I like to heat treat my entire lower rails before I install them. Some guys just heat treat the tip but I go for overkill. When I would get flats and rails from AK-Builder for whatever I was doing, I’d do all the lower rails at once and store them oiled in a bag for later use.
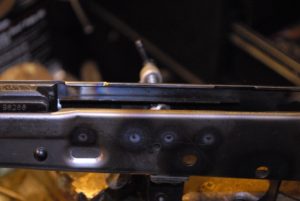
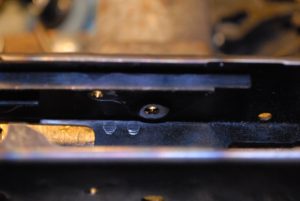
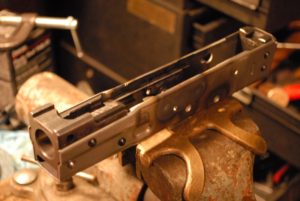
The process is simple, I heat them up with a torch to dull to medium orange, which comes out to around 1500-1600F. Some guys use magnets and stop the heathing when magnetism is lost, some use marker/applied heat indicators – there are many ways to do it. I tend to use my sheet metal/jewelers oxy-acetelene torch. It is known as a Meco Midget and the thing is awesome for sheet metal work. I’ve had mine for over 10 years and never had a problem. I have a giant Journeyman II set but find it too big and cumbersome for stuff like this.
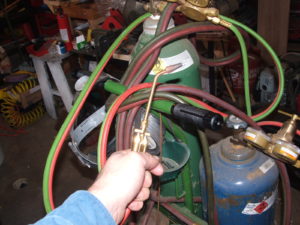
Tin Man Technologies (TM Tech), who I got mine from years ago and you will need to search around for it or find what some call a jeweler’s torch
Next, quench the parts in room temperature used engine oil. It works great for me. I have an old navy fuse can with a lid glued to a piece of wood that I use for this purpose.
After that, I anneal them by putting them in a flat pan, pouring in some brake fluid with some paper towel exposed, lighting the towel and then letting it all burn it off, which is about 500. It’s messy and you want to do it outdoors for sure – I let it all burn off and then air cool. Some guys put them in a toaster oven at 500F for 5-10 minutes and let them slowly cool down by turning the oven off. That works too.
Here the rails right after the brake fluid is finished burning off – you can see some of the soot that is generated:
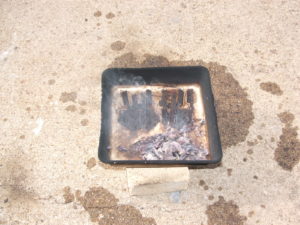
When you weld the rails in with a spot welder, just be careful not to ruin the heat treat by letting a tong get up against the ejector tip and heating up. I’ve done it twice over the years. One time I didn’t notice and had to repair a peened over ejector and the other time I saw the discoloring of the tip and did a spot hardening of the ejector tip while it was in the receiver.
At any rate, I’d then oil everything and put them in a ziploc bag for future use. I would sand the backs of the rails prior to installation to get good spot welds.
While I use OA for a lot of my work, MAPP works just fine too.
If you find this post useful, please share the link on Facebook, with your friends, etc. Your support is much appreciated and if you have any feedback, please email me at in**@*********ps.com. Please note that for links to other websites, we are only paid if there is an affiliate program such as Avantlink, Impact, Amazon and eBay and only if you purchase something. If you’d like to directly donate to help fund our continued report, please visit our donations page.