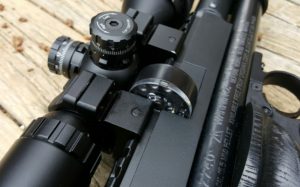
My magazine was a bear to pull out from my CP1002 BNM breech. I talked to Sergei at BNM about the tight fit and told me that they keep they keep their tolerances tight on purpose. He would rather things be tight vs. loose and that makes sense to me. So if your Marauder magazine is a bear to push in and out of the breach, a tiny bit of fitting is needed. The bottom of the Marauder magazine can be lightly sanded to allow magazine to be inserted easier. It probably is not the front to back dimension that you need to worry about so try the following first.
All you need to do is get some 320 grit sand paper, rub the bottom lightly, evenly and test. You just need to do the part that slides into the receiver. 320 was all I needed it took off enough to do the job gut also left a fine enough finish. Another benefit for those of you that may be nervous is that it can only take off a small amount of material. It will fill fast so with each pass, use another exposed surface of sandpaper. That is why you see two ends used on the second photo.
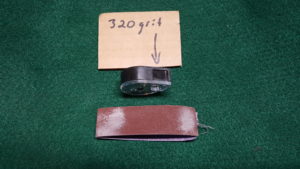
For mine to fit way better, it was just a tiny amount I had to take off. So don’t go crazy and take off a too much too fast. Literally, do 4-6 rubs, blow it off and test. Do this until it fits. I think I did all three of my mags with just a couple of rounds of sanding and testing each.
I could have sanded it with 400 grit and even gone up to a polish but just doing 320 seemed to work great so I stopped there.
If you find this post useful, please share the link on Facebook, with your friends, etc. Your support is much appreciated and if you have any feedback, please email me at in**@*********ps.com. Please note that for links to other websites, I may be paid via an affiliate program such as Avantlink, Impact, Amazon and eBay.
Like this:
Like Loading...