The short answer to that question is “No” but then when someone asks if they can use some Picatinny mount on a Weaver rail it becomes “It depends”. Why is that?
Well, the Picatinny rail does have a true military specification – “MIL-STD-1913″ that lays out the details but nothing like that exists for Weaver rails – when writing this post, I did some digging and I can’t find an authoritative width of the rail, the recoil slot is about 0.180” but their spacing, number and depth can all vary.
The reason that Weaver rings and mounts can typically fit a Picatinny rail is that the recoil slots are 0.206″ wild and spaced 0.394″ apart. However, if you are using rings that were on a Weaver rail, while the bolts or recoil bars may fit the Picatinny slots, the spacing between the mounts may need to be adjusted.
There are plenty of posts out there with more details but I would tell you to only use Picatinny rails and mounts going forward if at all possible. The reason is that because there is the published MIL-STD-1913 specification, the interoperability of parts from different vendors is far, far more likely.
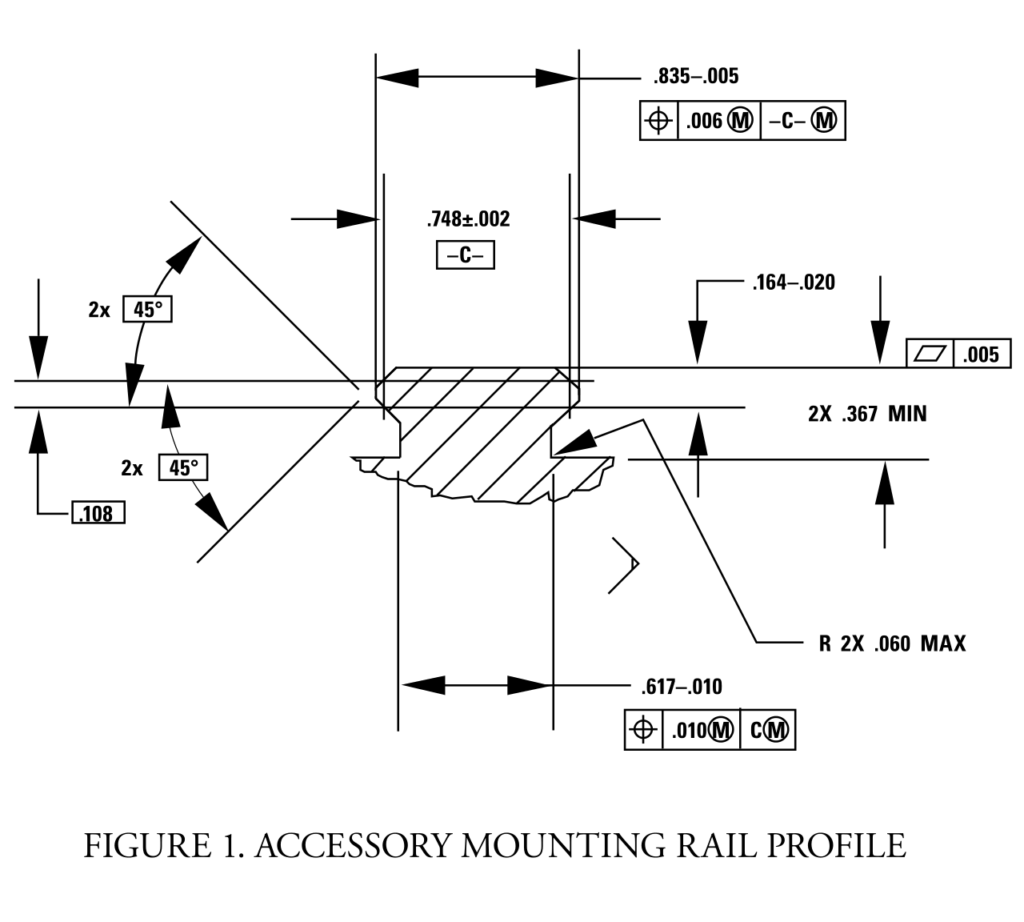
It is from the Wikipedia entry about the MIL-STD-1913 Picatinny Rail.
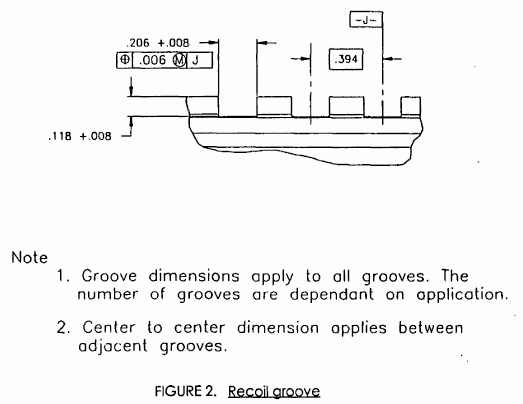
It is from the Wikipedia entry about the MIL-STD-1913 Picatinny Rail.
I was unable to find a US DOD direct link for the MIL-STD-1913 but I did find two sites hosting scanned copies – BiggerHammer and EverySpec
Some Photos
What inspired me to sit down and write this is my working on a 5.56 Polish Beryl right now. The actual Beryl optics rails are a both rare and cost a fortune. While there are Picatinny versions out there, I have two of the older Weaver rail design they started with and am lucky that my ADM and Vortex mounts all surprisingly fit – it’s always nice when things work out in a good way.
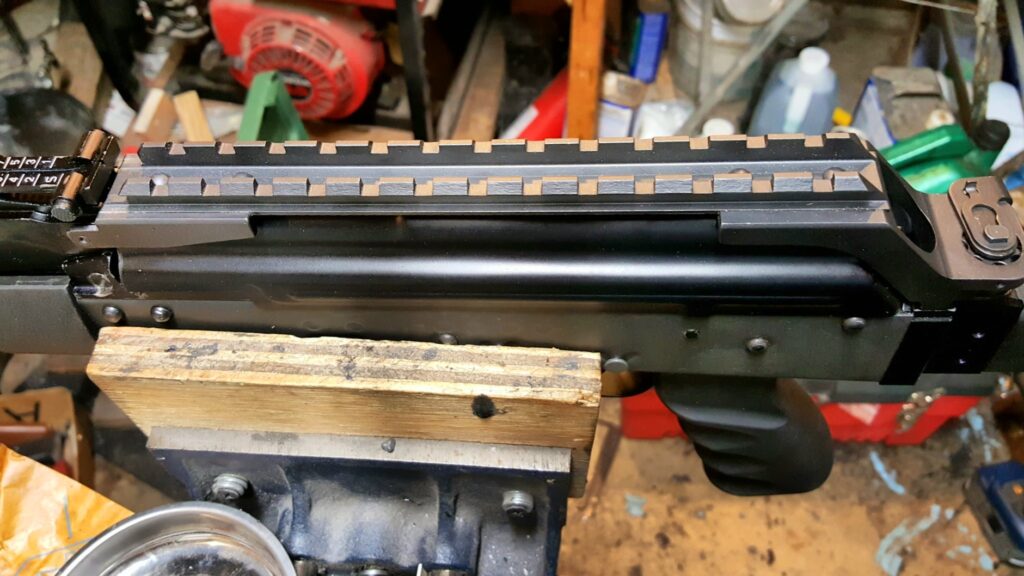
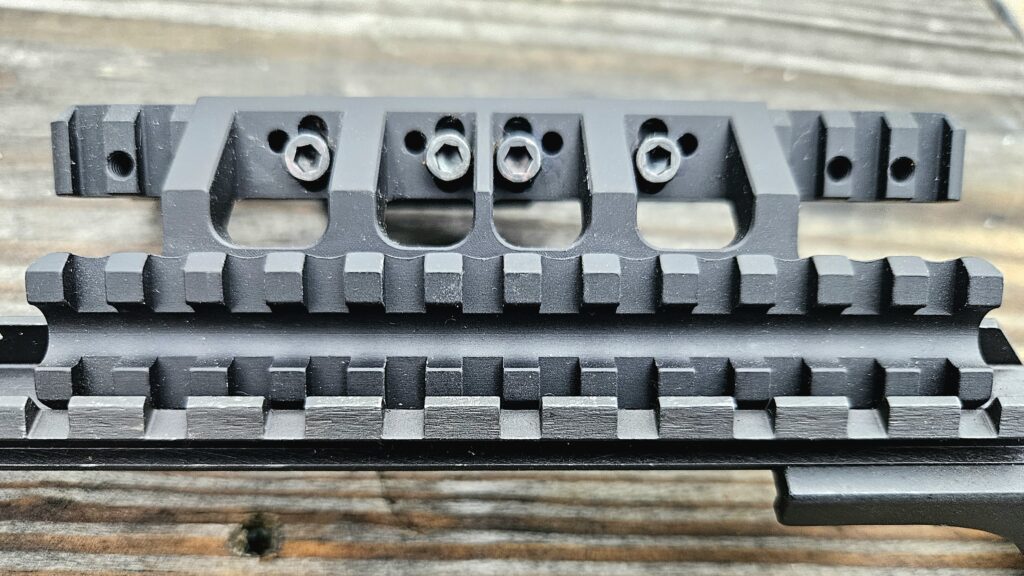
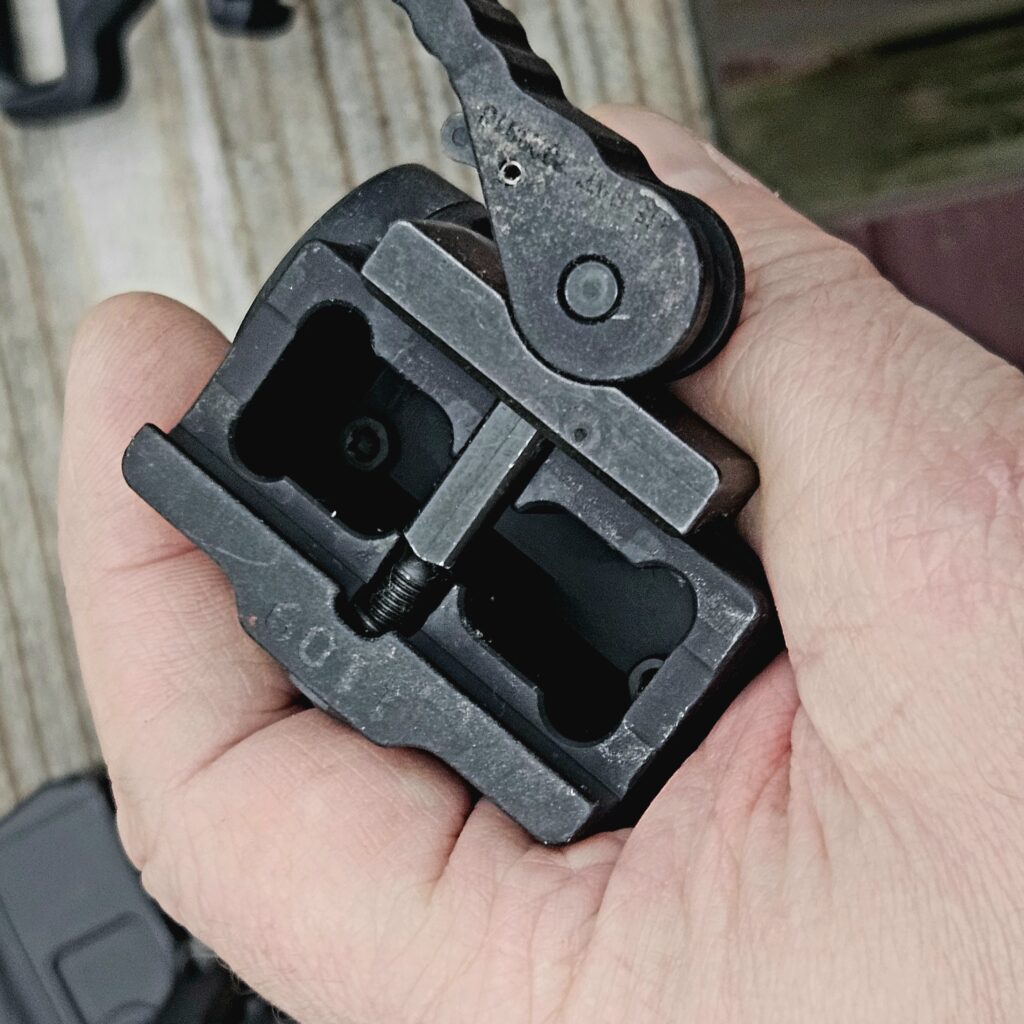
In Closing
Weaver and Picatinny rails are different. In general, you can use Weaver mounts on a Picatinny rail but you may not be able to put a Picatinny mount on a Weaver Rail.
In my case, I got lucky and could mount the red dots no problem. A mount with two screws/contact points may or may not line up – that will just depend on many factors in terms of the spacing between the recoil bars, size of the bars, etc.
Bottom line, go with Picatinny rails and mounts going forward to maximize your ability to move components around.
For more information:
- https://www.shootingtimes.com/editorial/optics_st_railcrazy_200907/99242
- https://www.biggerhammer.net/picatinny/
- http://everyspec.com/MIL-STD/MIL-STD-1800-1999/MIL-STD-1913_17705/
- https://bulletin.accurateshooter.com/2009/02/tech-tip-picatinny-vs-weaver-rail-specifications/
- https://www.army.mil/article/137761/picatinny_engineer_recognized_for_developing_venerable_picatinny_rail
- https://en.wikipedia.org/wiki/Picatinny_rail
- https://en.wikipedia.org/wiki/Weaver_rail_mount
Note, I have to buy all of my parts – nothing here was paid for by sponsors, etc. I do make a small amount if you click on an ad and buy something but that is it. You’re getting my real opinion on stuff.
If you find this post useful, please share the link on Facebook, with your friends, etc. Your support is much appreciated and if you have any feedback, please email me at in**@*********ps.com. Please note that for links to other websites, I may be paid via an affiliate program such as Avantlink, Impact, Amazon and eBay.