A fellow asked me the other day how I can run my shop Ingersoll Rand (IR) 2340 compressor, which is an oil lubricated 60-gallon compressor, in the winter in my unheated shop. The reason he asked is that as the compressor gets colder and colder, the oil gets thicker and thicker. The end result is that many compressors will not even start below 32F (0C) – the motor tries to spin the air pump, there’s too much resistance, the motor draws too many watts and trips the breaker… or burns out the electric motor. Because of this, many air compressor companies will tell you not to run your compressor when it’s below freezing. I’m going to tell you what I do and you can decide what works for you.
I’m sure you’re wondering why I just said that last part and it’s because I will not be liable for any problems you may have. I’m going to tell you what I do, or have done, and then you need to do some research, conduct some tests and decide what works for you. |
Run synthetic oil – not conventional oil
The first thing I will tell you is to run a good synthetic compressor oil and not the basic Petroleum 30 weight oil that probably came with your compressor. I use Ingersoll Rand’s All Season Select Lubricant because I bought it in bulk a few years back. It’s pretty good but you do have other options as well. Note, it does need a crank case heater to not trip the 30A breaker my 2340 is connected to when it gets really cold (down in the teens or lower).
Another option is moving to the thinner 10W30 Mobil 1 Full Synthetic engine oil in your compressor. I did this some years back with a Husky compressor that I eventually replaced with the bigger IR unit I have today. Some guys go even thinner to 5W30 but I have a hard time recommending really thin stuff like 0W-whatever but there are definitely guys out there who do it on smaller compressors – I’m just saying that I would not do so personally. Note, we are talking about full synthetic oils here and not regular engine oil.
Regularly change your oil
If you have never changed your oil or don’t follow the maintenance schedule of your compressor and oil combination, you really need to. Contaminants and what have you can make it harder for the motor to turn the pump over – even in good weather let alone cold weather.
Run heating pads on your pump
A trick I learned some years ago for stationary compressors is to put one or two of the small oil pan heaters on the pump alongside the oil reservoir. I run one Kat’s 24025 25 watt heating elements that measure 1×5″ on each side of my pump. No more tripped breakers for me.
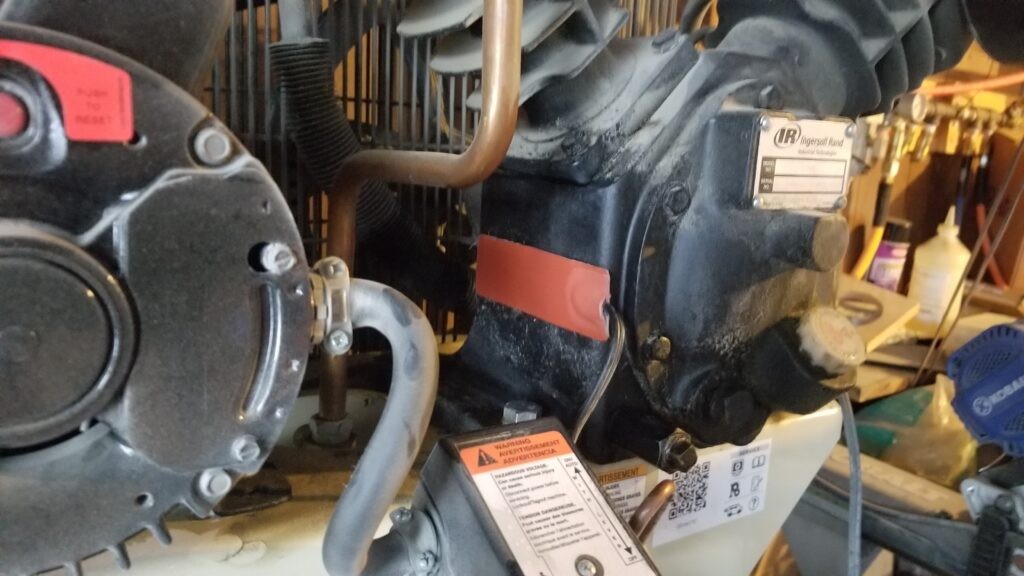
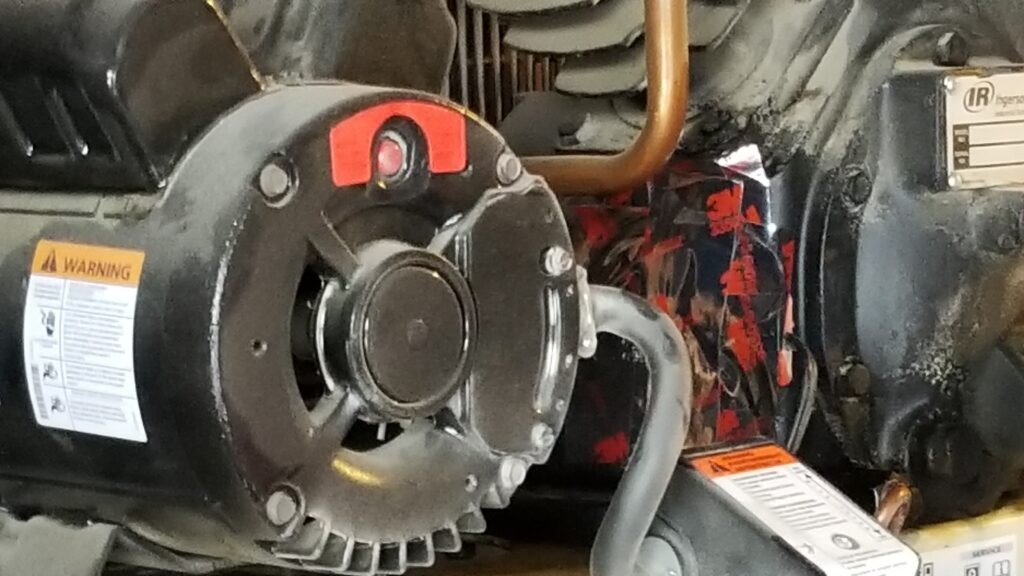
Be sure to keep your tank drained
Condensation is more of a problem in the winter. The relatively warm moist air can condense on the walls of your tank and then go through your air lines causing your tools to freeze up. It usually happens when the weather really sucks and you need the tools the worst.
Start With No Load
One trick to try in a bind is to start with little to no load. In other words, empty the tank so the motor isn’t fighting both thicker cold lubricant and pressure in the line as well.
The thought process is that your bleed off valve that empties the line from the pump to the tank and to the pressure switch might be frozen up from moisture or bad/failing. For example, the switch on my IR 2340LF-V is a real cheaply made POS – I’m miffed about the quality and am not going to mince words about it. I’ve replaced it once already and as of this writing it’s starting to fail again about a year later after the last time and I already have a replacement on hand.
Also, one trick I learned from an old timer is to add more line or a reservoir between the pump and the tank so the motor can get a running start before it encounters resistance. Here’s a post I did some time back about that.
Conclusion
You definitely can run an oil lubricated compressor in the cold weather. It just takes a little planning and preparation is all. It’s my hope that the above gives you some food for thought and you can then research what will work best for you. You’ll notice that if you do some Googling around, you’re in good company with a ton of other folks trying to figure out what to do as well.
I hope this post helps you out.
Note, I have to buy all of my parts – nothing here was paid for by sponsors, etc. I do make a small amount if you click on an ad and buy something but that is it. You’re getting my real opinion on stuff.
If you find this post useful, please share the link on Facebook, with your friends, etc. Your support is much appreciated and if you have any feedback, please email me at in**@*********ps.com. Please note that for links to other websites, we are only paid if there is an affiliate program such as Avantlink, Impact, Amazon and eBay and only if you purchase something.