In September 2021, I bought my first new truck – a 2021 Ram 2500 Tradesman. Something about it being straight forward without a ton of bells and whistles appealed to me and I managed to buy it – I’ll be making payments for four more years 🙂 At any rate, there were a number of things I did to customize it more to my needs – one area was lighting. For whatever reason, Dodge went cheap and used halogen bulbs and they were anemic.
The first thing I did was to buy a set of Lasfit LED replacement bulbs and upgraded the high beams. Wow – what a difference. I considered doing the low beams too but changed my mind. First, I could not get my hands into the low beam housings to make the swap without taking more of the truck apart. Second, after seeing how bright the high beams were, I was worried about blinding oncoming drivers so I just settled and left the low beams alone. I don’t really regret it – when I am on country roads at night and turn on the high beams, wow – there’s a HUGE difference.
Until you drive rural farm roads at night or go off-road, you don’t really appreciate having good lights. The new high beams were good but I wanted even better – I really wanted a light bar but I wanted it without making a ton of alterations to the truck. My 2500 has a cap and no roll bar or headache bar to mount on so that left the bumper, the A-frame or some form of roof mount. I did some thinking and decided to go with a non-traditional approach – I would mount the light bar behind the lower grill and add a yellow light bar for fog and snow below it angled downwards.
Legal Disclaimer: The LED light bars are rated for off-road use only. Be considerate and don’t blind other drivers. Not to mention you would likely get a ticket operating these on public roads. |
What LEDs To Use
Okay, I am short on funds right now and needed good enough parts. I’ve had pretty good luck with Nilight LED bars that you can get really good pricing on from Amazon plus they also have wiring harnesses with relays that you can use.
I wanted to fill the lower bracket from left to right so that meant about a 26″ light bar. To project the light both far and wide, I bought a triple row unit that combines flood and spot lighting.
For the amber LED, the biggest they had was 20″. I didn’t really want massive light from it because it is for snow and rain. In case you didn’t know, amber/yellow lighting is preferred for fog lights because that wavelength of light does a better job penetrating and letting you see objects in those conditions.
We were in the Smoky Mountains near Wears Valley between Pigeon Forge and Townsend a few years back trying to get to a cabin during heavy rain at night. Our old Highlander had so-so white fog lights that were better than nothing but I became a believer after that. Tons of white light just bounces back at you in rain, fog and snow. Go with amber lights.
In terms of the wiring harnesses, I bought two 14 gauge Nilight sets. I planned to remove their switch and plug into the Ram upfitter switches. The upfitter switches are an option and a truck is prewired with a number of access ports to let you plug in things like lights, pumps, etc. If your truck doesn’t have upfitter switches then just run their switches into your cab and mount them on the dash. I’ve used 3-4 Nilight light bars and switches over the years and none have failed on me – they look good too because they light up when turned on.
When it comes to wiring lights, I prefer to use relays when possible. This allows you to use a switch with fairly low amperage that then powers the relay and closes the switch that then feeds current from the battery through a thicker gauge wire. This avoids choking the power running too thin long wire to the switch and back. When your lights are properly powered, they will produce their maximum light is what it boils down to.
Designing the Bracket
Sticking with not wanting to alter the truck, I wanted to bolt the lights to a bracket and then the bracket to the truck. Since the truck was relatively new and not rusted like crazing, I had tons of potential bolts to use – I could have secured the bracket to the bolts of the tow hooks for example. What really caught my eye was the subframe for my Western Pro Plow 2. I’m a big Western plow fan – my dad had one when I was growing up and while I’ve had others – notably a Meyer and a SuperPlow – I still liked Westerns.
To mount the plow, Western creates bolt on sub frames that will connect to a given truck and then there are receivers that the plow connects to. Part of the sub frame is a 2″ x 1/4″ thick cross member that is secured by four bolts – two on each side. That was perfect. The inside bolts were on about 20″ centers. I would connect the bracket to that and go up with a cross member and a top shelf of angled steel. The material would be 1/4″ hot rolled mild steel – why? Because I didn’t want the bracket to bend or stress crack over time from the wind hitting the lights. On one hand, I figured the aerodynamics around the truck would stop some of the air flow but on the other, I’d seen guys in the past run big old school KC Daylighters on cheap light bars and they broke. So, yeah, I overbuilt the heck out of it.
I credit junior high shop class and the instructor, Mr. Tack, with teaching me the benefit of sketching a layout before starting work. Over the years, I’ve learned to sketch, mock up, and test fit before finalizing stuff. With that in mind, I sketched the bracket with pin and paper – young people will certainly think this is from the stone age but it works for me.
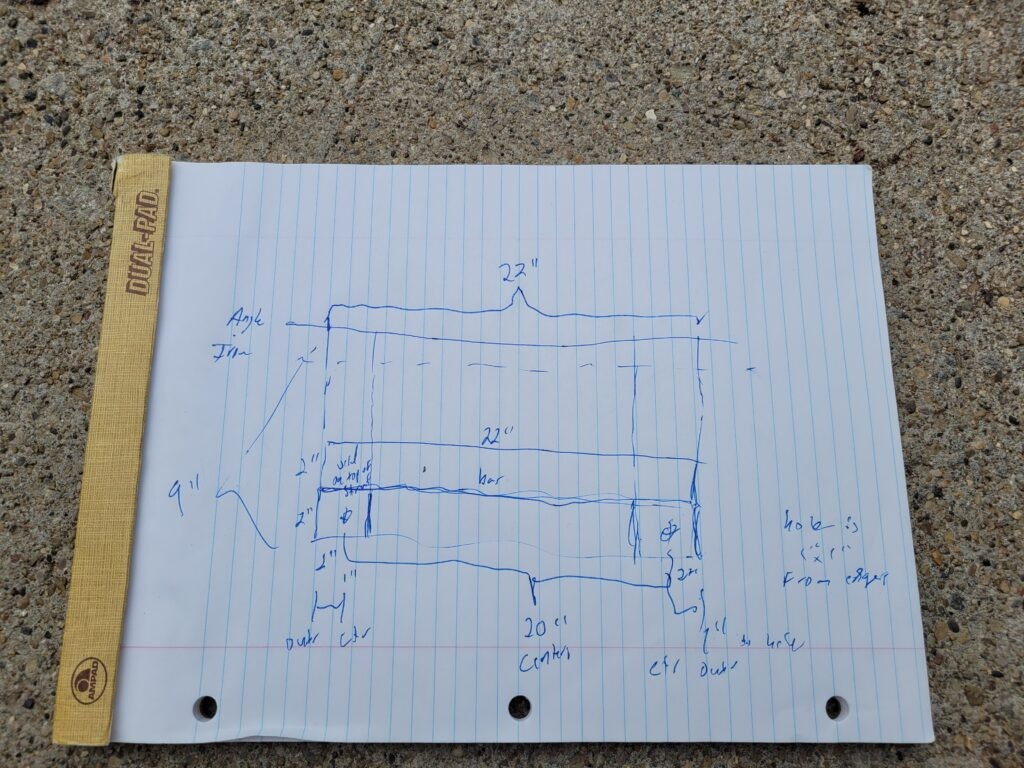
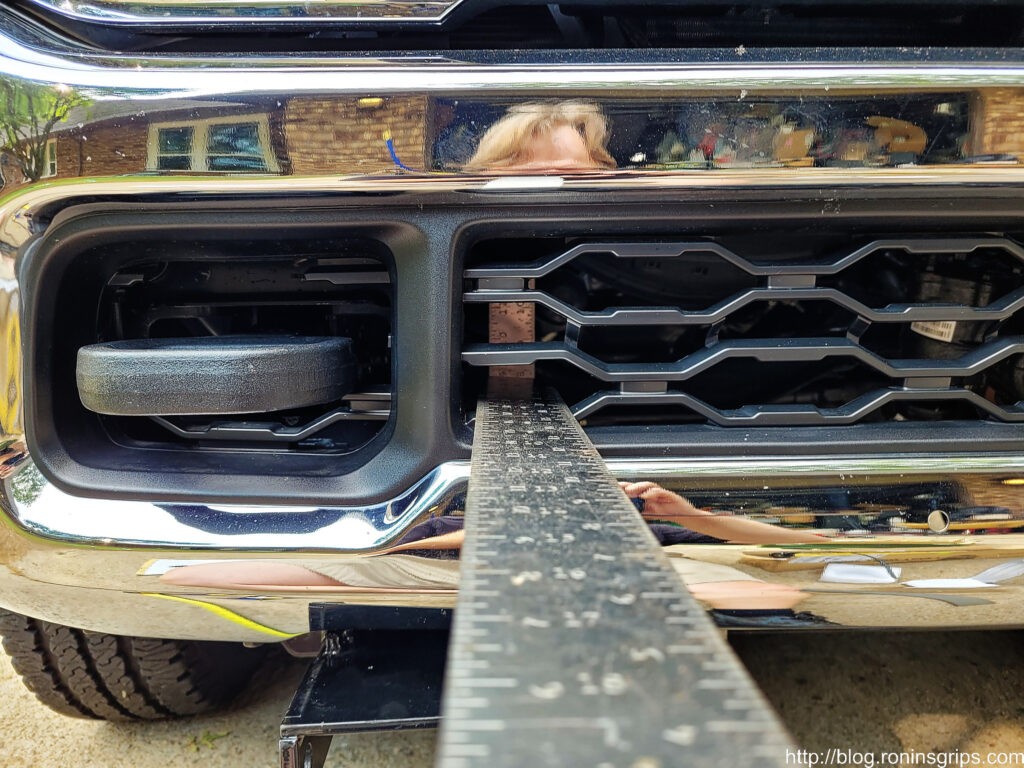
Before You Start!
When it comes to lighting in general, trust but verify. Before you do anything else, take the lights out of the boxes and connect them direct tot he battery to make sure they work.
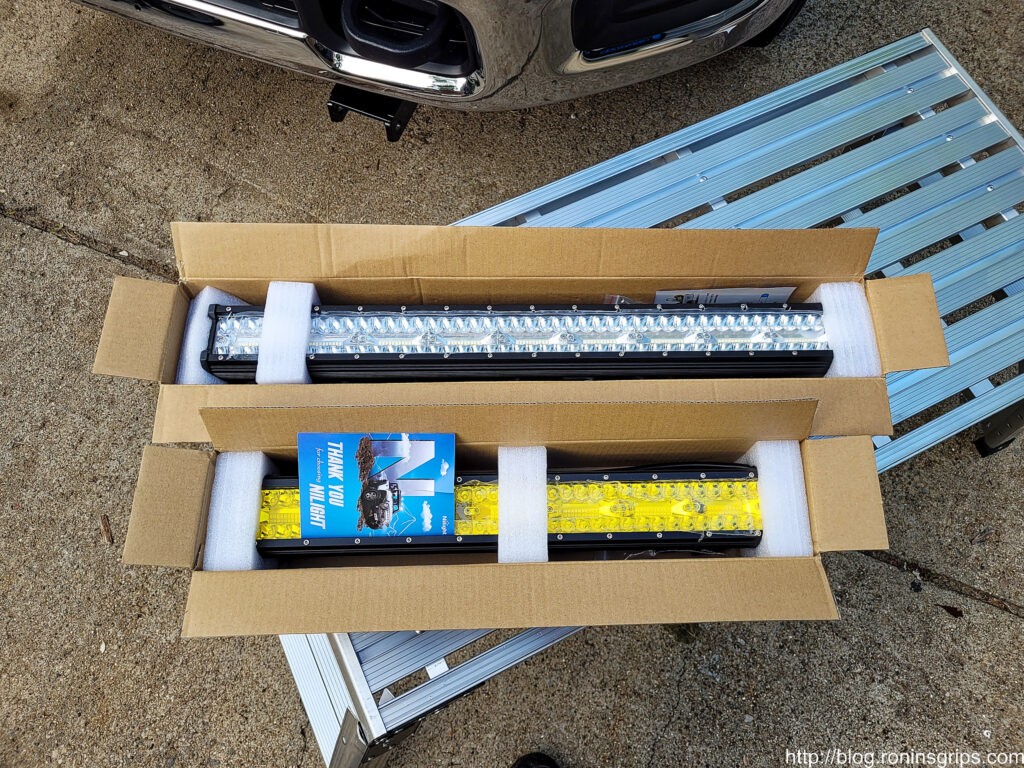
Fabricating the Bracket
With the design roughed out, the next step was to begin cutting out the pieces of steel. Over the years, I’ve learned that I am better off to work on a section at a time vs. cutting everything at once. This way, if I make a mistake or need to adjust the design, it’s easier. I tend to find design mistakes earlier on this way.
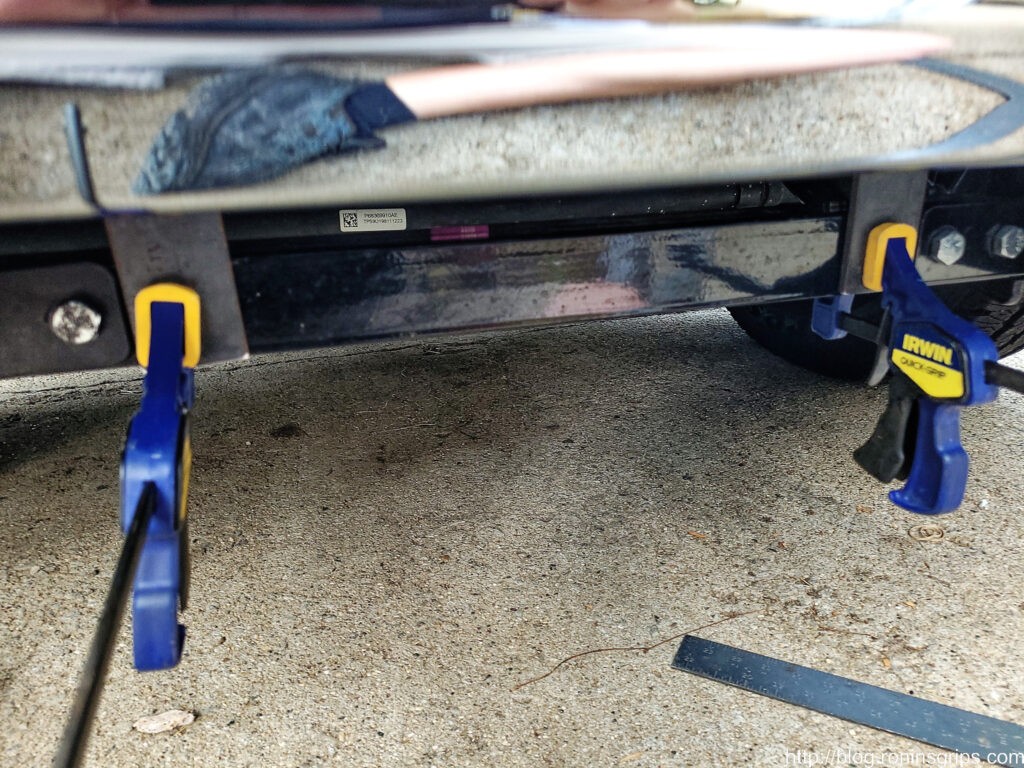
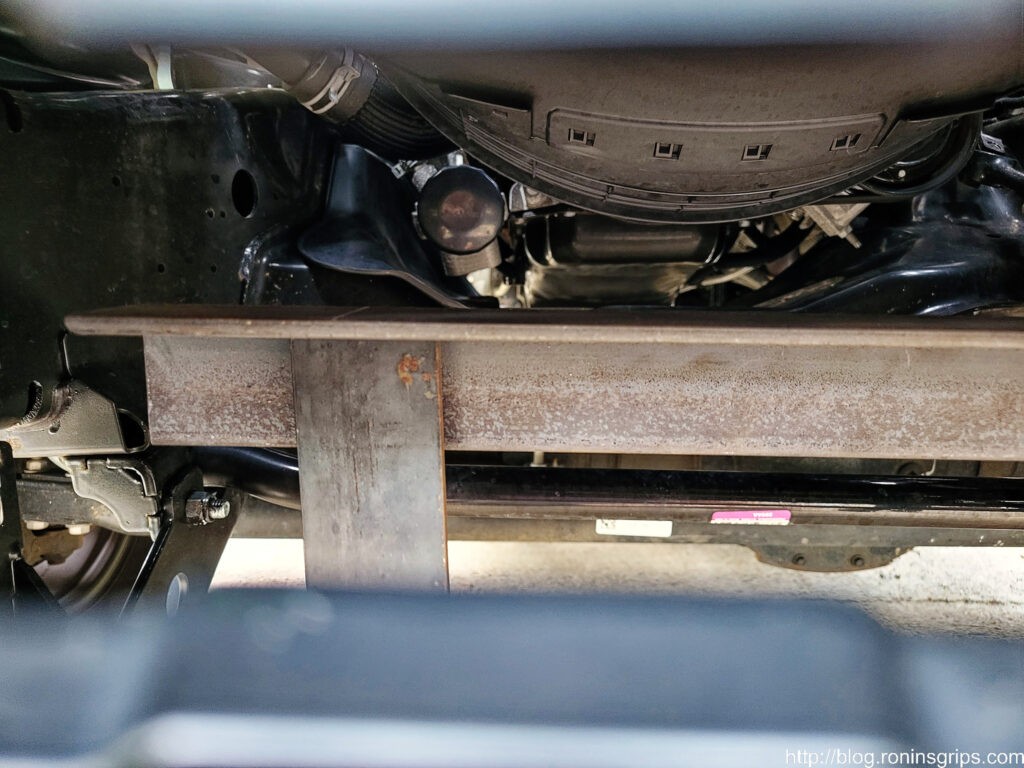
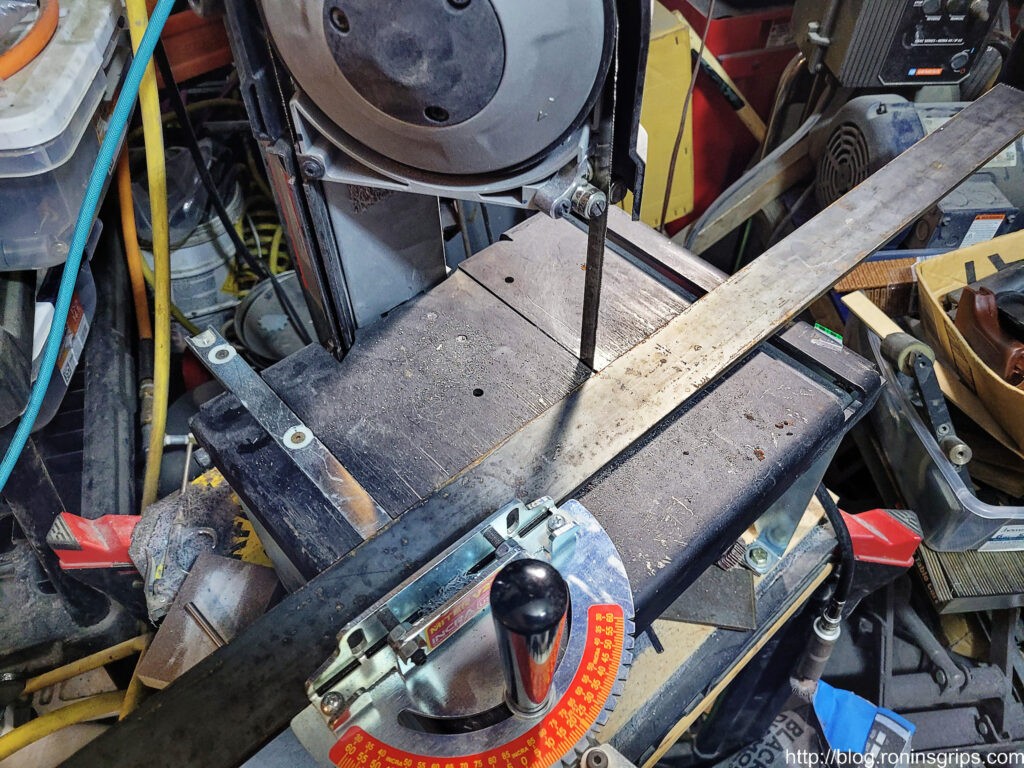
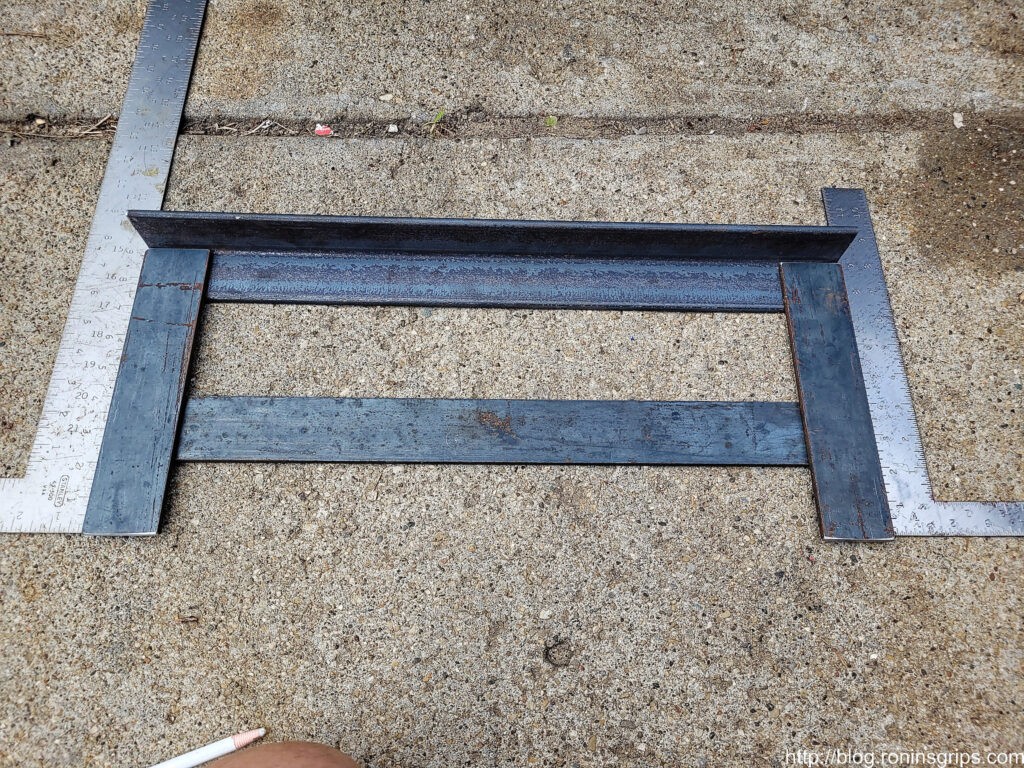
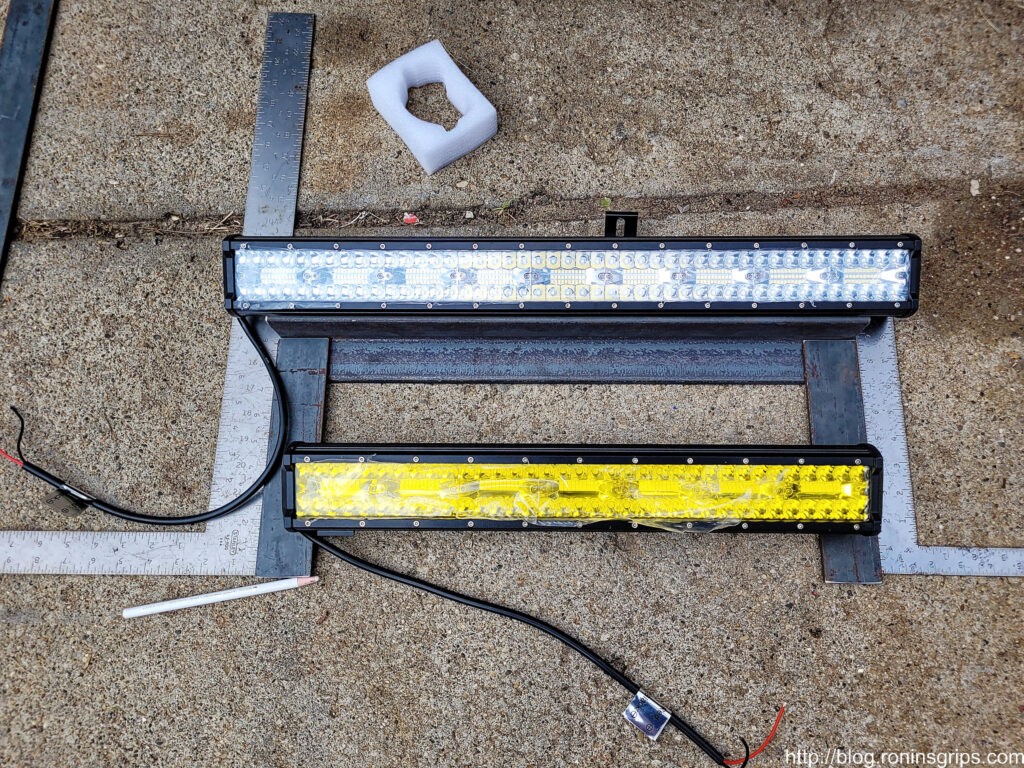
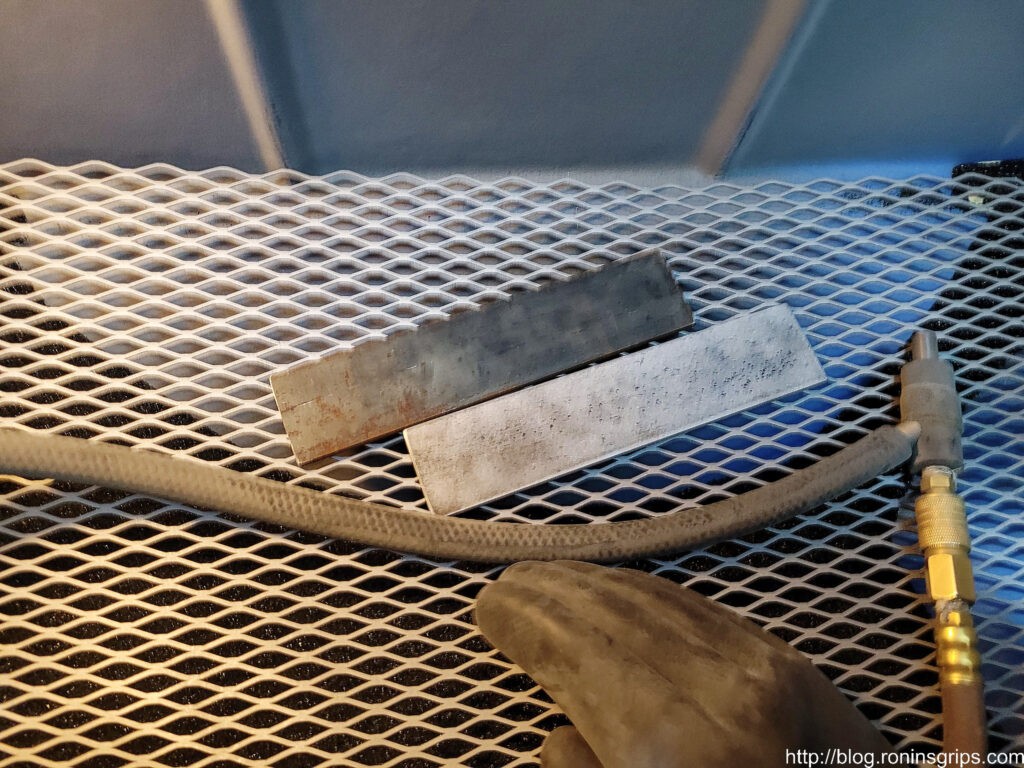
Welding the Bracket
I used my Miller Millermatic 211 MIG running 75/25 shielding gas and .030 wire. I set the thickness to 1/4″ and let the machine figure things out. I bought this machine years ago and it really does a great job for me – most of my work is light fabrication anyways with thicknesses usually at or under 3/8″ thick and relatively short weld times.
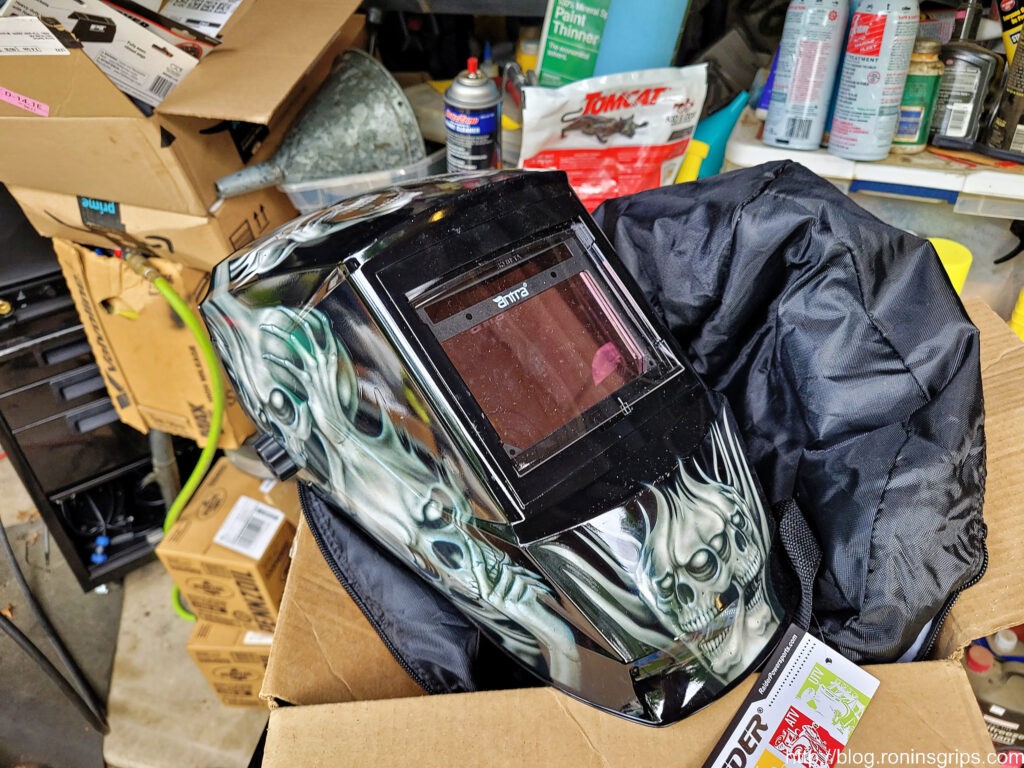
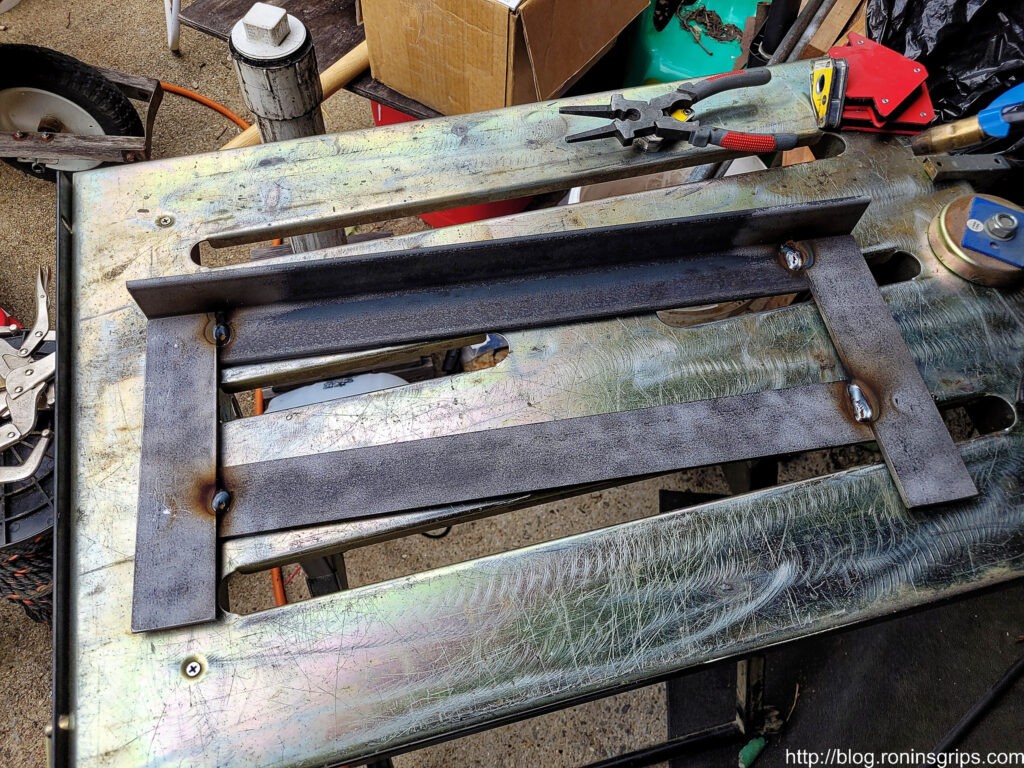
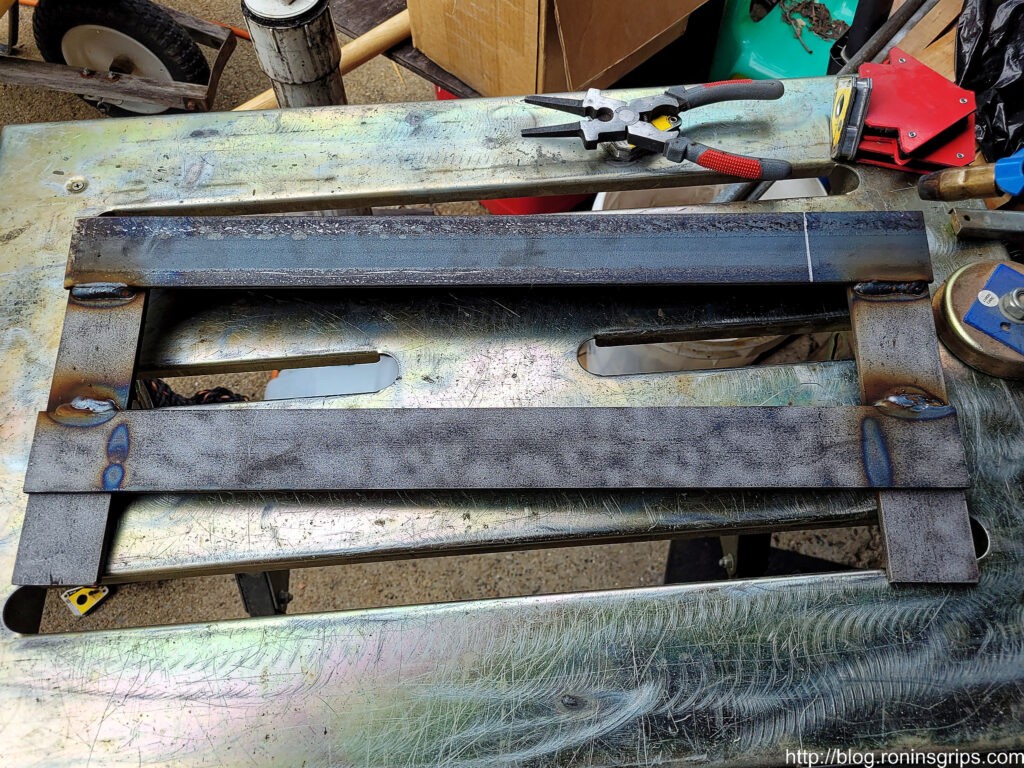
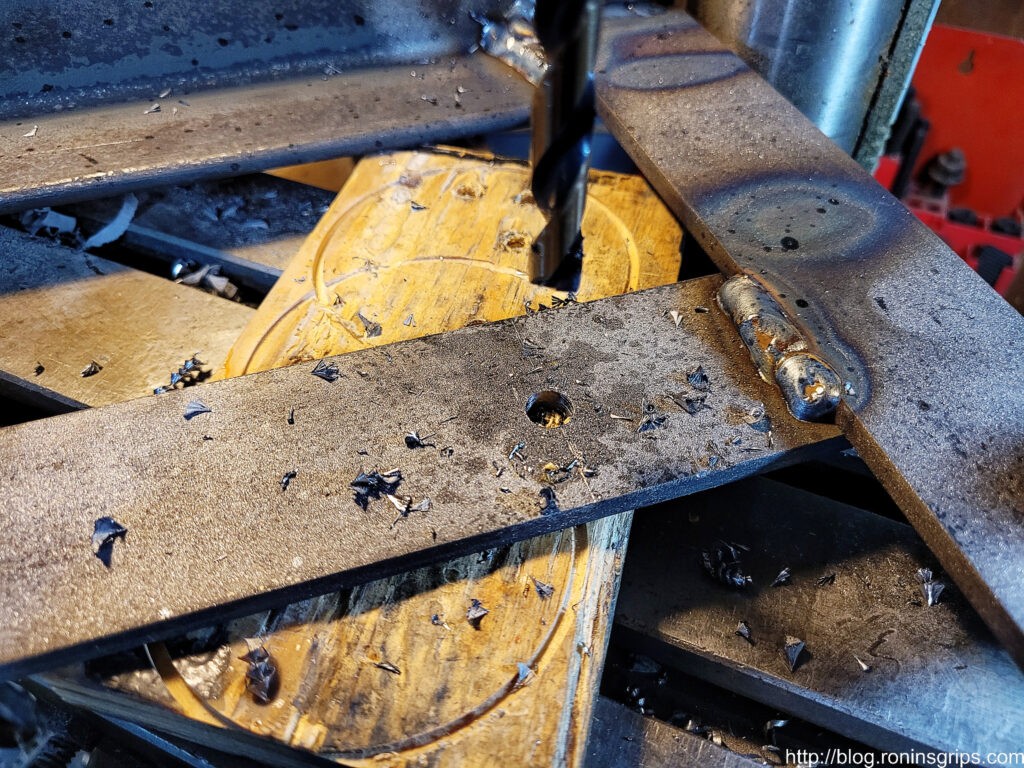
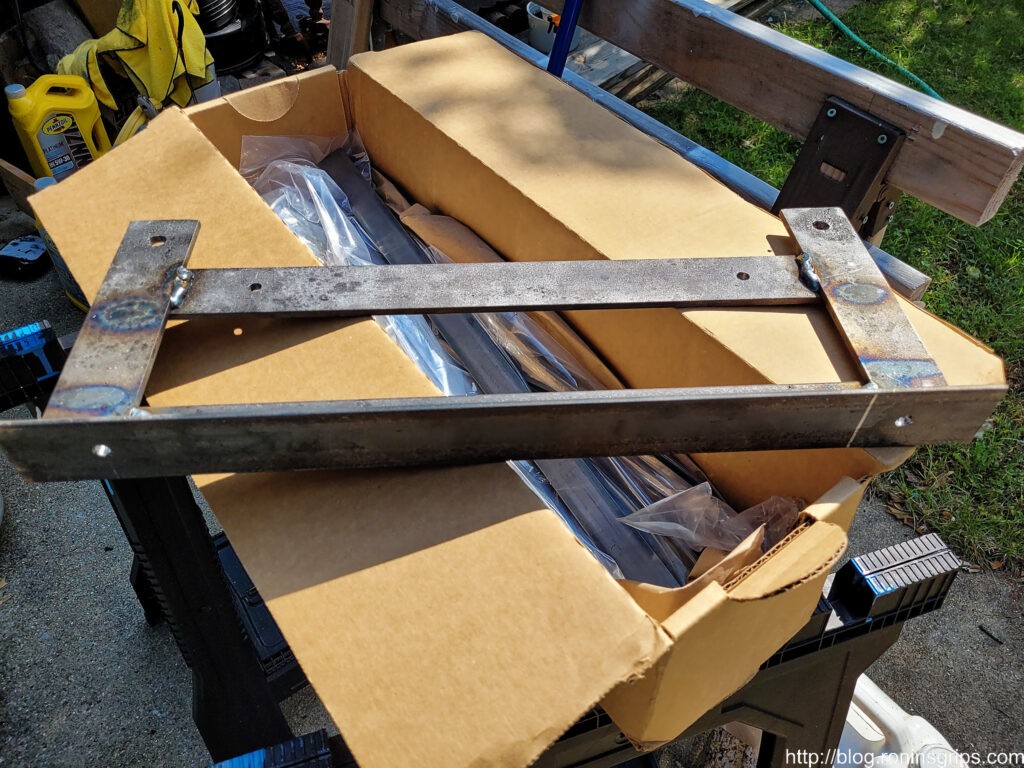
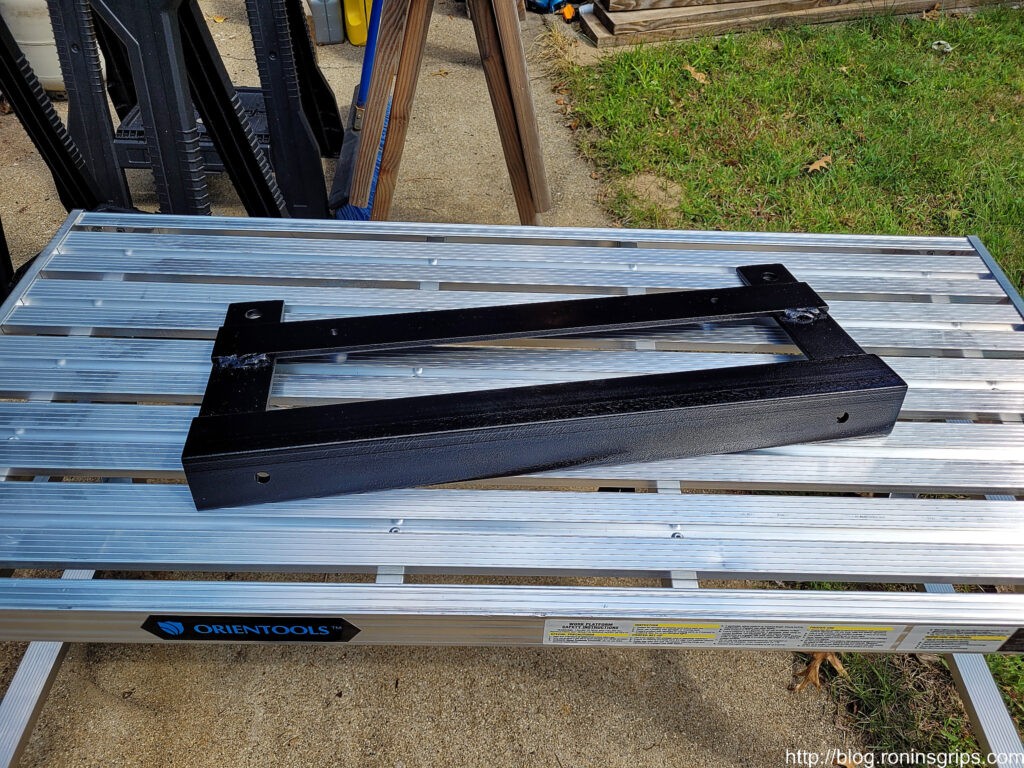
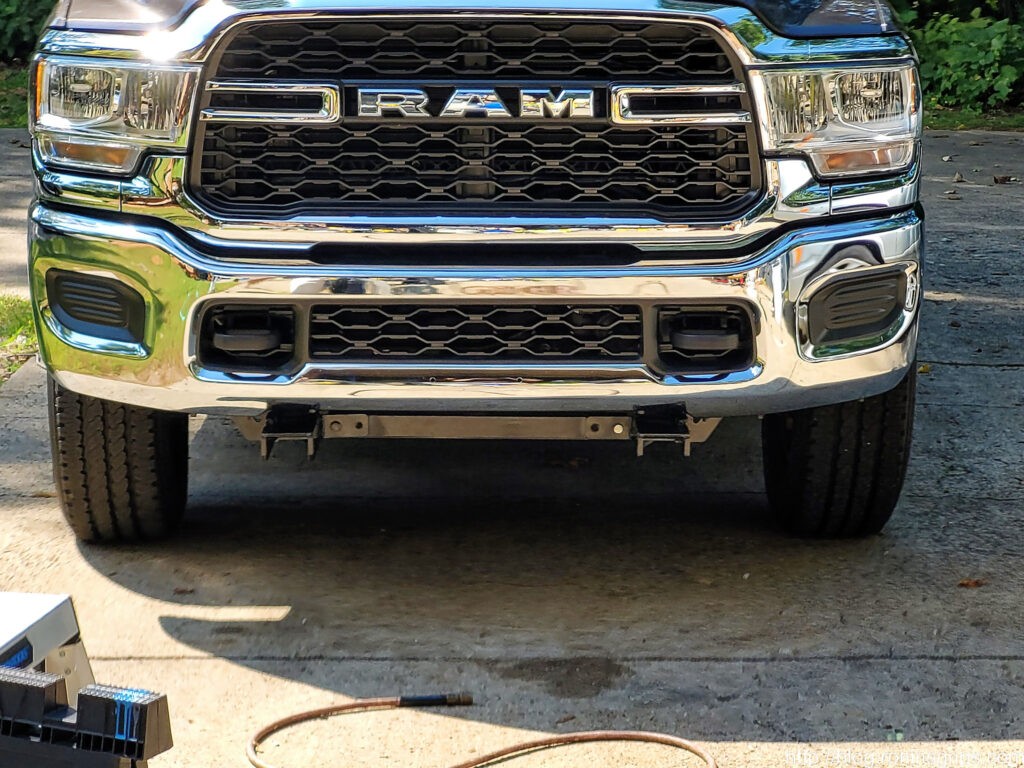
By the way, this was not light by any means. The bracket weighed just under 12.5 pounds prior to the lights.
Mounting the Light Bars
With the bracket completed, next up was to mount the light bars. I wanted to do that and then install the whole assembly into the truck vs. installing the bracket and trying to install everything in an awkward position under the truck.
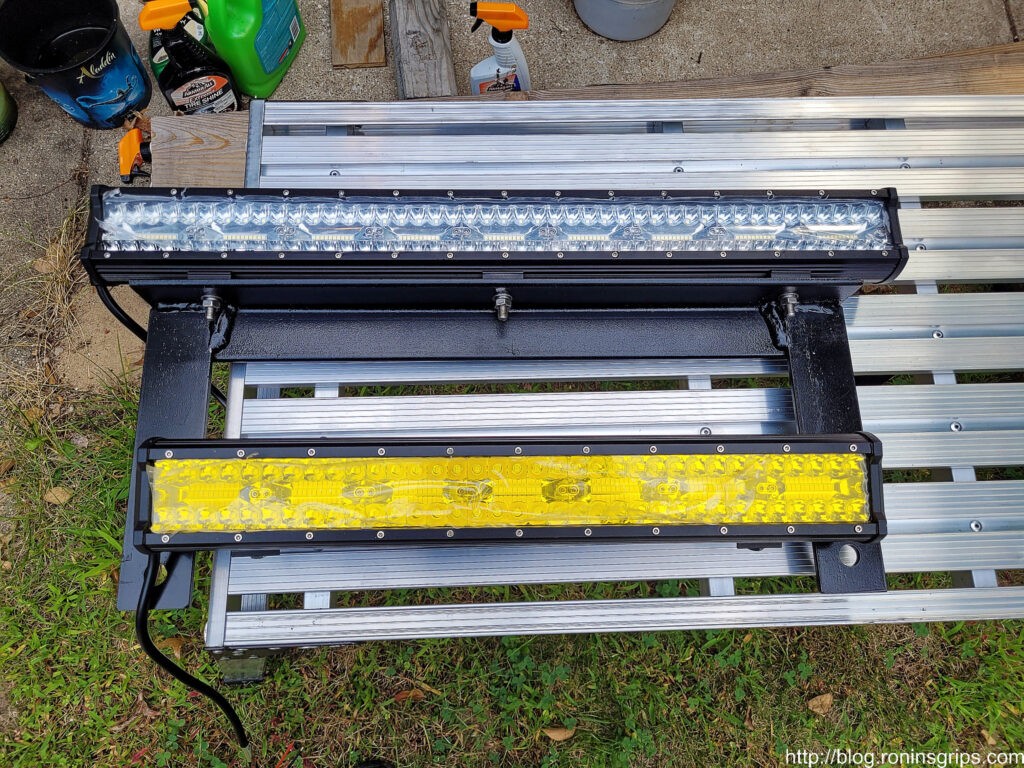
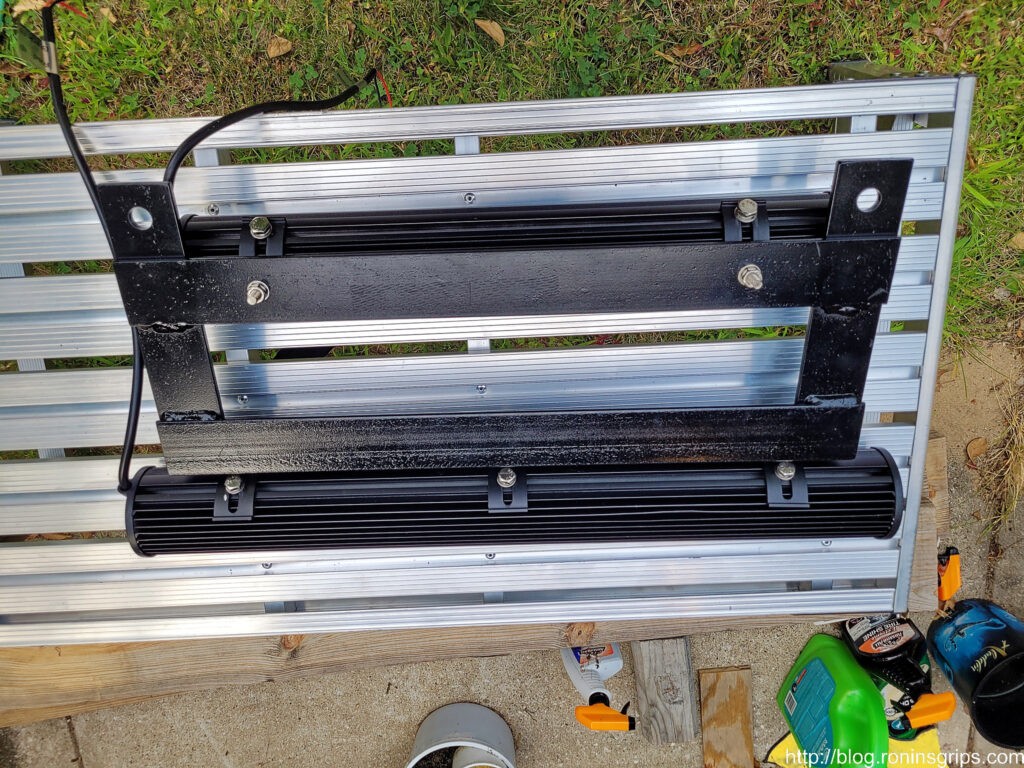
Wiring Up The Lights
As mentioned my plan was to use the upfitter switches and I did. If you do not plan to, then use the Nilight switch. I am going to detail what I did with the upfitter wiring. Why use the upfitter switches? Personally, I think it makes for a very clean look. You have the nice integrated switches in the dash and then RAM also did the wiring out to a number of different terminal locations for you hook up accessories.
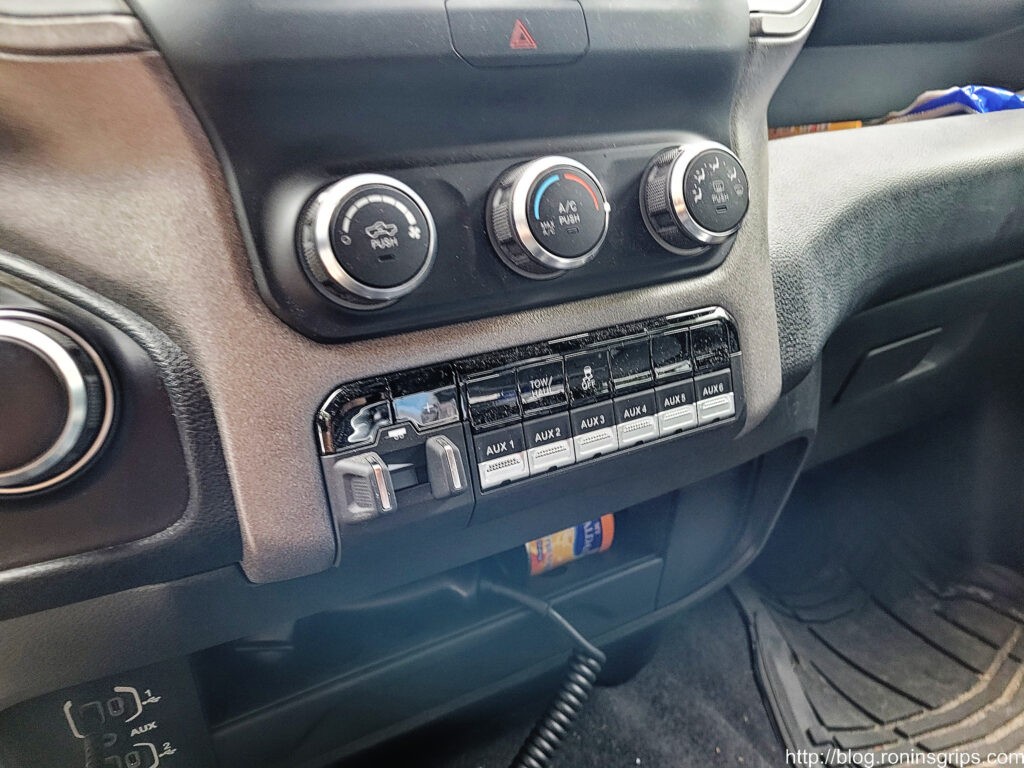
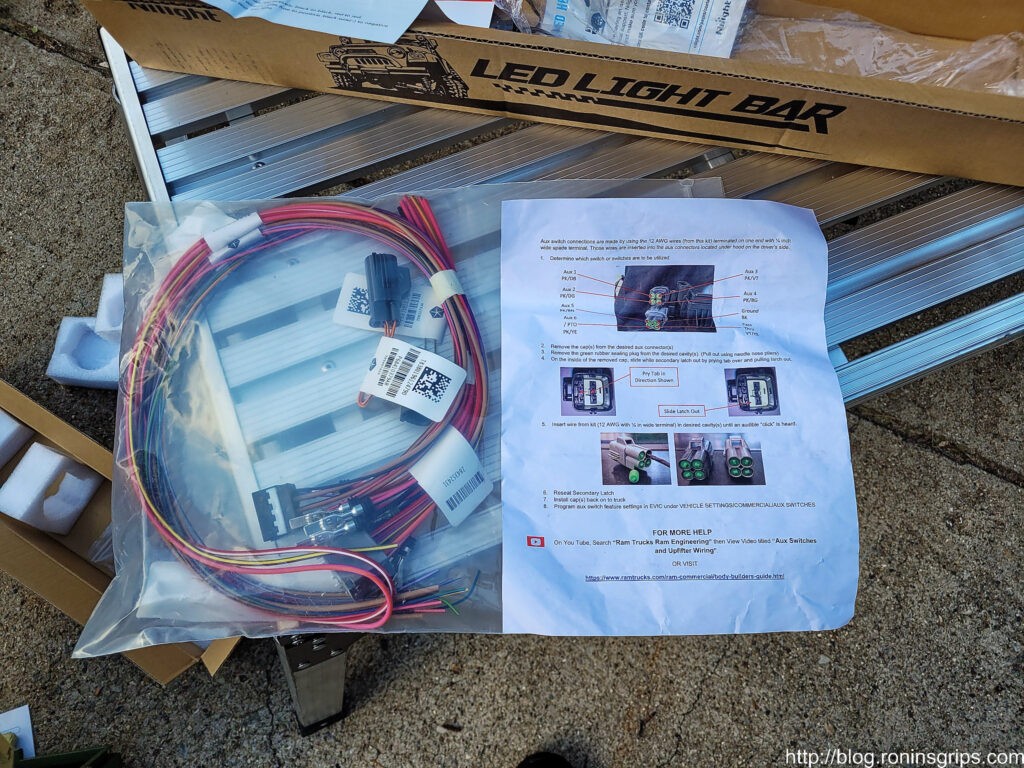
If you need more information about the upfitter wiring – click here for the official RAM page for commercial body builders (their choice of words not mine). The next photo actually shows what you need to do for the simple LED addition we are doing.
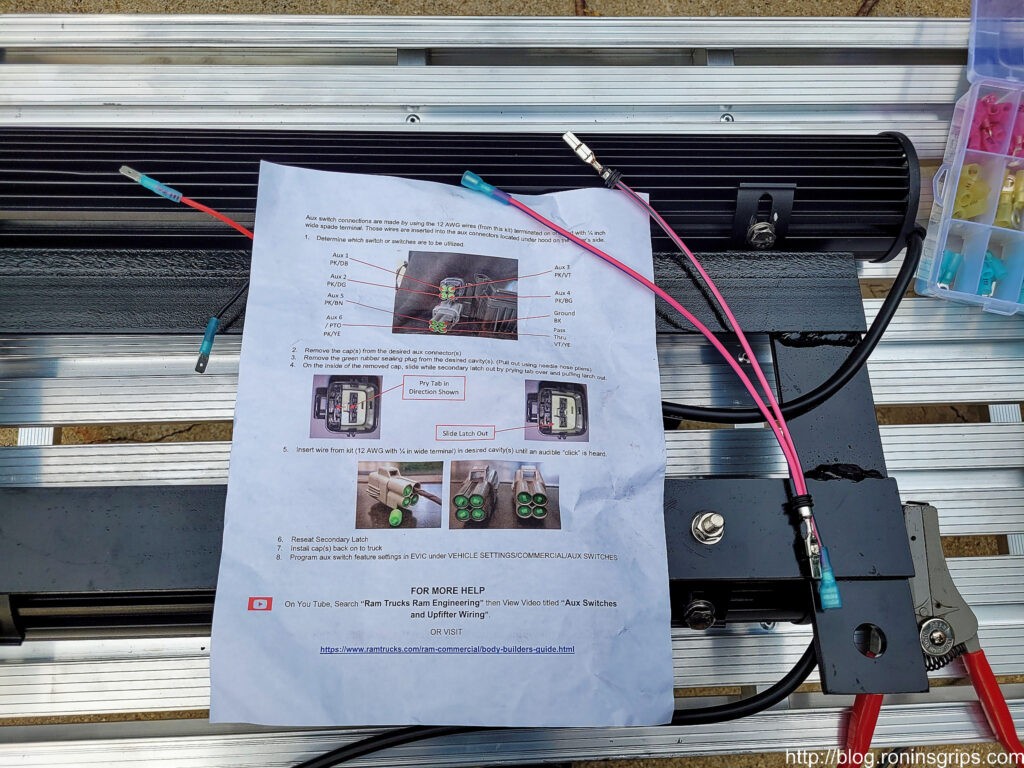
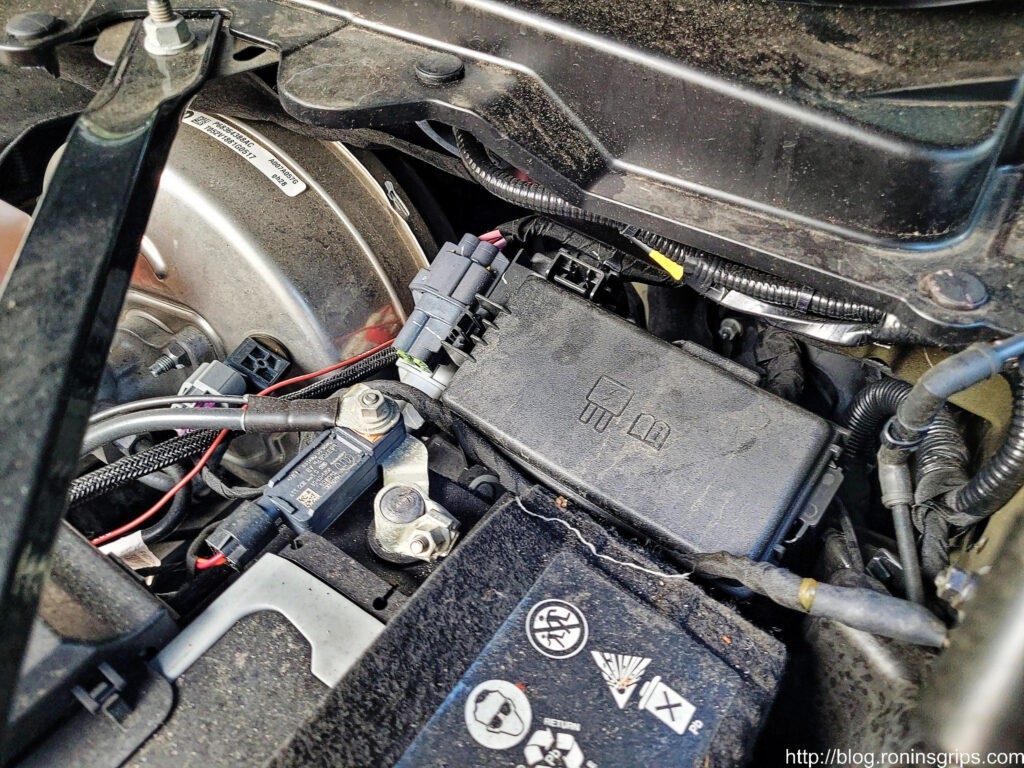
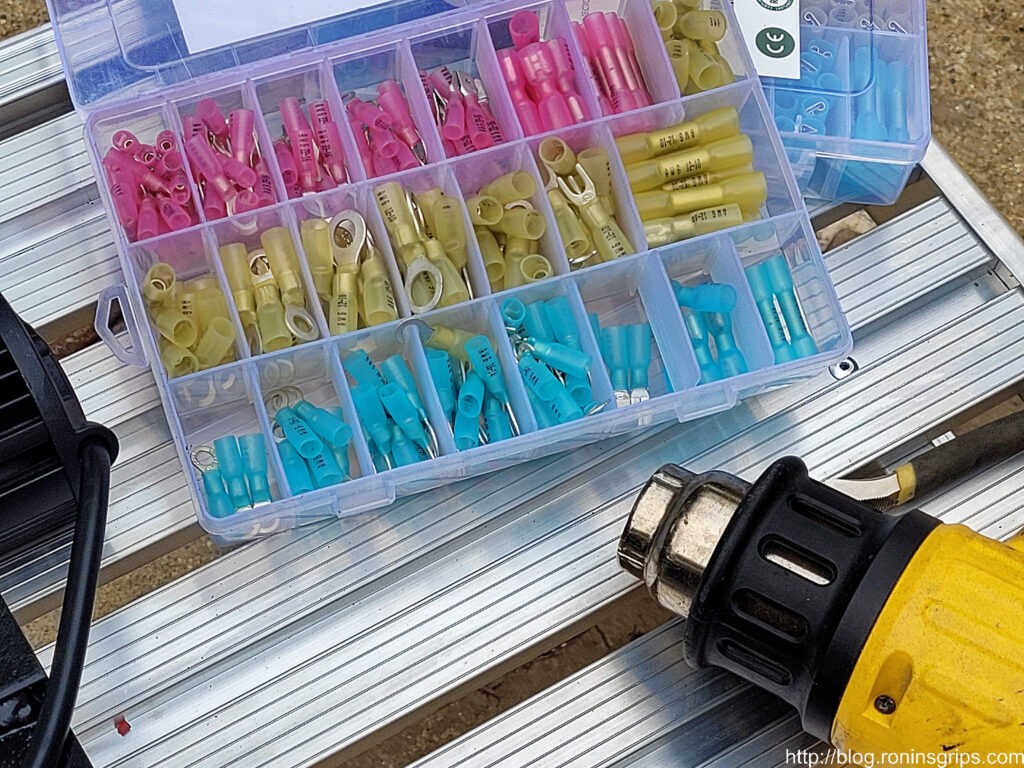
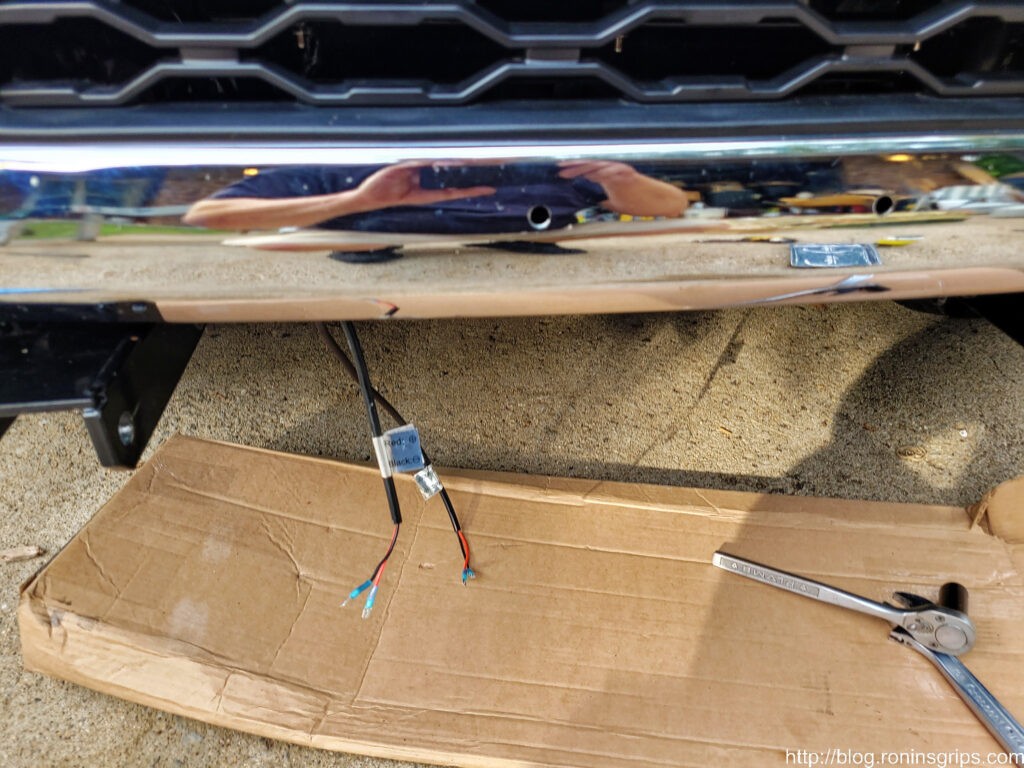
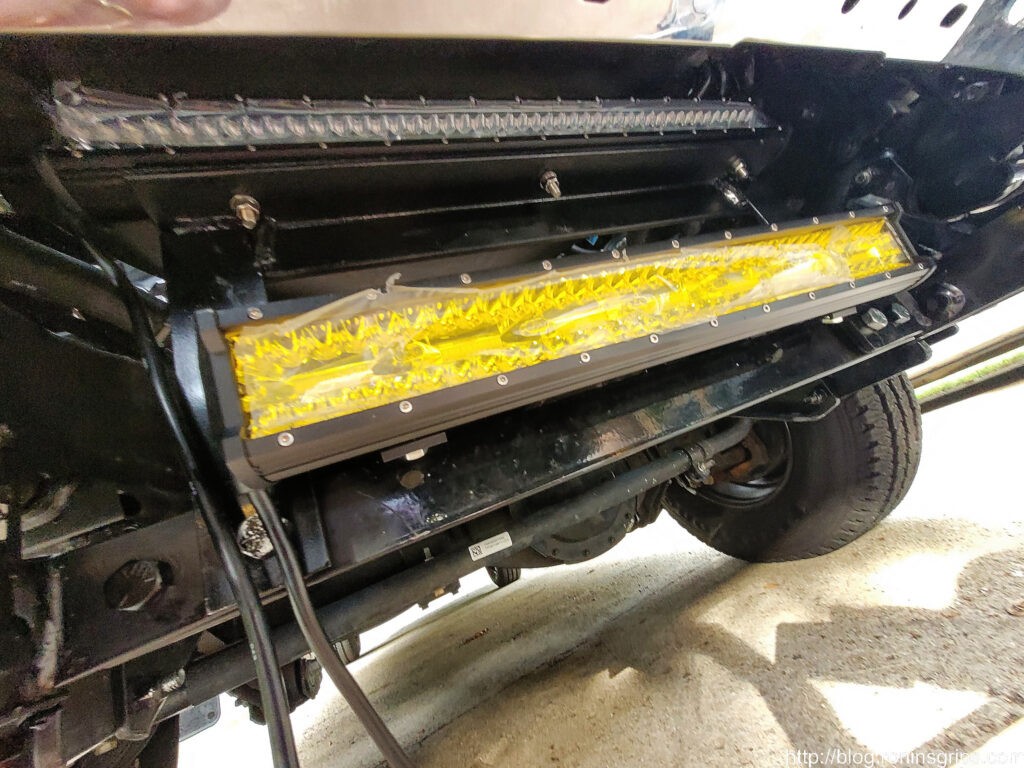
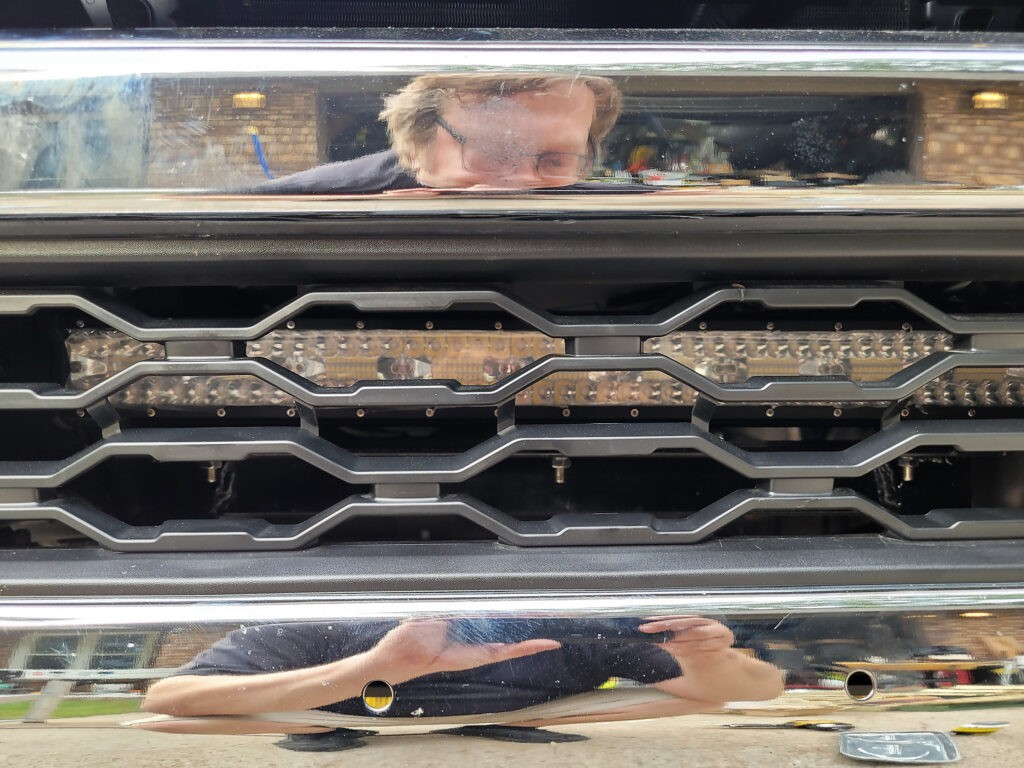
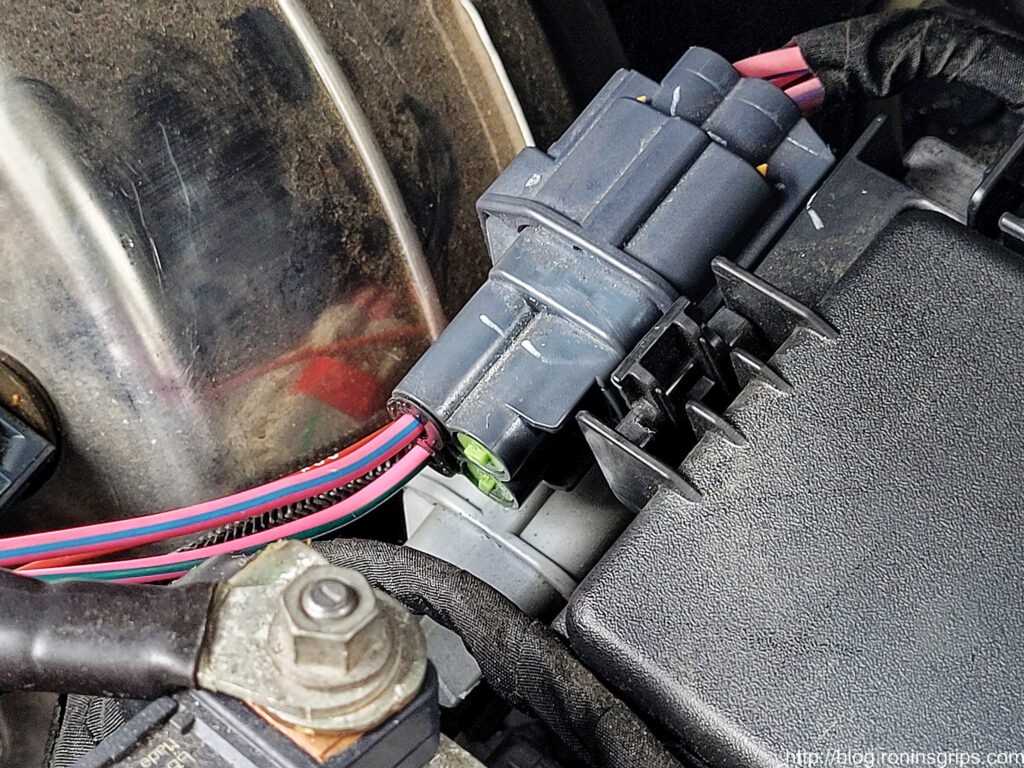
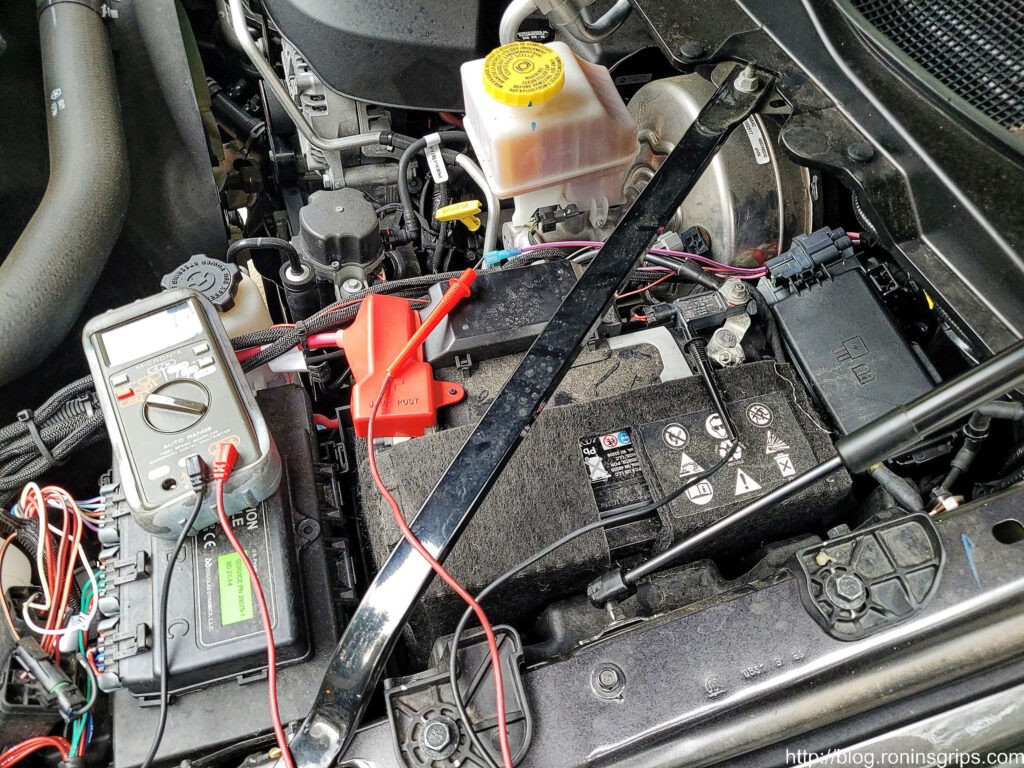
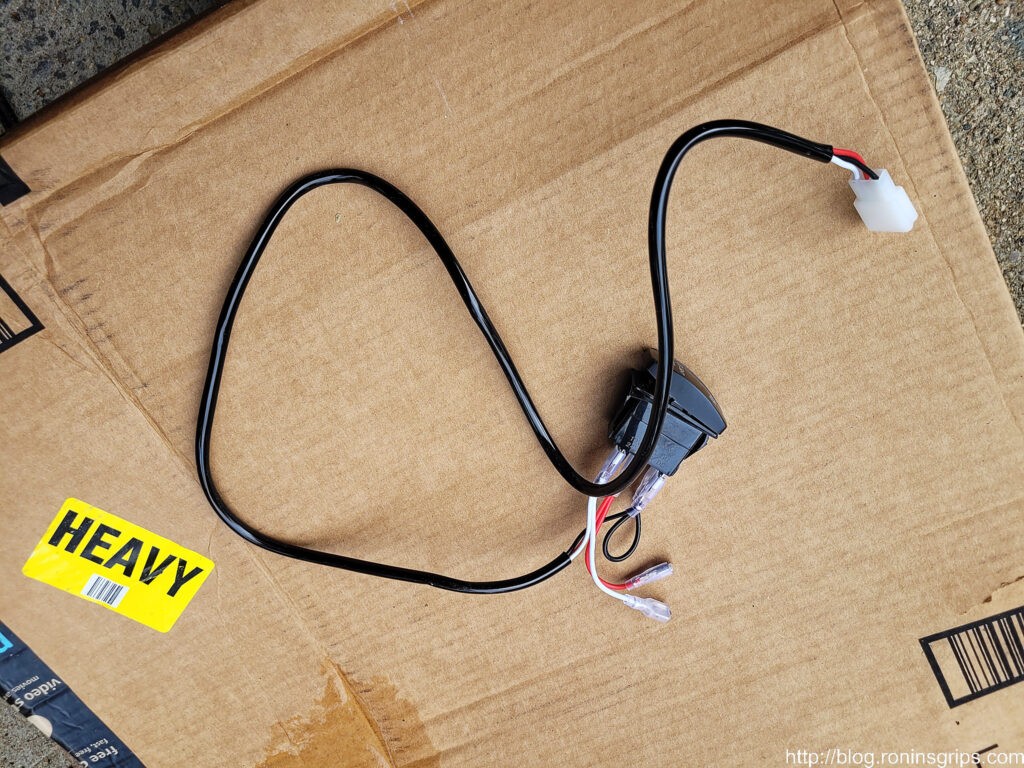
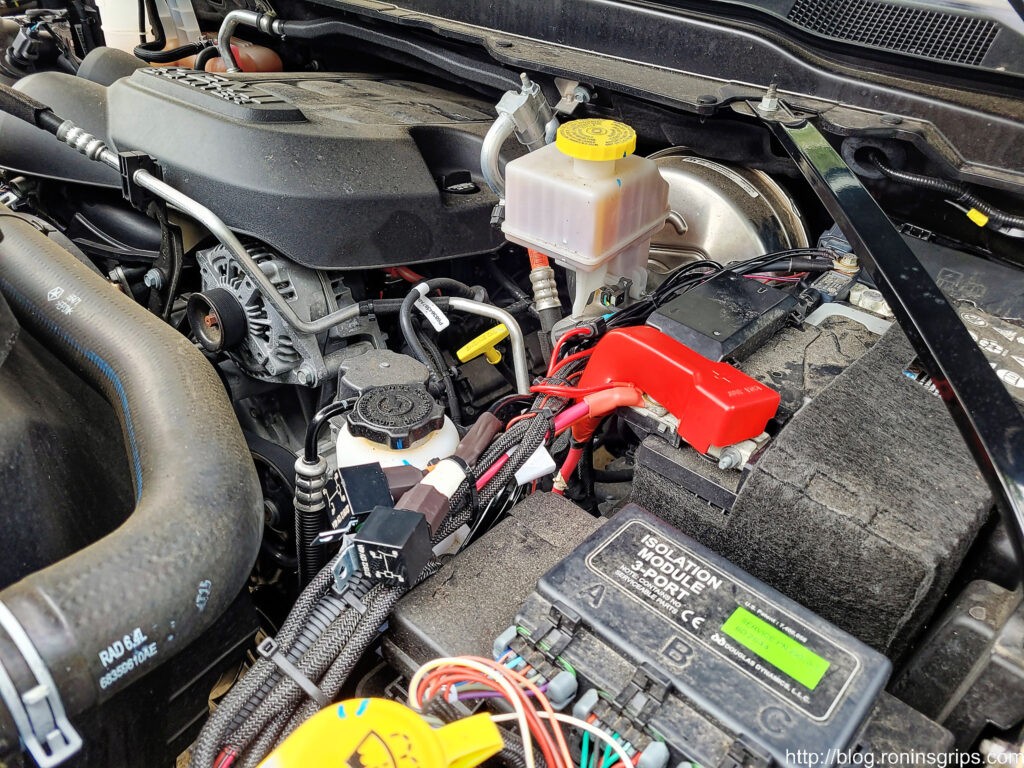
Testing and Results
I turned the switches on and confirmed the lights work then I waited for it to get dark. The following photos are of a tree line about 40 yards from the front of the truck plus are straight out of the camera – no color changing, sharpening, etc.
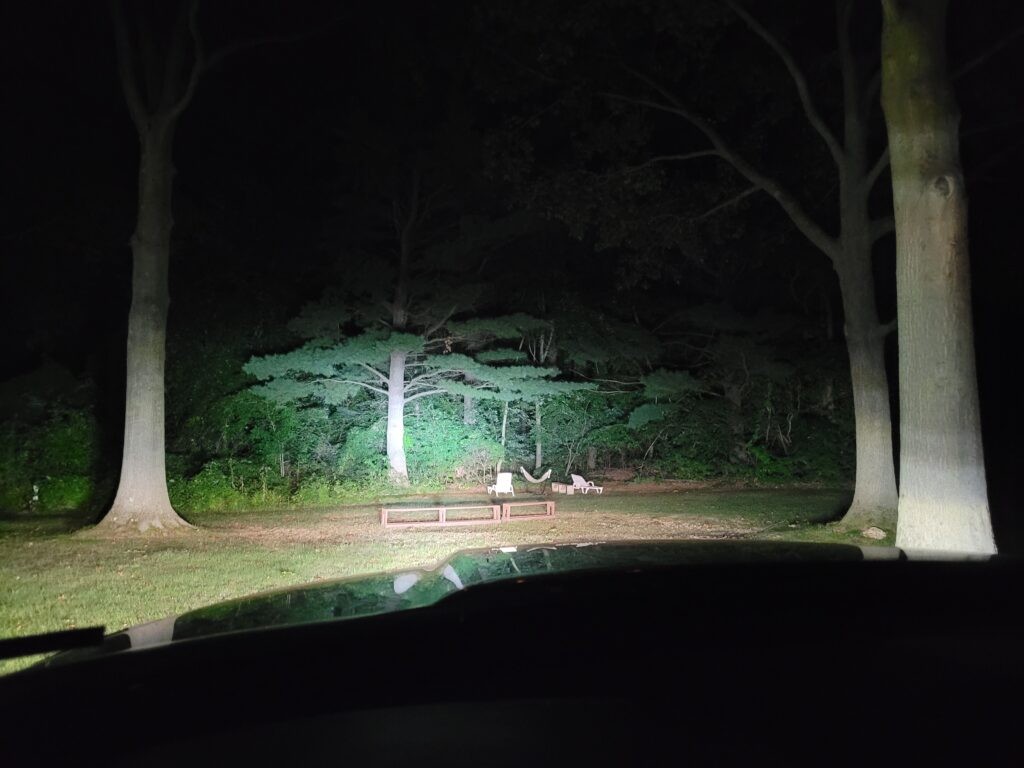
Here’s a video of the testing:
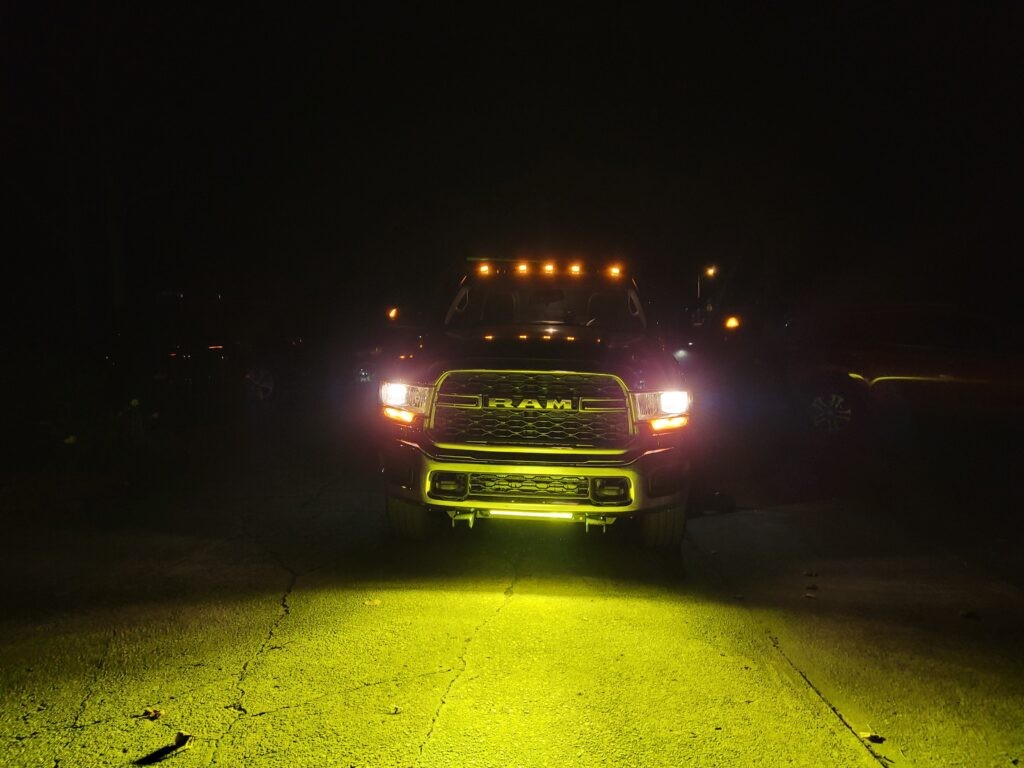
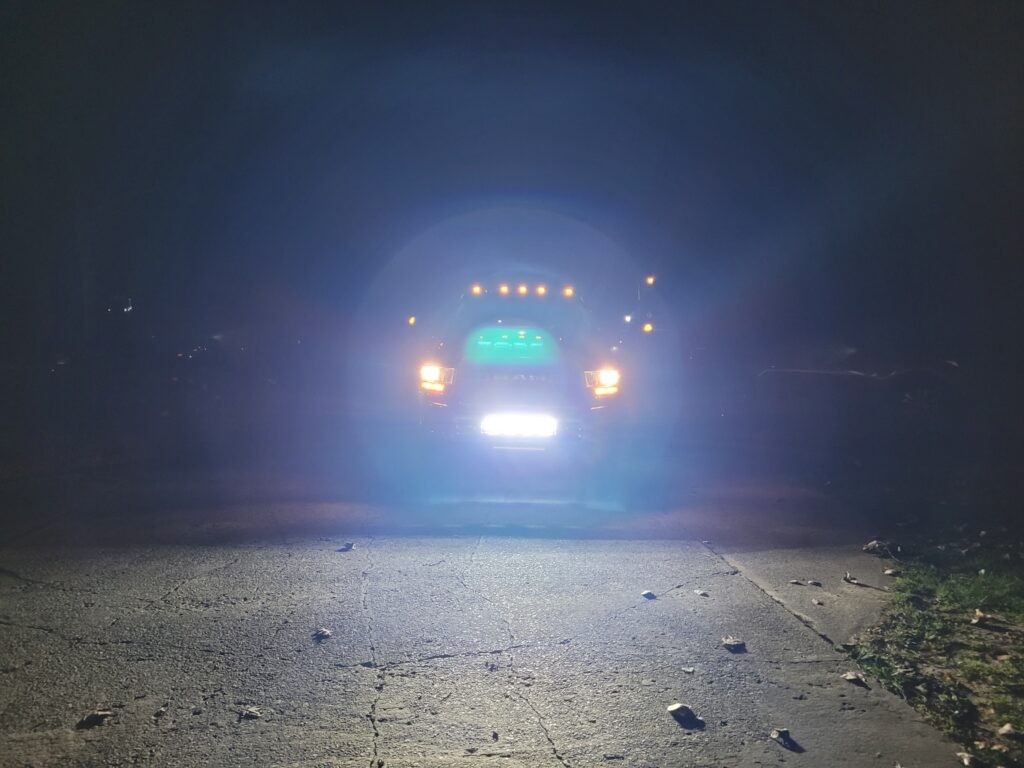
Conclusion
I like how things turned out. I’ve been using the set up for about a month now and am very happy. I’ll post updates down the road. Lighting may look daunting but it is actually quite straight forward. Nilight is a cost effective way to get started.
I hope this helps you out!
4/7/24 Update: Everything has held up just fine – no problems of any kind since I installed them.
Note, I have to buy all of my parts – nothing here was paid for by sponsors, etc. I do make a small amount if you click on an ad and buy something but that is it. You’re getting my real opinion on stuff.
If you find this post useful, please share the link on Facebook, with your friends, etc. Your support is much appreciated and if you have any feedback, please email me at in**@*********ps.com. Please note that for links to other websites, I may be paid via an affiliate program such as Avantlink, Impact, Amazon and eBay.