In 2014 we visited Greece, and on December 30th, we were in Delphi staying at a small quaint hotel whose elevator put the fear of God in us. The vibrant town was quiet and subdued – the summer tourists weren’t there and the arrivals for New Years Eve handn’t arrived so we had the town more or less to ourselves and some locals.
We walked by a shop and they invited us in. They had tons and tons of bowls, plates, spoons and what have you made from olive wood. There are huge ancient groves of olive trees tended by families for generations surrounding Delphi so there was an ample supply of olive wood to draw from.
Olive wood is simply gorgeous when sanded and finished bears all kinds of browns, tans and wavy grain structure. It’s strong, dense and does great indoors – especially when oiled but doesn’t do as well outdoors or with insects as it lacks natural oils.
At any rate, the products were all made in and around Delphi. We opted for some nice kitchen spoons and a juicer given the striking look of the wood. Before we knew it, the trip was over and we headed home.
December 2023
I was trying to think of something to do as a surprise for my wife and happened across the spoons and juicer from Delphi – they were looking pretty tough. The wood was faded and you could just barely see what they looked like 9 years prior so I decided to clean them up.

The first thing I did was to run over the spoons with a 220 grit sanding mop in a small drill press that I have dedicated for that purpose. I use sanding mops to finish grips so the station sees a lot of use.
The next thing I did was to use butcher block conditioner to revitalize and protect the olive wood. In general, the conditioners are some combination of food safe mineral oil and waxes that penetrate a wood surface to help protect it. I’ve used a few brands over the years and my favorite is the butcher block conditioner from Howard Products.
There is a bit of a trick I do with restoring a wood finish like this. First off, I rub it in with 0000 steel wool to knock down any stray wood fibers. In case you aren’t familiar with steel wool – “0000” is a very fine grade meant for final finishing. You put the conditioner on thick and let it set for 4-8 hours. You’ll be surprised how much gets absorbed by the wood.
I then wipe it off with a rag and apply it thick again by hand – I don’t use steel wool after the first application. Again, let it sit and absorbe for 4-8 hours, wipe off the residue and repeat.
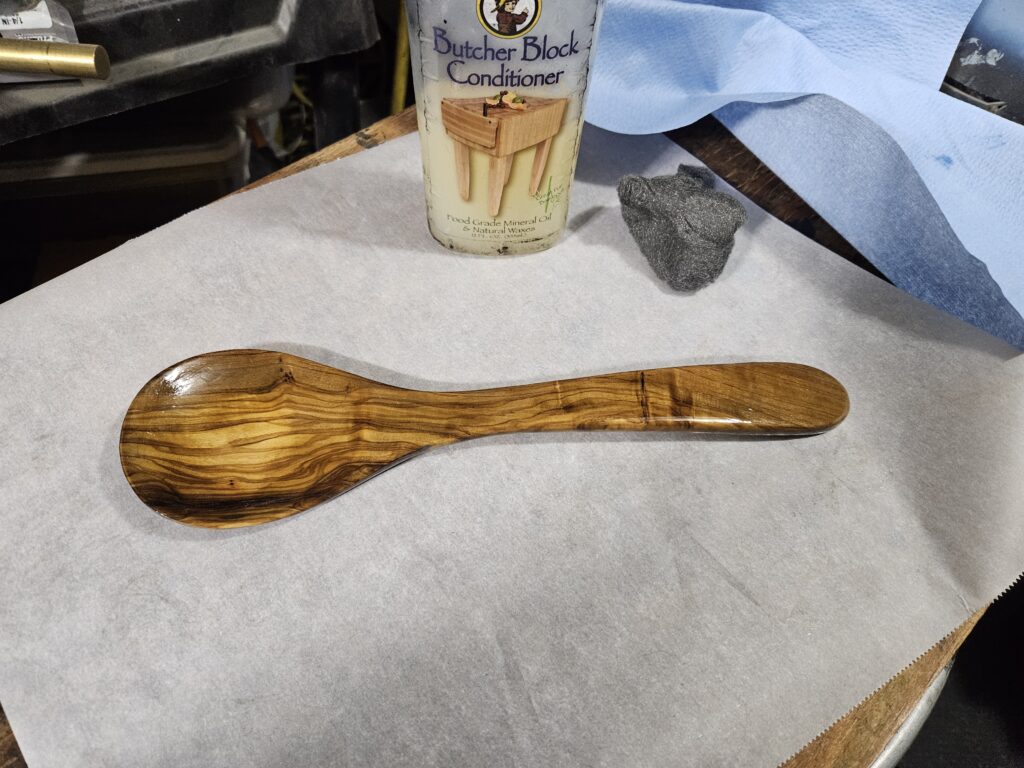
You’ll notice with the third or fourth application that less and less is being absorbed so stop where you want and buff the piece with a rag or shop towel.
You may still see or feel a hint of oil but it will disappear in a day or so as it finally gets absorbed. You really can’t go wrong with this finish – just apply, let it sit, rub it off, and repeat until you get the look you want.
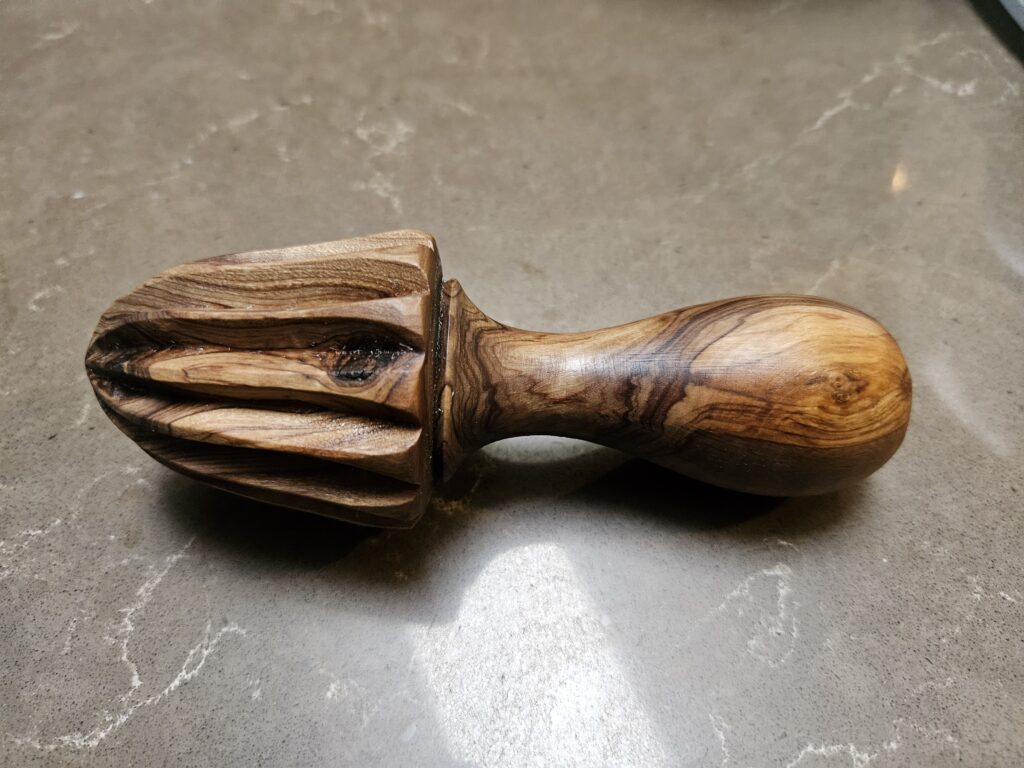
Summary
The utensils from Greece turned out really nice – like new really. My wife is very happy and I shouldn’t wait so long to do it again in the future. It’s amazing how fast time flies by.
Howard Butcher Block Conditioner is my go-to finishing product for breathing life into any wood that comes into contact with food – cutting blocks, wood bowels, utensils, etc. I pretty much follow the above process on all of them.
I hope this helps you out.
If you find this post useful, please share the link on Facebook, with your friends, etc. Your support is much appreciated and if you have any feedback, please email me at in**@*********ps.com. Please note that for links to other websites, I may be paid via an affiliate program such as Avantlink, Impact, Amazon and eBay.