I am routinely asked how to rehydrate khukuri wood handles that have dried out over time. This is a service we provide when tuning khukuris and have learned a few tricks along the way that we can share. We approach rehydration or moisturizing by using a 50/50 mix of quality boiled linseed oil (BLO) and turpentine, which we purchase by the gallon from our local Ace Hardware store and sometimes Lowes. The turpentine helps thin the BLO and avoids it becoming unduly tacky.
The procedure is pretty simple so let me outline it. I see handles that often need some tinder loving care such as this Keshar Lal Villager Utility Knife (KLVUK) khukuri handle:
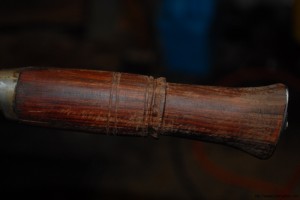
My first step is to do any wood repairs such as gluing cracks, filling holes and sanding. It is very common to find a poor fit between the end cap and the wood for example and I will true it up all the way around either with sanding strips or a sanding mop such as what is shown here:
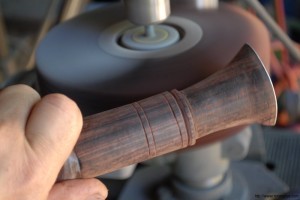
A mop is good for fast touch ups but not for leveling surfaces or otherwise intentionally shaping the wood. I buy big shop rolls of 1″ wide sand paper in 80, 120, 220 and 320 grits so I can select the grit I need.
The next step is to soak the handle in the turpentine and BLO mixture. I shoot for it being about 90-100 degrees and soak the wood for at least four hours.
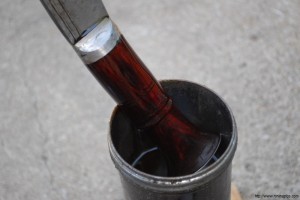
I then rub the handle down with a blue shop towel to remove the liquid and let it air dry for about a day. The results are striking. The below photo shows three KLVUKs that arrived with basically the same color of wood that I picked for this story for that very reason. The bottom handle is untouched. The middle handle is after sanding and the top handle is after following the above process. This helps you see the results.
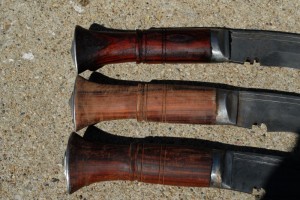
Here is one of our completed KLVUKs:
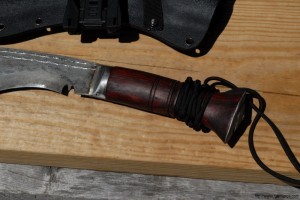
I hope this helps you do some care on your blades as well.
Like this:
Like Loading...