A few years ago, I bought a 1969 Polish Radom Circle 11 AKM kit from Arms of America. It has laminate furniture, matching parts and they populated a new Polish Chrome Hammer Forged (CHF) barrel with the front, gas and rear sight blocks. Furthermore, it was headspaced. I double checked that before I pushed out the barrel pin and then the barrel – that’s where things got interesting.
Pressing Out The Barrel
I have a 30 ton H-style hydraulic press with a 20 ton air-over-hydraulic bottle. The thing is a brute and have used it many, many times over the years on gun and car projects. There are a few things you learn over the years – 20 tons is 40,000 pounds and is a serious amount of pressure – steel parts can bend, break or even shatter under those loads. You learn to go slow, watch carefully feel the pump and listen. I also learned long ago to use the air to move the ram quickly but always do the real work by hand for those very reasons – I’ve bent the crap out of stuff in years past because you can’t tell what is going on.
I wear a full face shield when working with a press. I’m not joking when I say things can go bad fast when there is a lot of pressure. When you push out a barrel, you just don’t expect a ton of pressure from a new kit – at least I don’t. I’ve had some real hairy barrel pins and barrels in years past when dealing with surplus… but not on a new kit with a populated barrel … not until now.
Pressing Out the Barrel
As you can guess, the barrel did not press out easily. I had to apply a boatload pressure – way more than average. So much that I put a 3/4″ piece of plywood between me and the trunnion/barrel assembly. I was also checking and double-checking that my barrel press tool squarely on just the barrel and not a part of the trunnion – guys I was nervous.
I reached the point where I knew I was squarely on the barrel and something had to give. I was whacking on the press trying to shock the barrel out and I kept upping the pressure – pump, whack, pump, whack… Finally the barrel came free like a gun shot. Guys- do you remember the old Romy kits where the pins and barrels sometimes felt like you were taking your life into your own hands? That’s what this felt like.
I actually inspected the front trunnion very carefully looking for cracks. I then inspected the chamber end of the barrel – nice and smooth – remarkably smooth. No signs of galling. Ditto on the inside of the trunnion. I suspect that someone was using some kind of press system that included a barrel support and slammed that new barrel in using a level of force I couldn’t do without damaging parts. I noted to myself that reassembly was probably going to be just as colorful.
Building The Kit
Nothing new about building the kit – I had fun. In the below photo, the front trunnion and rivets are just sitting there. I was mocking things up and they are not actually set. I installed the trigger guard taking care to orient the selector stop properly and using a rubber band to keep the assembly together as I used my press and an AK-Builder trigger guard rivet jig to do the job.
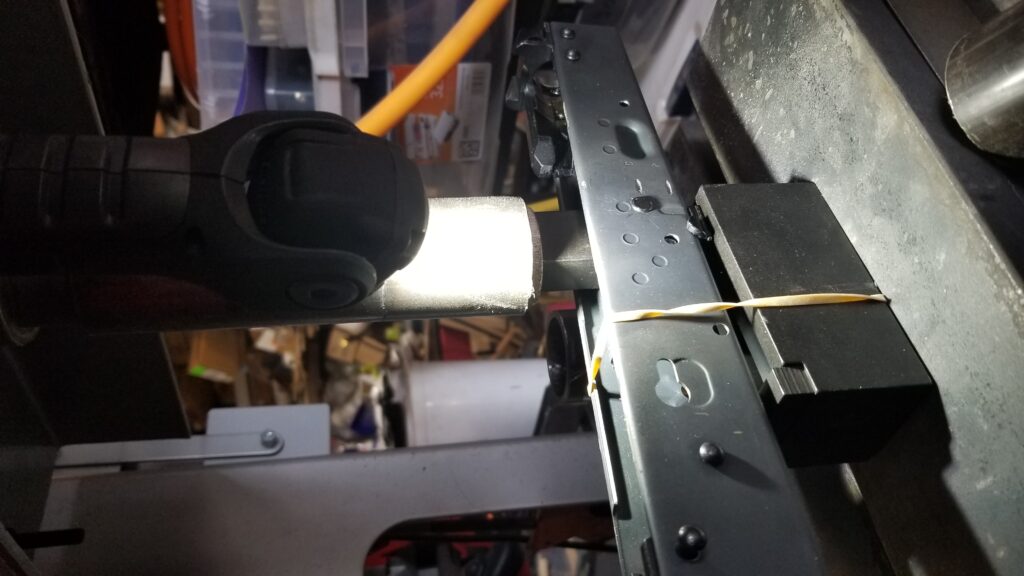
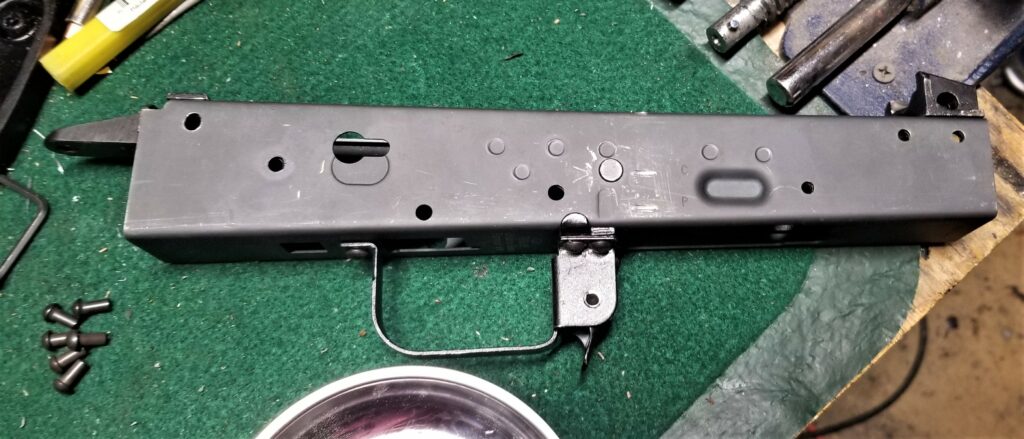
So let’s get back to the main point of this blog post and why you are probably reading this – what do you do when the interference fit is too tight and the barrel will not go into the trunnion all the way.
Life Got Colorful Trying to Press The Barrel Back In
Yeah, that tight fit came back to haunt me. I tried polishing the trunnion and applying non-seize. Usually this works for me but when I went to press the barrel back in, it would not go. I saw the barrel begin to deflect in the press and immediately stopped. Let me explain what I mean by deflect – a material will bend so much and spring back into place. When I saw the barrel begin to deflect, I immediately stopped – it was taking way too much pressure and I was risking bending the barrel permanently. It was time to press the barrel back out and rethink the situation.
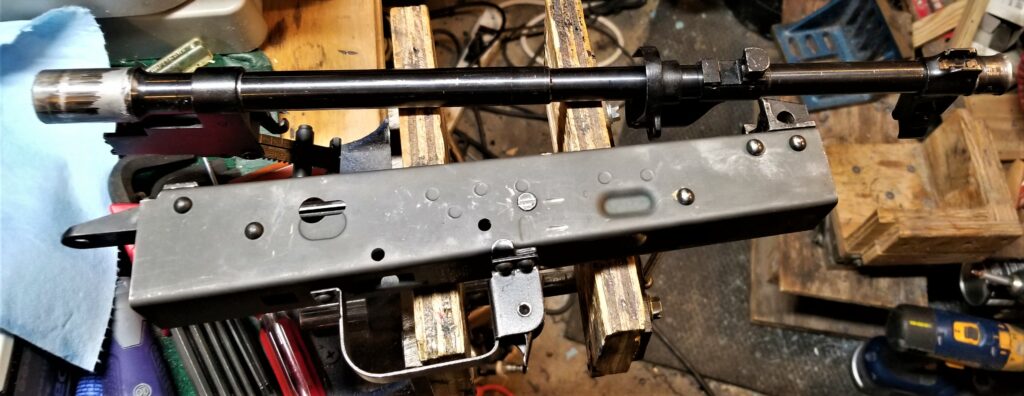
So, what this confirmed for me was the someone slammed this thing together – hard. An AK barrel is press fit into the trunnion. To do this, the barrel is a tad bigger than the hole made for it in the trunnion by about 0.0010-.0026″ (0 .025-0.065mm) according to Robert Forbus who is a true machinist and has shared a ton with the AK community – click here for his page). At the tighter end (around 0.002″) it is getting hard, if not outright impossible, for someone to press the barrel into the front trunnion without the proper specialized barrel press equipment that supports the barrel. I have a big press but nothing to properly support the barrel in these high-pressure situations. It would likely warp like a wet noodle if I just kept adding pressure.
I don’t own a machine shop but I am a redneck with a shop. I needed to open up the barrel channel in the trunnion and opted to use an OEM brand brake hone. Why? Because I’ve used these small bore hones in the past for other things and was pretty sure it would work for this too.
There are tons of brake hones on Amazon. Click here to open a tab and see them. |
I also need to point out that I have no way to accurately measure the barrel or the trunnion so I figured I would remove a bit and try to install the barrel, remove a bit and try, over and over until it went in. The next picture shows my OEM hone (and the Lisle is virtually identical):
Take a look at the above picture – by tightening the knurled nut at the base of the spring, you can apply more and more pressure to the 220-grit stones at the end of the arms. (The Lisle tool’s stones are 240 grit purely FYI – not a big difference.) I just used the basic pressure and did not increase it. Life lesson for me years ago – it’s easier to take more material off than it is to put it back on.

I applied cutting oil to the trunnion liberally and then slid the hone in and out with my drill on slow speed. I would do this for a bit, clean stuff, and then tested how far the barrel goes into the trunnion by hand and then keep removing more. This is not the time or place to get impatient.
By the way, OEM makes fine 400 grit stones that you can swap into place and use to polish the interior further if you . I got the job done with the 220 grit stones and silver Permatex anti-seize compound. If I had the 400 grit stones handy at the time, I would have done so but I did not. Also, be sure to clean out the grit/dust before you try to reinsert your barrel.
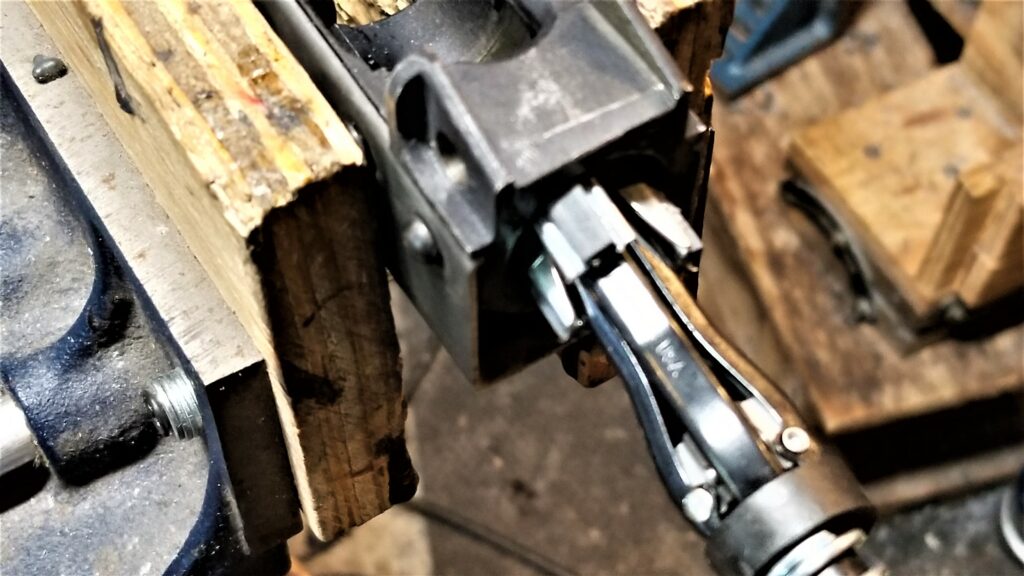
This is a down and dirty “git ‘er done” approach and will make machinists cringe. I go slow and test — I would push the barrel in, test and the press it back out if need be. [Click here to see how to make a barrel backout tool].
*IF* you see a bur or squished rivet protruding in the trunnion, then carefully grind that down with a Dremel and polish with the hone. Don’t try to do it all with the hone or you will be removing material elsewhere that you may need – the arms are spring loaded and independent so they will go where ever they can. This is a pro and con.
After a couple of tries, the barrel went all the way in with the press. To be safe, I confirmed the head space using real Manson brand 7.62×39 gages (use real gages folks and treat them well – don’t go cheap). The barrel headspaced just fine so I pressed in the pin and finished the rifle up.
Bottom line, a brake hone can help you carefully remove steel from the front trunnion and get a tight fitting barrel to go in. It worked wonders on this 1969 cold warrior that is now ready to go to the range.
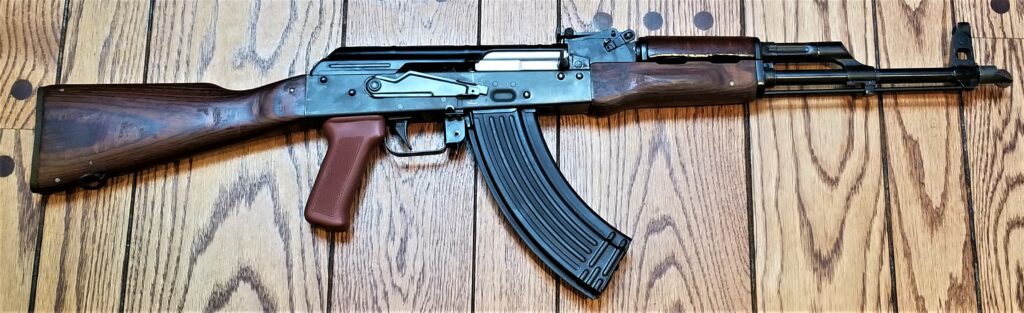
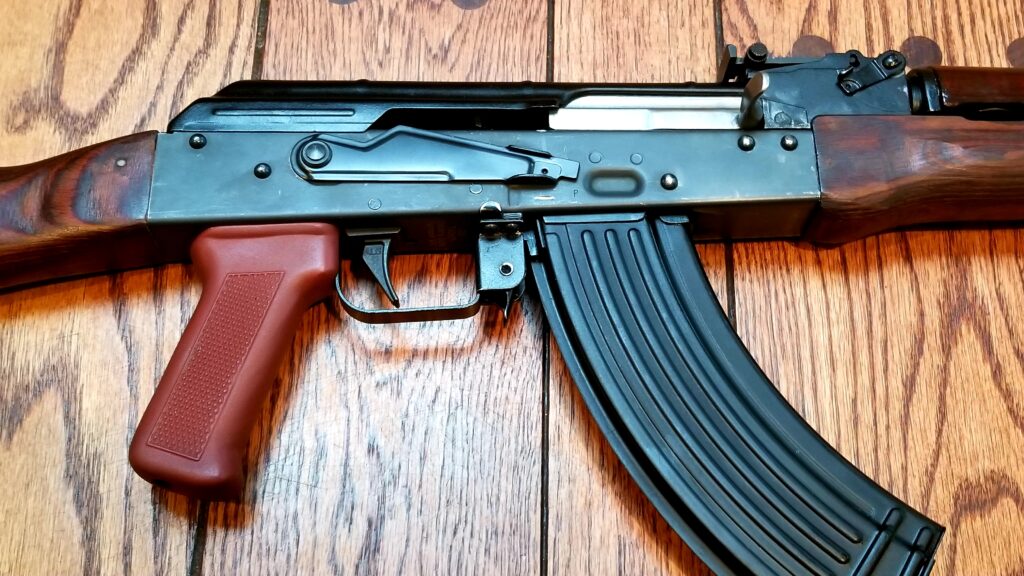
Click here to learn more and order one of our Polish Tantal/AKM grips.

One of our fire control group retaining plates. that fits all AKMs and rifles that use standard AKM fire control groups.
It also has an ALG fire control group – they are awesome triggers – and one of our fire control group retaining plates. Click here for our fire control group retaining plates.
If you find this post useful, please share the link on Facebook, with your friends, etc. Your support is much appreciated and if you have any feedback, please email me at in**@*********ps.com. Please note that for links to other websites, we are only paid if there is an affiliate program such as Avantlink, Impact, Amazon and eBay and only if you purchase something. If you’d like to directly donate to help fund our continued report, please visit our donations page.