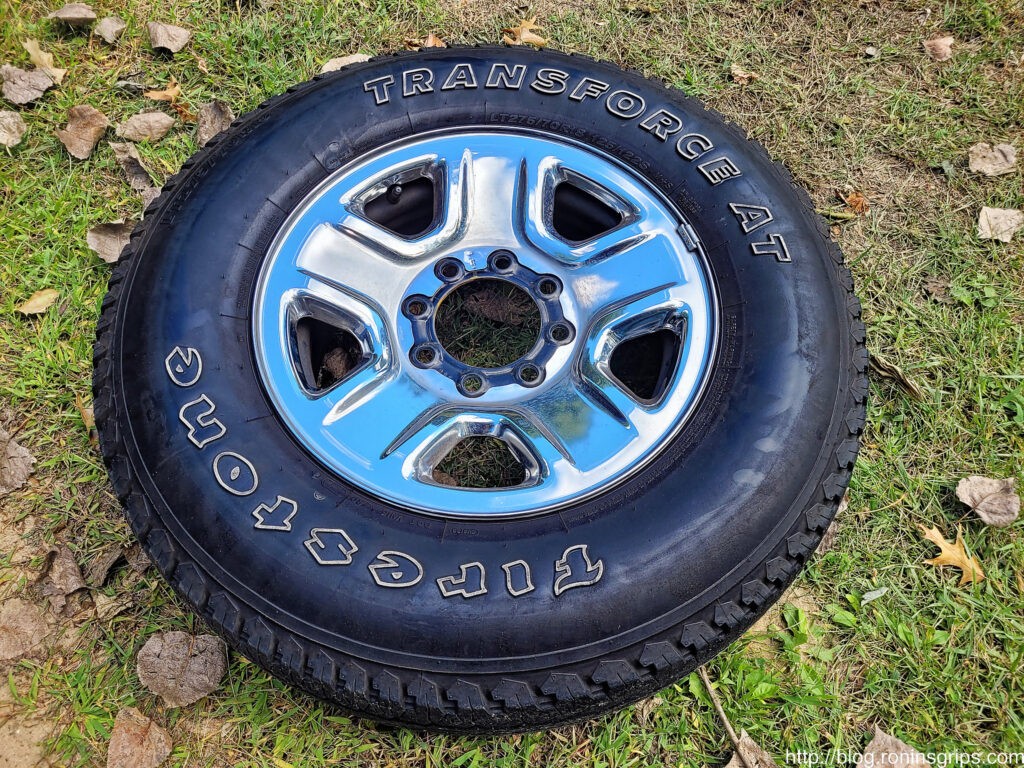
From years of doing stupid stuff, my back and hands are nowhere near as strong at 55 as they were in my 20s and 30s. I’ve always done my own oil changes, tire rotations repairs in general and didn’t plan to stop and pay the ridiculous prices the dealer was quoting. I knew it would be a heck of a struggle for me to lift the tires up and hold them in place while getting the first couple of lug nuts on to hold it. I needed to figure out a way I could lift the 33″ 96 pound tires up into place using mechanical advantage.
So I started by searching on the web for tire/wheel lifts and most of what turned up had to do with moving truck tires across a shop on a dolly. I wasn’t finding anything that said “use this to lift your tires up and down at the vehicle.” My next stop was the local Harbor Freight store to look at various automotive tools and jacks to get ideas. It was there that I got an idea.
There are ratcheting vehicle dollies for garages where there is one dolly for each wheel. You pump a foot pedal and a pawl engages a notch and pushes two cylinders together under the tire. As it does this, the tire and vehicle are lifted up. You do this on all four corners. The dollies have caster wheels under them and if you have a clean concrete floor, you can then slide the vehicle all over the place to either store or work on it. One early trade name was “Gojak” and since then tons and tons of companies have made them.
Hmmm…. I could take one of those and use it to lift the tire into position and hold it as long as I could lift the tire high enough. These jacks are rated at over a 1,000 pounds and my truck’s tires were going to be far, far less than that. No, it was the height that concerned me because I needee to lift the truck high enough to remove the tires in the first place.
I didn’t particularly care for the looks of the Harbor Freight model so I did some digging and found a Sunex unit on Amazon that works in a purely mechanical manner – some hydraulic models from other brands are reported to leak.
It arrived and took just a few minutes to install the caster wheels. I did make one mistake, I was curious if it could lift one corner of the truck – the answer is a resounding “NO” and I did bend the outriggers that hold the casters slightly. I really didn’t expect it to bend but it also didn’t really hurt the unit from an intended use perspective.
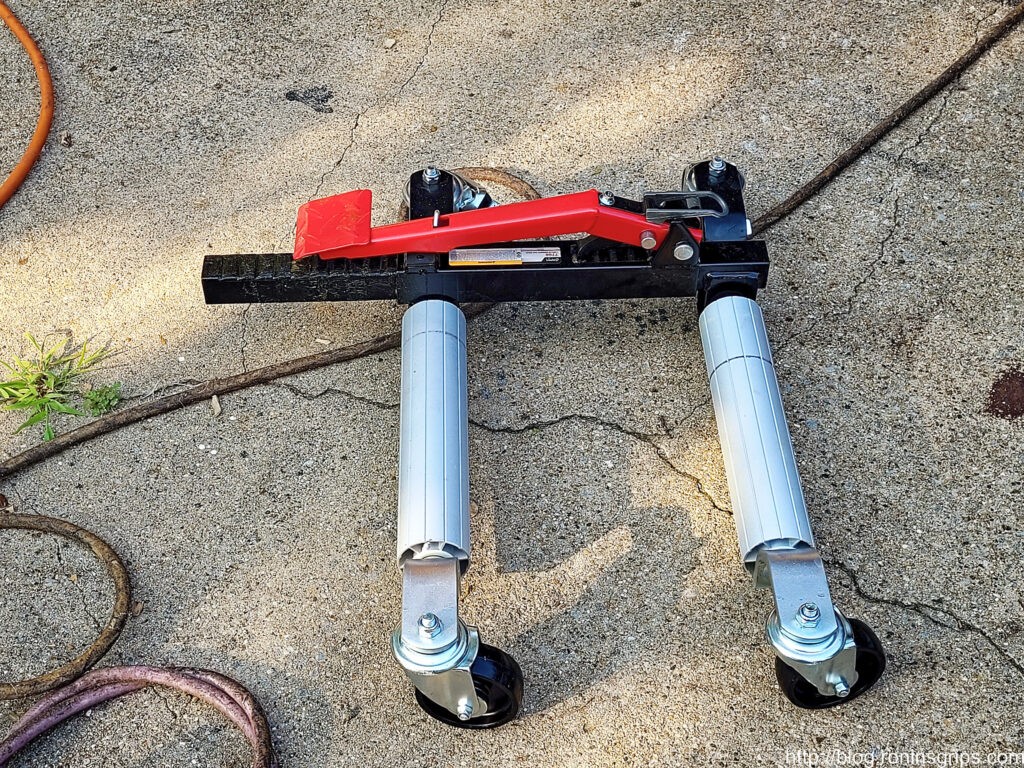
Most importantly, it worked perfect. I would roll the tire over to my truck, slide the jack in by the edges of the tire and then pump the foot lever until it was the right height. I could then install the lug nuts in an amazingly easy manner. It worked so well I did it both on my Ram 2500 and on our Highlander.
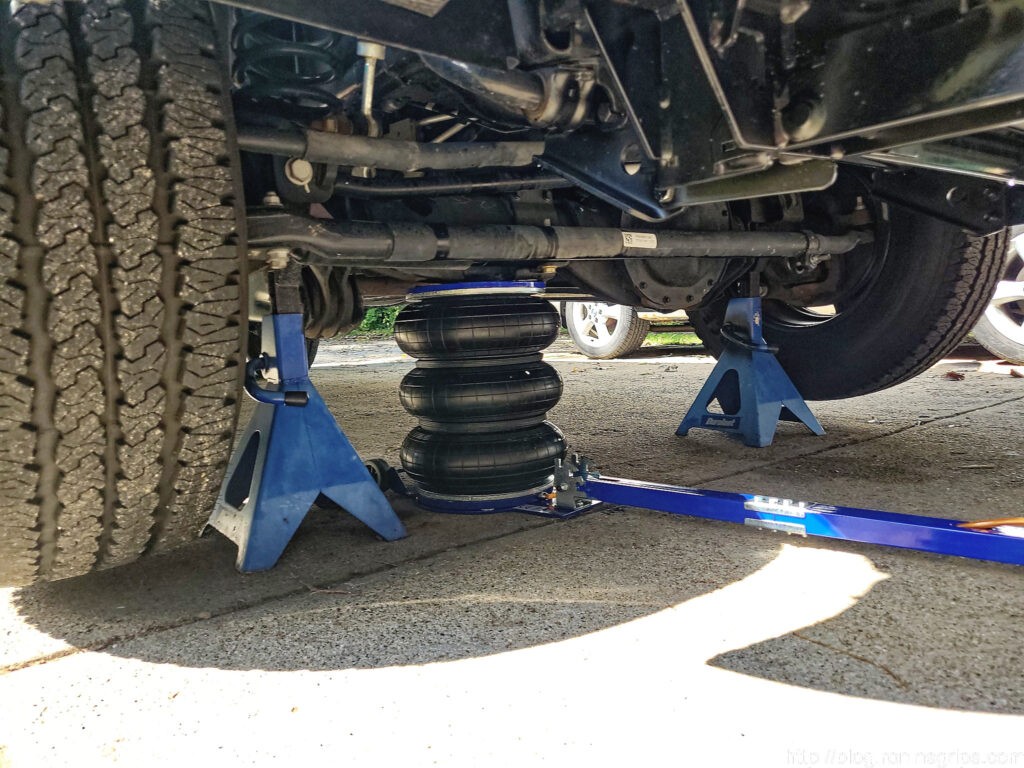
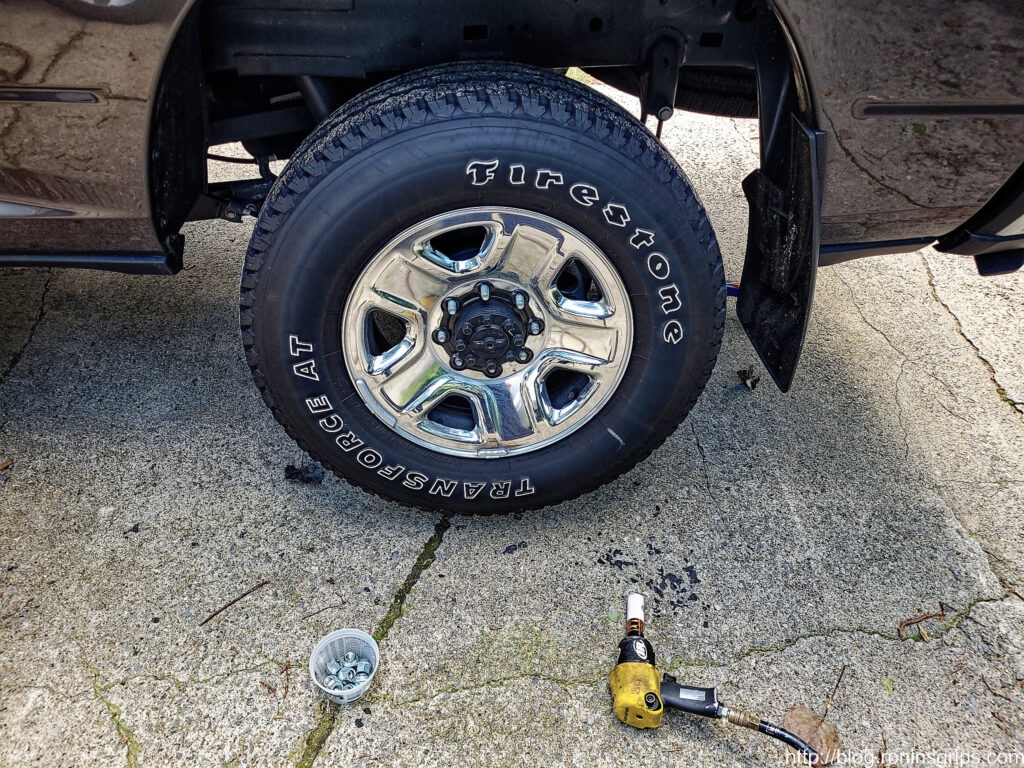
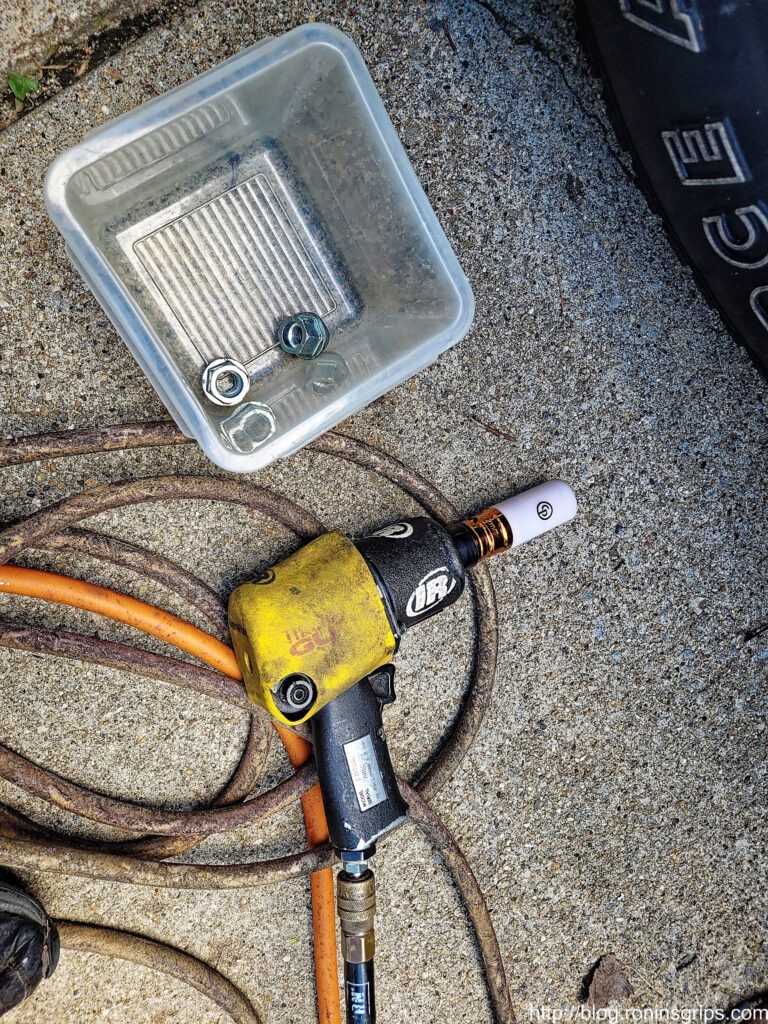
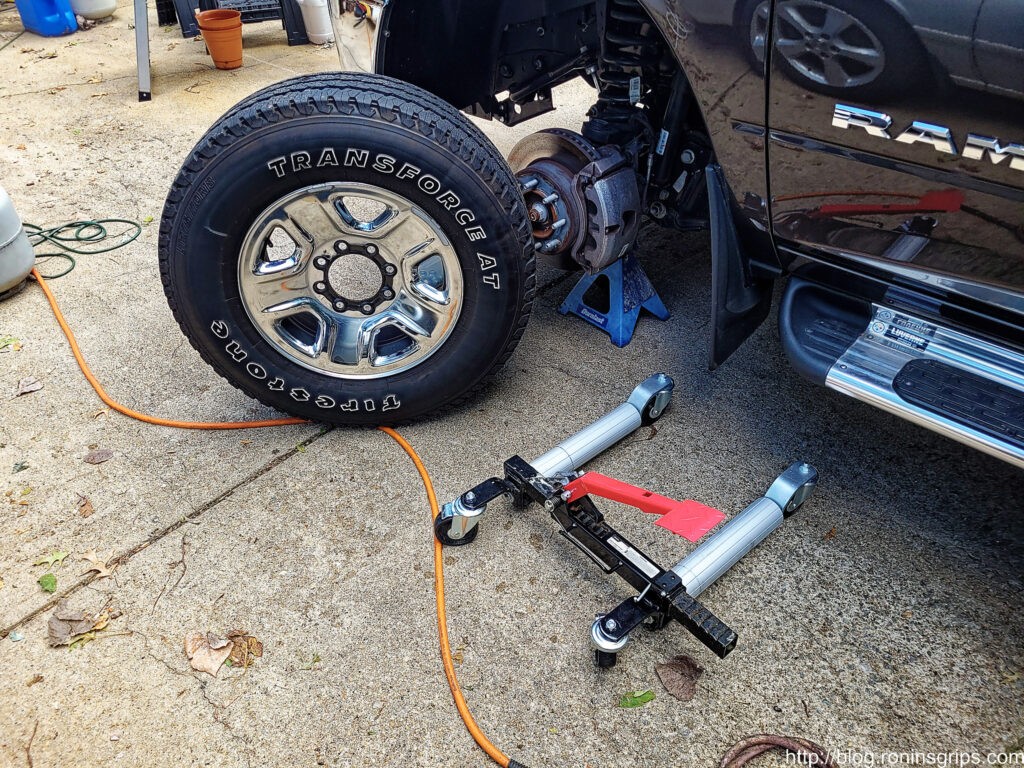
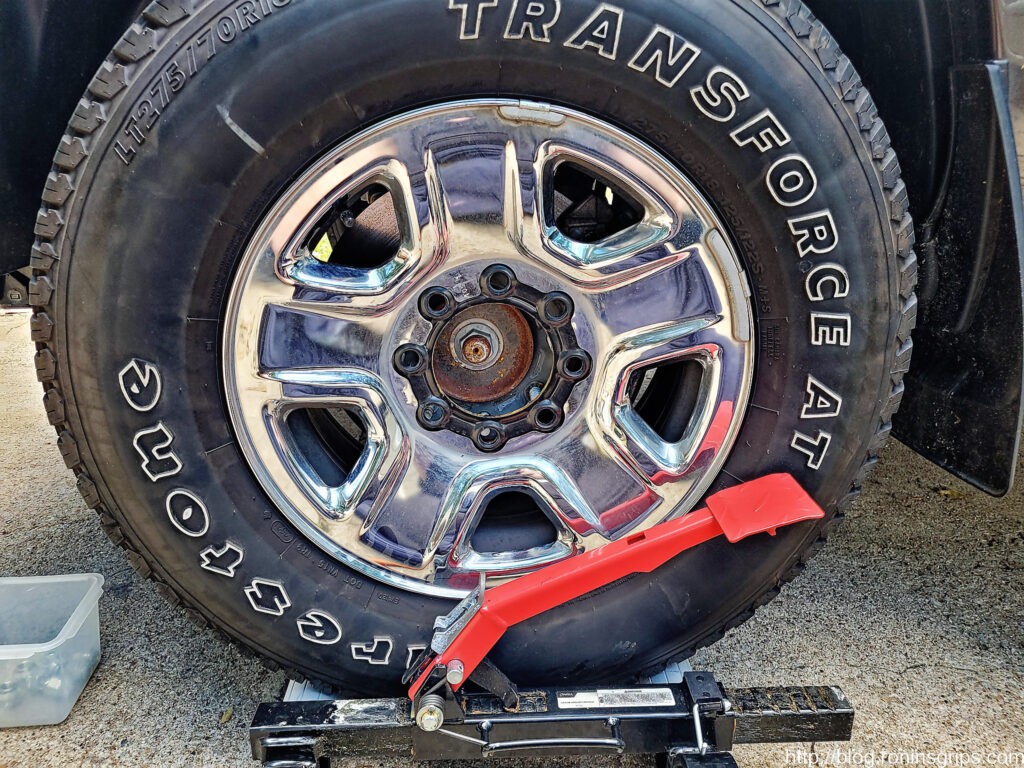
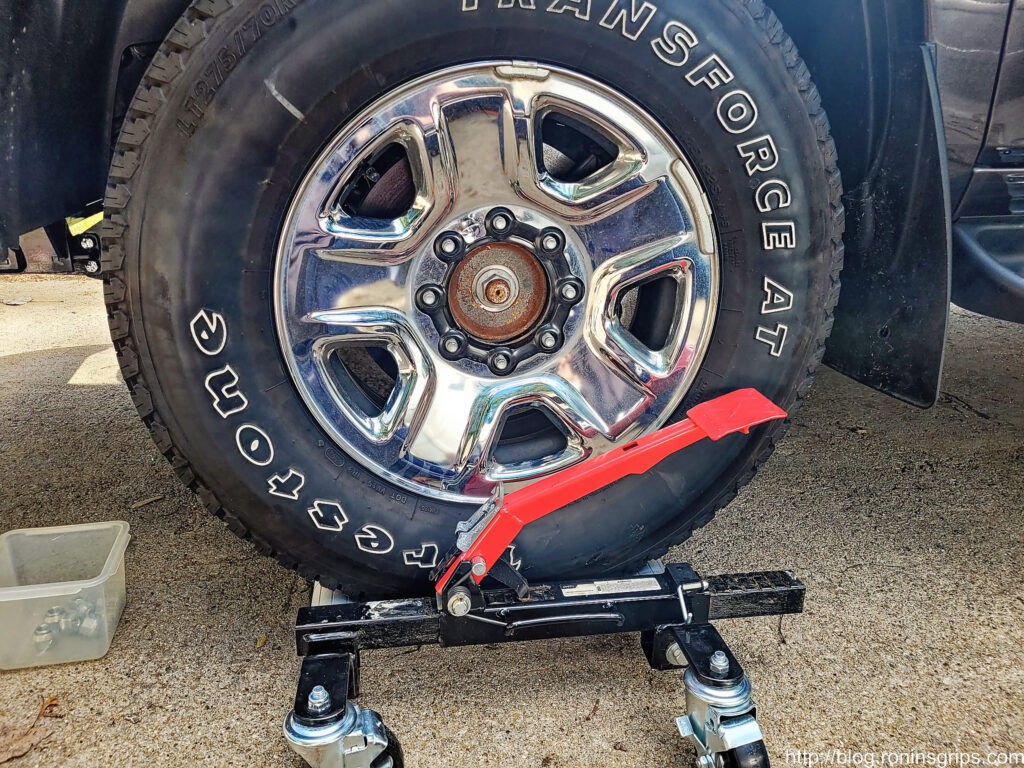
So, in hindsight after actually using the dolly, it really doesn’t take much actual lifting distance to get the tire into place. When I jack up any vehicle, I typically only lift until the tire is 2-4″ off the ground after I put the jack stands in place – so the gap between the floor and the bottom of the tire is not huge. I also realized you can go with just about any of these jacks – you don’t need super heavy duty because the weight of the tire is relatively small. Just read the review for whatever before you buy it.
Additional Details For Fifth Gen Ram 2500 Owners
By the way, in case you are trying to find the rotation pattern, it is a reverse cross meaning the front driver’s side goes to the back passenger side. The front passenger side goes to the back driver. The two former rear tires move straight up – rear driver to front driver and rear passenger to front passenger.
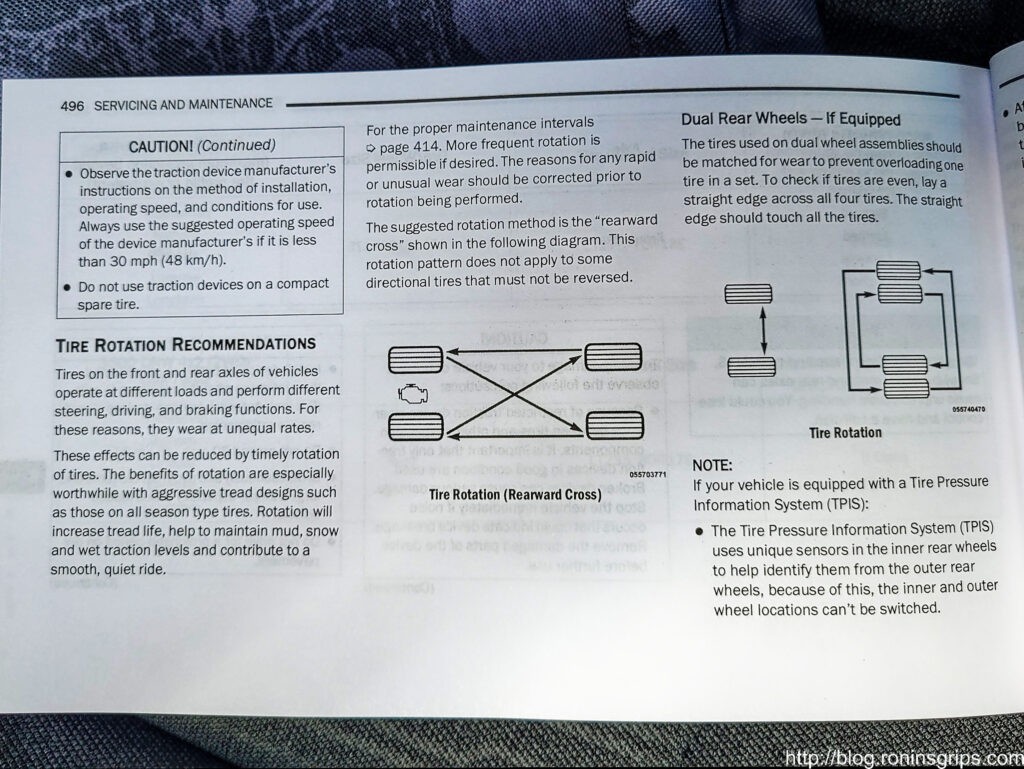
If you are looking for the lug not torque spec, it is 130 foot pounds for cone lug nuts – mine had cone lug nuts. If you have flanged lug nots, it is 140 foot pounds.
On the topic of torquing the nuts down, I start mine by hand to avoid cross-threading the nuts and then I run them in quickly with my impact wrench using a torque limiting “torque extensions” – these extensions work with impact wrenches and twist at a predetermined torque but get weaker with time so they are great for bringing the nut down to the rim but not for setting the torque. I do the final torquing down with a 1/2″ torque wrench. Do NOT keep tightening with the impact wrench or bad things may happen such as cracking your rim.
Lastly, the Tire Pressure Monitoring System (TPMS) will learn where the tires are automatically. Note, you can’t change the minimum tire pressures for the front and rear without going to the dealer or knowing how to re-program the appropriate computer settings. At least, I can’t in my Tradesman. If you can in another model, that is something I don’t know about but count yourself lucky – I wish I could.
In Summary
The car dolly idea to do the lifting and positioning really paid off and now I can do the tire rotations safely and easily. I hope this helps you out.
2/19/23 Update: It’s still working great. This is one purchase I am very happy with.
Note, I have to buy all of my parts – nothing here was paid for by sponsors, etc. I do make a small amount if you click on an ad and buy something but that is it. You’re getting my real opinion on stuff.
If you find this post useful, please share the link on Facebook, with your friends, etc. Your support is much appreciated and if you have any feedback, please email me at in**@*********ps.com. Please note that for links to other websites, I may be paid via an affiliate program such as Avantlink, Impact, Amazon and eBay.