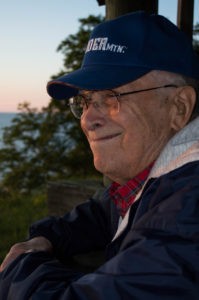
Well folks, yesterday was my dad’s birthday and he would have been 91 years old. I owe him a lot and often think of him. The pain of losing him is less but I miss him. He started me shooting when I was so little that he had to hold the .22 rifles and BB Guns and help me aim. He taught me the basics of shooting rifles and shotguns along with a very heavy dose of how to keep them clean and oiled plus firearms safety.
At any rate, I want to share a special story with you – how a great bunch of guys on AKFiles cared in amazing way and helped me get a Garand for my dad. It’s a very, very special memory for me so I am combining two posts I did back in 2011 telling the guys there how things went with the purchase and the first trip to the range. I’ve wanted to do this for a long time just in case something ever happened to the original posts. So, here they are in memory of my dad.
This first part of the story is from a post I did on AKfiles on February 15, 2011, telling guys how things went — I can’t believe it’s been over six years:
Well gentlemen,
The Garand arrived today via FedEx from CMP and was in fantastic shape. The finish is great, fittment seems solid, action is smooth and the wood is in pretty good shape. I’d say the CMP outdid themselves. You know what, they shipped it FedEx Priority Overnight because they knew why I had ordered this rifle from the very start. I am so very impressed by the staff I talked to there.
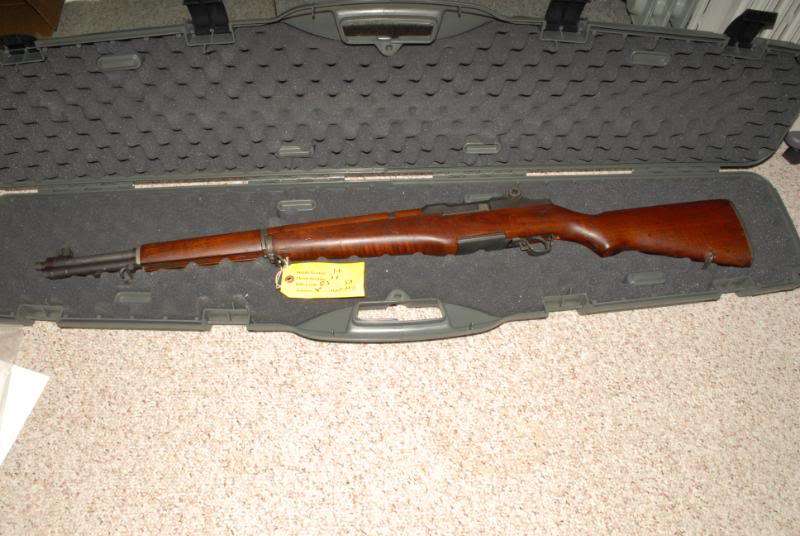
So, after looking the rifle over around 9:30am this morning, I called my parents to come over for lunch. My dad had no idea what was going on. I had them sit down on the couch and gave my dad a 1960s Garand tech manual I told I had found and let him read it while my wife and I finished getting things ready.
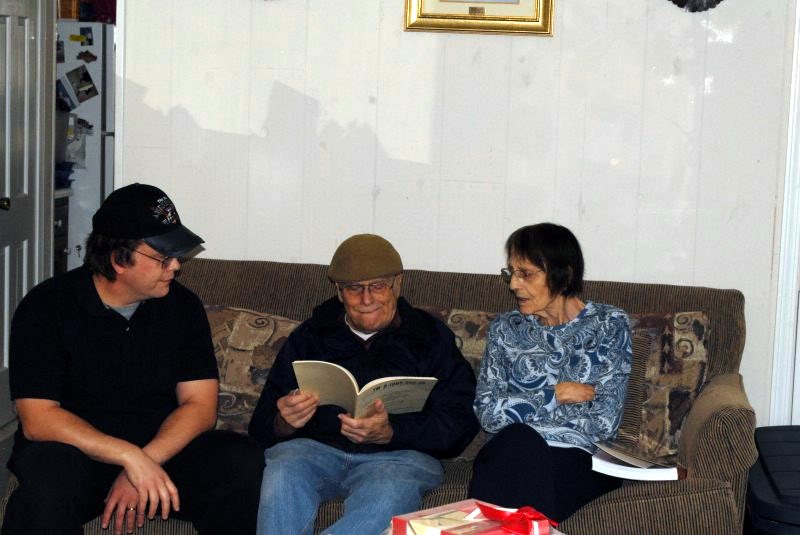
So he’s looking at the manual and my mom and wife are in the room and I ask him – “Isn’t that the rifle you had in the Army but could never afford?” My dad said “Yes” and was thumbing the pages of the manual while I went downstairs. He really had no idea.
So I went downstairs, got the rifle in its CMP case and came up to them without my dad seeing what was in the case and he really didn’t pay it any mind. So I told him “I think its about time you have one” and at first it didn’t really hit him what I said. He even took the rifle from me without really saying anything.
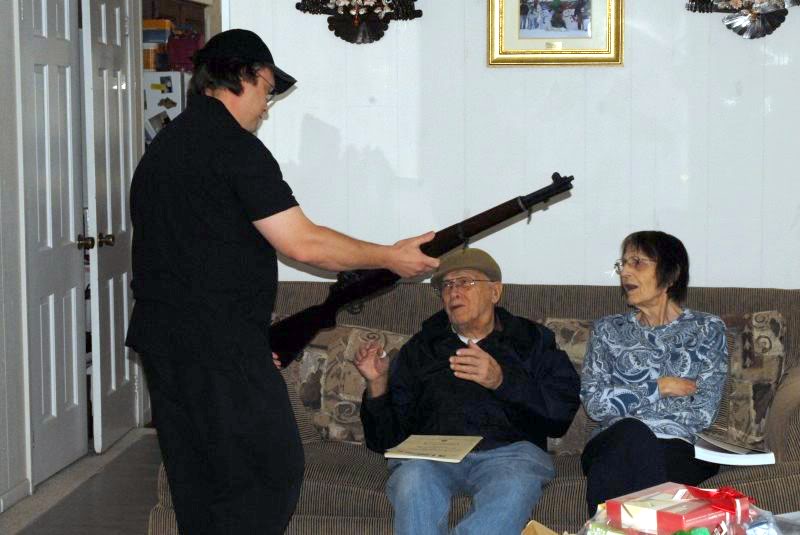
I told him “Dad, this is your rifle and we are going to enjoy it together this summer.” At that point, I think it registered and he asked “It’s mine?” and I told him it was and that it was a real Springfield Armory M1 and not a reproduction. The government Springfield Armory has always been special to him because he grew up in Massachusetts and New Hampshire and I guess because it was close to home.
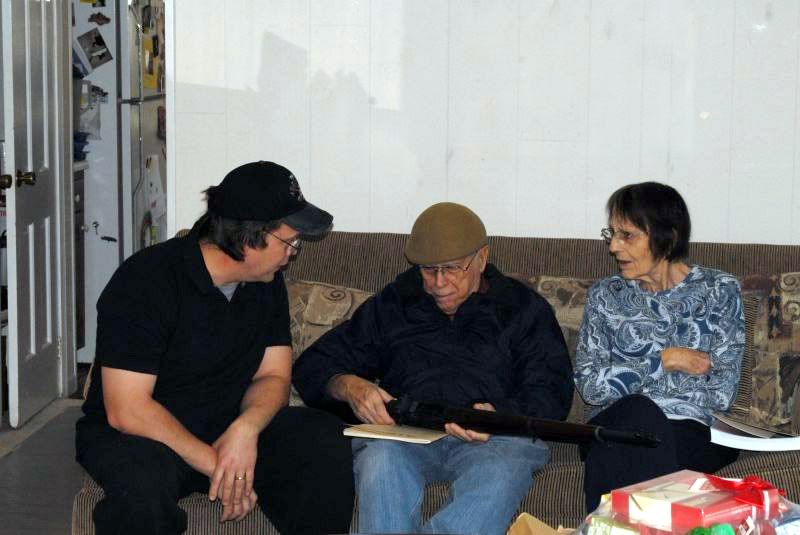
He was looking it over and while he did that I told him about all of you and what you did to help. The prayers, the well wishes, guys wanting to send money, the stories of their fathers, what the CMP did to help and at that point, the only time in my life I have ever seen it, my father started to cry. He told me he never thought he would hold one again.
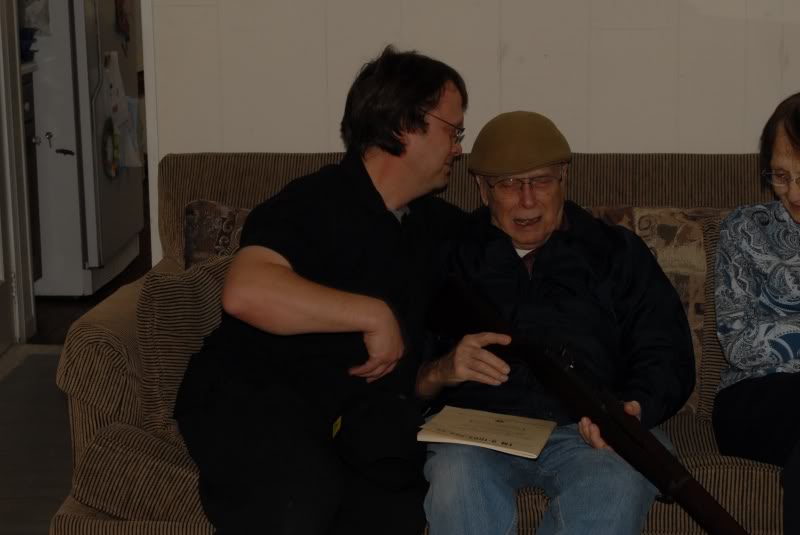
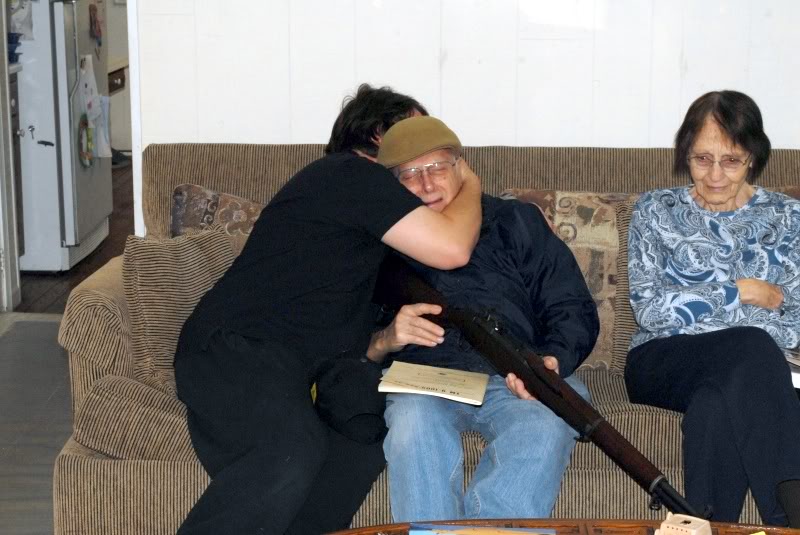
After a few minutes, we got ourselves together and he started really looking the rifle over. He pushed down the follower assembly, or whatever you call it, in the magazine well and carefully pushed the bolt closed saying he didn’t want to get “Garand thumb” and he explained what that meant to us and then the stories began.
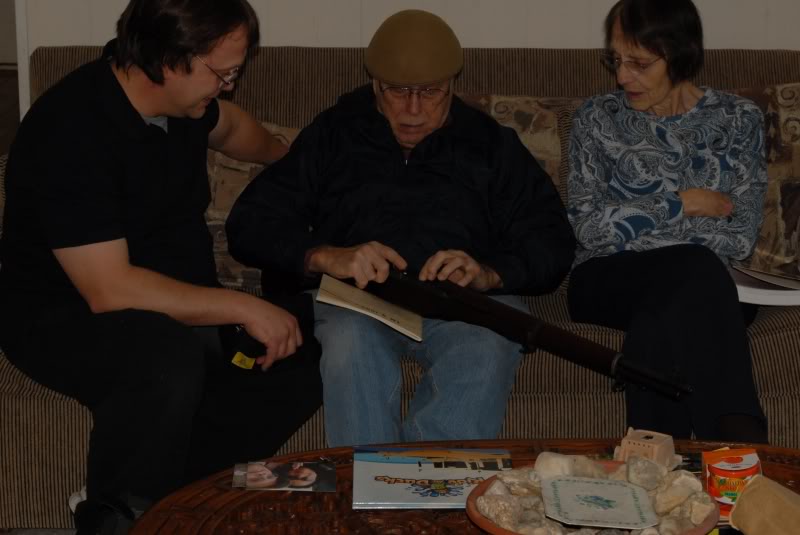
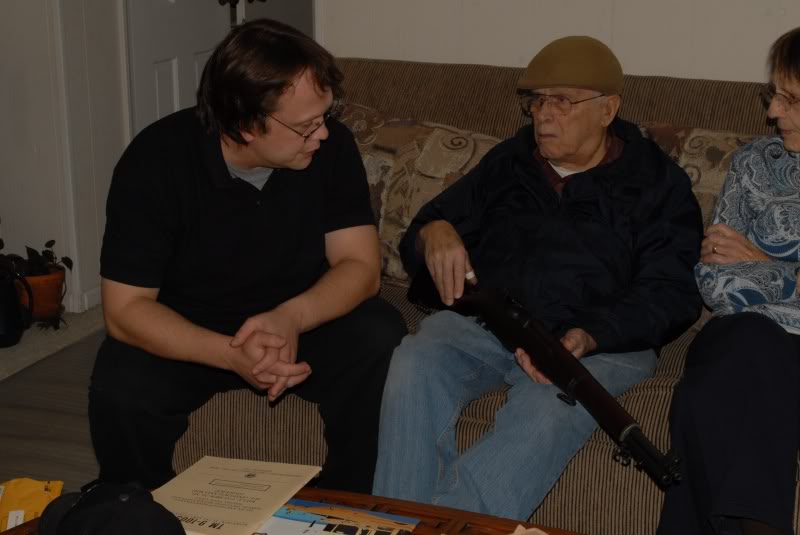
Towards the end, he looked at the rifle again and tears started one last time.
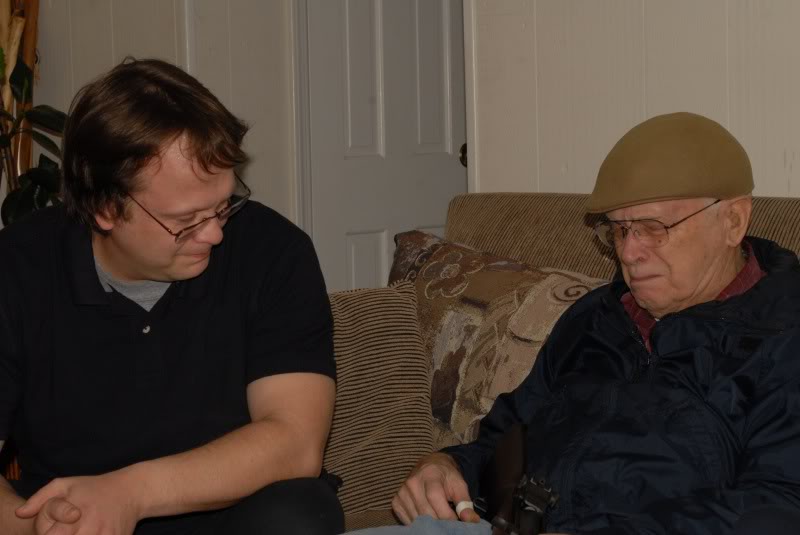
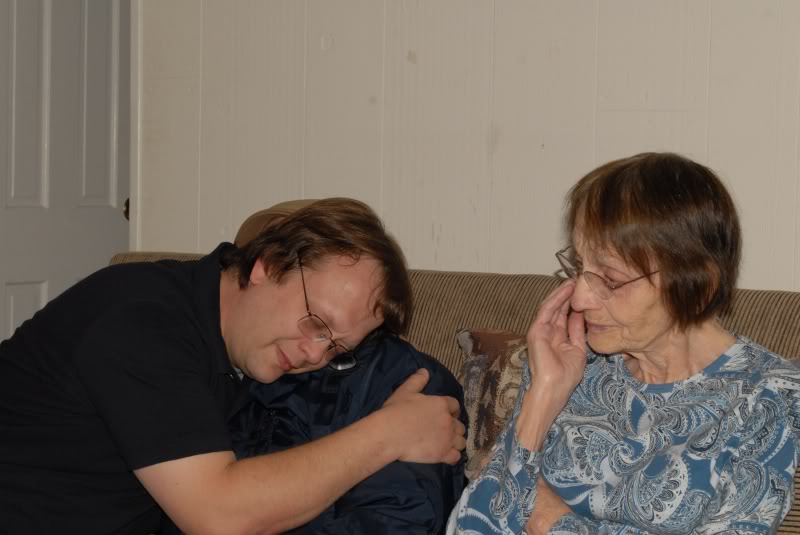
Guys, thank you so much for all you have done. He was so excited – so happy. It was amazing and I am not a good enough writer to tell you how he looked other than to say he was profoundly touched by all that you guys did to help, what the CMP did and so on.
I have a lot to learn about M1 Garands, that’s for sure and I look forward to learning about this one with my dad.
Tomorrow we go to find the results of his bone marrow tests and I told him that no matter what he and I have the Spring and Summer to look forward to so we can take his new Garand out and test it.
Never take your loved ones for granted and do whatever it takes to be able to spend some time with them. Life is precious and time is short.
Thank you my dear, dear friends. You are all amazing.
The second part of the story is from July 27, 2011 when my dad I finally were able to take the Garand to the range:
It’s funny how fast time flies by. As you know, I bought an M1 Garand for my dad and gave it to him. Getting to the range with him was always on the “to do” list but never quite made it to the top due to job conflicts, health, kid stuff, and so on. Before I knew it, time flew by. You don’t realize how fast time slips by until you look back.
On June 27th, my father in law fell over a small 18″ tall dog fence, cracked a neck vertabra hitting a couch and compressed his spinal cord. He will not recover from the injury and subsequent complications caused by kidney and heart disease. It was such a freak accident because he was only 75 and full of energy. Now, he is sedated and kept alive by machines in ICU but still able to think and move his eyes. Calls and well wishes from you guys really, really helped. Bubbazan, Elkaholic, Ding … you guys are great. I can not thank you enough.
I told my wife that it really showed me that we can’t take loved ones for granted or leave loose ends undone. I told her I absolutely had to take my dad to the range with the new Garand. We are home this week catching up on bills and work while my wife’s family takes turns watching my father in law. Thus, I got an opportunity and seized it. Sometimes, and this was one of them, you need to make things happen and that’s what I did.
It’s been real dry and hot here which, for my dad, is perfect because there are fewer mosquitos – when they bite him he swells up huge because his compromised immune system goes nuts. Monday night I had a crash course in M1 Garand disassembly, cleaning and lubrication. Youtube videos and some web pages people had sent me helped tremendously. The CMP armorer knew about the situation with my dad and other than cosmoline in the stock, the rifle was immaculate. The trigger group was gun metal grey and lightly oiled inside. If I didn’t know better, I would have sworn I was looking at a new rifle based on the quality of the parts, lack of wear and cleanliness.
I used Mobile synthetic grease to lubricate the rifle. It really made the rifle nice and slick. I was very concerned about recoil hurting my dad so I installed a medium Limbsaver Slip-On Pad just to be safe. It fit great and really cushioned the butt. So, I packed it up and made sure I had the ammo, targets, hearing protection, and so on for the range.
On Tuesday, my dad arrived and we loaded his van up and headed to the sportsman’s club for an afternoon of shooting. When we got there we had the range to ourselves as it was 3pm. It was sunny, hot and no mosquito in sight – things were looking great.
We set up on the range. My dad was definitely excited – he’s always been a big one to understate things but I could tell. Bear in mind an 85 year old man doesn’t move too fast and he was clipping right along. We set up on the 50 yard line to do our testing.

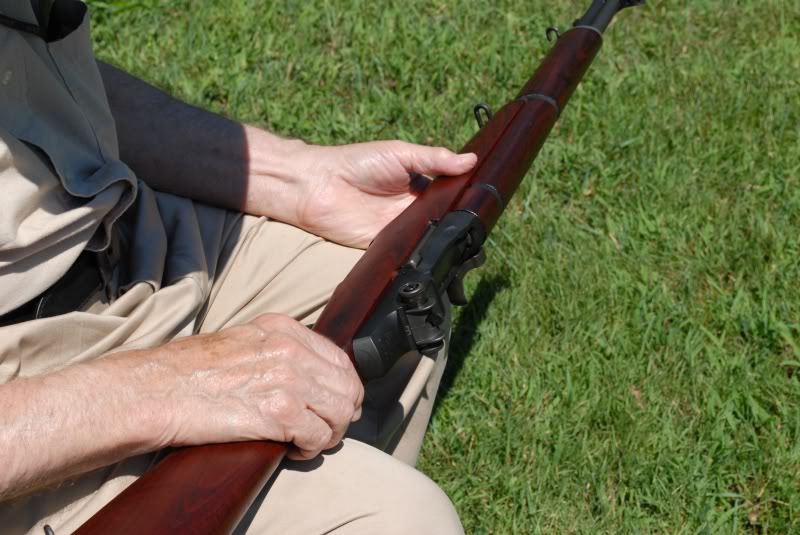
Now I had cleaned and inspected the rifle as best I could. Even so, we installed it in a stand and fired a test round with 25′ of string. Of course, my dad had the honor of pulling the cord and doing the first test firing.
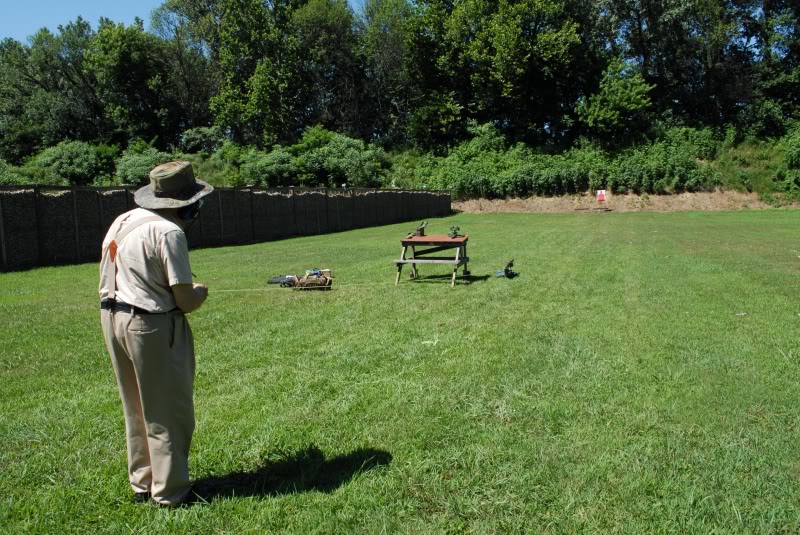
The rifle functioned flawlessly on Greek M2 ball ammo. No bulges, primer looked great – the cartridge looked just fine. We inspected the rifle and everything looked great. My dad had this huge grin on his face.
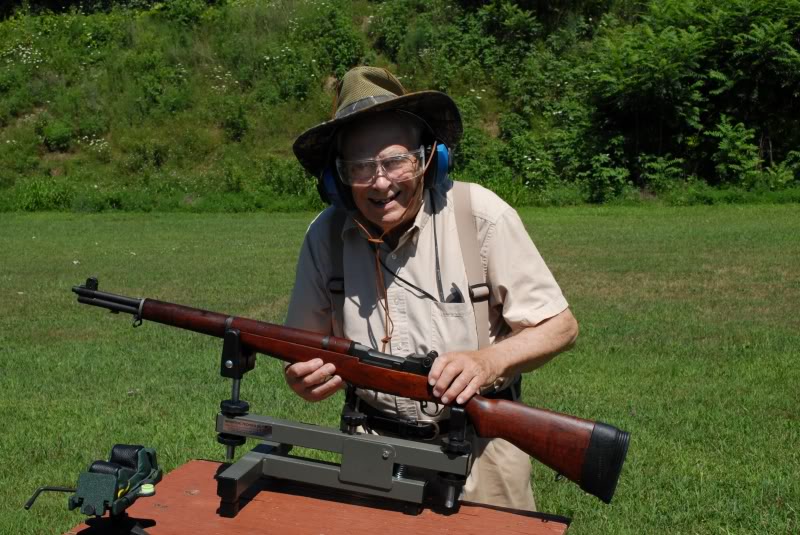
Of course, the next thing to do was to fire for effect! The old man got down on the bench and lined up. He did it so smoothly that you just knew he and Garands knew each other. I was running around taking photos.
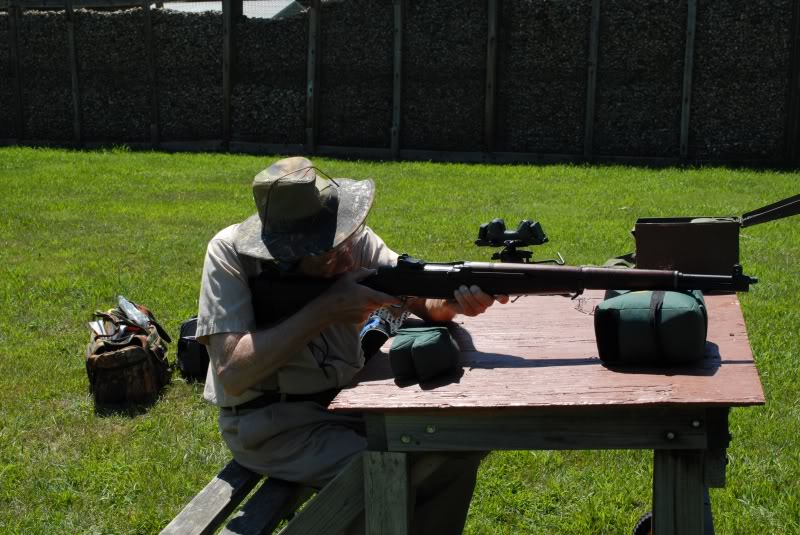

He squeezed off his first shot from an M1 Garand since the last time he fired one in Korea in 1945 – literally 65 years ago. Now bear in mind this was round #2 from the rifle – no changes to the sights plus my dad hasn’t been shooting for almost a year.
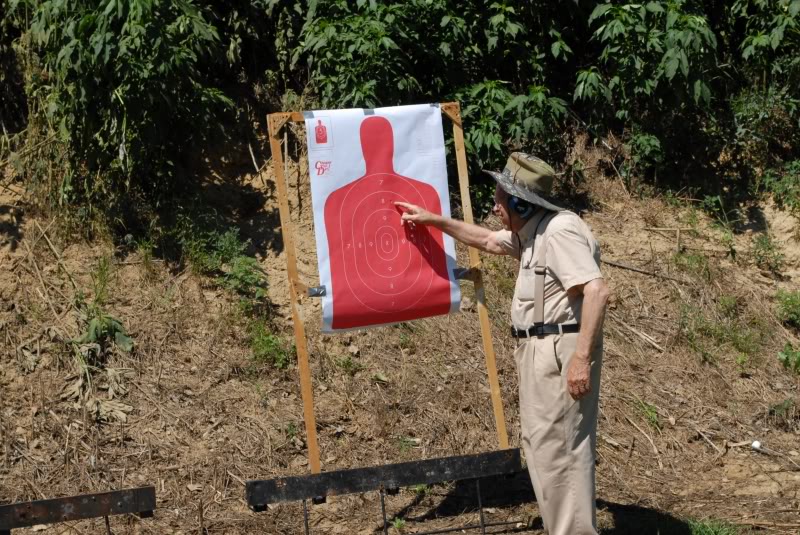
That definitely excited both of us so he got down to business
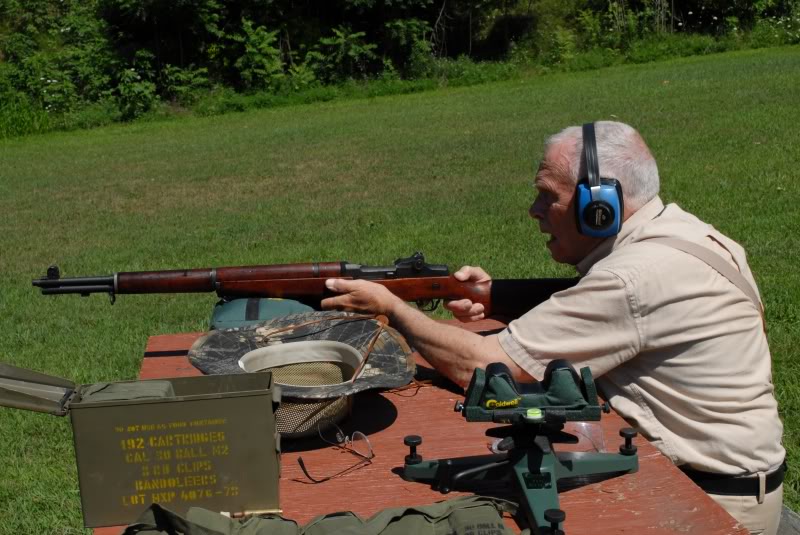
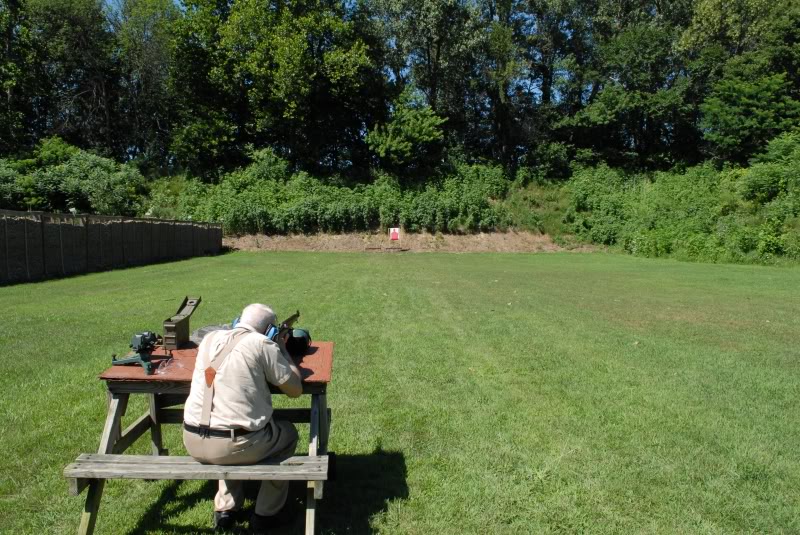
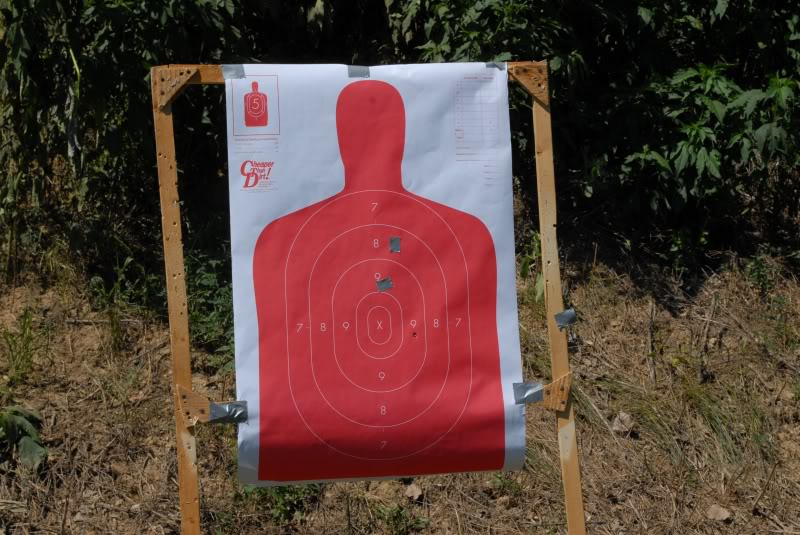
He fired 7 rounds – each time we’d unload the rifle and walk down to look at the target (I forgot my spotting scope). He was happy and talking about the rifle, how to adjust the sights, it was great. My dad got tired and asked that I shoot the rifle. I went on to fire 9 rounds realtively quickly from 50 and 100 yards before we had to leave. Not one single failure or problem of any kind – not one. The rifle functioned perfectly. I got a real nice note from the lead armorer at CMP wishing my dad well and I think they are an awesome group – all of them.
After shooting the rifle I was amazed at how little recoil there was. More of a push than a slam plus the recoil pad made it a joy. My dad said it didn’t hurt at all. We were able to spend about two and a half hours at the range and just had a great time. I’m definitely going to take him more this summer. We have a checkup on his cancer at the end of August and we’ll need to decide whether to keep watching, or just what. When we were packing up, I told him that I couldn’t afford the fishing boat but at least I could get him a Garand and that brought out a big smile. It was a great day – I was so happy and he was too.
Again, I want to thank all of you for your awesome support. We all have our own personal trials but having people go out of their way to help is an amazing thing. I feel very lucky to have a wonderful family and to count so many of you as friends.
God bless all of you and your families.
Sincerely,
George
In closing
Never miss a chance to spend time with your families. Just before my dad passed away on September 20, 2014, we were planning on taking the Garand out to the range. The day we were to go he decided against it as he didn’t feel up to it. A day or two later he passed away in his sleep. I really wish we had that one last shooting session but I do have some great memories and they outweigh the regrets.
We miss you dad.
In case you are wondering, here’s a bit about my dad:
Carroll Spafford, 88, of Stevensville, formerly of Battle Creek, MI, passed away peacefully on Saturday, September 20, 2014, at the Hanson Hospice Center.
Born in Boston, MA on June 26, 1926, to George RH Spafford and Hazel Holmes (Mr. & Mrs. Spafford) of Everett, MA. His parents, older brother (George Kendall) and younger sister (Phyllis) moved to a farm his parents bought in Derry, NH, when he was a young teenager. While there, he attended Pinkerton Academy in Derry and graduated in 1945.
On March 30, 1945, Carroll enlisted in the US Army and was sent to Korea to join the 6th infantry division guarding against any attempts by the Japanese to retake Korea. While there he rose to Corporal overseeing a seven man heavy machinegun squad. He was honorably discharged on December 30, 1946, and returned home.
As part of the GI Bill, he attended the Wentworth Institute of Technology and obtained his MC&TD degree in 1949. After several years working, he then attended Ohio State University and received his MBA in 1955.
Carroll’s career took him to Detroit and Ford Motor. While in Detroit he met and married Alpha Lee Turman on November 26, 1964. Following a brief stint working in research at the University of Michigan he then accepted a rewarding position at Kellogg Community College in Battle Creek, MI, where he taught business management and economics/
In 1967 he and Alpha had a baby boy, George, who was joined by his sister, Rebecca, in 1971. They had a small farm North of Battle Creek with a collection of dogs, cats, horses and gardens plus summer car trips all over the US that occupied their time.
In 1986, he retired from KCC and he and Alpha volunteered at Junior Achievement in Battle Creek. In 2002, he and Alpha moved to Stevensville, MI, in order to be closer to their grandchildren.
In 2012, Alpha passed on and Carroll continued on with the help of many talented and much appreciated care givers. He is survived by his son, daughter, three grandchildren (Paolo, Alyssa, and Erika), his sister (Phyllis) and a very large extended family who all love and miss him greatly.
Like this:
Like Loading...