Back when AK-Builder flats didn’t have the top rails cut to size, we had to do the work. I’m talking circa 2006 and then late that year he came out with a simple layout tool that was so awesome. You applied Blue Dychem do your flat, clamped the layout jig to the rail, used a scribe to mark the profile and then you came through with your mill (or Dremel) and cut out the shape. It was faster than doing it all by hand and the one plus was that you could get the exact spacing between the upper rails that you wanted.
Category Archives: AK & Related Rifles
Used to discuss AK-47, AK-74, and related rifles
Setting an AK’s Internal Front Trunnion Rivets with the AK-Builder rivet jig
It’s pretty straight forward really. You need to insure the rivet jig is sitting on good strong steel cross plates – don’t use wood. I’ve seen guys try so don’t laugh too hard. For the record – that one I never tried – I used 1/2″ steel plate from the get go. Wood is not your friend under high pressures.
Be sure to use the right rivets – AK-Builder sells the best rivets and tailors them to what you are building. Lay them all out and identify what rivets are for the front, the swell neck rivets for the lower back of the front trunnion, etc. A rivet should stick out 1.5x its diameter – that’s it. Just for example and to keep the math easy for me, a 4mm rivet should only stick out 6mm. If you go further, you are going to have problems. As you get experienced, you can buy rivets in bulk and use rivet trimmers but you might want to save that for down the road.
Make sure the rivet and your receiver are all nice and square and that the little cup is under the rivet’s head to support it. Make sure everything is nicely supported too. If you don’t you will bend the receiver. When I make cautions, it’s usually because I did it the wrong way already at some point 🙂
Only extend the rivet arm the minimum amount necessary. The longer it sticks out, the easier it is to bend it. I’ve done that and you may too. If you do, just bend it straight again by pulling it out of the jig, supporting it by steel block and press it straight.
Now go slow. Speed will only help you mess up faster, especially if you are new to this. Extend the little set screw enough to squish the rivet and clear the trunnion walls.
Do not go crazy with the pressure. You want to squish the rivet, not start bending stuff. The rivet swells inside the hole and and the end caps it – that is all you need to accomplish. Too much pressure and tooling starts to bend.
If you find this post useful, please share the link on Facebook, with your friends, etc. Your support is much appreciated and if you have any feedback, please email me at in**@*********ps.com. Please note that for links to other websites, I may be paid via an affiliate program such as Avantlink, Impact, Amazon and eBay.
First Romy G Build – October 2006!
So I have been taking photos of guns and tools for years and years and year. I just recently decided to start dipping in and sharing. I was pretty floored to find this collection of photos of my first build. It was a 1981 Romanian G pattern AKM, affectionately known to many AK builders as a Romy G. I’d invested in AK-Builder tools and used them and a big 20 ton hydraulic H-frame press to do the work. You’ll notice the older AK-Builder flat bending jig is shown. They worked great and the only drawback I ever noticed, and it was not a big one, was that the flats need to have a positioning hole for a roll pin at the end of each flat. This definitely was not a big deal but he did evolve the design to not need that later on.
You can also see the old style AK-Builder flats. They were great to bend but you really needed your act together to do the top rail. I actually botched this first one and made the rails too narrow. Because of this, the gap between the upper rails was too wide and the bolt carrier kept popping out. So, I did a new one and was very careful to get the rails held in place nice and rigid plus I would mill a little and test, mill a little and test to dial the fit in.
I bought a HF mini mill so I could get better looking and more consistent upper rails. Note the 3″ milling vise. I bought that from Little Machine Shop and it works great. I still have both the mini mill and the vise. My one comment on the mini mill is that it is light duty. On my bucket list is a full size mill at least with a digital read out (DRO) if not with CNC. To this day I do a lot of “eye balling” of work and would like to be more precise. Also, I eventually moved away from oak wood fillers to precise steel blocks at some later date. The fun thing about writing this up later is that I recall lessons learned and stuff but remembering dates has never been a forte of mine. As I used the mill more, I really learned to value work holding systems. Old timers’ advise of “take the time set it up right so the work doesn’t move” proved to be a life lesson I draw on to this day.
Here’s the 1981 parts kit. Notice how nice and smooth the barrel is machined. Starting around 1983, the quality started going down hill and you’d see kits where the barrels literally had turning marks going down them that almost looked like threading. By the way, the “G” series AKs were actually well made semi-auto rifles despite one some detractors would say. They were made for the Patriotic Guard hence the “G” for Garda.
The wood was always so coated with goop, I would spray them down with Bix wood stripper several times until I got down to the wood and would then do finish sanding. Now on this rifle I used satin polyurethane and over the years moved to boiled linseed oil as the latter was very easy to fix/maintain. I used a number of reddish brown Minwax stains over the years. I think that was red oak.
I had AK-Builder rivet jigs but I didn’t take photos of them while doing this build for some reason.
Here was the end result. I would have used a US slant brake, Tapco G2 FCG and that might be a Tapco or generic brown US grip. I used to get most of my parts from Copes, Centerfire and DPH Arms back in the day. The finish was Duracoat but I stopped using it after a few years and moved to a combination of parkerizing and Molyresin that held up great. The AK’s selector lever can wear a strip through a finish real fast.
I kept this around but shot it less and less then when the kits skyrocketed to about $300, I cut the receiver off and sold the kit. The funds went to other projects but with 20/20 hindsight, I wish I had kept it for nostalgia. My dad and other family members all had fun shooting this rifle.
If you find this post useful, please share the link on Facebook, with your friends, etc. Your support is much appreciated and if you have any feedback, please email me at in**@*********ps.com. Please note that for links to other websites, I may be paid via an affiliate program such as Avantlink, Impact, Amazon and eBay.
How to Install a Flat’s Lower Receiver Rails So They Align With The Front Trunnion
I heat treat the lower rails before I install them. The best way I found to align the lower rails in a flat so they were both parallel with the upper rail and aligned with the trunnion was to use a drill bits of the proper size to locate the lower rail and I would then clamp the lower rail in place prior to spot welding. This is one of those things where you want to check and double-check prior to and after each weld to make sure nothing shifted on you.
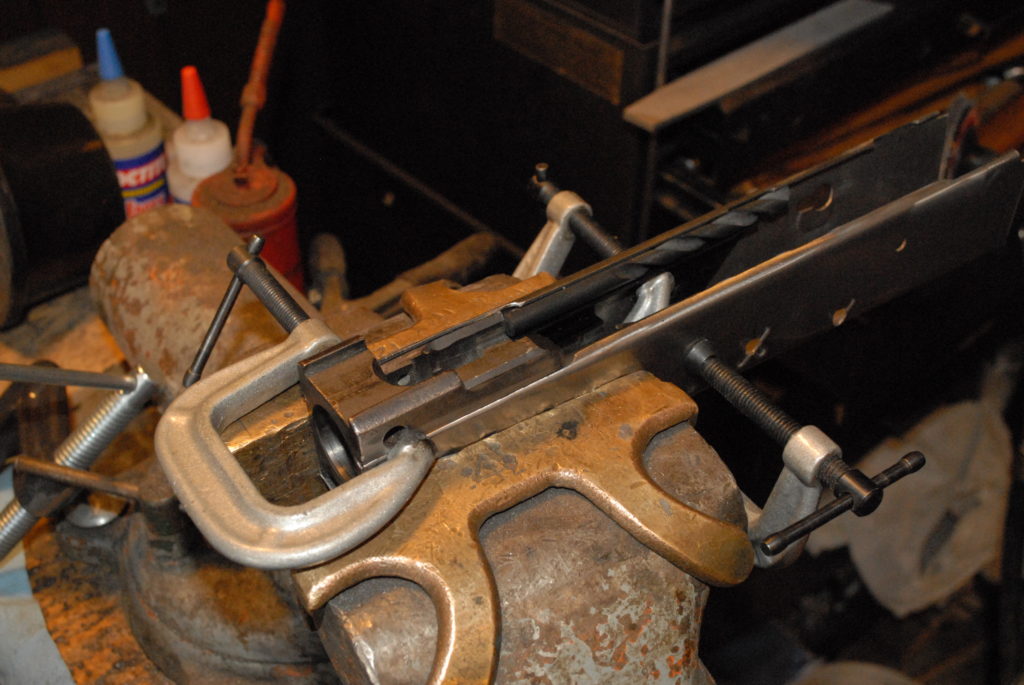
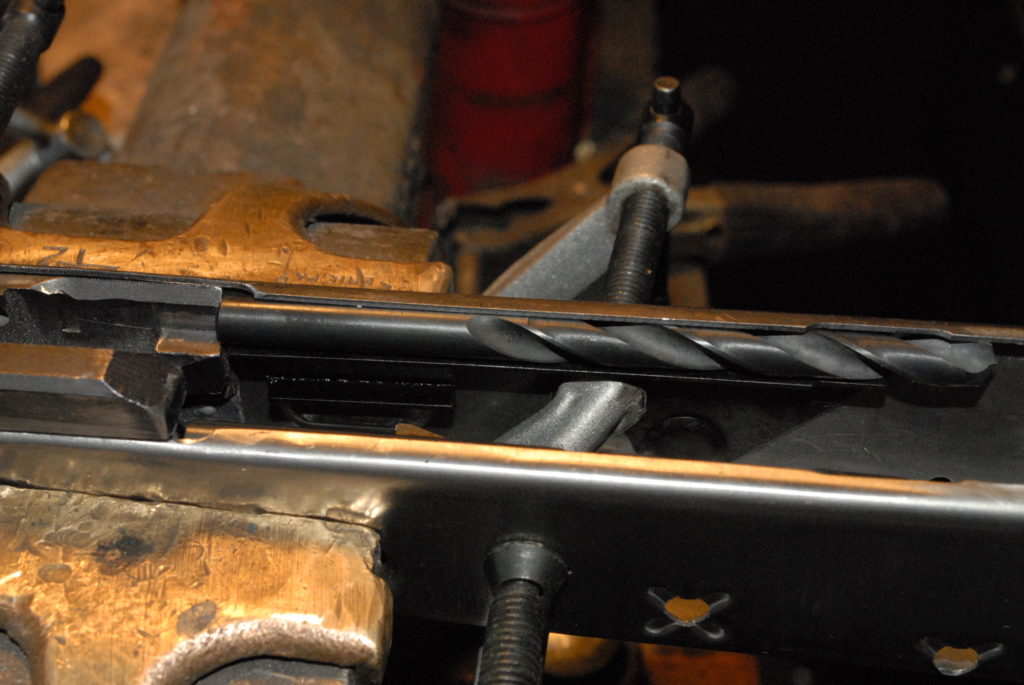
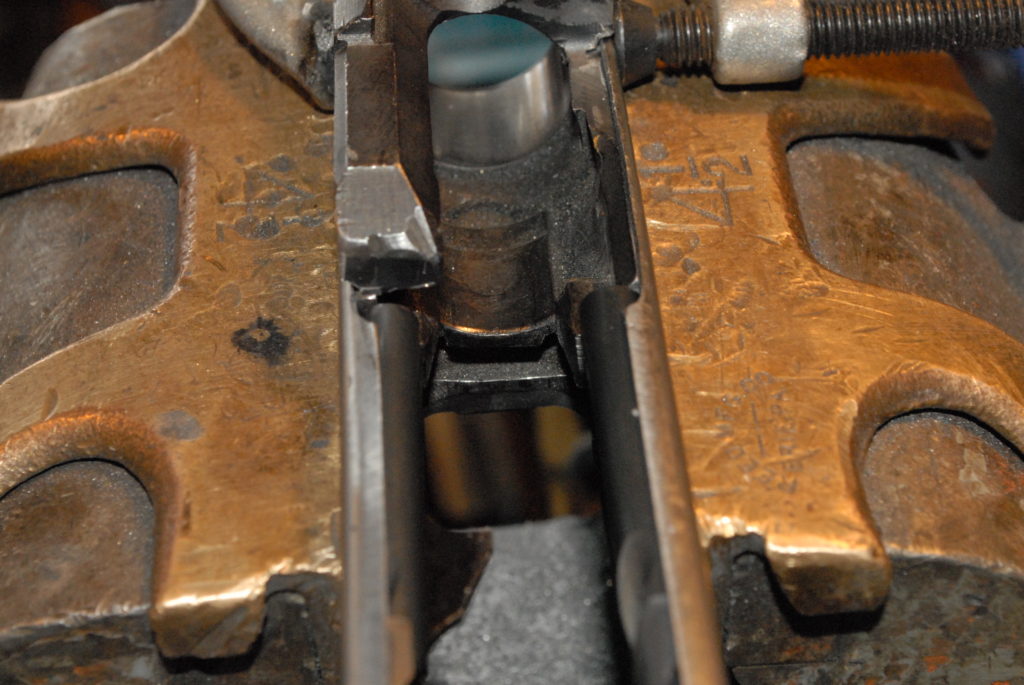
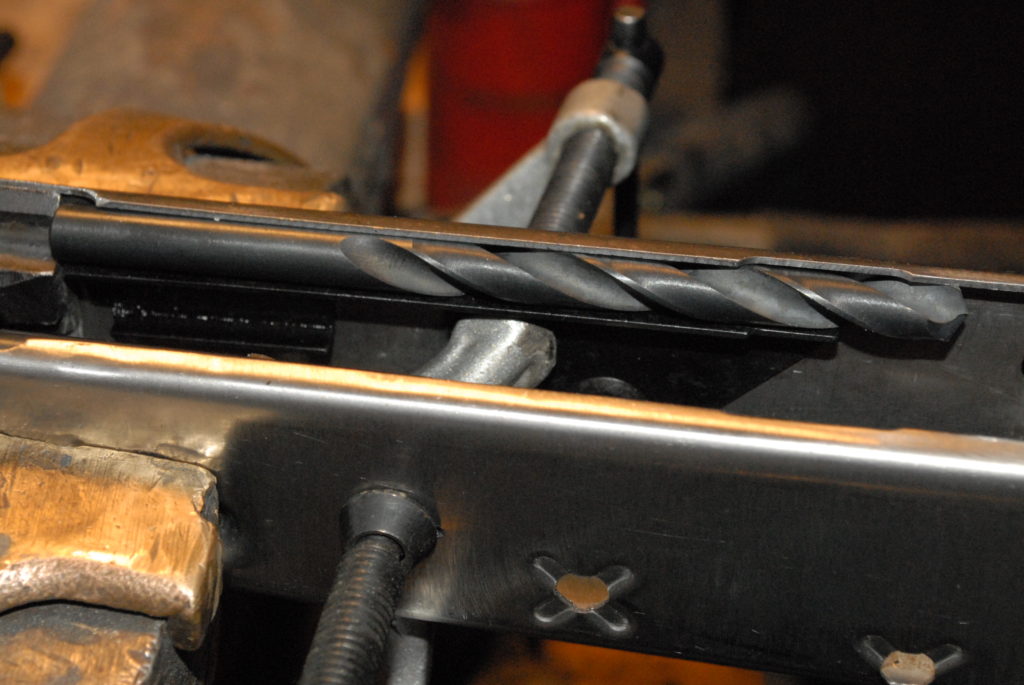
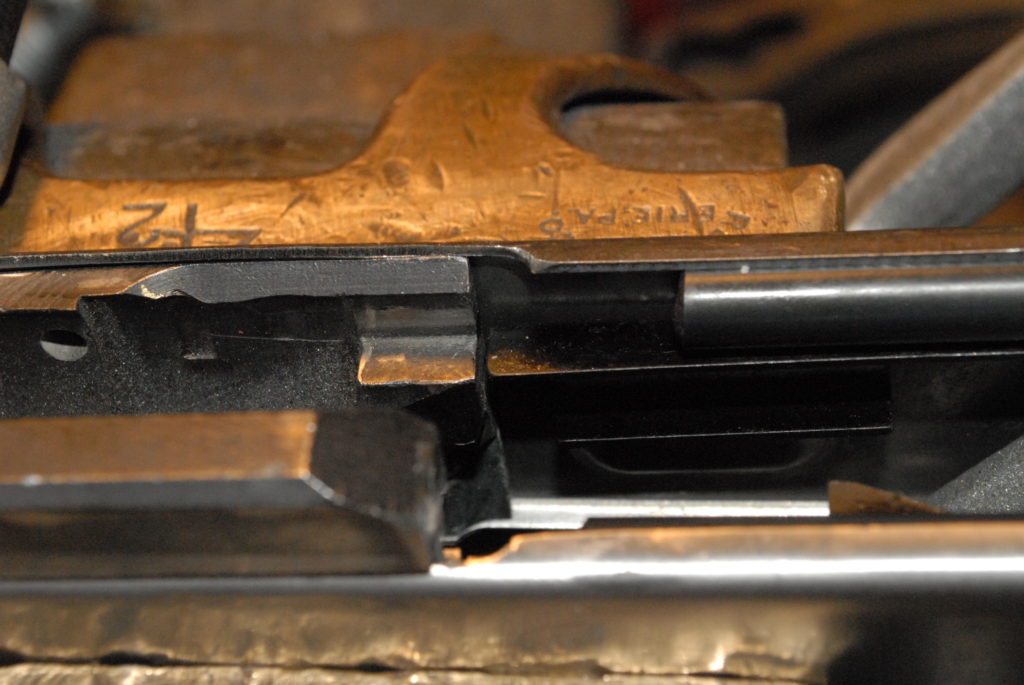
I use a Harbor Freight #45689 115 Volt spot welder with AK-Builder upper replacement tong and also tips. It’s lasted me through quite a few builds over the years and is still going strong. The tong makes it way easier to reach in and make the weld and the tips make the spot weld look a lot more like the real ones. I have had to replace the tips once so far, just FYI. You need to keep them clean to be most effective.
For beginners, there is no way to tell you how long to clamp and trigger the current for – many factors can affect how long it takes to heat the steel up enough for the two pieces of sheet metal to weld together. You need to practice and you’ll notice the color, sound of the welder. the amount of time it takes to get a good weld and especially the feel of the clamps as they come together during the weld. With practice you’ll feel when you have a good weld especially but it all adds up but you need to actually do it to learn.
Get scrap metal of about the same thickness to practice with. AKM receivers are 1mm thick. 18 gauge is 1.02mm so it is good to practice with and old scrap receiver stubs are another. With your first practice weld, go long and let the pieces really melt together so you can see. You want to burn a hole to understand how long it takes, the sound and the feel of the tongs. Then practice with less amounts of time until you find the sweet spot. These welds should be pretty strong and not pull apart easy. I do more spot welds than most and some guys look at photos of the rifle they are building and try to approximate the count and location, which is just fine. One thing, if you do heat treat your rails before hand like I do, be careful you do not get the tongs up against the ejector and ruin the heat treat. I’ve done it and the tell tale sign is that the ejector will be discolored from the heat. If you do make this mistake you will need to heat treat the tip while it is in the receiver or else it will definitely peen over and be deformed in its softened state. By the way, the steel should be relatively clean also and not have tons of grease or other contaminants on it either that might inhibit a good weld.
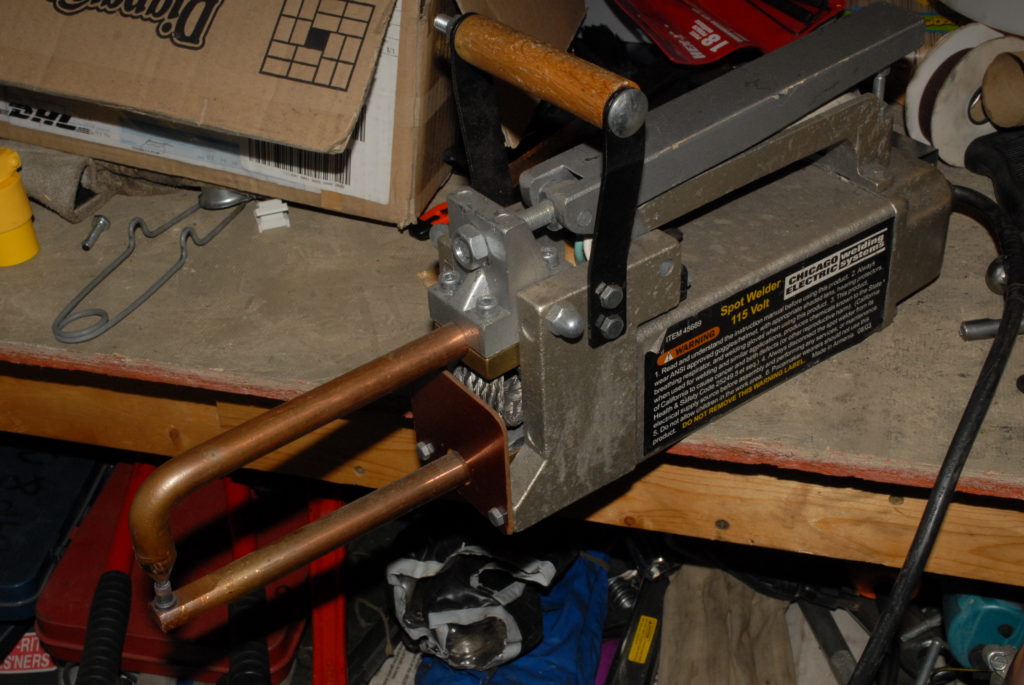
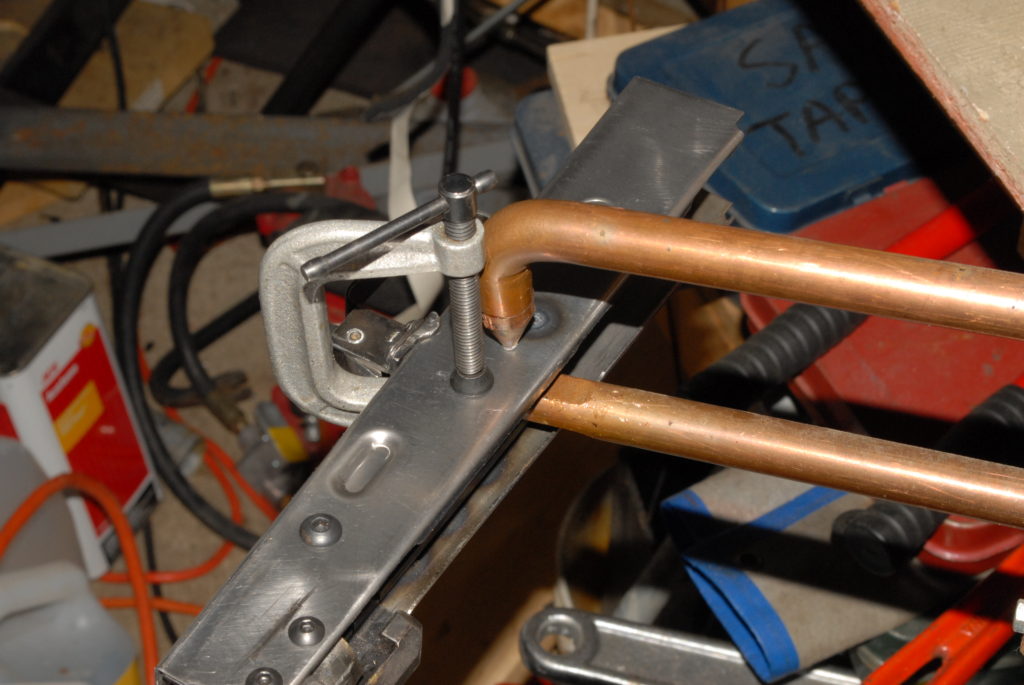
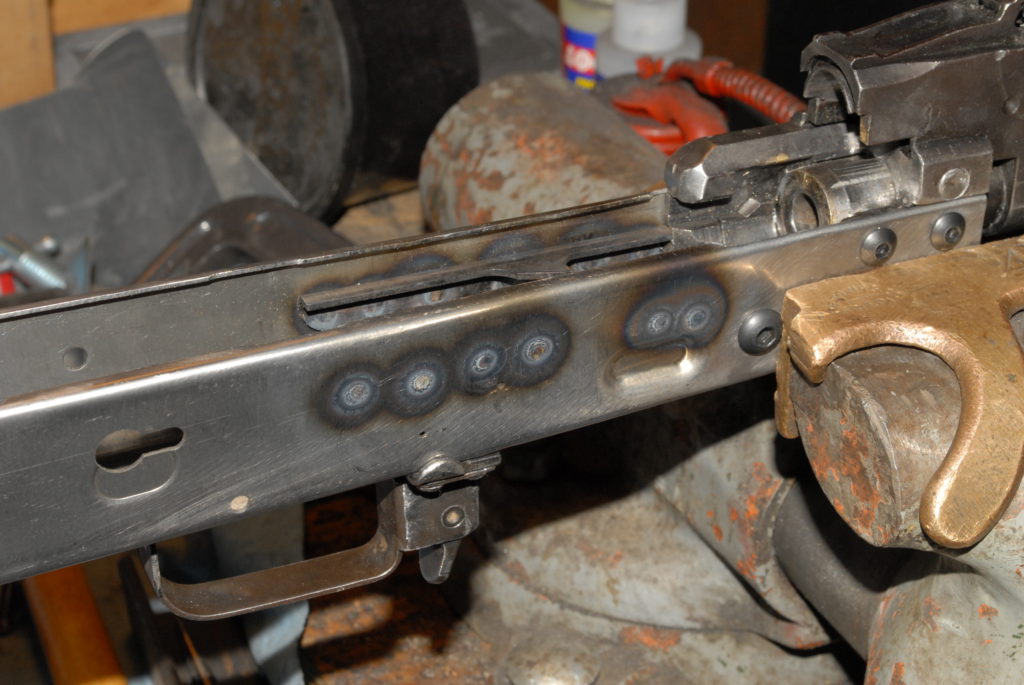
Just double check alignment very carefully before you spot weld and also that your welder’s tong does not get against the ejector and ruin the heat treat – assuming you did that before installation.
I hope this helps you out!
If you find this post useful, please share the link on Facebook, with your friends, etc. Your support is much appreciated and if you have any feedback, please email me at in**@*********ps.com. Please note that for links to other websites, I may be paid via an affiliate program such as Avantlink, Impact, Amazon and eBay.
Converting a Milled M70 Front End for a Sheet Metal Receiver Using Screws
Let me open this article with a comment for people new to building AKs – the best proven method is to use rivets. The Soviets did a lot of testing and the best mechanical join of the forged trunnions to sheet metal was a mechanical rivet. To this day, all commercial and military AKs are built using rivets. In my journeys, I have built AKs using welds, screws and rivets – all have pros and cons. What would I build an AK with that I care about? The answer is easy – rivets. This blog post documents my building a prototype using screws. Has it held up to casual non-military non-full-auto use? Yes. What would I recommend to you to build your AK? The answer is rivets.
In a previous post I described taking a milled stub and welding it to a sheet metal receiver. Another approach is to drill, tape and use alloy screws. So, let’s talk about that a bit. I did this build back in 2010 also. I actually still have the rifle and it’s one of my most reliable AKs. It takes about any ammo I stuff in it and I don’t recall ever having any issues.
For those of you who are wondering why I didn’t do rivets – I was bored and wanted to try something different plus this is a range gun and not something mission critical. Here we are 7 years later and it’s still doing fine – no cracks, no loose screws … but it isn’t stressed either. When in doubt, do rivets or a milled gun.
Also, bear in mind that the front trunnion was made from the milled receiver stub so screws made it real easy.
In terms of this build, I milled the trunnion down the same as I did for the weld build. I used my Hungarian AMD trunnion as an approximate guide for locating the holes and used two #10 screws for the front top and a 1/4″ for the rear. In both cases, I opted for national fine. 10-32 and 1/4-28. So, for 10-32, I used a #21 drill bit to make the hole and for the 1/4-28, I used a #3.
For drill locating and drilling the receiver holes, I used the AK-Builder trunnion rivet locating jig. You just put the trunnion on the jig, locate the hole, slide the receiver on and drill the hole.
Now for tapping, being square is a good idea. I squared my table to the drill press’s chuck and used it to hold the tap. I use Tap Magic cutting fluid to lubricate everything.
For the screws, I used alloy button heads and secured them with red thread locker. I reached in with a Dremel and ground down protruding screws.
So there’s the front. I used an air riveter to do the trigger guard.
End Result
Here’s a link to the AK-Builder Trunnion Hole Jig.
If you find this post useful, please share the link on Facebook, with your friends, etc. Your support is much appreciated and if you have any feedback, please email me at in**@*********ps.com. Please note that for links to other websites, I may be paid via an affiliate program such as Avantlink, Impact, Amazon and eBay.
How to Bullet Drop Test a Barrel?
Plenty of AK barrel have seen heavy use and some are pretty much sewer pipes at this point – blown out, dirty and most of the rifling a distant memory. A quick way to check is to take a cartridge of the correct caliber, such as 7.62×39, and put it in the muzzle. If it stops before the case hits, there is hope. It the case hits or even goes into the muzzle, the barrel is pretty much history.
Pass:
Fail:
I’m not saying the barrel is perfect but it may still be useful. I built both M70 stubs on their original barrels and they shot good enough – about 8-10″ – at 100 yards fired with iron sights with cheap ammo. Still a fun rifle to shoot though.
If a barrel fails, I would definitely get a replacement and not even bother trying to use it but that’s just me. I’ve known a few guys over the years that proudly built and fired sewer pipe rifles.
Converting a milled M70 receiver stub to a stamped receiver front trunnion using plug welds
I miss building AKs – I never have the time any more. At rate, some years back I wound up with two Yugo M70 front milled stubs, and then decided to convert the rifle to a stamped receiver because I liked working with AK-Builder flats. So, in the spirit of trying something new, I decided to convert a stub to a trunnion and plug weld it in place vs. trying to machine the rivet seats inside.
Yes, I’ve heard tons of people say not to weld them together and that rivets are better. Yes, rivets are better and I have done many of them. Have I ever had problems with a weld build where I filled the holes I drilled with plugs, stayed away from the locking lugs and was careful with the heat? No, I have not had any problems. I have an AMD-65 with tons of rounds through it that still runs fine. My thinking is that I am not firing full auto, not using grenades, don’t use this in combat … I’m not really stressing it. What would I use for a reliable build vs. a test like this? I’d use rivets.
Why the big caveat in the previous paragraph – I get one or two emails a year from a purist telling me that what I did was evil, that I am a clueless half-wit, etc. Folks, innovation happens by trying new things. I have built more AKs than most – using rivets mainly because they do work best. There are a ton of reasons why rivets are best for joining forged blocks to sheet metal. In terms of welds, do I understand the risk of destroying the heat treat in the locking lug area, the risk of causing embrittlement around the plug welds, that the Soviets explored this and dropped the idea due to cracking? Yes, I do and tried it anyway because I wanted to explore how to compensate. So, don’t send me hate mail me because I will not bother responding. When I first shared this, three guys immediately sent me hate mails and unfriended me – I did not lose sleep about it. If you want to try and experiment, go for it. Should you do this with an AK build that you want to be historically accurate or plan to use heavily perhaps even under full auto, then the answer is “no – don’t do it”. |
The build I am sharing photos of was done in 2009. I found the photos and thought you might like to see them.
Here are the front stubs.
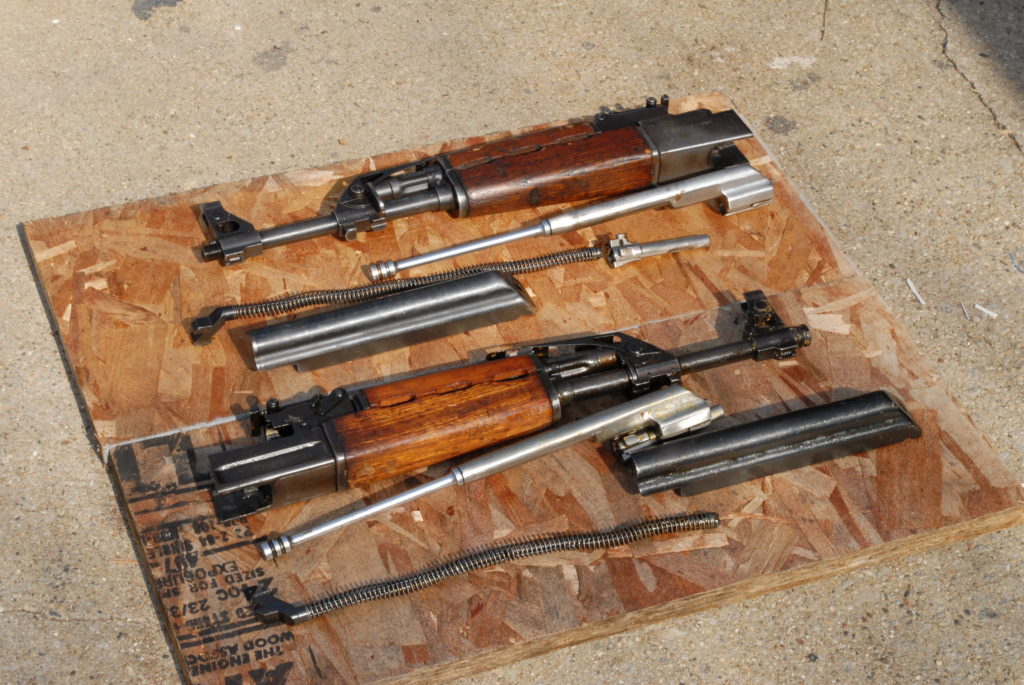
When you look at the front stub, you can see readily hiw it could become a trunnion.
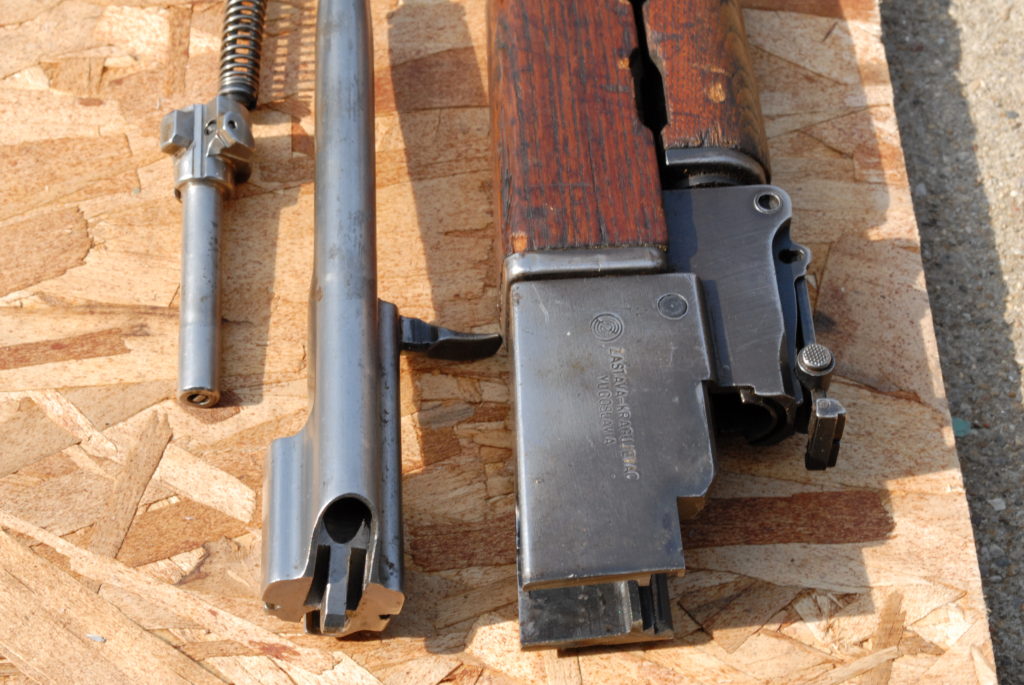
Here’s a Hungarian AMD trunnion next to it.
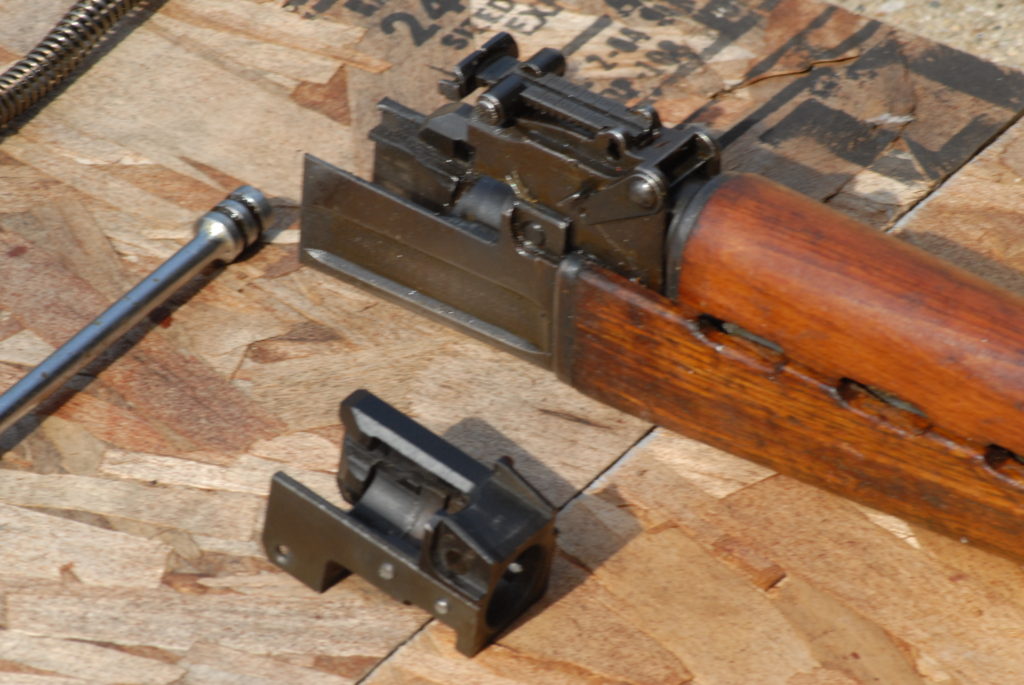
Here are the stubs from a couple of angles. I already used my bandsaw to cut the top one
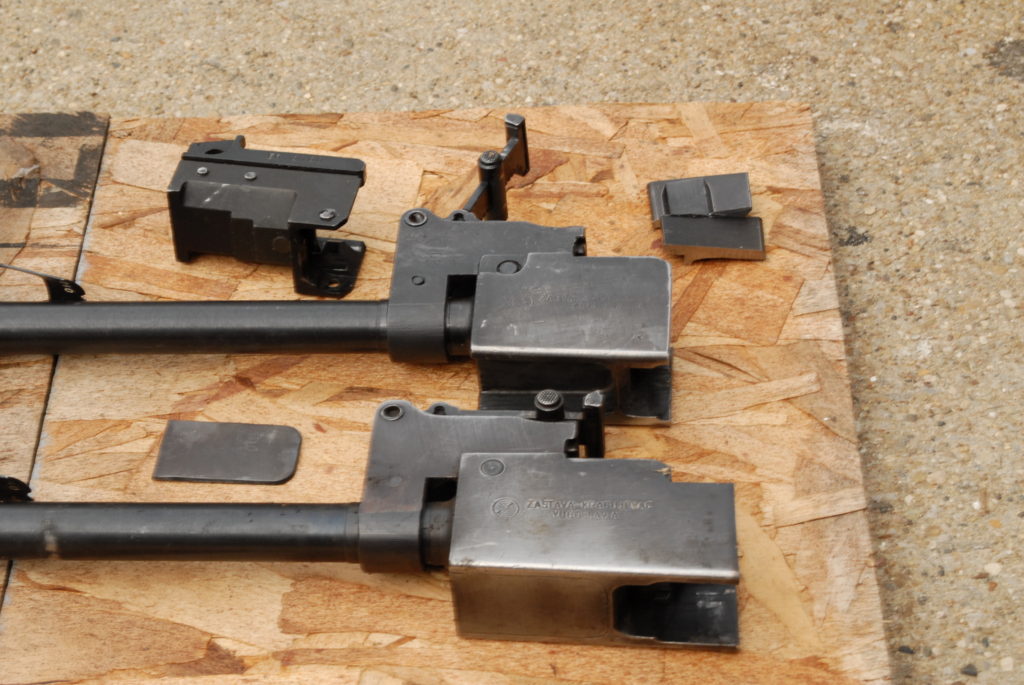
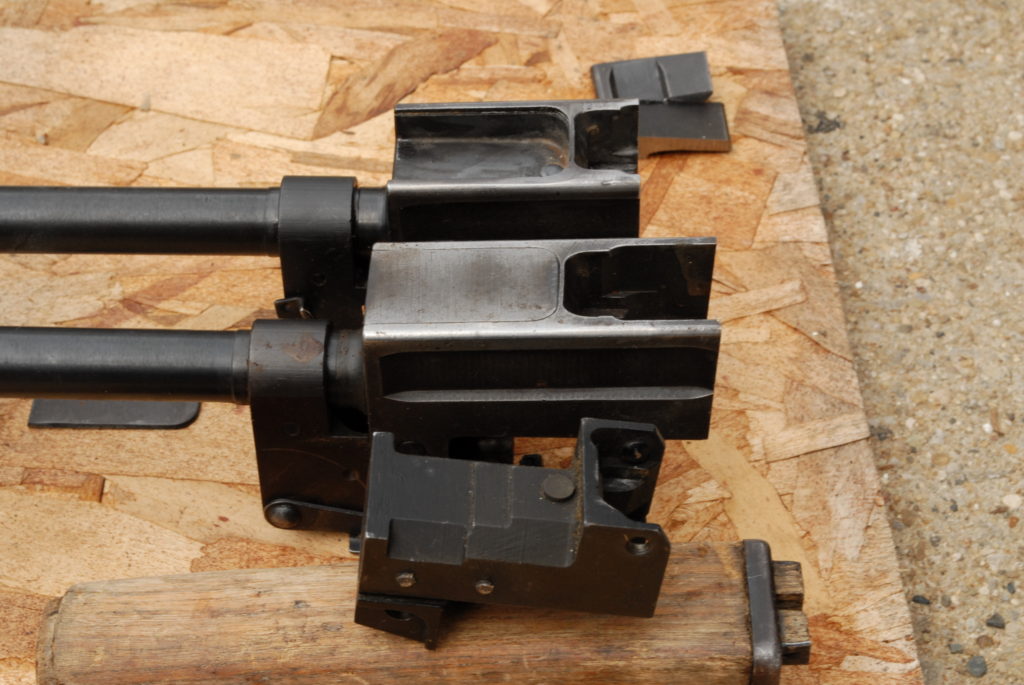
Ok, time to make some chips. It’s secured an I’m milling the OD under the top shelf of the trunnion that sticks out over the receiver:
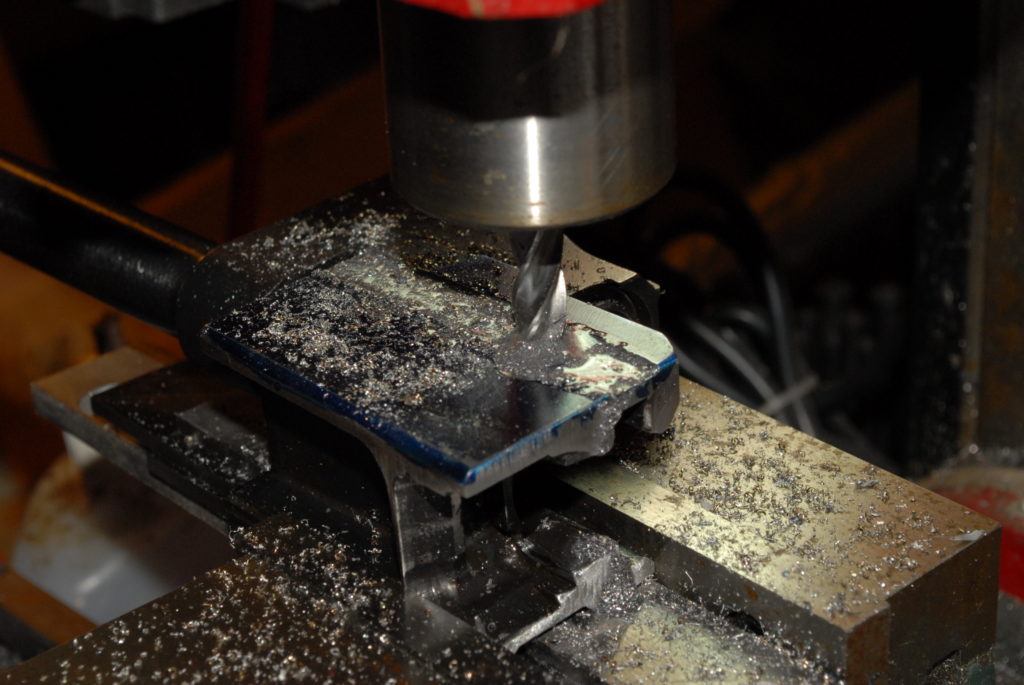
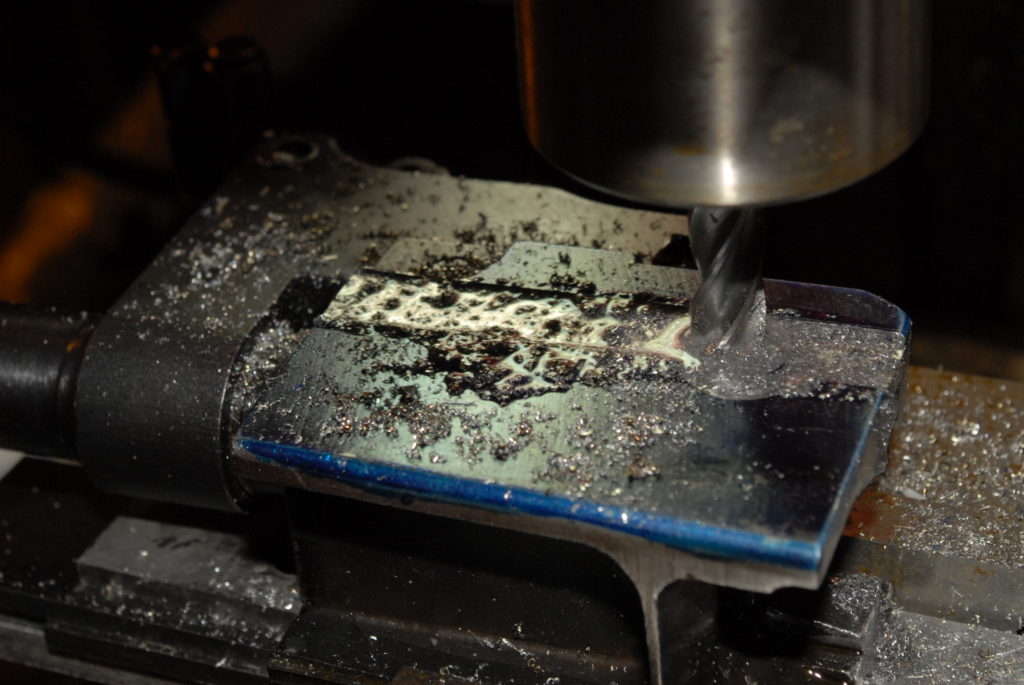
I didn’t have anything to cut the slot with for my mill so I clamped a straight edge and then ran a Dremel wheel down it over and over until I got the depth and width needed for the stamped receiver to to slide into:
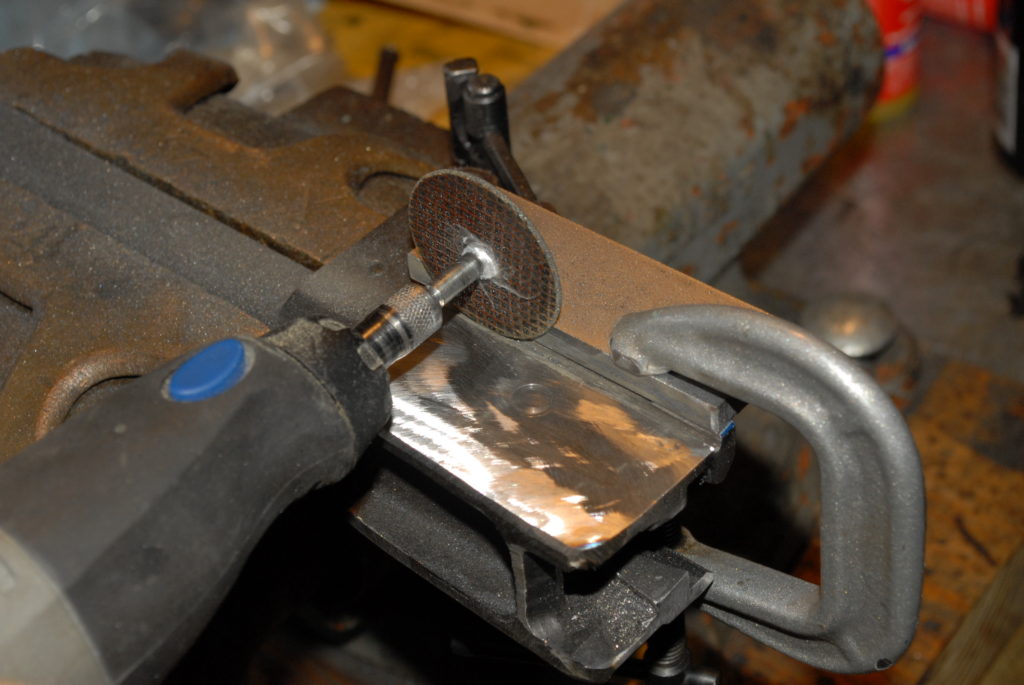
My theory was that by drilling holes and filling them via plug welds that I could lock the receiver into place. Thus, I drilled holes for the plug welds both in the stamped receiver and into the newly made trunnion:
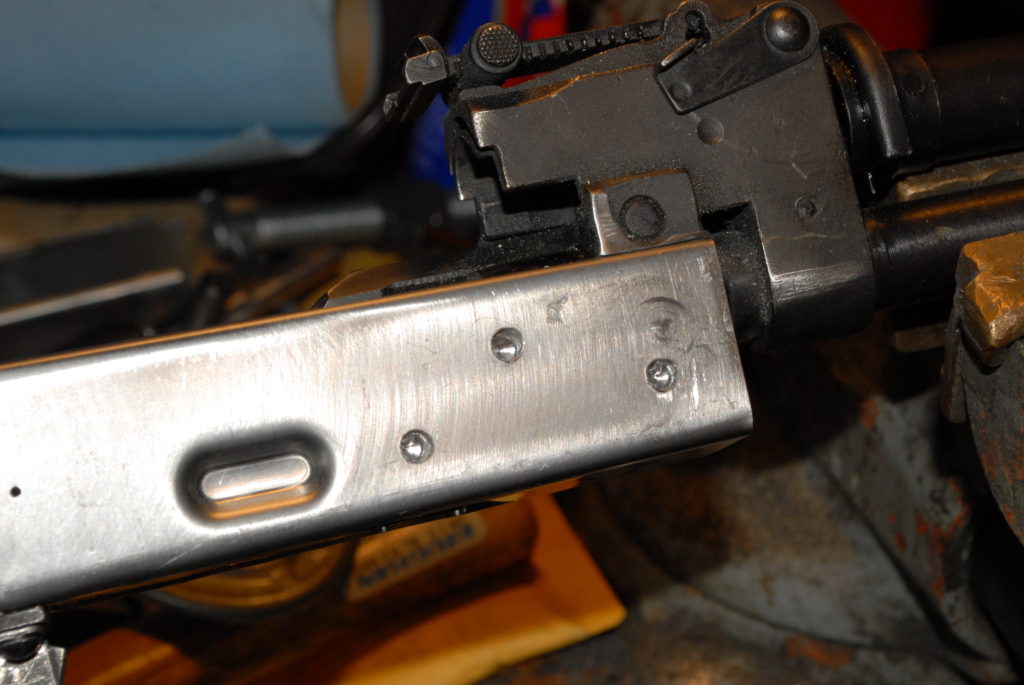
The plug welds were done with a Harbor Freight 220V MIG running ArCo2 gas and .030 wire. I let it cool down after each weld and was careful not to pour on a ton of heat. Notice the relatively big weld area to distribute the load.
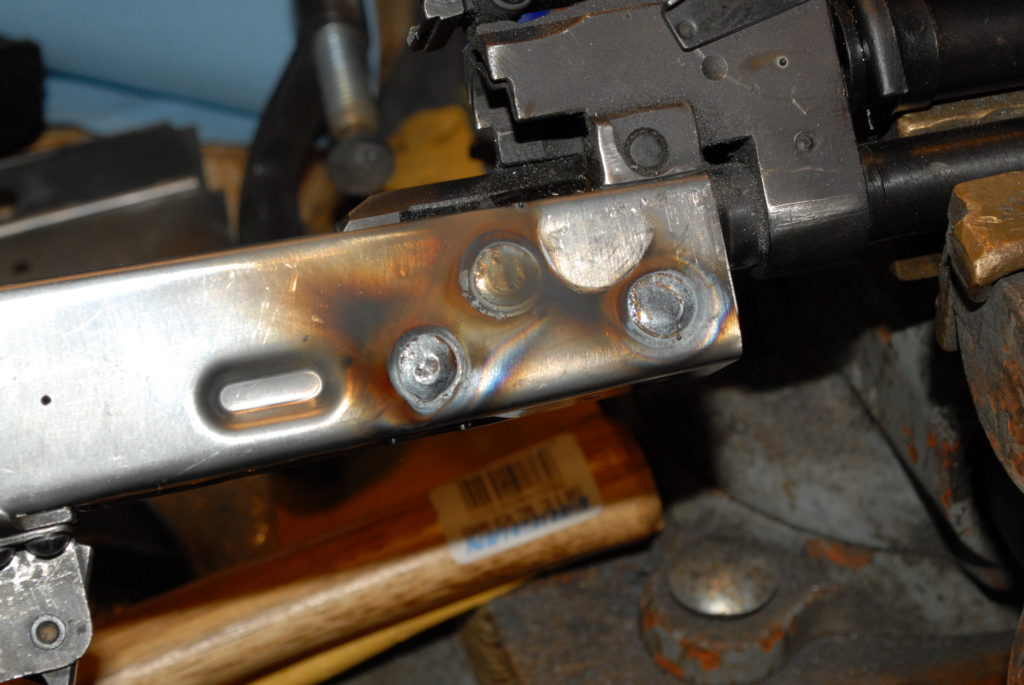
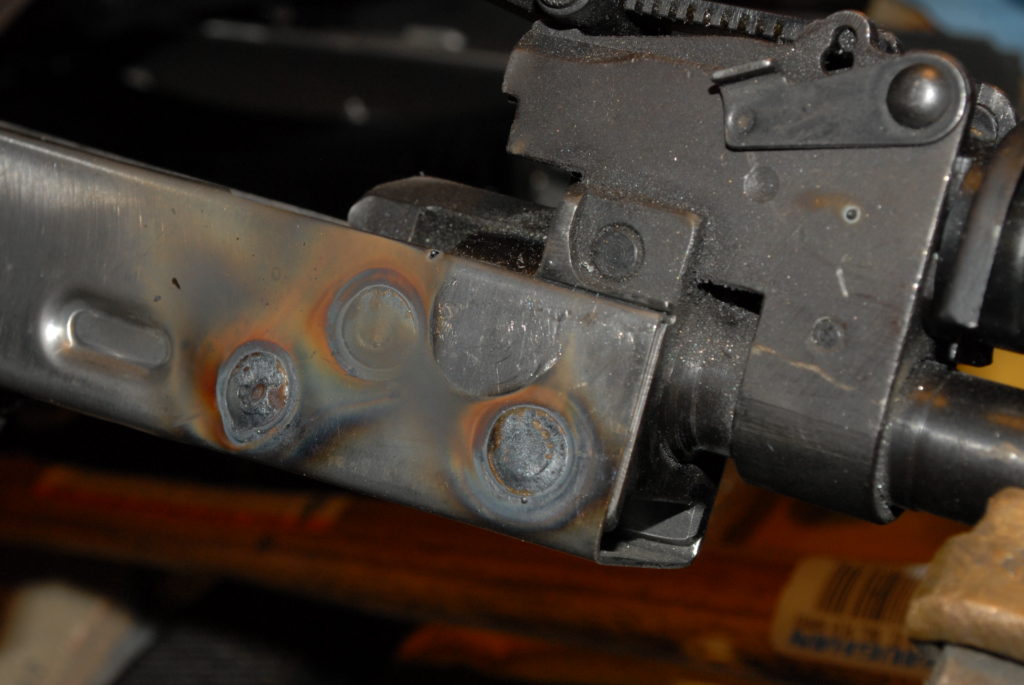
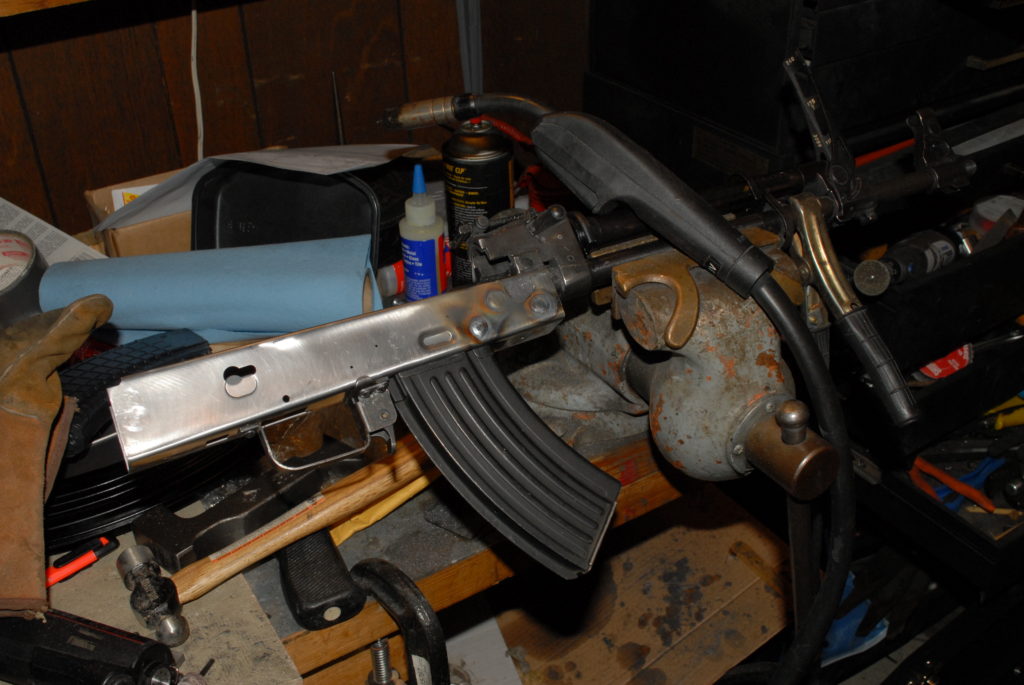
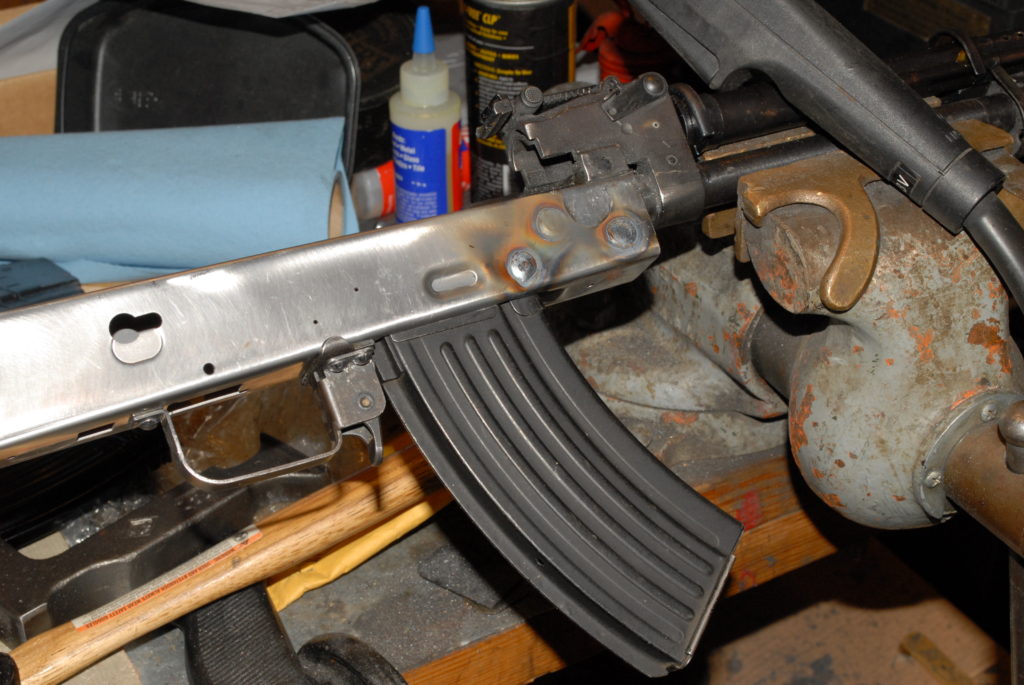
I then sanded it all down with a flap sander. The back was just a regular M72 rear trunnion that I found at R-Guns. I never had problems with cracking, etc. The experiment seemed to work for a casual use semi-automatic rifle.
That’s all I have as far as photos go. I hope maybe it gives you some ideas.
Writing this makes me wish I had time to build another AK but it’s back to our grips and handguards 🙂
Note, I have to buy all of my parts – nothing here was paid for by sponsors, etc. I do make a small amount if you click on an ad and buy something but that is it. You’re getting my real opinion on stuff.
If you find this post useful, please share the link on Facebook, with your friends, etc. Your support is much appreciated and if you have any feedback, please email me at in**@*********ps.com. Please note that for links to other websites, I may be paid via an affiliate program such as Avantlink, Impact, Amazon and eBay.
Custom Yugo M72 RPK By Two Rivers Arms and Ronin’s Grips
Two Rivers Arms is an impressive group – they can really build Yugo rifles (and just about any other AK for that matter). I recently had them build a replica M72 RPK that looked like it came fresh from the factory. I also had them build this rifle and it took some creativity on their part and our’s.
I sent them a Yug0 M72B1 kit from Apex with a Green Mountain barrel, Tapco FCG, Nodak Spud NDS-9 receiver and asked that they turn the barrel down to 16.5″ and not bother with the bipod. I also asked Tim to fabricate a scope rail so I could mount my RS!Regulate rail system there. Thus, they got started and did their assembly and tuning of the rifle. As many of you know, AKs can be pretty gritty until they wear in. The guys at Two Rivers have tuning the AK down pat and when it arrived, everything was silky smooth. By the way, I had them put the original funky wood on it so it looked pretty funny when it arrived and then I went to work.
We’ve been working on a custom M72 RPK handguard set off and on all year. First we had problems with the gas tube and then the lower turned out to have issues twice! Finally, with this generation, we nailed the M72 handguard set and I am very happy. You’ll notice it is very thick as the mold was cast from wood originals and is a very snug fit.
What you see in these photos is the M72B1 rifle from Two Rivers but to it I have added our custom Yugo M72 handguard set, a custom Bulgy Arm-9 grip and one of the Magpul ZHUKOV-S butt stock with the 3/4″ riser as I needed to get my cheek into better position to look through one of my favorite Vortex Crossfire II 1-4x scopes. These are one of the best values in scopes in my opinion.
I also replaced the original Yugo hammer and operating springs with fresh ones from Falcon Arms to give everything a bit more life. To top it off, I added a Precision Armament M4-72 AK-47 Severe-Duty Compensator.
The rifle about 1/2″ groups at 50 yards with Golden Tiger FMJ. I am very happy with the results. The rifle handles great and between the weight and the aggressive Severe-Duty compensator, recoil was very, very mild.
Here are some photos of the rifle:
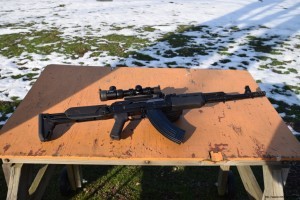
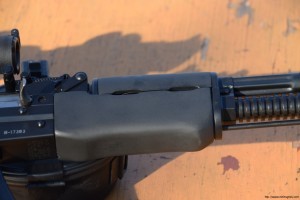
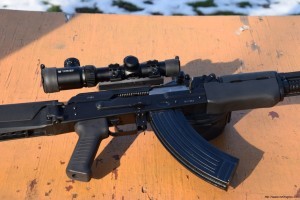
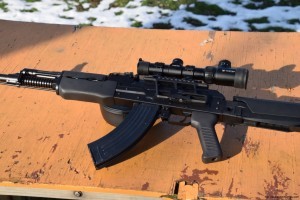
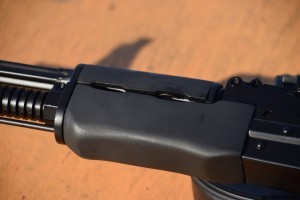
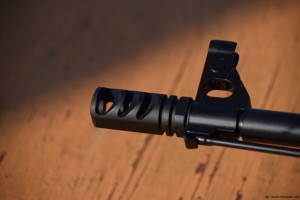
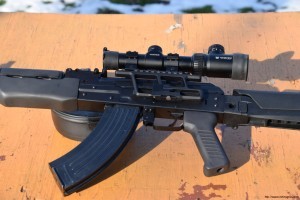
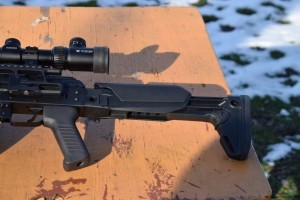
If you are interested, here are some links:
Our M72 Handguard Set: http://shop.roninsgrips.com/Yugo-M72-Handguard-Set-No-Ferrule-Needed-YugoM72RPKHGSetNoFerrule.htm
Our Bulgy ARM-9 grip: http://shop.roninsgrips.com/Bulgarian-ARM-9-Grip-Converted-For-All-AKs-No-Notch-w-Screw-BulgyARM9NoNotchWithScrew.htm
Two Rivers Arms is at: http://tworiversarms.com/
Precision Armament Severe Duty Compensator: http://precisionarmament.com/product/m4-72-ak-47-compensator/
Magpul Zhukov-S Stock: https://www.magpul.com/products/zhukov-s-stock-yugo
Falcon Arms Springs: http://www.falconarms.com/ak47/ak-spring-kit.html
If you find this post useful, please share the link on Facebook, with your friends, etc. Your support is much appreciated and if you have any feedback, please email me at in**@*********ps.com. Please note that for links to other websites, I may be paid via an affiliate program such as Avantlink, Impact, Amazon and eBay.