The next step after installing the trigger guard assembly was to rivet the front and rear trunnion in place. The modern Kalashnikov design uses a stamped sheet metal receiver with steel inserts at the ends known as “trunnions”. The sheet metal receiver is really holding the components in alignment vs. providing the strength necessary for the chambering and the rear butt stock.
Historically these were forged and many makers like to point out that these parts still are. For example, the Polish maker WBP likes to point out they use forged trunnions. Some makers are using cast trunnions and the quality can differ. When done right, cast parts can be plenty strong … emphasis on when done right.
The following photo is of the WBP front trunnion.
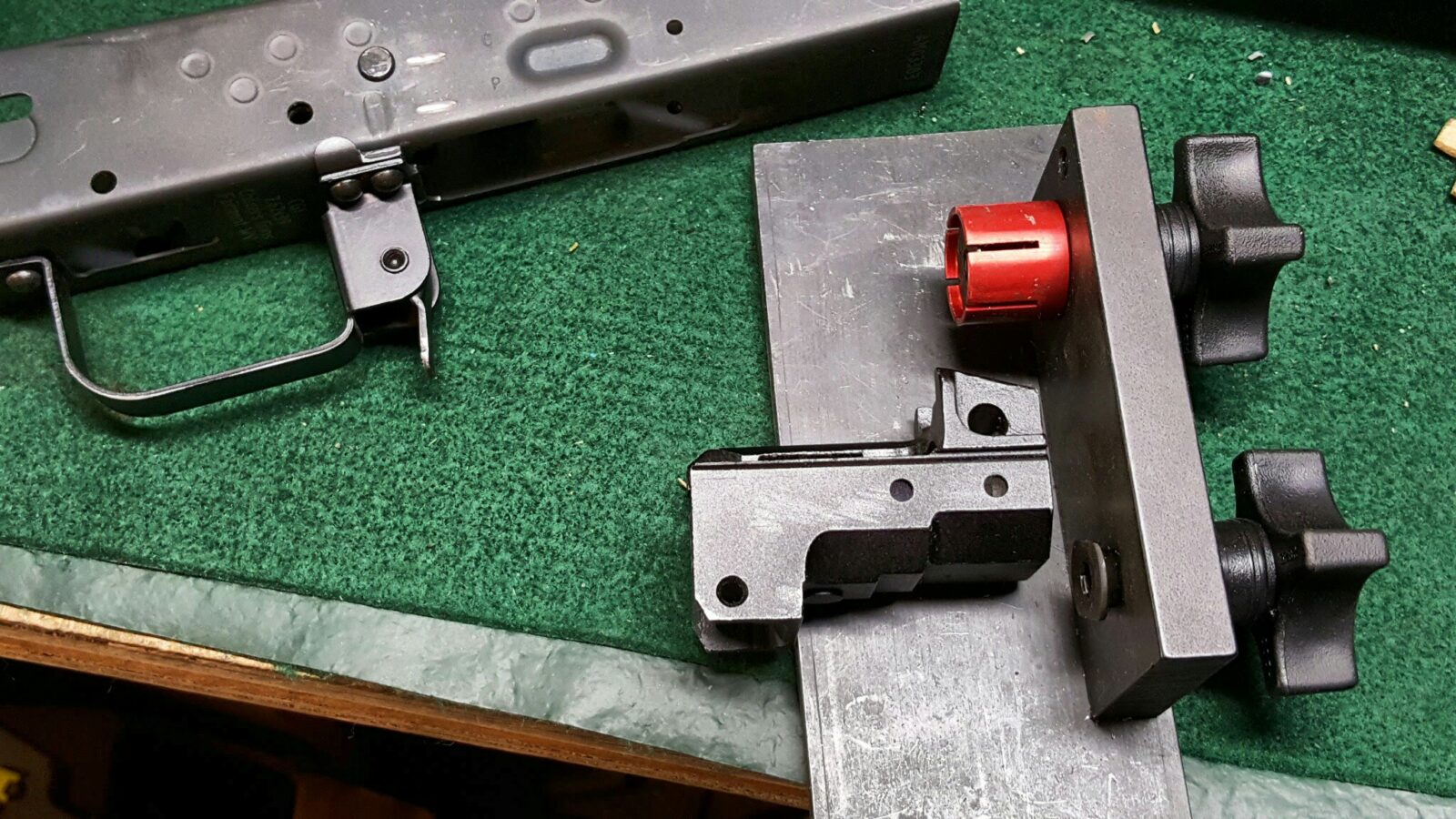
The following photo is of the unique rear trunnion that is designed for the optic rail to lock on to the post you see:
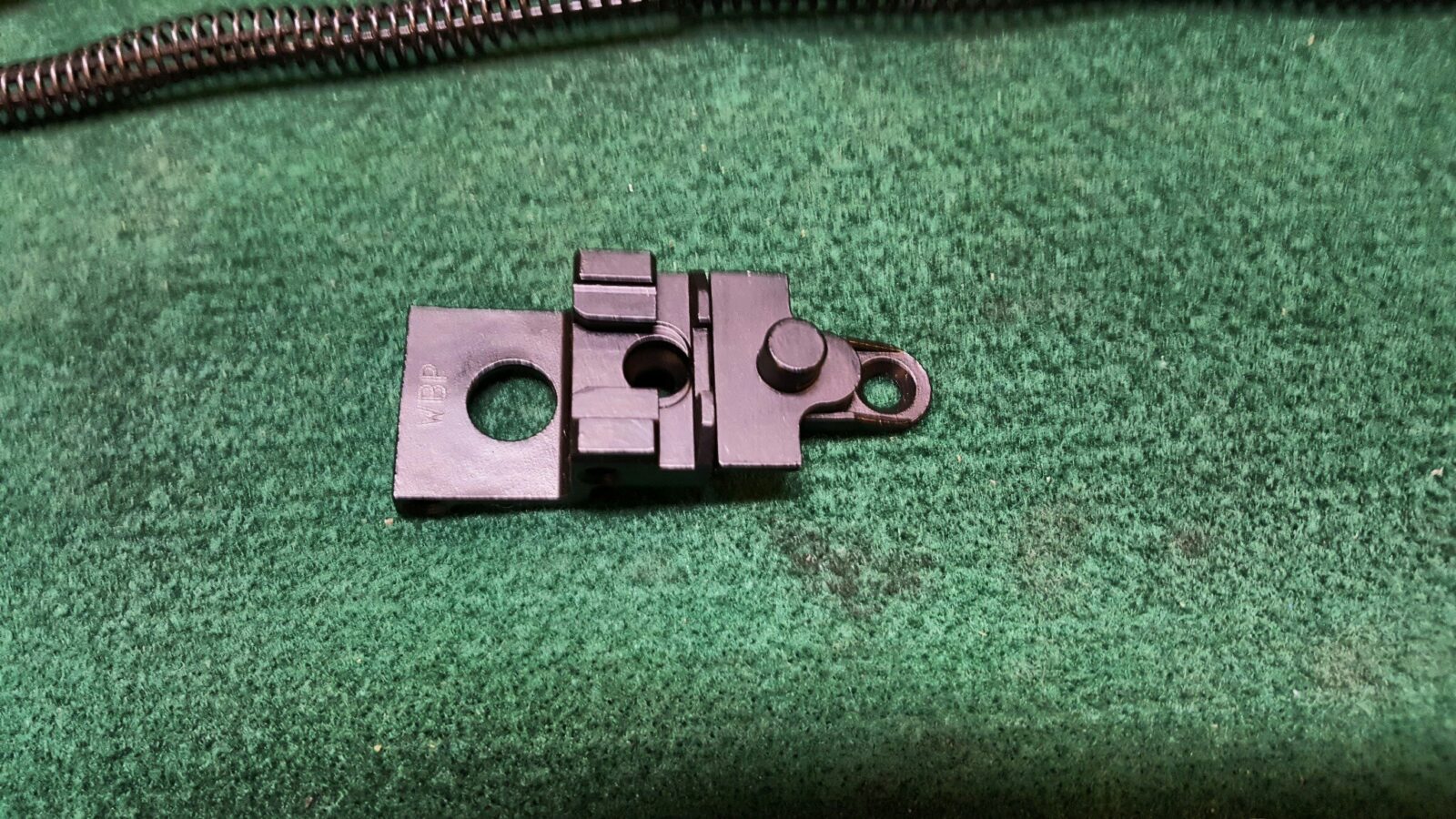
Rivets and Countersinks
The trunnions are held in place by steel rivets. The front rivets are about 5/32″ and the rear is about 3/16″. You’ll want to measure your holes or confirm with your maker what to use. I use AK-builder rivets mostly now and am happy with them. Note that there are many, many different types of rivets in terms of materials used, width, and length. AK-builder makes it easy – if you are going to build an AKM kit then get one or two packets of AKM rivets – he has removed the guess work by putting one of each in the bag. A tip I’d give you is to always have one or two spare bags just in case you lose a rivet or need to redo one.
Before I go further, rivets are the most proven method of assembly for high-strength reliable applications involving automatic fire and military use. For low volume semi-auto use you can also do weld builds. Screw builds are an option but they do risk coming loose and AK guys will honestly give you a hard time when they see the screw heads – I know this first hand 🙂 My recommendation is to go the proven way and use rivets.
On the WBP kit, the front trunnion that holds the barrel is a fairly generic AKM-type forged trunnion. This means it slides into the front of the receiver and the top of the receiver walls form a lip that slide into the recessed grooves in the trunnion. There are two front rivets on each side and a third lower rivet on each rear side that is countersunk.
Now countersunk rivets are actually pretty cool but not everyone understands why. When you look at the trunnion, the rear two rivets also have countersinks. When you install the rear rivets, you actually press receiver material into the countersink before you drill your final holes and install the countersunk rivets. This serves to lock the trunnion into place and would reduce the odds of the trunnion shooting loose over time under heavy military use.
The following photo shows a regular front trunnion rivet with a flat area under the domed part (the bottom rivvet) and a countersunk front trunnion rivet that is tapered under the dome at the top of the photo:
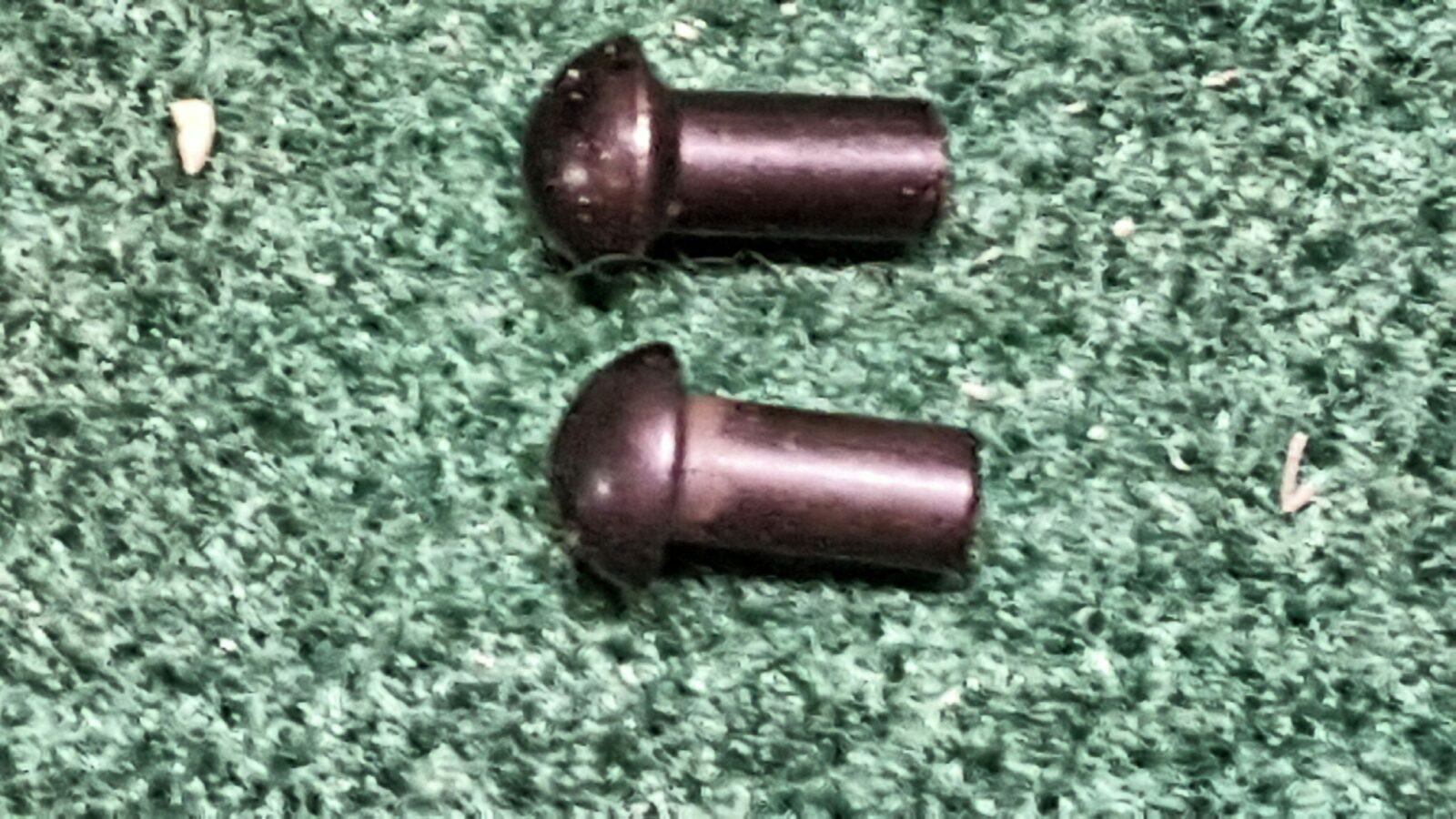
Headspace the Kit Before Proceeeding
Back in the old days we had to remove the parts off the demilled kits and that was a chore. Now with these businesses creating ready-to-build kits, you may just have to press off the front trunnion. I’m really constrained my time so I buy the receiver pre-made by Childer’s and the kits with completed headspaced barrel assemblies.
As the old saying goes, “trust but verify”. In theory a kit that claims to be headspaced better be. Before I did anything else, I got out my Manson Reamer GO and NO-GO gauges, put the barrel assembly in my wood vise and tested the headspace. It passed with flying colors closing on GO, meaning it was not too-tight and not closing on NO-GO, which would have indicated the chamer was cut too long.
In the next photo, you can see the bolt assembly and the two gauges.
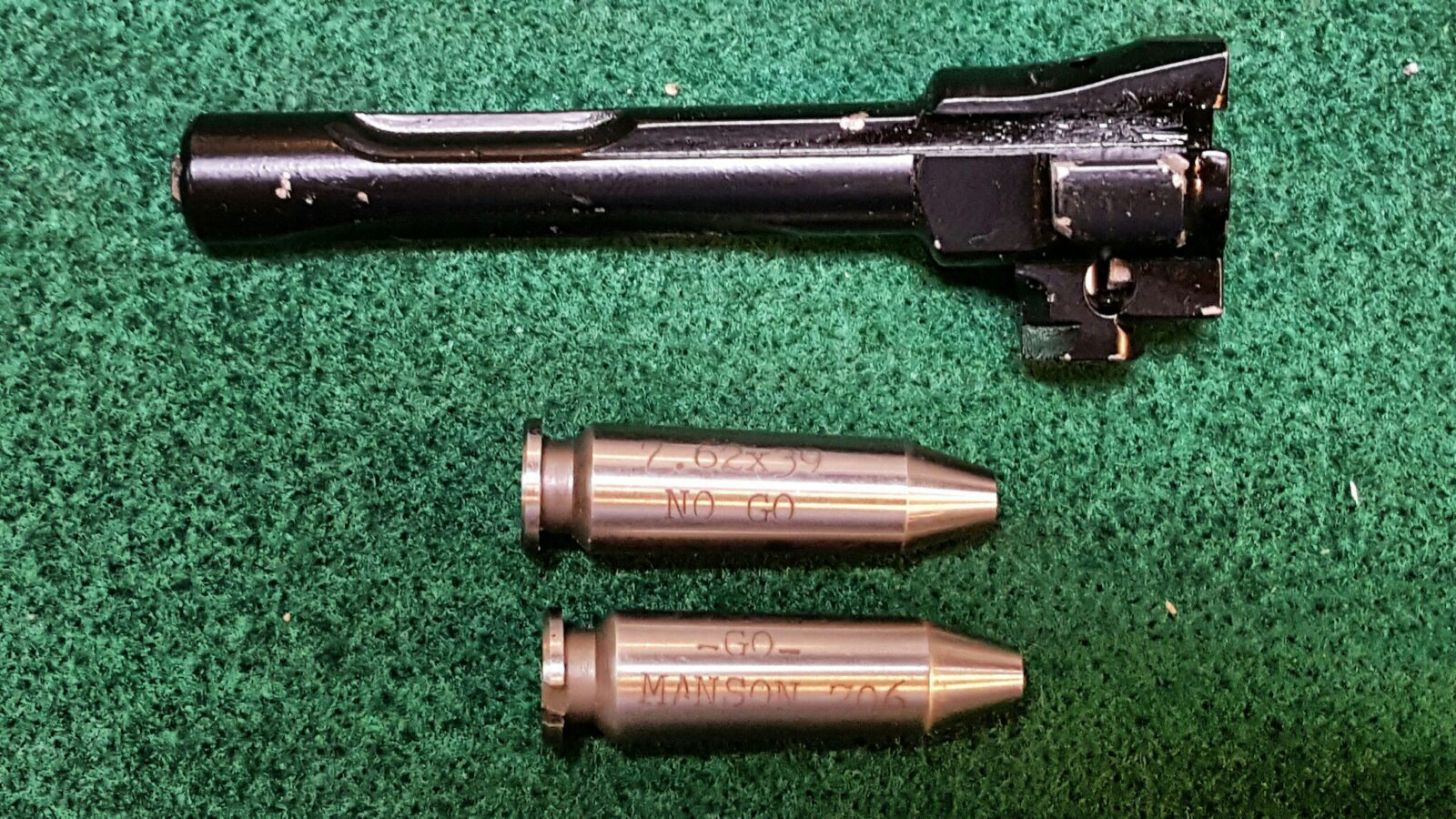
It closed on GO:
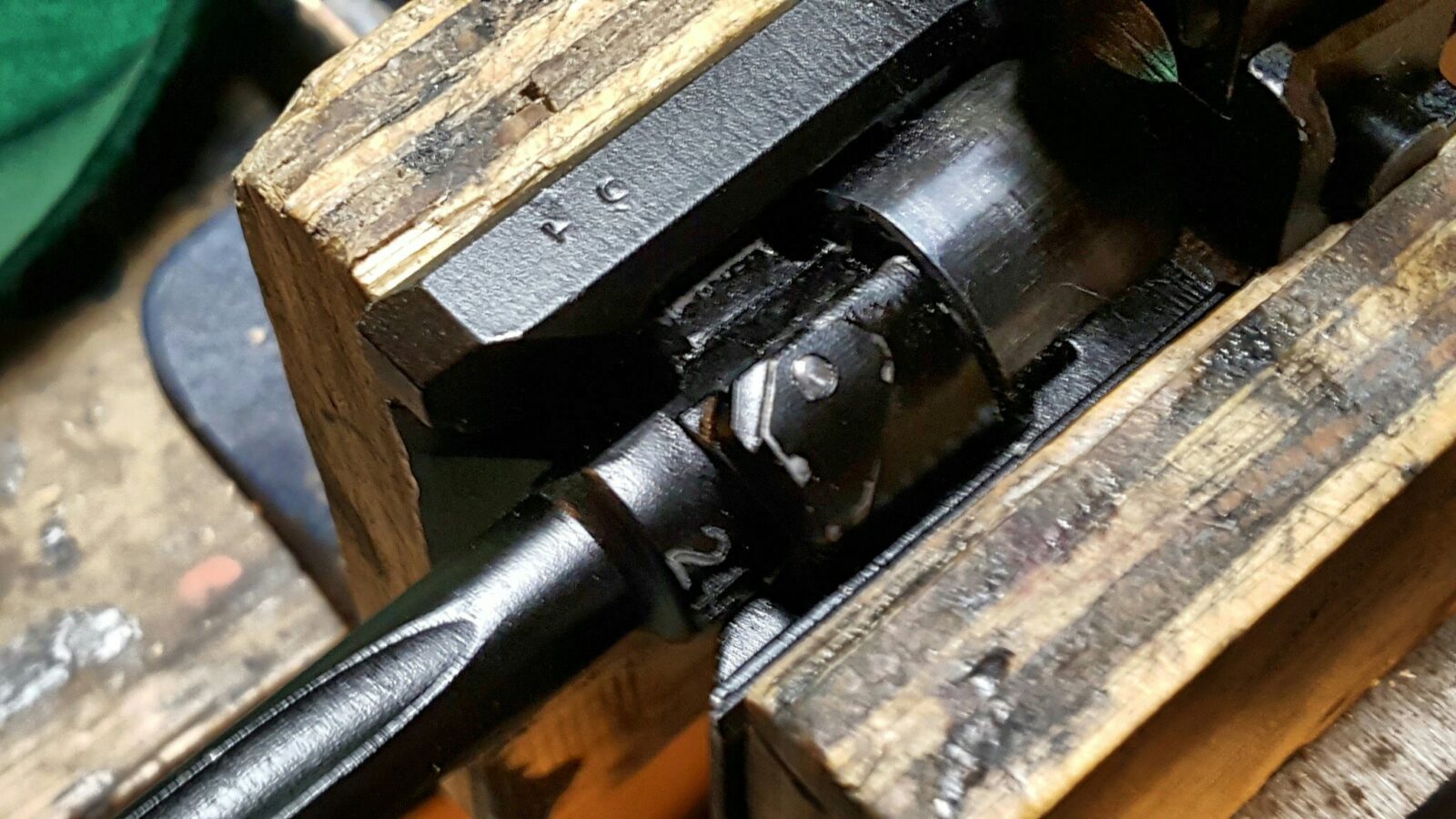
It did not close on NO-GO
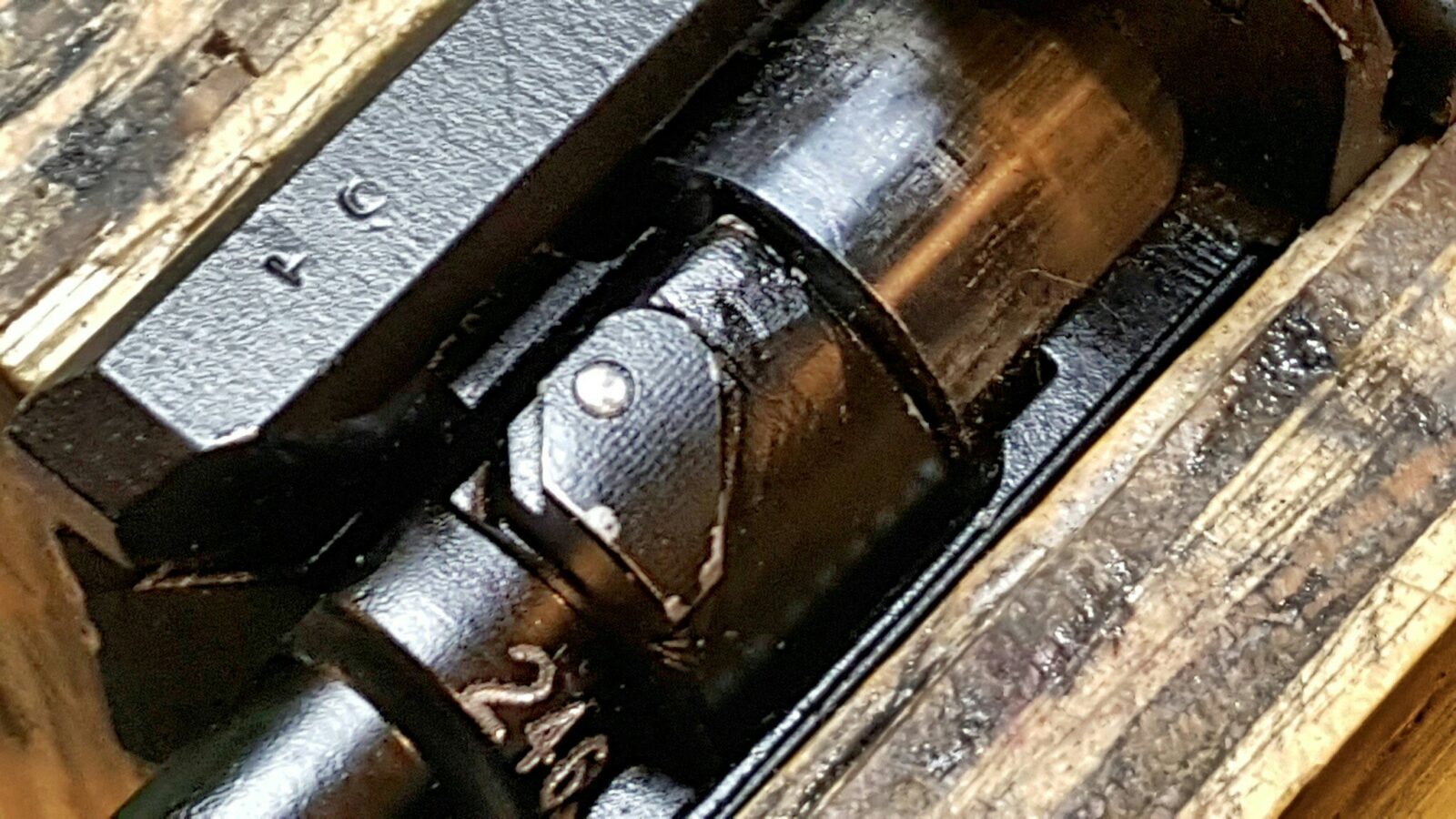
Confirm the Block Alignment
The next quality control check I would recommend is to verify that the barrel “blocks” all align. In other words that the front sight block, gas block and rear sight block all line up properly. Look down the rear trunnion and make sure they all line up properly. If they do not, you have two options. First, if you bought an assembled barrel, I would contact the vendor and arrange either a return or an exchange. They messed up is the bottom line. The second option is to straighten the problem block(s) yourself by driving out the pins from each, correcting the problem and either drilling new holes or using oversize pins. The reason you would go with oversize is if the newly drilled holes would result in a loose fit.
Not only do I want straight blocks for aesthetics but also because I “sight” down the ears of the front trunnion and center the rear sign block (RSB) between the ears when I re-install the barrel – in my case with my IR air hammer.
Press Out the Barrel Pin and the Barrel From The Front Trunnion
So the next step was to knock out the partially installed barrel pin. I used a hammer, one of my gunsmith punches and a block. Note in the next photo how I am ensuring the who barrel assembly has good support before I hammer.
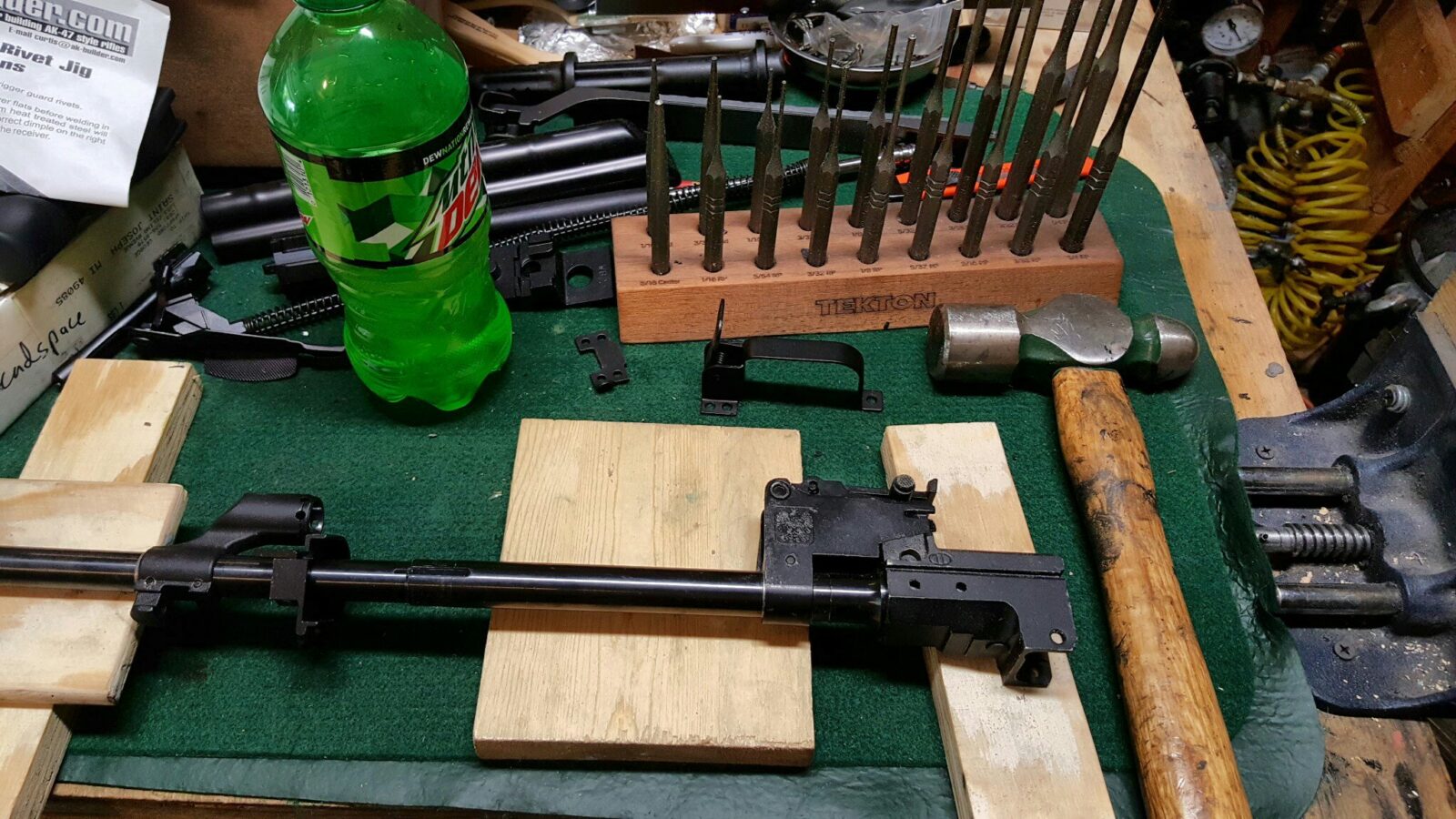
I have also done the above with the trunnion in a vise with brass jaws to prevent marring and used an air hammer with a drift punch in it. I didn’t bother with the air hammer because whomever installed the pin after headspacing the barrel had not inserted it fully. My bet, and I was right, was that it would not take much force to knock the pin out.
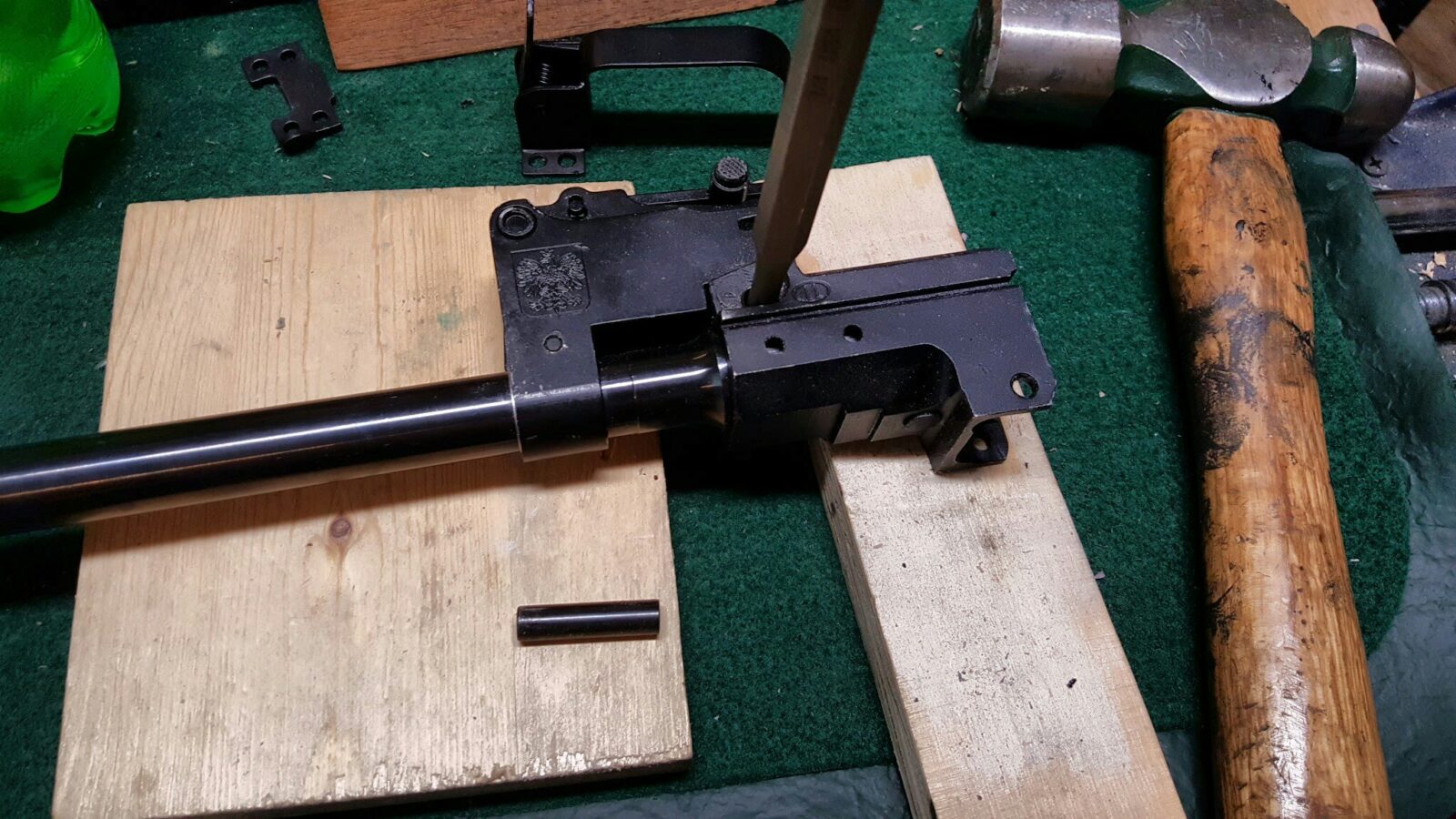
You have at least three options to remove the trunnion and all will work. All of the above will work and it really comes down to what tools you have and what you are comfortable with.
Option One: Press the barrel off the trunnion
To press the barrel off, I would recommend you have at least a 12 ton press. Many guys use Harbor Freight presses and buy them when they go on sale. Basically you either buy a barrel removal jig from some like AK-Builder or you can simply make one from a 1/2″ bolt, a 1/2″ brass nut and a steel backing nut. [Click here for the blog post where I explain how to make a barrel back out tool.
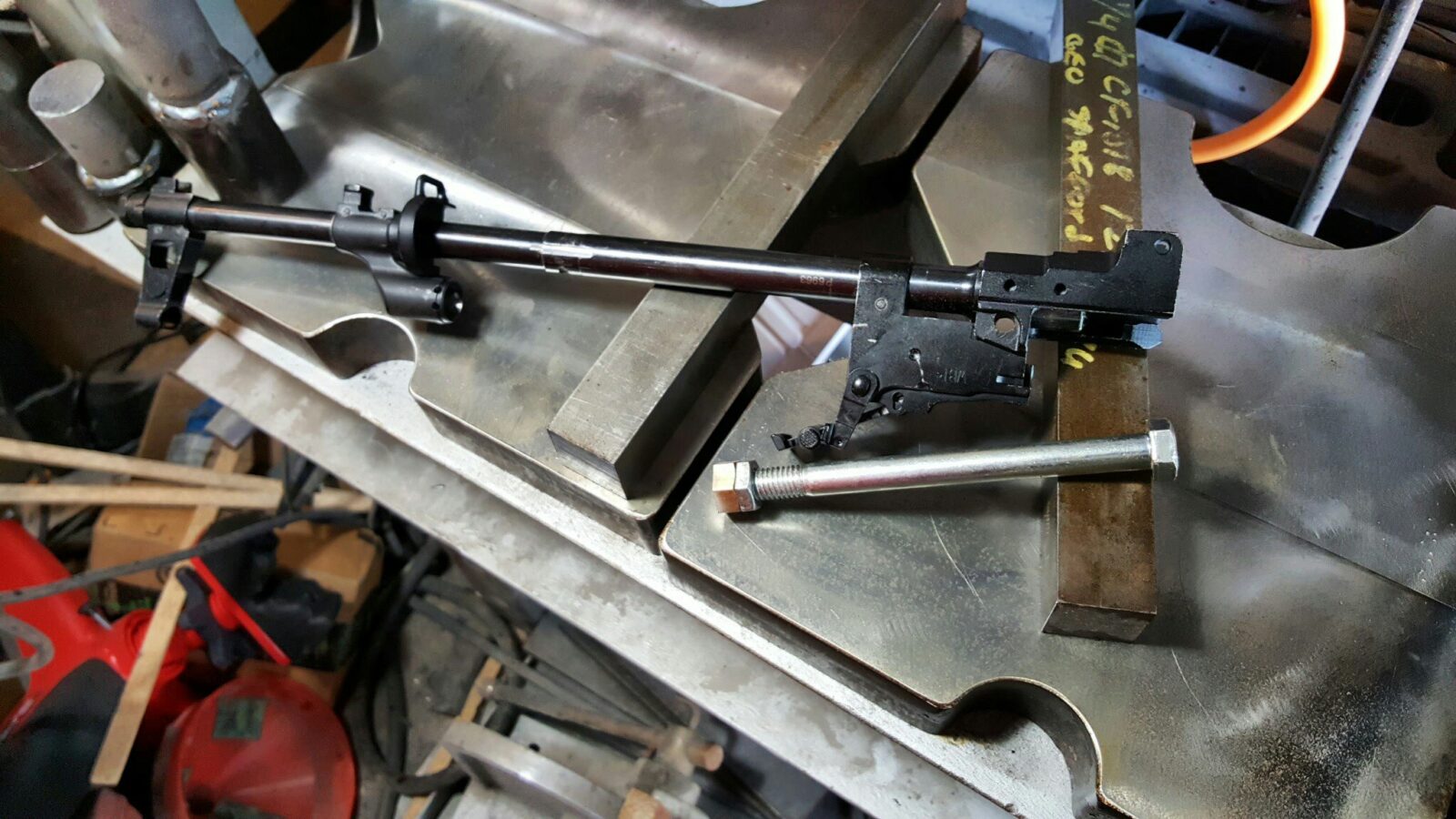
All you need to do is to dangle the barrel downwards and support the front sides of the trunnion with steel blocks. Insert the barrel back out tool, and then apply pressure which will drive the barrel out of the supported trunnion. Be sure to flip the rear sight leaf out of the way.
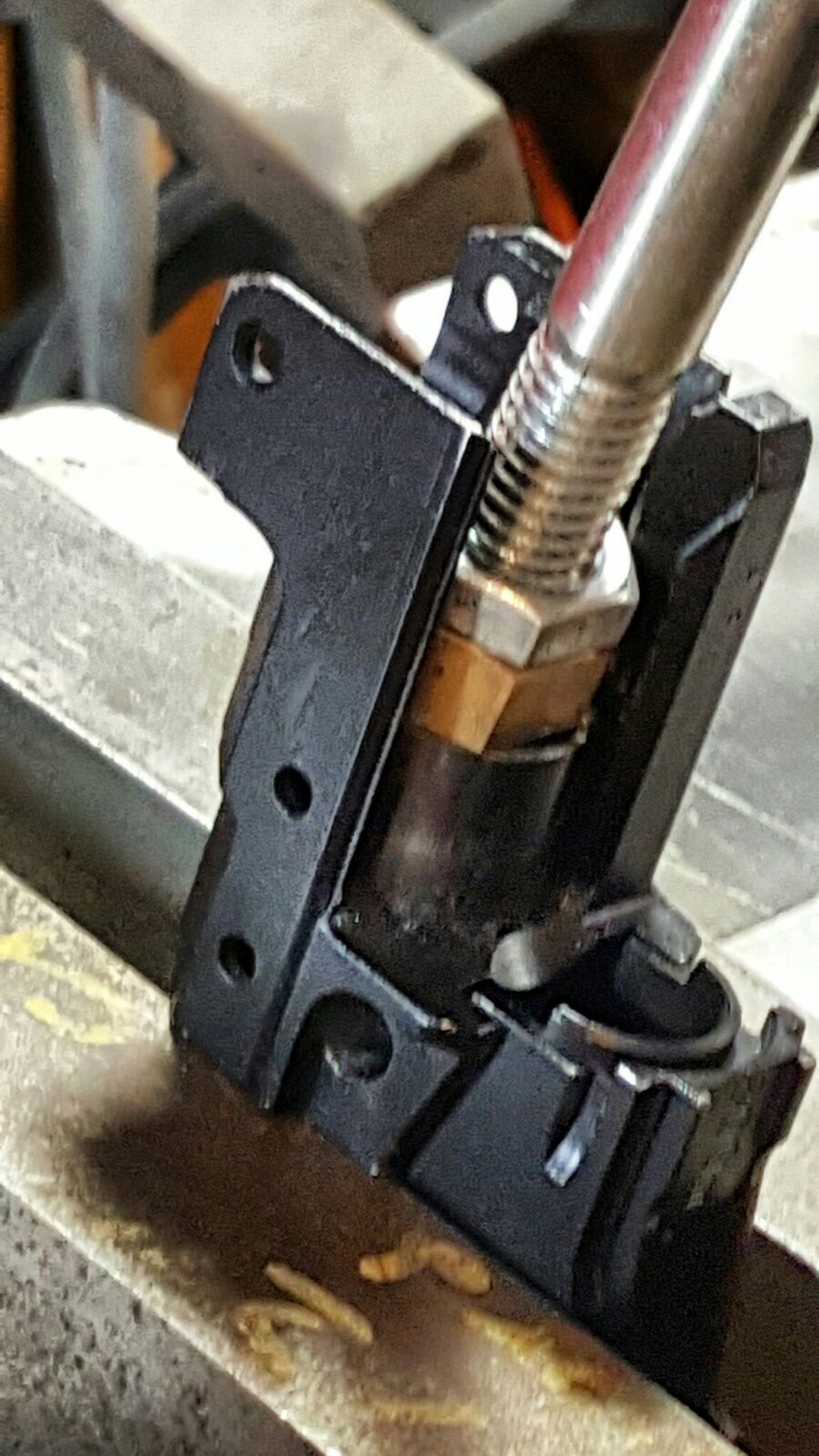
Ensure there is a cushion under the barrel just in case it drops out and you aren’t holding it. I put a box underneat with old shipping materials for example. Also, make sure that the barrel back out tool is sitting only on the barrel and not resting on something else in the trunnion or you may mess something up accidentally.
One thing to bear in mind – this should not take tons and tons of pressure. Guys have cracked their front trunnions by thinking the answer was to apply more and more force. If the barrel doesn’t start moving, make sure the back out tool is not resting on a part of the trunnion by mistake. If it still will not move, then hit the side of the press with a mallet so the shock causes the barrel to break free. Note – this also applies to barrel pins but the pins do take more force to start on old kits. This will be a topic for another day.
Option Two: Use an Air Hammer or Air Riveter to Drive Out the Barrel
This is the actual method I used for this rifle. Being a new barrel, I did not expect a big fight to get the barrel and trunnion to separate. I wrote this up in more detail in another post – click here to read it.
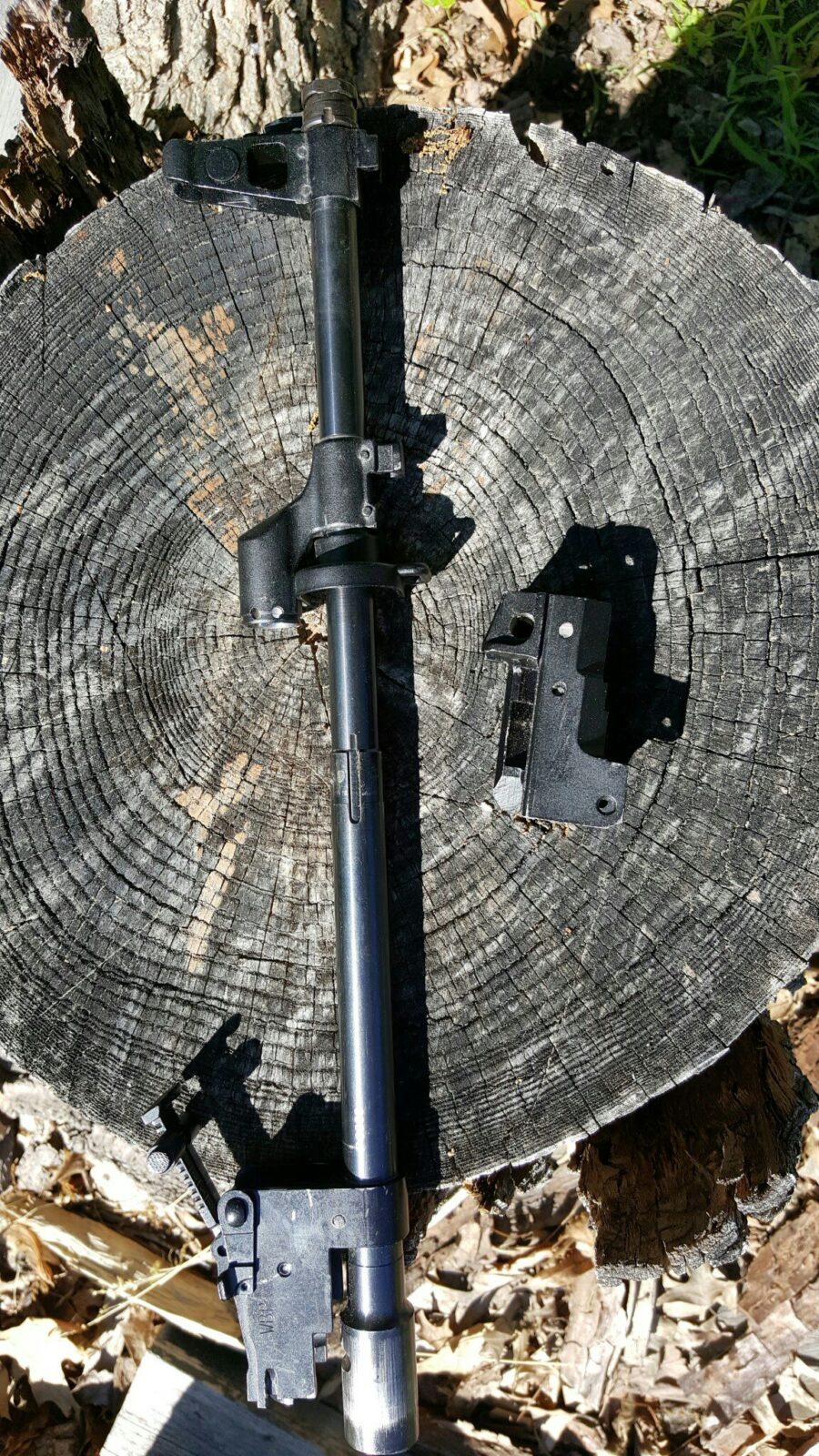
Option 3: Use a Big Hammer
This is very similar to the previous option but a big “fricken” hammer (BFH) is used to hit the barrel back out tool which then drives out the barrel. I don’t care much for this option.
Now, of the three, using an air-hammer or air-riveter is my preferred method. I have talked to guys that have used other methods such as making contraptions out of all-thread rods to press out and install barrels and various types of gear pullers. I suppose you are only limited by your imagination.
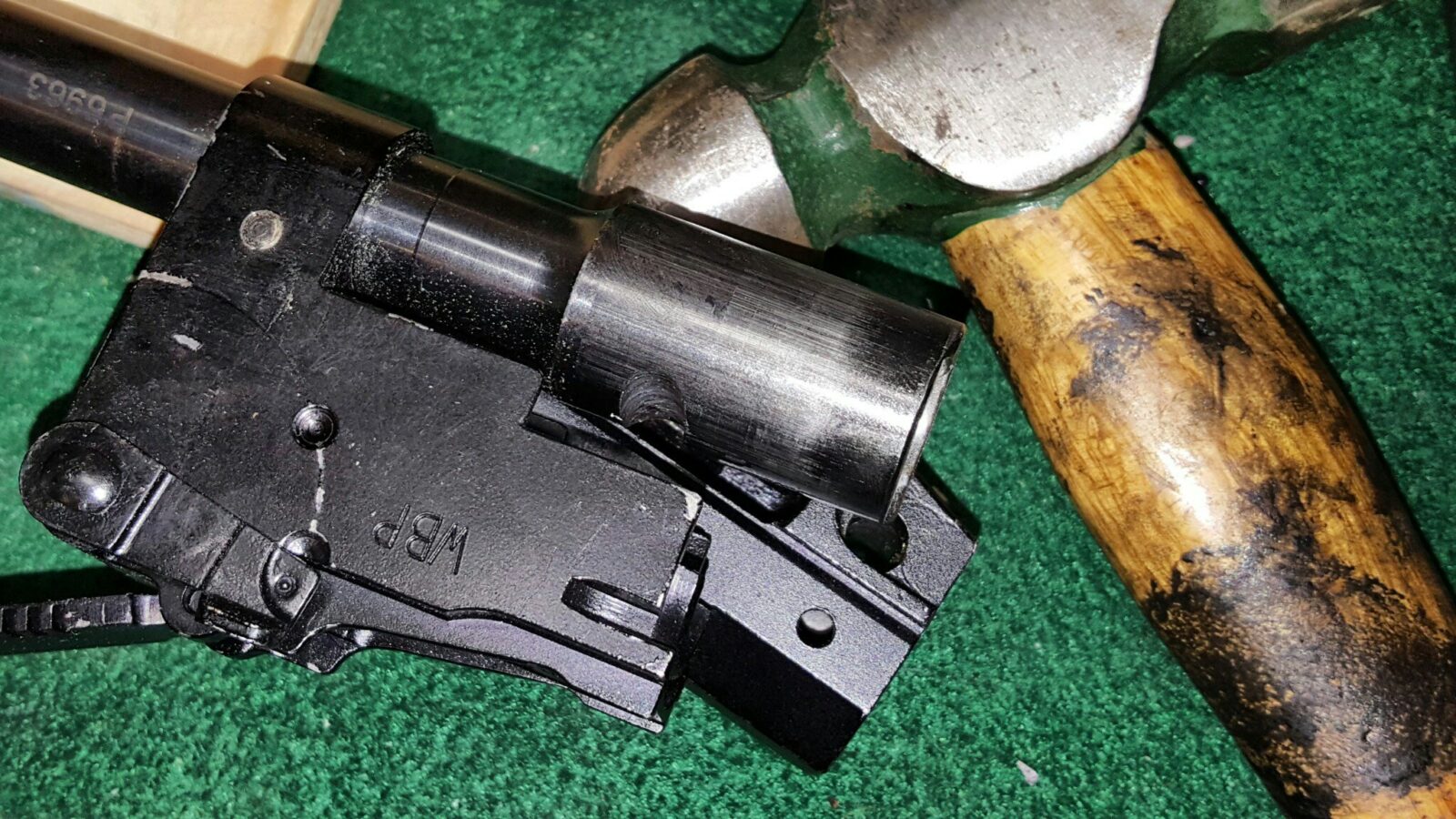
So at this point we have confirmed the head space and removed the front trunnion. We’re ready for the next step which is to install the trunnions in the new receiver. That will be our next blog post.
If you find this post useful, please share the link on Facebook, with your friends, etc. Your support is much appreciated and if you have any feedback, please email me at in**@*********ps.com. Please note that for links to other websites, we are only paid if there is an affiliate program such as Avantlink, Impact, Amazon and eBay and only if you purchase something.
Like this:
Like Loading...