I recently did two posts about building a new heated tank out of PVC pipe and a digitally controlled heating element that is both effective and affordable. This also marked my first batch of blades where I moved from my traditional hot apple cider etching to using a mix of 70% ferric chloride and 30% apple cider vinegar heated to 90-94F.
The Chemicals
Let me give you a quick overview of the two chemicals I used to make my blade etching solution:
The primary ingredient is liquid ferric chloride from MG Chemicals. It’s available in quarts and gallons and is about 38-42% ferric chloride by volume. The MG Chemicals product is well regarded and that played a big factor in my selecting it. I purchased mine from Amazon and it arrived quickly and well packed.
The second chemical is regular apple cider vinegar from the grocery store. They tend to be normalized around 5% acetic acid by volume. The brand I used was at 5% and there were other brands at 4% that I passed over – go for 5% because you need the acetic acid. I literally bought this at my local grocery store – nothing special.
The solution I made was 70% of the ferric chloride and 30% apple cider vinegar. I wore lab goggles, nitrile gloves, old clothes and am in a well ventilated area when I slowly add the ferric chloride to the relatively weaker apple cider vinegar.
The ratio was based on looking at the end results from other blade smiths and talking about what they learned. In my case, I can tell you that this combination makes for a very nice dark etch.
The Process
- Heat the etching solution up to 90-94F before I put in the first blade. MG Chemicals recommends the operating range from 94F to 131F and not to exeed 131F. [Click here for their technical data sheet and MSDS]
- The blades need to be at least 70F prior to dunking in the solution. The warmer the solution and blade, the better chemical reaction you are going to have.
- Clean the blade with brake cleaner throughly
- Abrasive blast the blade – I am using Black Beauty these days. It is a coarse coal slag based product. Note, not all guys blast their blades – some just clean them very carefully.
- From this point on, wear nitrile gloves when handling the blades to avoid any oils and contaminants from your skin
- I again use brake cleaner to do a final cleaning and make sure it fully evaporates. Some guys rub down with acetone – do what works for you but it must not leave a residue
- Fully submerged the blade in the heated etching solution for 10 minutes
- Remove the blade and wipe off the remaining solution with a paper towel [as a reminder, you must be wearing gloves to not contaminate the blade]
- Used clean/bare 0000 steel wool to buff the surface of the blade and remove any loose particles. Note, this 0000 steel wool is bare wool – no cleaners or anything. You find these in woodworking / hardware sections of stores – not in the kitchen area.
- Submerge the blade for another 5 minutes and again wiped and rubbed the blade down with steel wool. I think I repeated this process three times per blade but experiment and see what works for you.
- Soak the blade in warm water with baking soda to neutralize the acid
- Spray the blade down with WD-40 to displace the water
- Apply finish – I like to use a 50-50 mix of boiled linseed oil and turpentine to apply severa thin coats. This gives my blades the worn post-apocalypse look. Many guys just coat the acid etched surface with oil to inhibit rust.
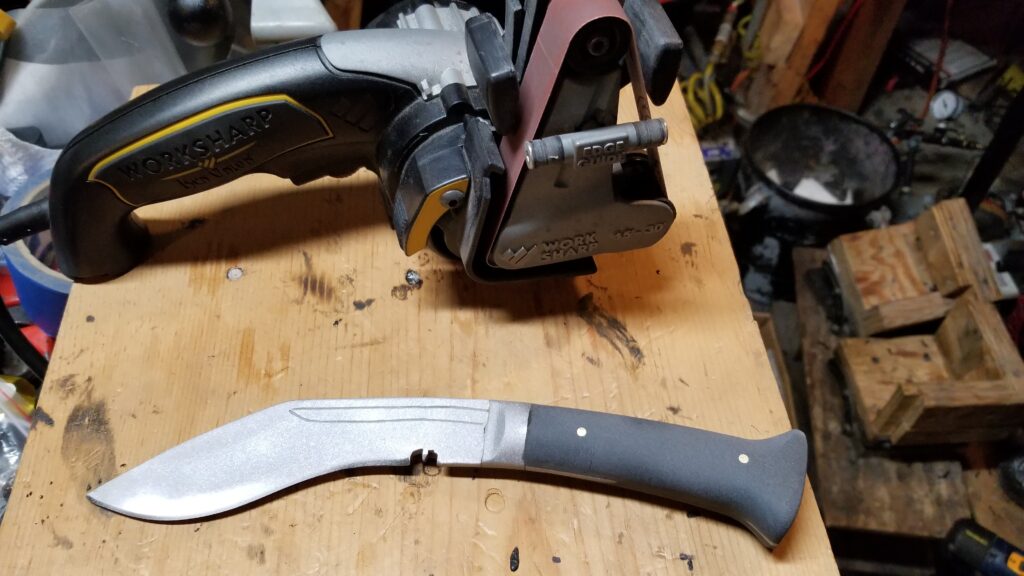
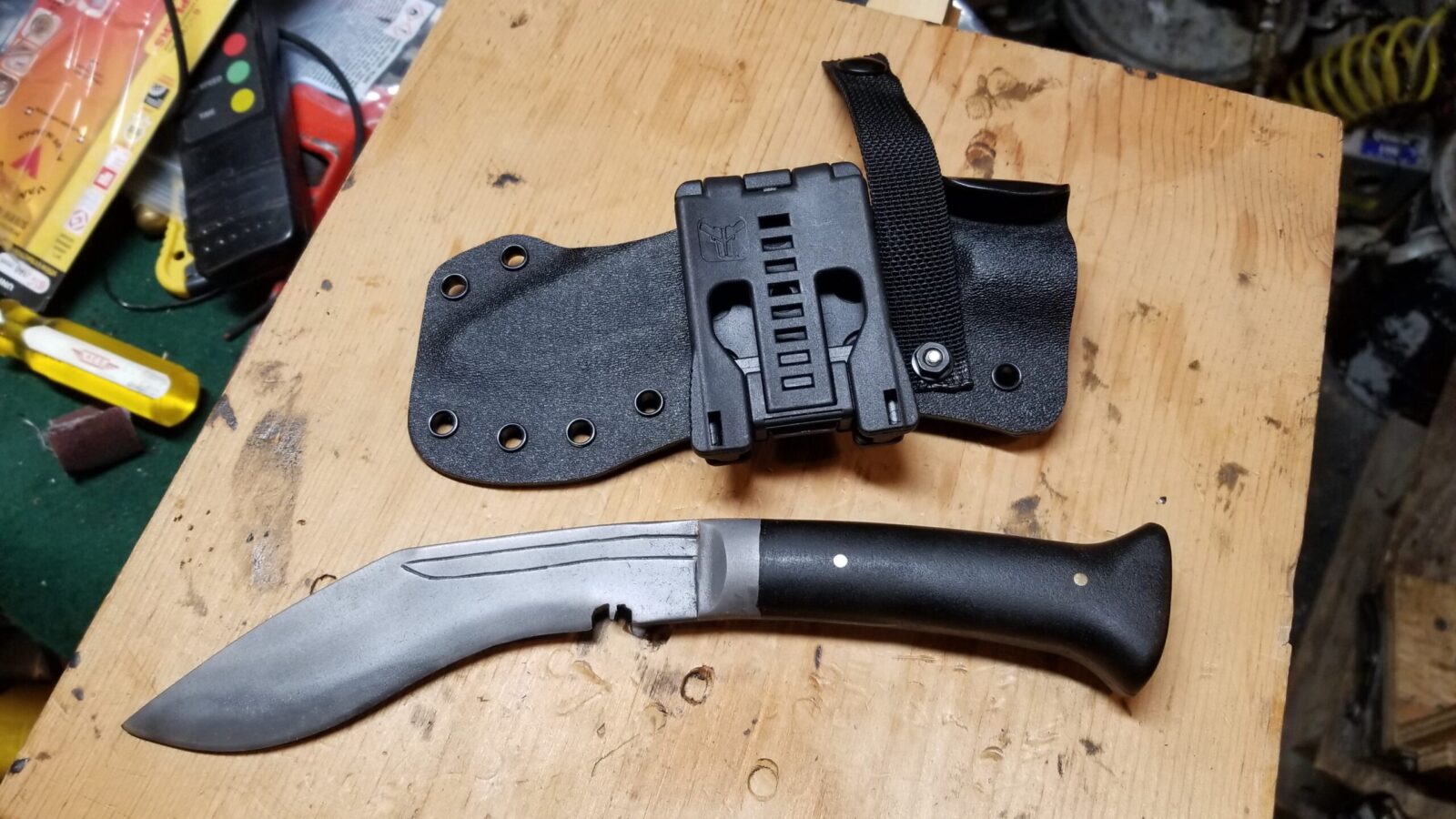
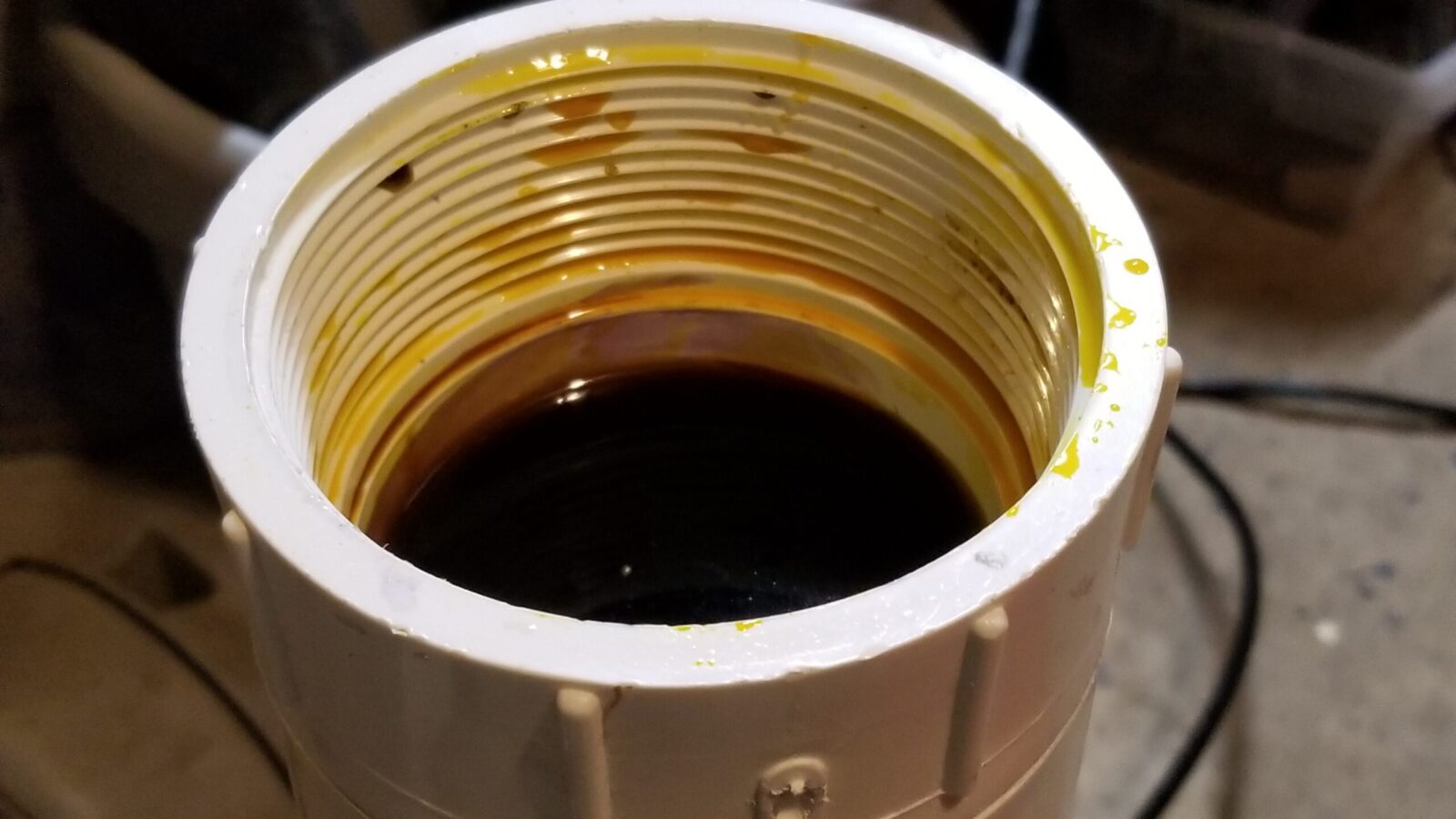
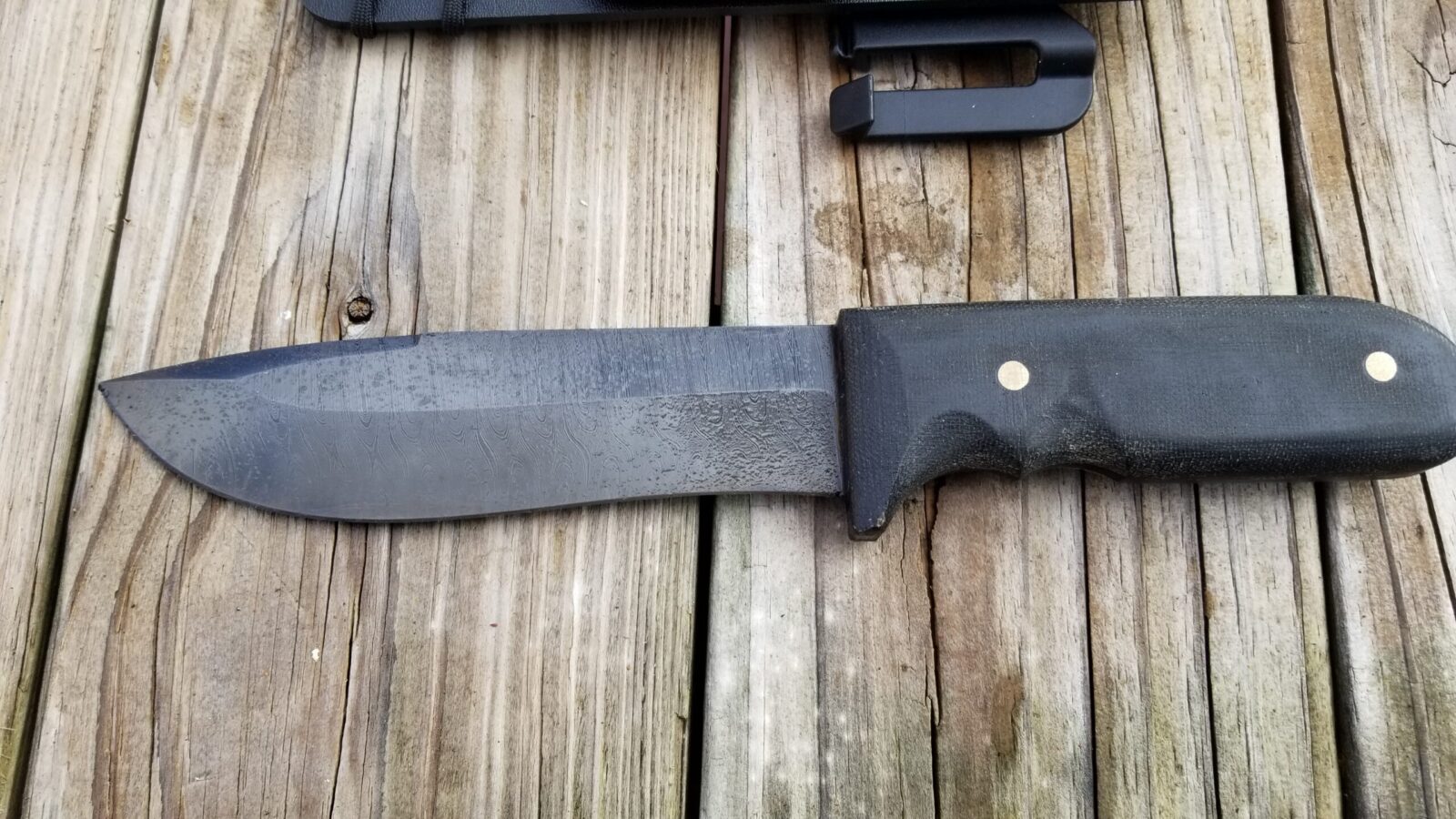
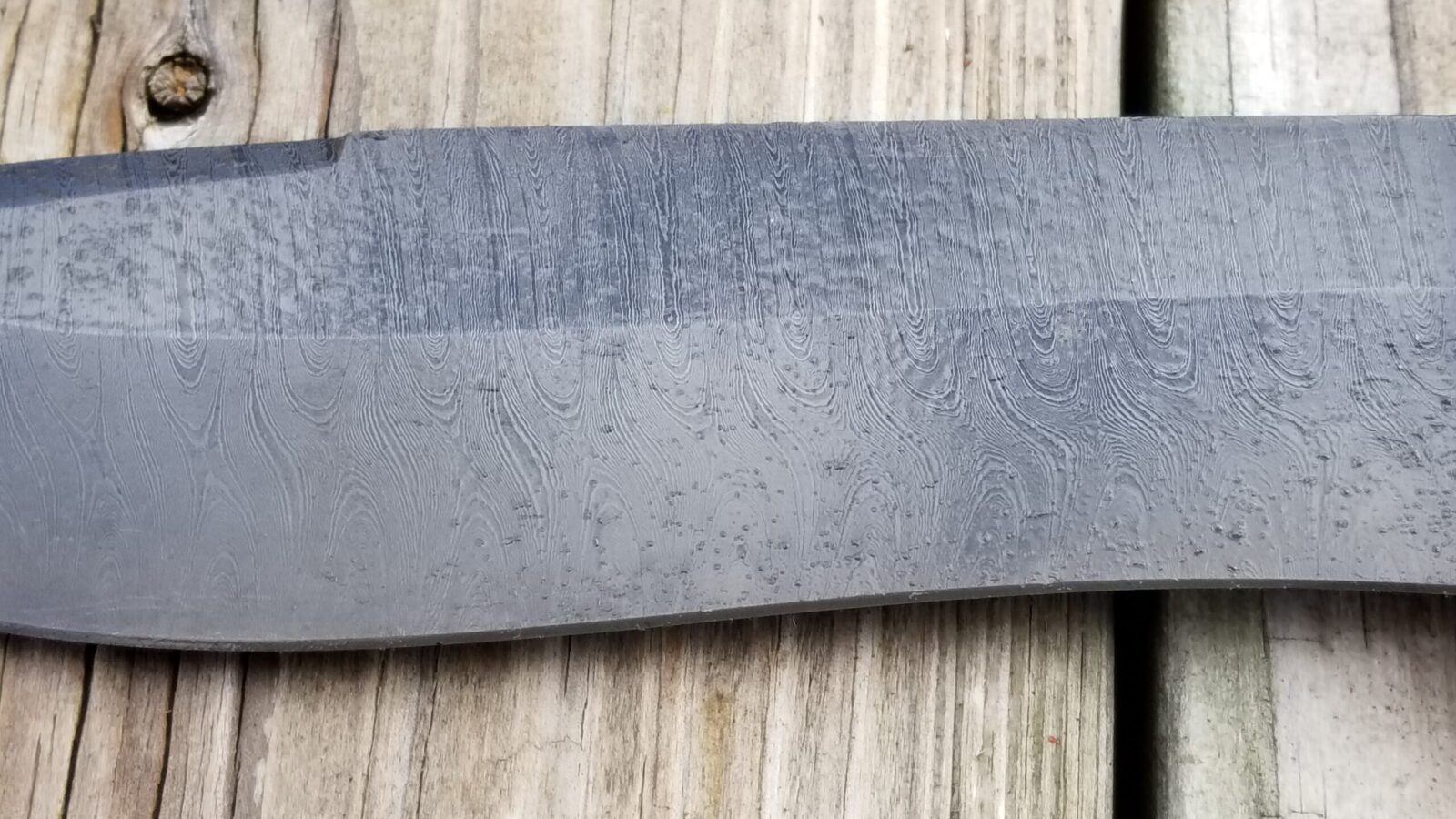
Summary
I’m definitely very happy with the results and will be using this solution going forward.
If you find this post useful, please share the link on Facebook, with your friends, etc. Your support is much appreciated and if you have any feedback, please email me at in**@*********ps.com. Please note that for links to other websites, I may be paid via an affiliate program such as Avantlink, Impact, Amazon and eBay.