In the first post, I documented my favorable first impressions of the SDS Lynx 12 shotgun. After posting, at least 10 gentlemen have come forward stating how much they like their Lynx 12 shotguns and nobody reported any problems. In this post, I’ll write about taking the shotgun apart in order to install my planned customizations, which will be in the next post.
Palmetto State Armory has SDS Lynx 12 gauge shotguns for sale – click here to go to their order page. |
Call me old school, but the first thing I did was to read the manual 🙂 The next thing was to hose down the hole shotgun and wipe it down to remove all the odd smelling rust preservative. I really didn’t care for the tacky feel to be there while working on it. Once removed, I sprayed on Rem Oil to prevent rust while I was working on it. Rem Oil is nice and thin and doesn’t have too much of a smell. It’s my go to for situations like this. If you do remove the preservative, just be sure to apply whatever oil or rust inhibitor you prefer.
Removing the Dust Cover and Recoil Spring
The dust cover comes off by pushing the release latch (the little button that sticks up) on the recoil spring and pushing the whole assembly forward while lifting the dust cover up and off the receiver.
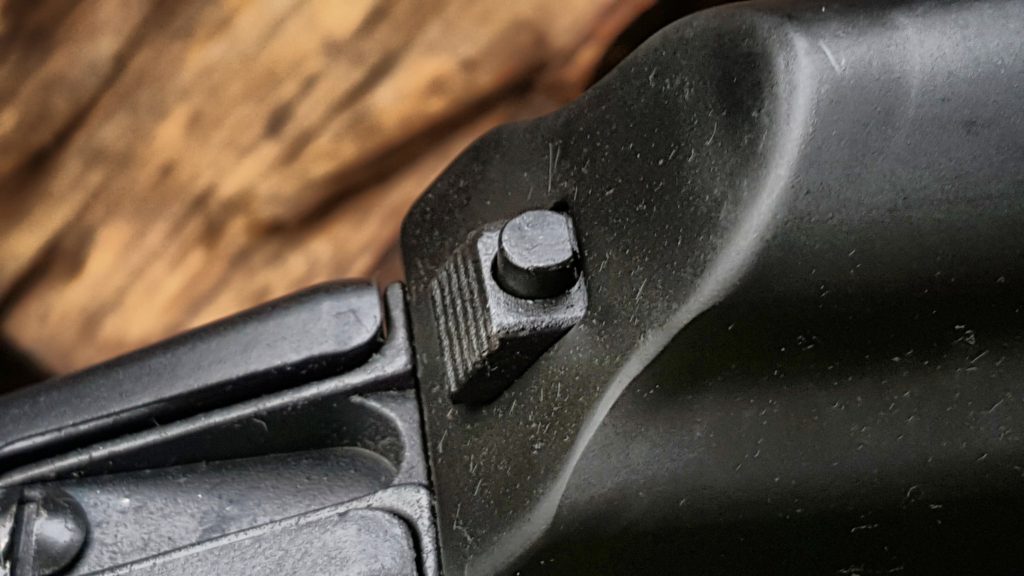
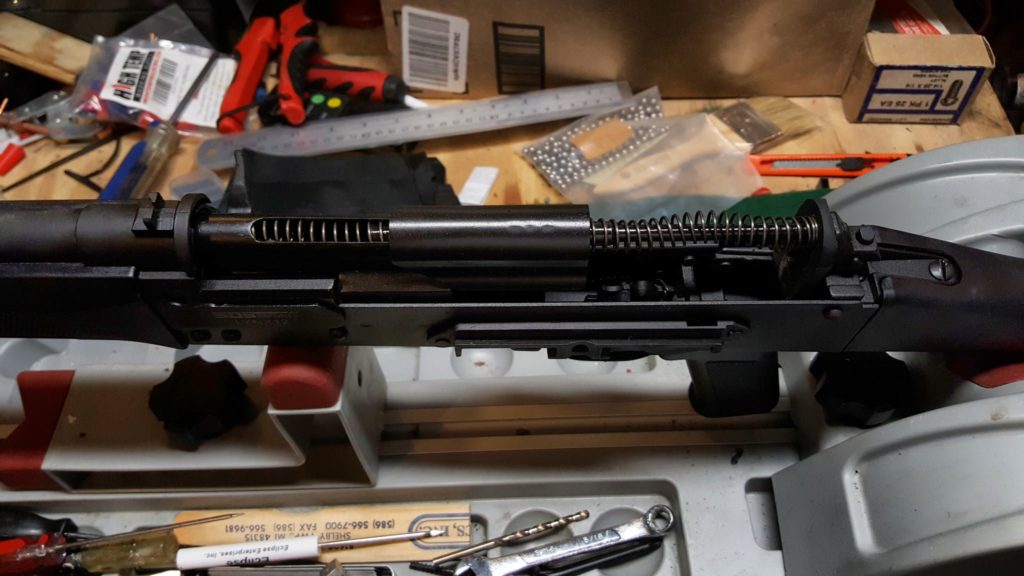
You’ll notice I have the Lynx sitting in my Tipton vise. I’ve had it for years and it really makes working on long arms way easier.
With the dust cover off, you can get a good look at the recoil spring assembly. Some guys will call this the operating spring or the return spring but basically it absorbs the energy of the bolt carrier assembly coming back after firing and then when the spring has enough energy, it pushes the bolt carrier assembly forward to then cock the trigger and strip a round off the magazine and go back into battery.
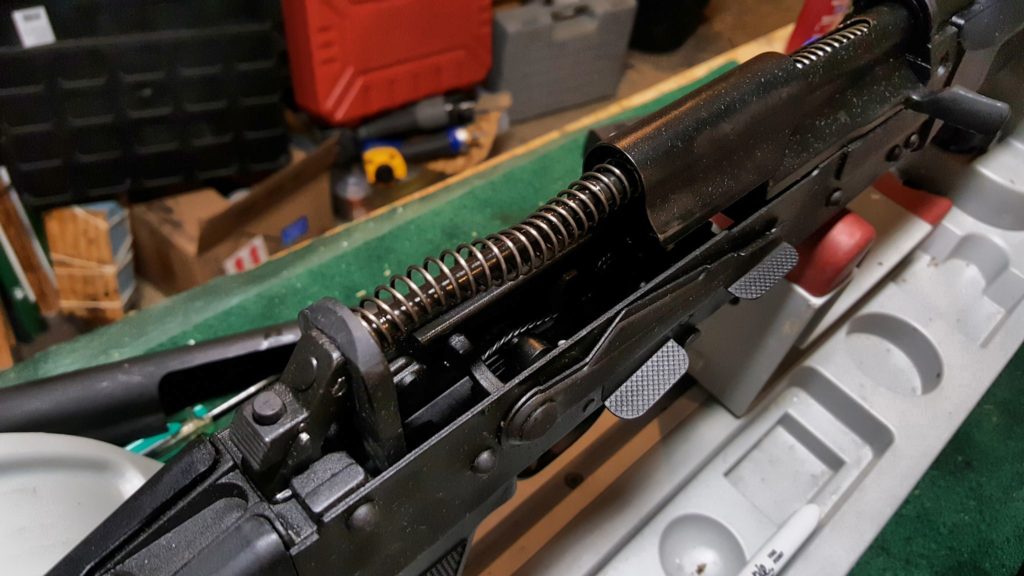
Compared to a regular AKM, you will notice the release latch and the rubber buffer assembly at the rear. I find the use of a buffer interesting. Normally the spring should absorb the energy and my bet is that the designers put it there in case the user either adjusts the gas regulator such that the system is over-gassed and the carrier comes back with more force than the spring alone can handle or they put it there just in case of a round that generates more pressure than what the spring can handle but the gas regulator doesn’t exactly have the right setting — imagine needing a gas setting of “3.5”. At the third position there is too much gas but at 4 there is too little. I have little doubt it is a good idea. I’d recommend to keep a spare buffer on hand and inspect the one in the shotgun regularly. It ought to last a long time under most conditions but the buffers are dirt cheap.
To remove it, push forward on the rear part that normally protrudes from the dust cover. It should slide forward in the slot that holds it on the trunnion until it is free and you can then lift up and pull back to remove the assembly from the bolt carrier and shotgun overall.
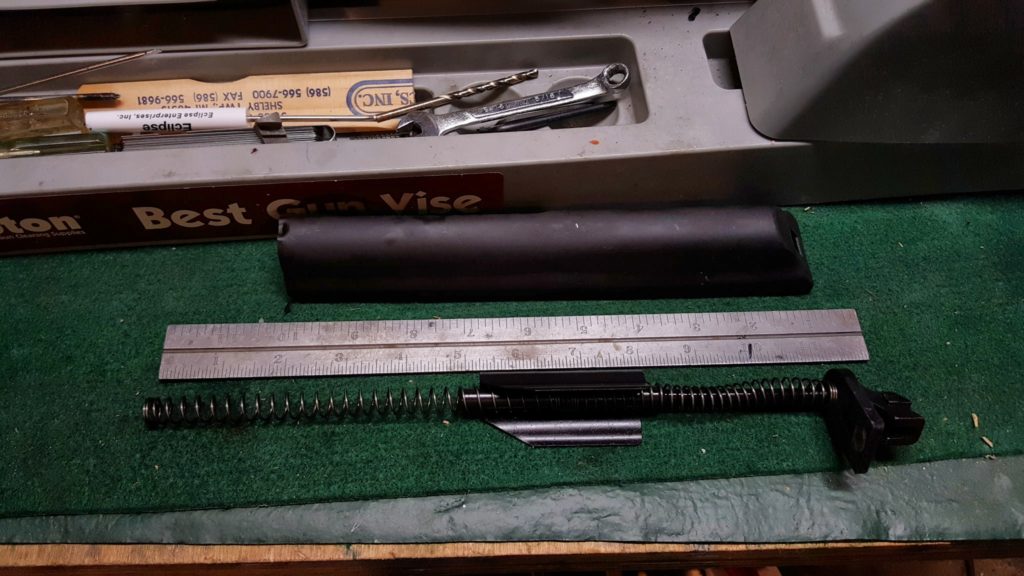

You will also note that the designers made the recoil spring assembly two parts – the rear is a tube like an RPK or older milled AKs with one spring. There is then an additional cover that rides on that rear tube and normally closes the otherwise enlarged ejection port in the dust cover. In front of that is then a floating spring.
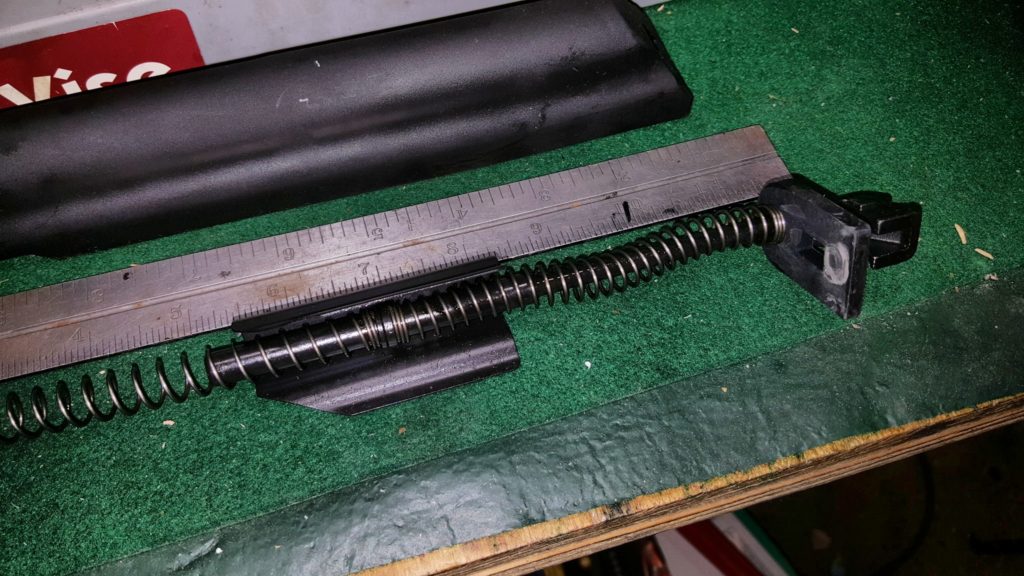
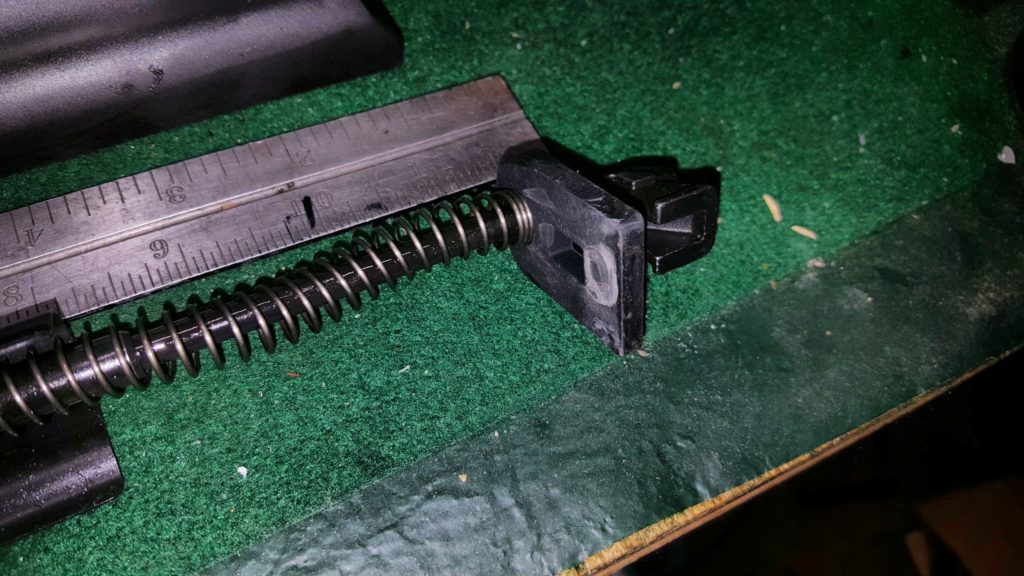
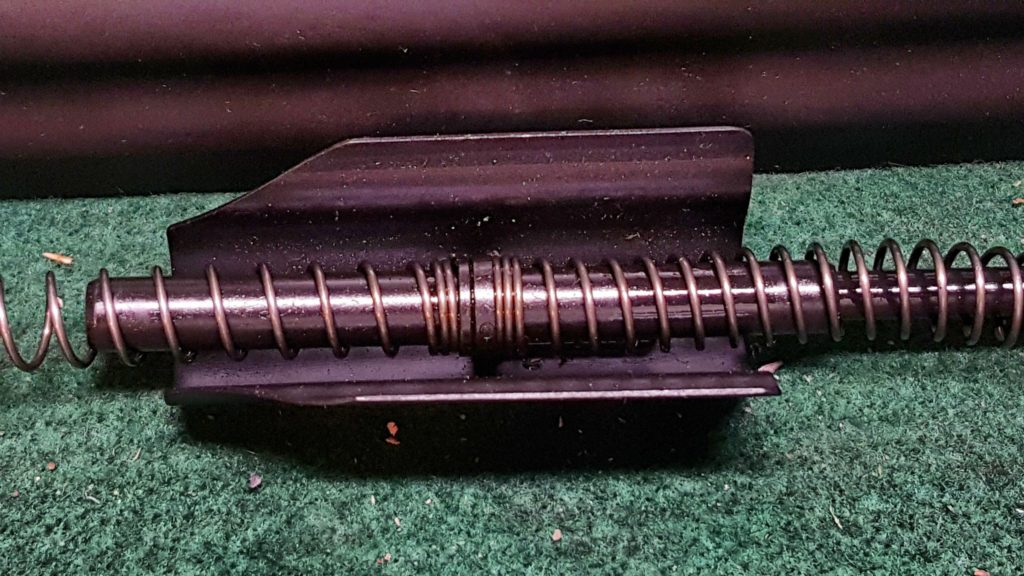
Removing the Bolt Carrier Assembly and Looking Inside the Receiver
First, remove the bolt carrier assembly. It slides to the rear of the receiver and can then be lifted up out of the receiver. Note – it must be fully to the rear or the receiver’s guide rails will retain it.
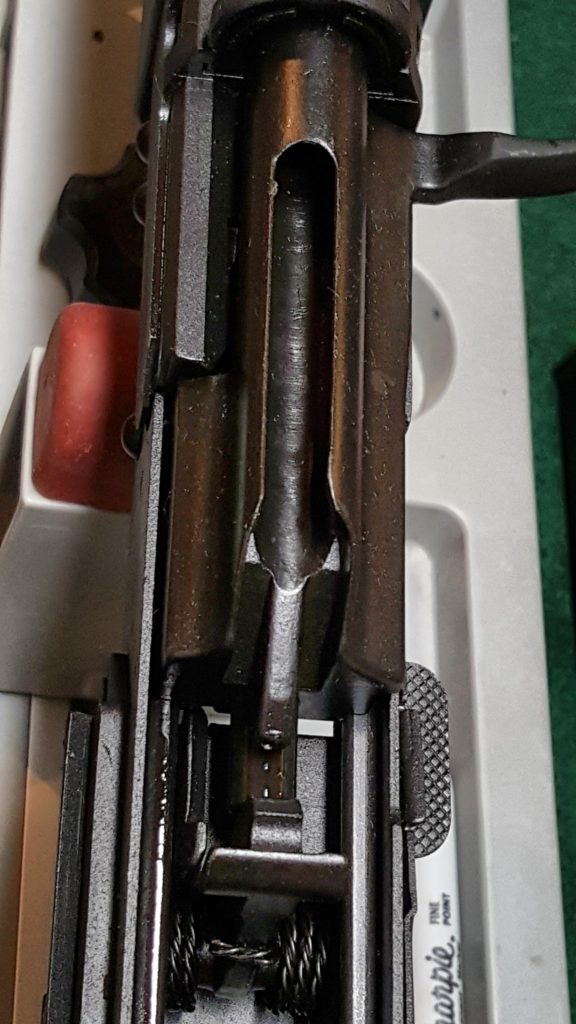
It’s interesting how the bolt carrier is short. In the gas tube, which is pinned in place, is a disc, that some call the “gas puck” or just “puck” which is the gas piston. Unlike an AKM, the gas tube is held in place by the gas tube seat (it reminds me of a rear sight block in a way) that would need it’s retaining pin to be punched out to be removed. When you tilt the shotgun forward and back, you can hear the puck moving back and forth in the gas tube. I didn’t take the gas tube assembly apart but it looks straight forward enough.
The carrier is holding a really massive bolt. It operates very much like any AK – the bolt head has a cam that travels through a slot in the carrier that in turn rotates it into or out of battery.
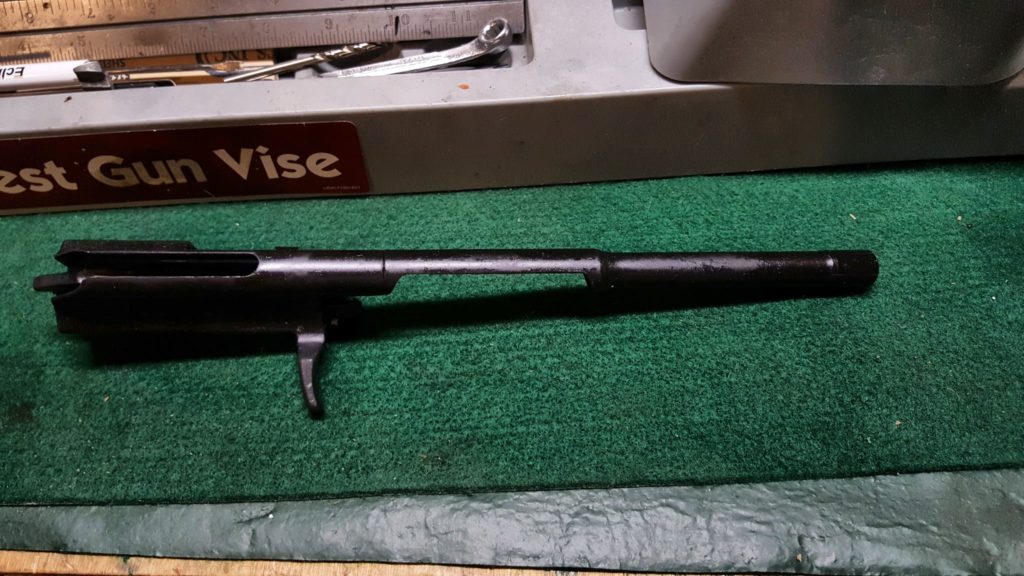
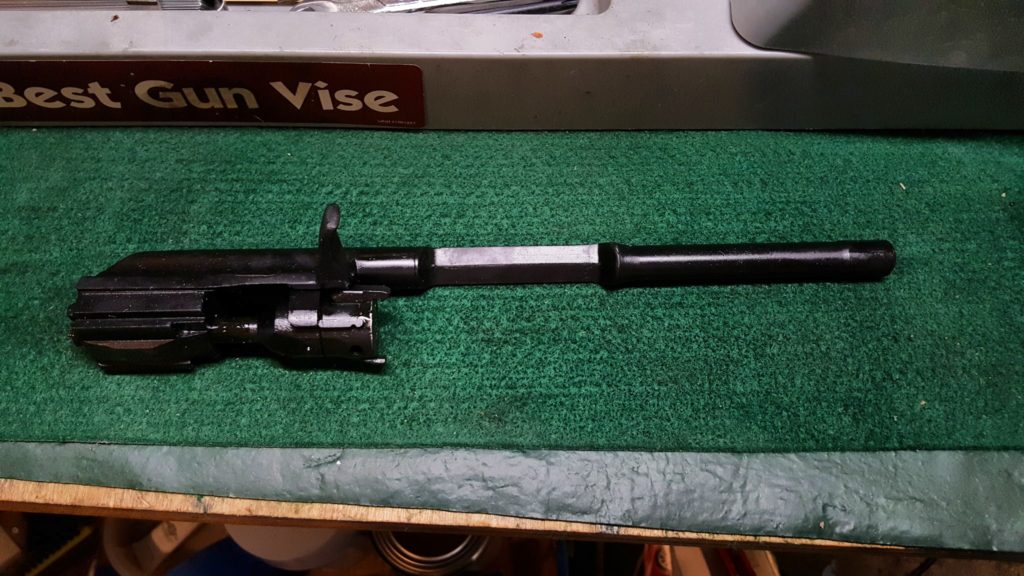
By moving the bolt head to the rear, the cam can be rotates out of the slot and the bolt head then removed from the carrier.
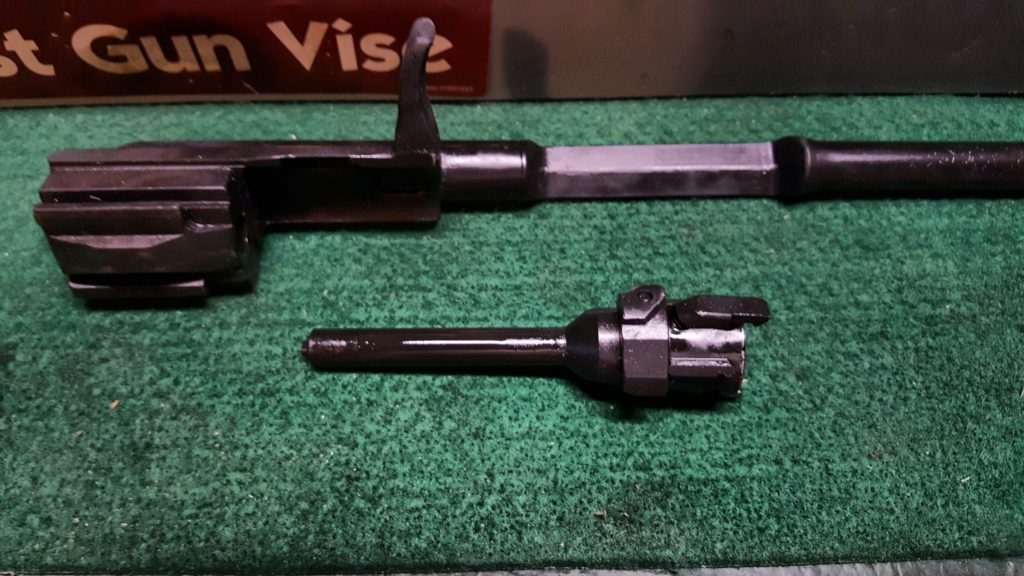
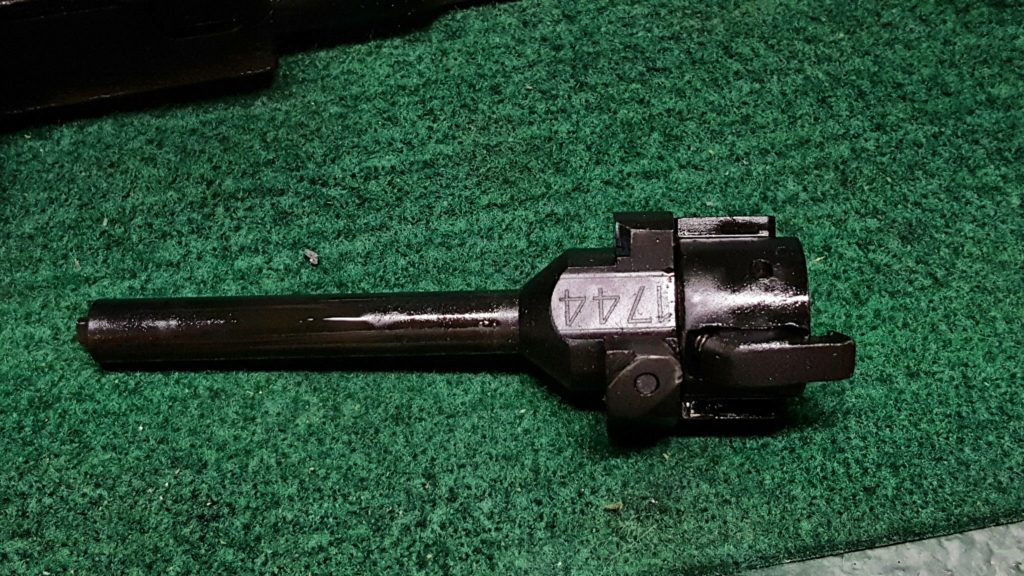
Look at the size of the extractor!
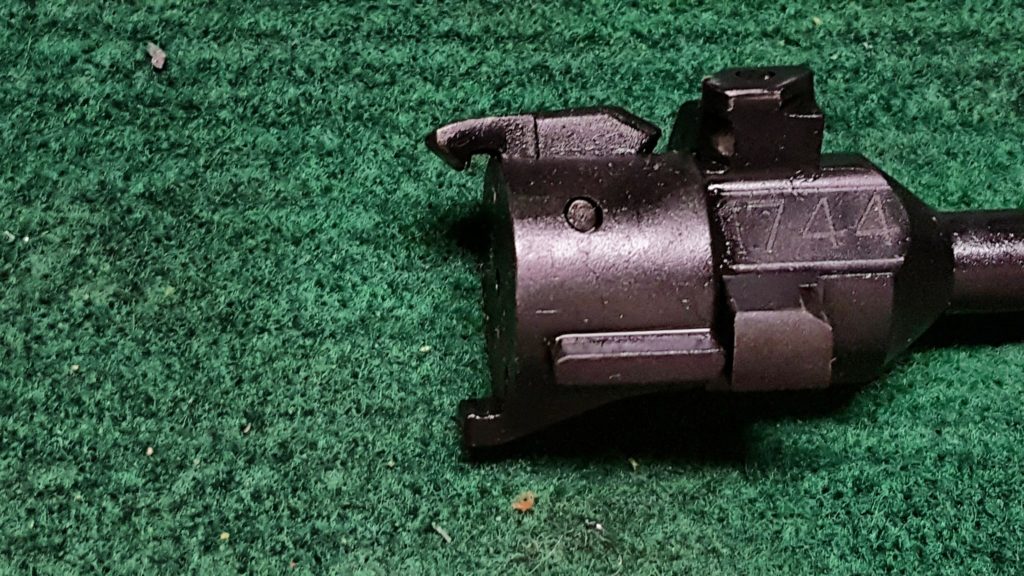
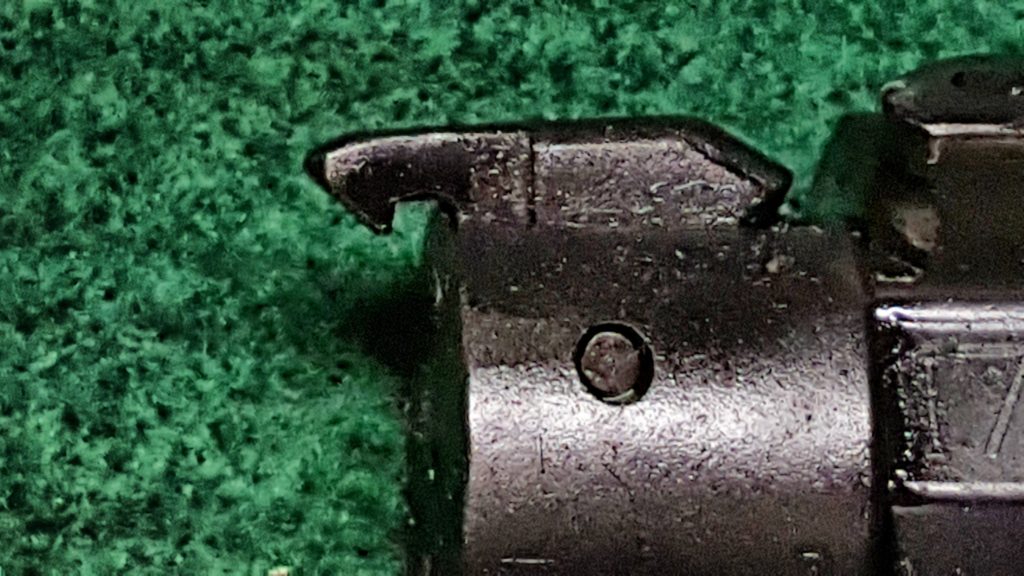
Interestingly, the firing pin has a spring pushing it backward compared to the floating firing pins you normally find in an AK rifle. In this photo you can see the tail of the firing pin pushed out the back of the bolt body by the spring.
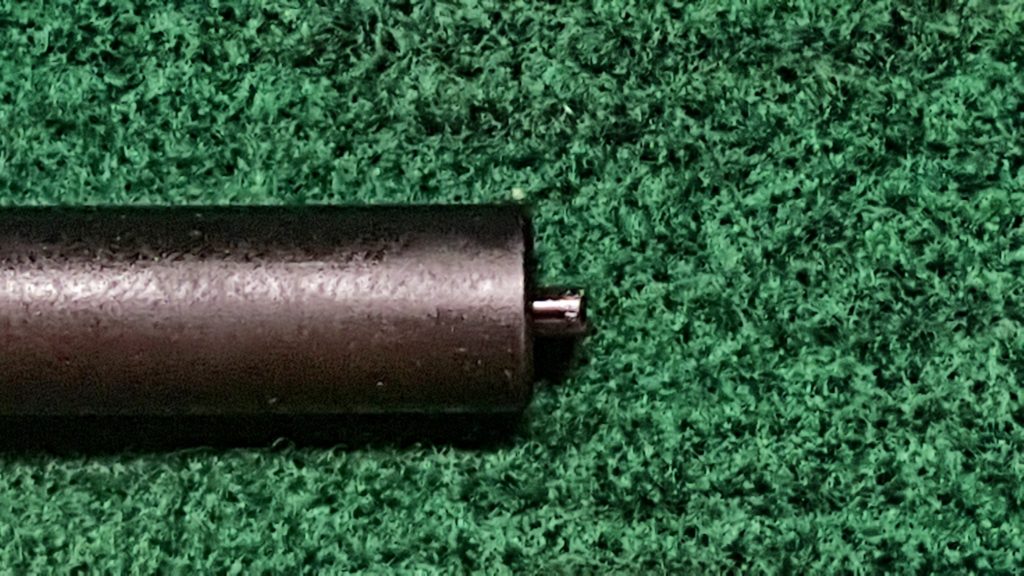
Looking down in the receiver was a very typical looking fire control group. Note, it has been tweaked slightly to work in a Saiga or Lynx so if you want to replace the fire control group you will need to either buy one made for the the Saiga or Lynx or you will need to make some modifications.
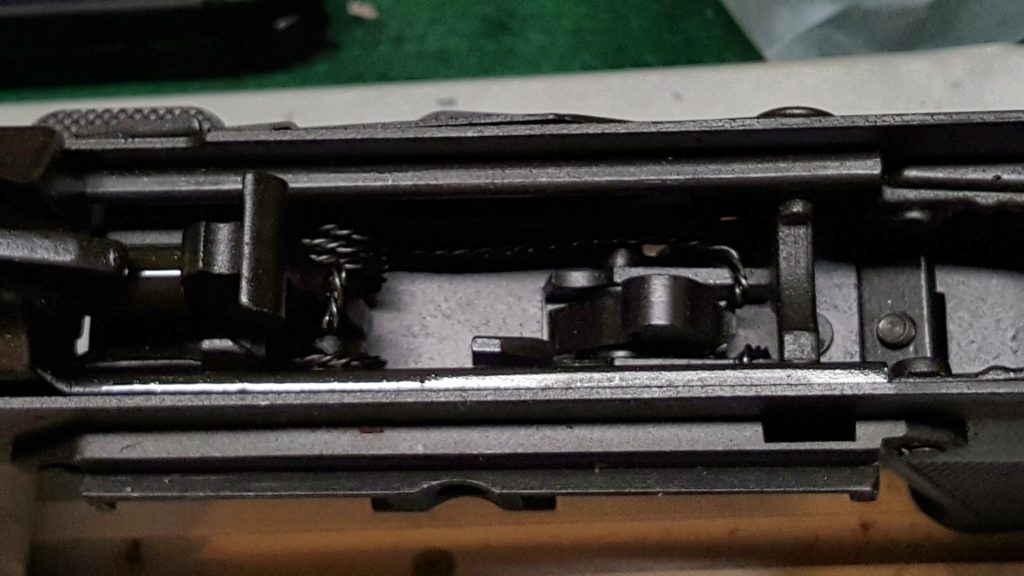
Normally I replace the fire control group (FCG) with a US made set but the Lynx’s trigger is surprisingly decent. Not great, but decent. It was gritty from the parkerizing and lack of use but I figured grease and time could cure that. I may well swap it out in the future but time will tell.
The Pistol Grip
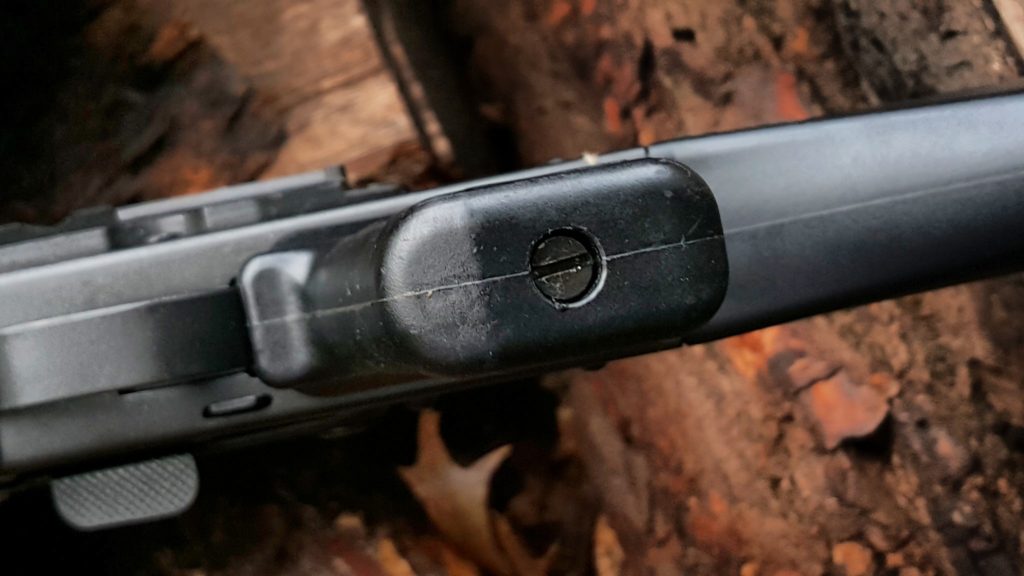
Now I did run into one surprise that I did not expect – see the grip nut below? I figured it would be a regular AKM nut meaning threaded for a 6mm diameter x 1.0mm pitch screw. It’s not. I did not expect this but the grip screw is actually smaller than an AK’s. The screw is actually 5mm diameter x 106mm long. I did not bother finding out the pitch by the way because it would not be staying! Instead, I focused on the hole in the receiver – it was the same size as a normal AKM grip nut. Whew – Problem solved. I would replace it with a beefier AKM nut and one of our high-strength alloy grip screws (I’ll detail that in the next post).
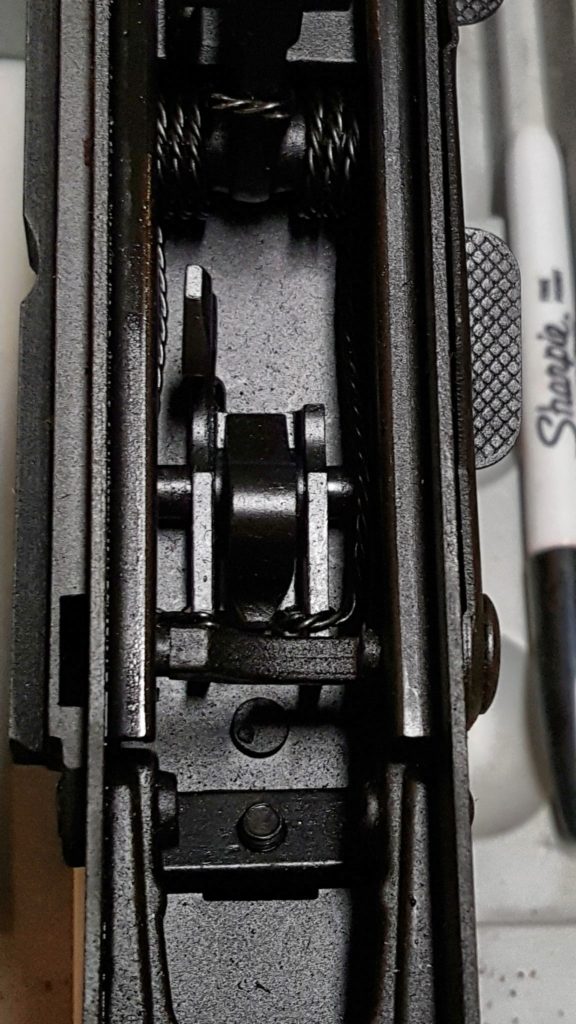
To remove the grip, there is a blade screw head on the base. Simply unscrew it and remove the grip and the grip nut.
Removing the Buttstock
The plastic buttstock is held in place by two machine screws on the top of the rear trunnion. The rear trunnion is an AK-74 forked style with the front portion open. The stock with its lightning cuts on the side harks to the 74 also other than having a recoil pad thicker than what you would find on a 74.
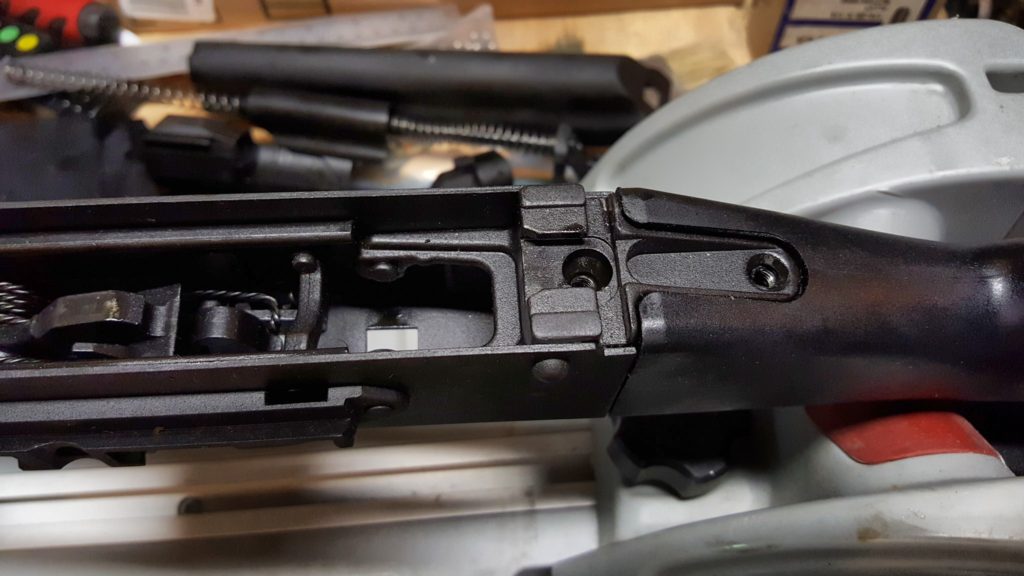
Given how front heavy the shotgun felt, I was not surprised to find out that the buttstock was actually hollow. The Chinese installed threaded inserts for strength. I think that is commendable actually. The fit of the buttstock to the receiver is both well done and very tight. This is what will bear the recoil – the screws are just there to hold it together.
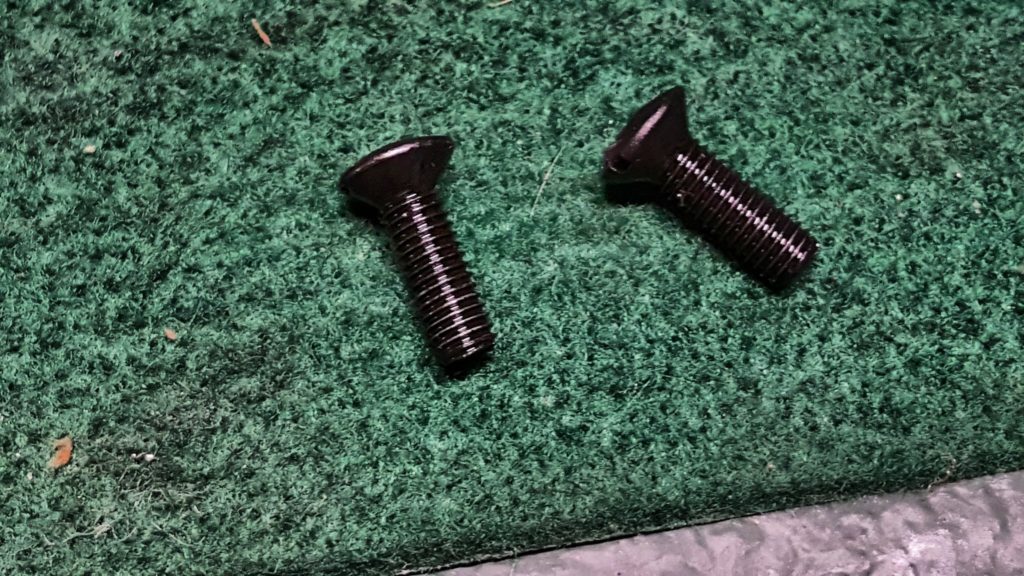
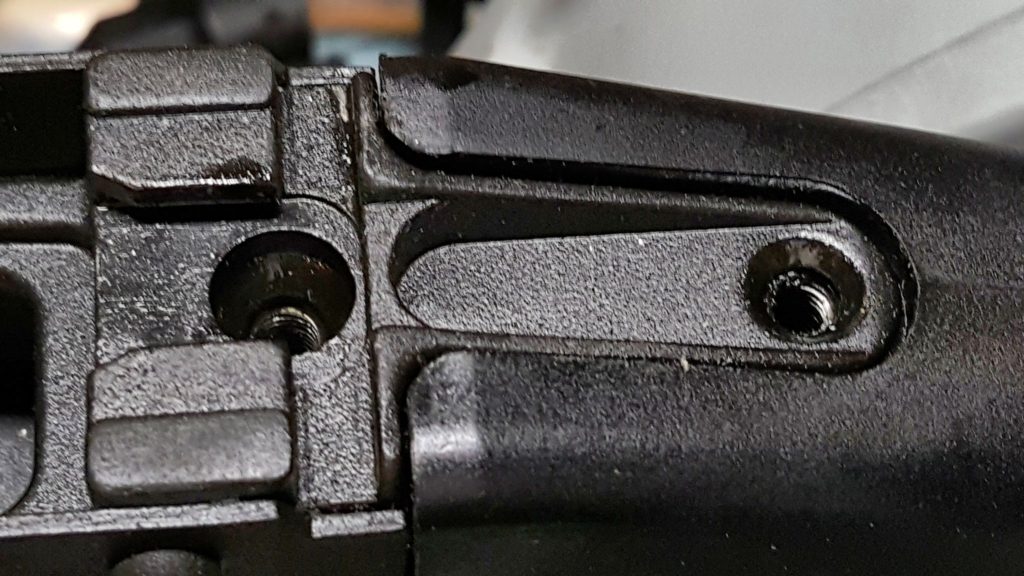
Because of the tight fit, I secured the rifle in my vise after removing the selector lever. I then used a wood dowel and hammer to tap on the lip of the stock to push it backwards out of the receiver. It really didn’t take much force to get it out. For those of you who have tried to get an old varnished AK-47 stock out of a receiver, you know exactly what I mean and the Lynx requires just a small fraction of that.
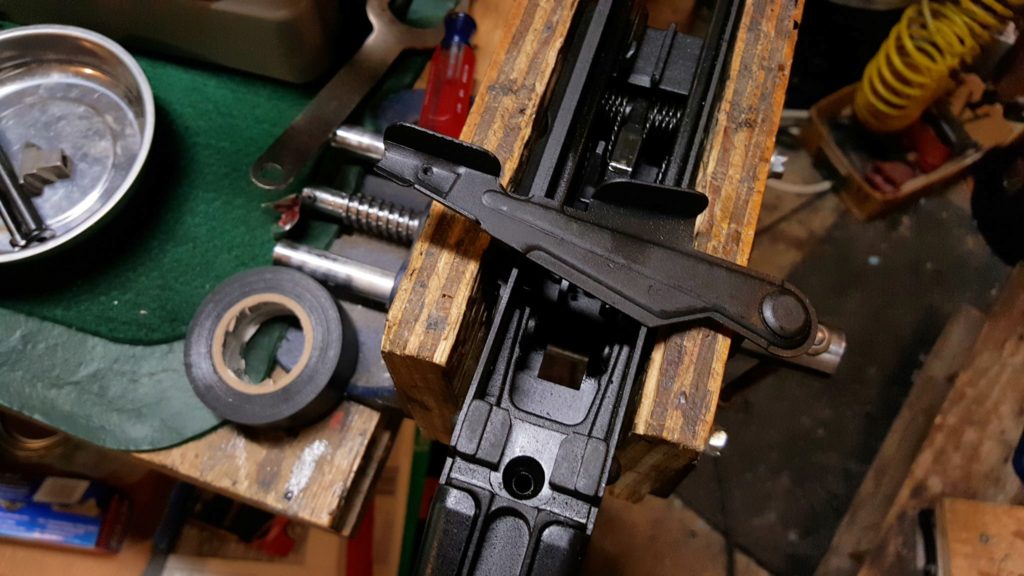
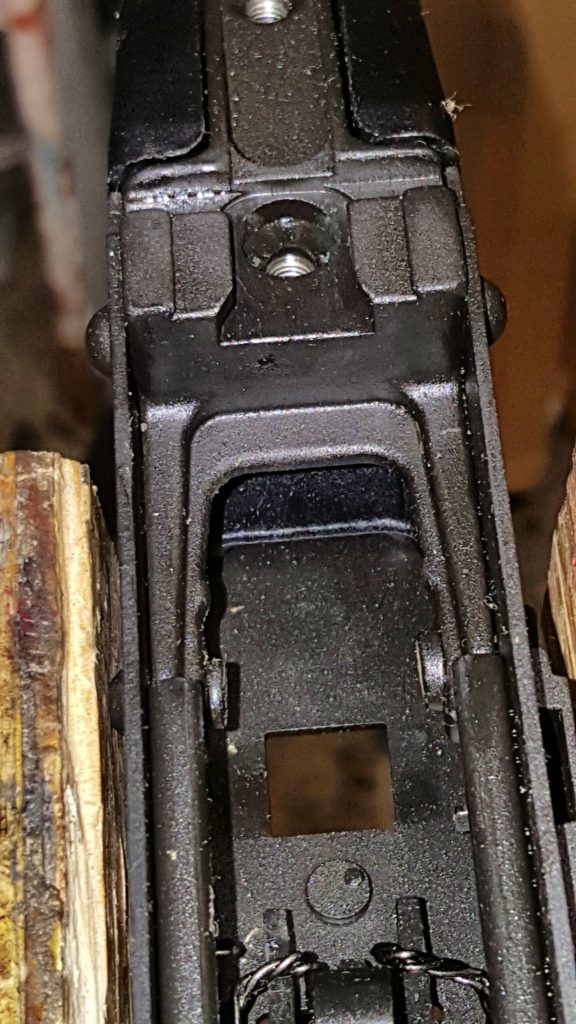
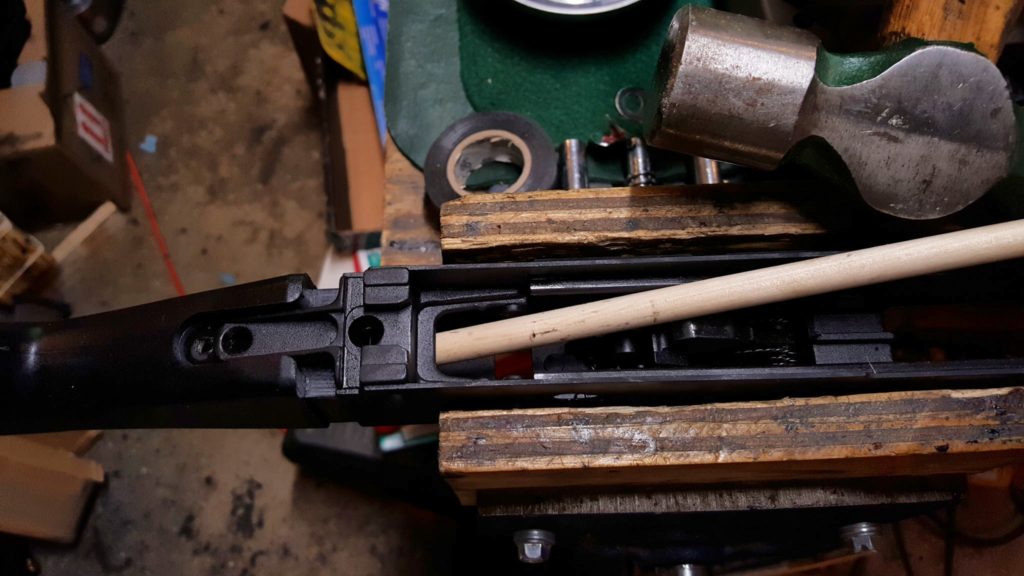
The Forearm
The sporting looking forearm is held in place by a 5mm diameter x 11mm long screw. Unscrew it and push the handguard forward past the gas tube and then pull it off the barrel. Mine was a tight fit so I did need to pull it off the barrel and not just lift. I did use a small piece of wood and a hammer to get it started out of the receiver.
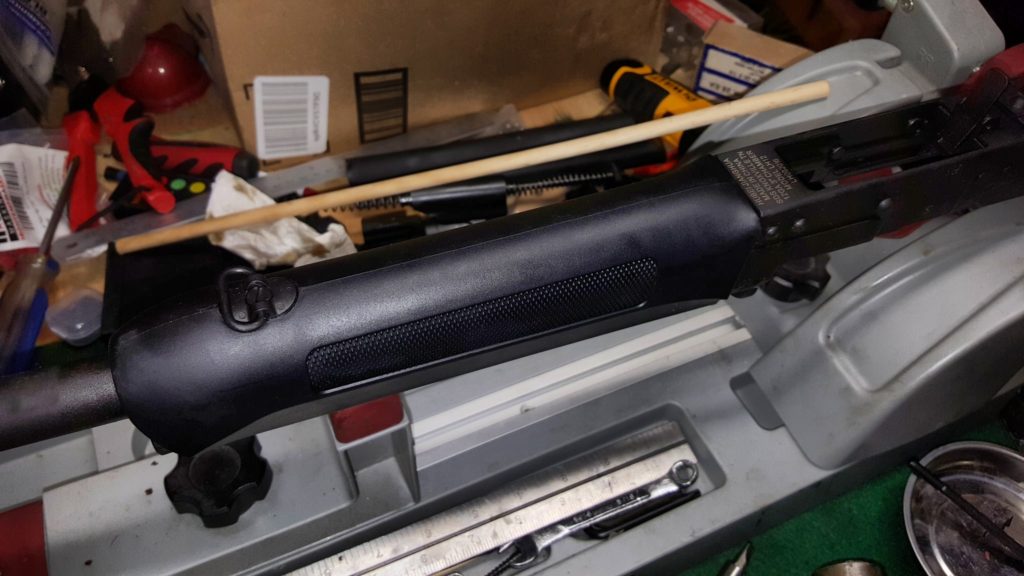
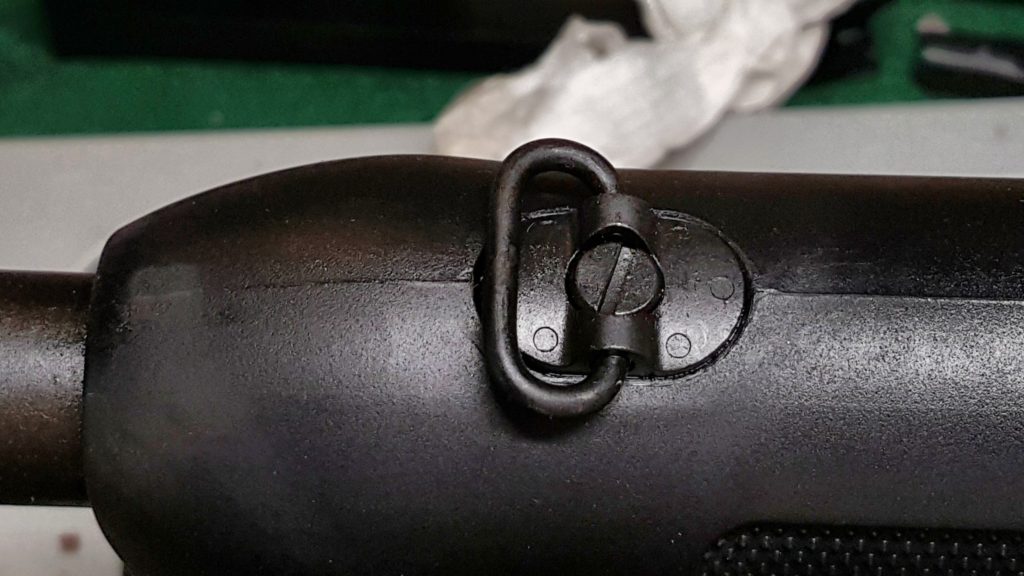
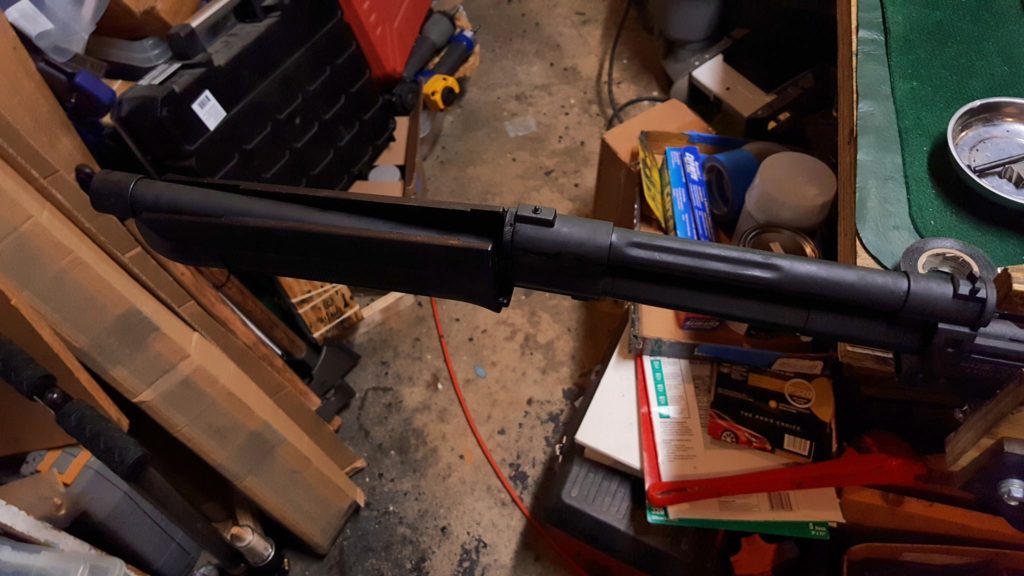
Done
At this point, I had the shotgun all the way apart other than the muzzle cap. I left that on to protect the threads while I worked. The next blog post will detail the customizations and a few surprises that happened along the way.
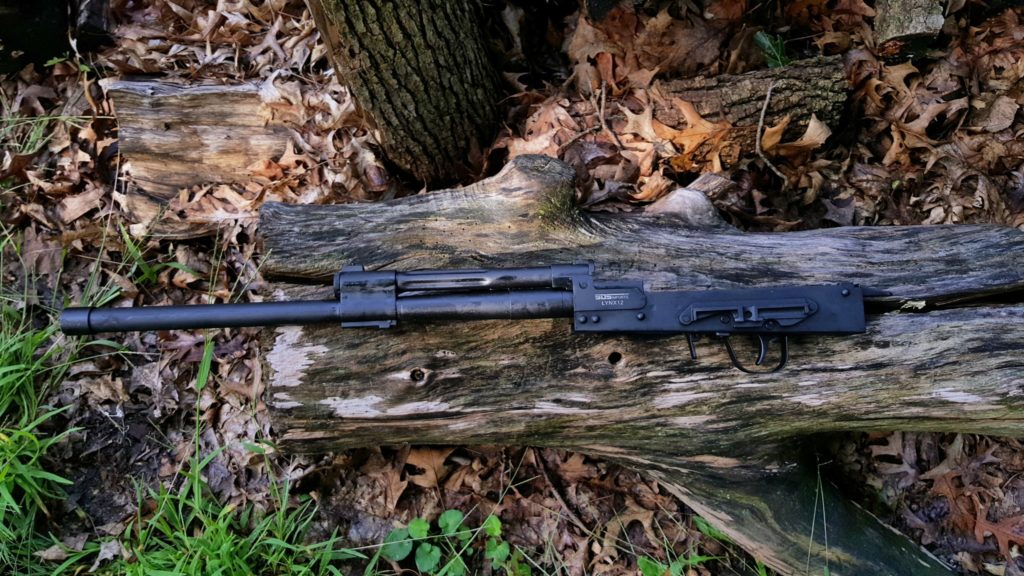
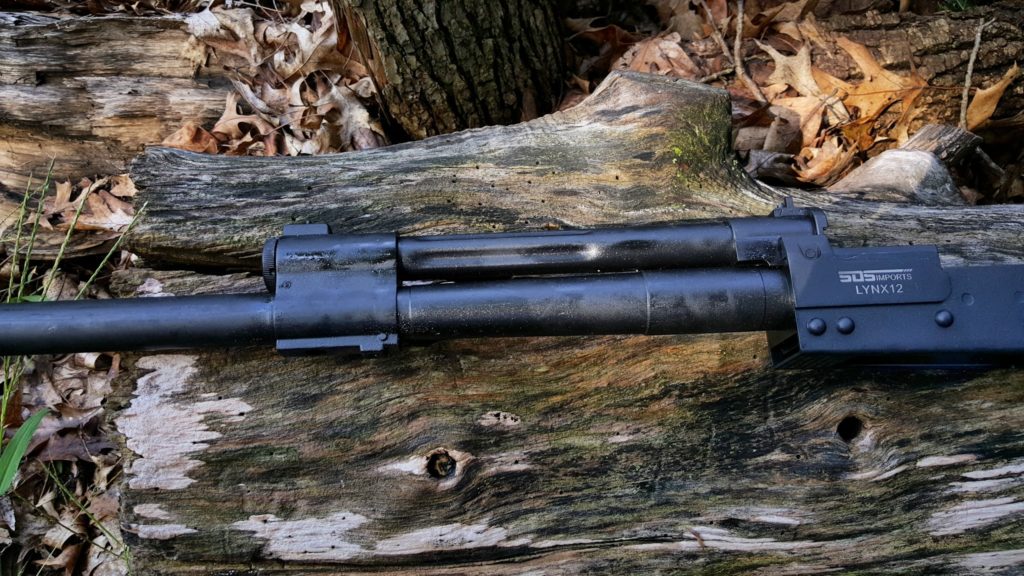
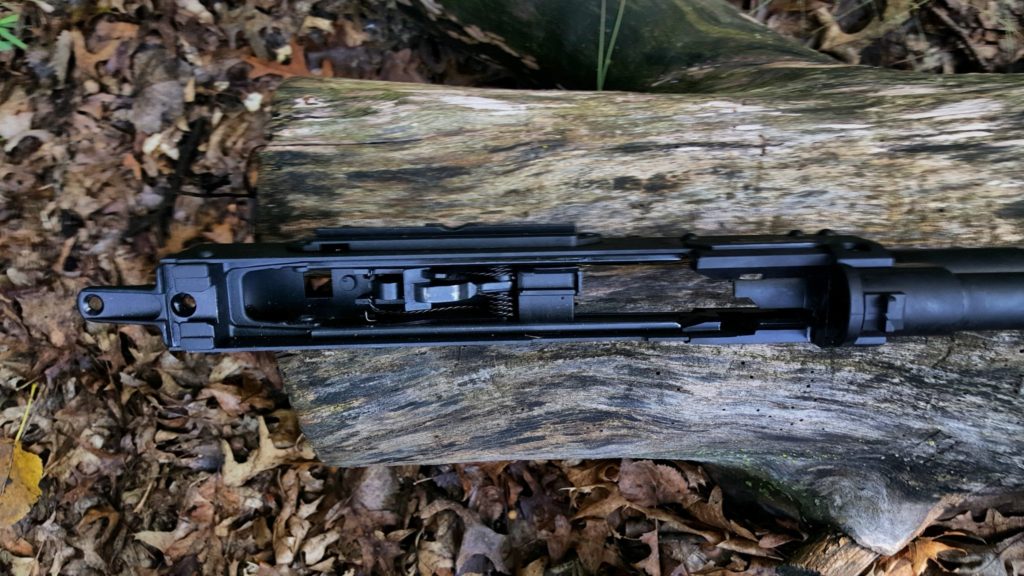
If you find this post useful, please share the link on Facebook, with your friends, etc. Your support is much appreciated and if you have any feedback, please email me at in**@*********ps.com. Please note that for links to other websites, we are only paid if there is an affiliate program such as Avantlink, Impact, Amazon and eBay and only if you purchase something. If you’d like to directly donate to help fund our continued report, please visit our donations page.