The 1959 introduction of the Avtomat Kalashnikova Modernizirovanniy (AKM) marked a pivotal moment in the history of Soviet small arms manufacturing and global military doctrine. This modernized rifle represented the culmination of a decade-long effort to refine the original AK-47 design, moving away from the costly and time-consuming milled receivers that characterized the Type 2 and Type 3 variants.1 The AKM’s design was revolutionary in its embrace of a mass-producible 1.0 mm stamped sheet steel receiver, a manufacturing approach that had proven problematic in the earliest Type 1 AK-47s but was now perfected.4 This fundamental shift in construction philosophy, from a solid block of steel to a lightweight folded sheet, necessitated the creation of a new, discrete component to bear the immense stresses of firing: the front trunnion.
Known in Russian technical literature as the передний вкладыш (peredniy vkladysh), or “front insert,” the trunnion is the functional heart of the AKM. While the stamped receiver provides the chassis, the trunnion performs the critical tasks previously handled by the forward section of the heavy milled receiver block. It is the structural hub that rigidly secures the barrel, provides the hardened locking abutments for the rotating bolt, contains the immense chamber pressures generated by the 7.62x39mm cartridge (The CIP maximum chamber pressure for the 7.62x39mm cartridge is 355 MPa, which is equivalent to 51,488 psi ), and transmits the violent recoil forces from the bolt carrier group to the receiver shell.6 The mechanical integrity, material composition, and manufacturing quality of this single component are therefore paramount to the safety, accuracy, and operational longevity of the entire weapon system. Its design and fabrication were not afterthoughts but central to the engineering solution that made the lightweight, ubiquitous AKM possible.
The enduring reliability of the AKM platform under the most adverse conditions is a direct testament to the material science and manufacturing doctrine behind its key components. This report seeks to provide a definitive, evidence-based analysis of the specific type of steel used for the front trunnion of the Soviet-era AKM, also commonly referred to by collectors as the AK-47 Type 4.1 By synthesizing data from Russian-language technical and historical sources, analyzing Soviet-era state material standards (GOST), and drawing comparisons to modern engineering practices, this investigation will forensically identify the specific steel grade, manufacturing process, and heat treatment protocols employed by the Soviet military-industrial complex to create one of the most robust and critical components in modern firearms history.
Section 1: The Engineering of the AKM Trunnion: Function and Fabrication
The journey to the AKM’s stamped receiver was neither simple nor direct. Initial attempts at producing a stamped receiver for the Type 1 AK-47 were plagued by manufacturing difficulties, particularly in welding the critical guide rails, leading to high rejection rates.5 The immense pressure to field a new service rifle forced a pragmatic but costly deviation. Soviet industry reverted to a more traditional and resource-intensive method: milling the entire receiver from a solid block of steel. This resulted in the heavy, durable, but slow-to-produce Type 2 (milled from a forging) and Type 3 (milled from bar stock) AK-47s.1 While effective, these rifles were antithetical to the Soviet doctrine of rapid, large-scale production for a mass-conscript army.
The introduction of the AKM in 1959 signaled that these production hurdles had been overcome.1 The design genius of the AKM was not merely in stamping a piece of steel into a U-shape; it was in the strategic isolation of stresses. The engineers recognized that 90% of the receiver was simply a housing, while all of the critical forces were concentrated at the front, where the barrel joined and the bolt locked. The solution was to concentrate the complex, high-strength requirements into a relatively small, precision-made front trunnion that could then be securely riveted into the simple, inexpensive, and rapidly produced stamped steel shell.3 This modular approach was a masterstroke of production efficiency. It allowed the receiver shell to be made quickly on massive presses, while the more complex trunnion could be manufactured on a separate, specialized line. This component was the enabling technology that made the lightweight, reliable, and globally prolific AKM a reality.
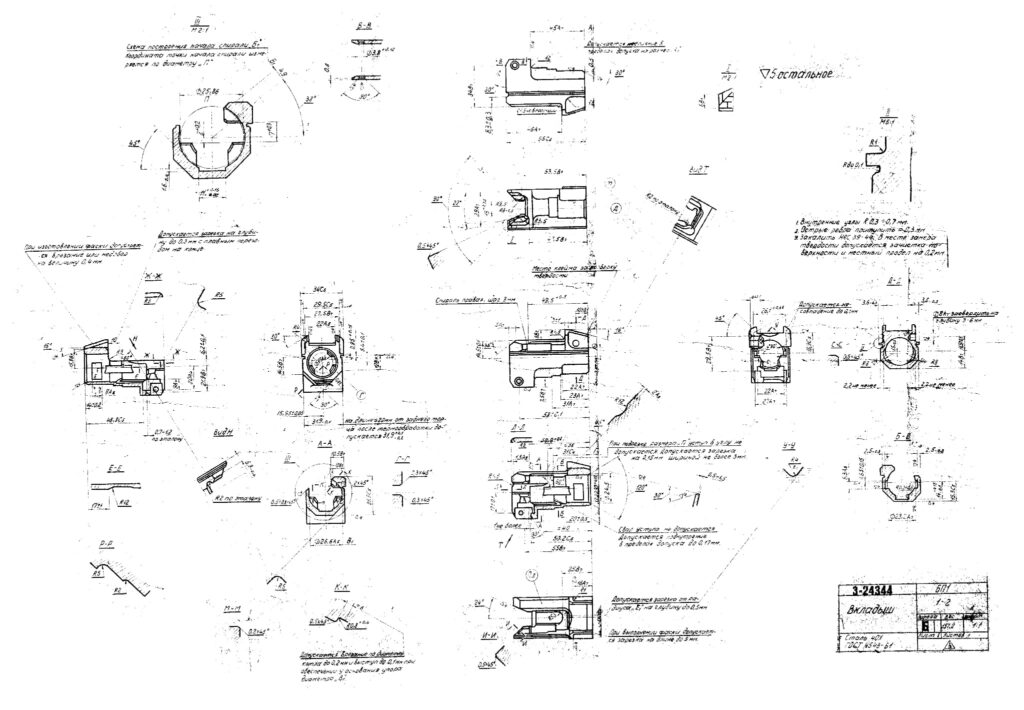
Subsection 1.1: Anatomy of a Critical Component: Analyzing the Forces on the Front Trunnion
The front trunnion is a marvel of compact, multi-functional engineering, subjected to a brutal cycle of forces with every shot fired. A detailed mechanical analysis reveals its four primary roles:
- Barrel Mounting: The trunnion features a precisely machined journal into which the barrel is pressed and secured with a transverse pin.3 This interface is responsible for maintaining the rifle’s critical headspace—the distance from the bolt face to the cartridge seat—and ensuring a rigid, consistent alignment of the barrel with the sighting plane. Any failure or deformation here would be catastrophic.
- Bolt Lock-up: Inside the trunnion are two robust, precisely machined locking recesses. As the bolt rotates into battery, its two opposing lugs engage these surfaces. This lock-up must contain the full rearward thrust of the cartridge case upon firing. For the 7.62x39mm M43 cartridge, this involves peak chamber pressures that can exceed 51,000 psi. The trunnion lugs must withstand this force without shearing, deforming, or developing stress fractures over tens of thousands of cycles.
- Impact Absorption: The AKM operates on a long-stroke gas piston system, known for its powerful and violent action.5 At the rearmost point of its travel, the bolt carrier assembly slams into the front face of the trunnion to initiate the camming action that unlocks the bolt. The trunnion must absorb this high-energy, repetitive impact without cracking or peening.
- Recoil Transmission: As the central structural element, the trunnion serves as the bridge between the barrel/bolt group and the receiver. It transfers the entire recoil impulse from the point of firing into the receiver shell and, ultimately, to the shooter’s shoulder. Its riveted connection to the receiver must be strong enough to handle these shear and tensile loads without loosening over time.
Subsection 1.2: The Soviet Manufacturing Doctrine: From “Стальной Поковки” (Steel Forging) to Final Form
The method of manufacturing the trunnion was as critical as the material itself. Russian-language military and historical sources are unambiguous on this point: the AKM front trunnion was fabricated from a “стальной поковки” (stal’noy pokovki), which translates directly to “steel forging”.6 This was not a part cast from molten metal or machined directly from a simple bar of steel. The process began with a block of steel being heated to a plastic state and then hammered into a rough shape using a set of dies, a process known as die forging.10
The metallurgical advantages of this choice are profound and speak to a deep understanding of materials science within the Soviet design bureaus. Forging imparts several key benefits over other methods like casting:
- Refined Grain Structure: The intense pressure of the forging process breaks down the coarse, random grain structure of the initial steel billet, refining it into a fine, uniform structure.
- Oriented Grain Flow: Crucially, the forging process forces the metal’s internal grain to flow and align with the contours of the part. This creates continuous grain lines that follow the shape of the locking lugs and barrel journal, drastically increasing the component’s toughness, ductility, and resistance to fatigue and impact. It is analogous to the difference in strength between a piece of wood cut with the grain versus against it.
- Elimination of Porosity: Forging physically compresses the steel, eliminating the microscopic voids, gas pockets, and inclusions that can be present in castings. These defects act as stress risers and are often the origin points for catastrophic fractures.
The explicit choice of forging over casting—a method used in some modern, lower-quality commercial AK variants which have demonstrated notable failures 11—is a foundational Soviet military principle in action. For a critical, high-load component like a trunnion, where reliability is paramount, the superior toughness and fatigue life of a forging was non-negotiable. After the initial forging process created the basic shape and optimized grain structure, the part was then subjected to precision machining operations to cut the final, critical dimensions of the locking lug surfaces, the barrel journal, and the rivet holes.10 This two-step method combined the raw strength of forging with the high precision of machining, creating a component optimized for its demanding role.
Section 2: Primary Evidence and Interpretation: Decoding Soviet-Era Documentation
Subsection 2.1: Analysis of the Key Descriptor: “Легированная Конструкционная Сталь” (Alloy Structural Steel)
The most significant piece of direct evidence regarding the trunnion’s material comes from the Russian military history publication dogswar.ru. It states that the primary load-bearing insert—the front trunnion—is manufactured from “легированная конструкционная сталь” (legirovannaya konstruktsionnaya stal’).6 A careful deconstruction of this technical term provides the primary vector for our investigation:
- Сталь (Stal’): “Steel.” The base material is an alloy of iron and carbon.
- Конструкционная (Konstruktsionnaya): “Structural.” This is a broad but important classification. It designates the steel as being intended for use in construction and machine-building applications where mechanical properties—such as tensile strength, yield strength, toughness, and fatigue resistance—are the primary design considerations. This immediately rules out tool steels (valued for hardness and wear resistance at the expense of toughness) and simple sheet steels.
- Легированная (Legirovannaya): “Alloyed” or “Alloy.” This is the most critical descriptor. It confirms that the steel is not a simple carbon steel. Elements other than iron and carbon have been deliberately added to the melt in controlled quantities to achieve specific, enhanced properties that cannot be obtained with carbon alone.
This three-word phrase, therefore, narrows the field of potential materials from hundreds of possibilities to a specific class of steels defined under the Soviet standards system: alloyed structural steels. In the context of the Soviet Union’s focus on logistical simplicity and the use of widely available materials for mass production 5, this term does not imply a complex or exotic high-alloy steel (like a modern chrome-moly-vanadium specialty steel). Instead, it points toward a well-defined, economical, and extensively produced family of medium-carbon structural steels that contain key, but common, alloying elements.
Subsection 2.2: Contextual Clues from the Soviet Military-Industrial Complex
To further refine the search, it is instructive to examine the material specifications for other related components produced within the Soviet sphere of influence. This establishes a pattern of material selection and demonstrates the specificity of Soviet engineering.
For instance, analysis of the 5.45x39mm 7N6 cartridge, which replaced the 7.62x39mm, reveals that its mild steel penetrator core was made from Steel 10 (Сталь 10), a plain low-carbon steel.13 This shows that specific, numbered grades of steel were indeed called out in technical packages.
More directly relevant is the material used for Warsaw Pact AK magazines. High-quality Bulgarian steel magazines, produced to Soviet-era specifications, are explicitly documented as being manufactured from heat-treated, high-grade carbon steel compliant with GOST 1050-88.14 This provides a direct and powerful link to a specific Soviet state standard for a high-stress firearm component. The use of different steels for different parts—a soft, low-carbon steel for a bullet core designed to deform, a hardenable carbon steel for a magazine body requiring rigidity, and a tough, forgeable alloy steel for a trunnion—reveals a highly sophisticated and deliberate material selection process. It was not a crude, one-size-fits-all approach but a tailored engineering strategy based on the unique mechanical demands of each part. The evidence strongly suggests that the “alloy structural steel” of the trunnion would also be defined by a specific GOST standard.
Section 3: Identifying Candidate Materials: An Analysis of Soviet GOST Standards
The entire Soviet industrial base operated under the framework of the ГОСТ (GOST, an acronym for Gosudarstvennyy standart or State Standard). This all-encompassing system of technical standards ensured uniformity, interoperability, and quality control. The description “alloy structural steel” points toward two primary candidate standards, each representing a different but equally valid Soviet engineering philosophy.
Subsection 3.1: Candidate Standard 1: GOST 1050-88 — The “Mass Production” Philosophy
The first candidate is GOST 1050-88: “Sized Bars Made Of High-Quality Structural Carbon Steel with A Special Surface Finish.” While its title specifies “carbon” steel, the standard includes grades with significant manganese content (0.50-0.80%), which technically classifies them as low-alloy steels and fits the description of “alloy structural steel” in the Soviet context. The use of this standard for other high-stress components like magazines supports its candidacy. This choice would reflect a philosophy of using a common, economical, and versatile steel suitable for massive-scale production. The most likely grades from this standard are Steel 40, Steel 45, and Steel 50, which possess the medium carbon content necessary for effective heat treatment.
Table 1: Chemical Composition of GOST 1050-88 Candidate Steels (%)
Steel Grade | Carbon (C) | Silicon (Si) | Manganese (Mn) | Chromium (Cr) | Sulfur (S) | Phosphorus (P) |
Steel 40 | 0.37 – 0.45 | 0.17 – 0.37 | 0.50 – 0.80 | ≤0.25 | ≤0.040 | ≤0.035 |
Steel 45 | 0.42 – 0.50 | 0.17 – 0.37 | 0.50 – 0.80 | ≤0.25 | ≤0.040 | ≤0.035 |
Steel 50 | 0.47 – 0.55 | 0.17 – 0.37 | 0.50 – 0.80 | ≤0.25 | ≤0.040 | ≤0.035 |
Subsection 3.2: Candidate Standard 2: GOST 4543-71 — The “High Performance” Philosophy
The second, and perhaps more likely, candidate is GOST 4543-71: “Rolled products from alloyed structural steel.”10 The title of this standard is a near-perfect match for the primary source description of “легированная конструкционная сталь”.7 This standard covers steels with more significant alloying elements, such as chromium, which are specifically designed for high-strength, high-fatigue applications. This choice would reflect a philosophy of selecting a specialized, higher-performance material specifically for the most critical component in the rifle. The most likely grades from this standard are
40X and 45X, which are chromium-alloyed steels.
Table 2: Chemical Composition of GOST 4543-71 Candidate Steels (%) 12
Steel Grade | Carbon (C) | Silicon (Si) | Manganese (Mn) | Chromium (Cr) | Sulfur (S) | Phosphorus (P) |
40X (40Cr) | 0.36 – 0.44 | 0.17 – 0.37 | 0.50 – 0.80 | 0.80 – 1.10 | ≤0.035 | ≤0.035 |
45X (45Cr) | 0.41 – 0.49 | 0.17 – 0.37 | 0.50 – 0.80 | 0.80 – 1.10 | ≤0.035 | ≤0.035 |
Section 4: The Decisive Process: Heat Treatment and Final Performance Characteristics
Subsection 4.1: The Metallurgical Imperative: Balancing Hardness and Toughness
The raw, normalized properties of the steel forging are insufficient for the final application. A trunnion must possess a complex combination of competing properties: the locking lug surfaces must be extremely hard to resist wear and deformation from the repeated impact and friction of the bolt lugs, while the core of the component must remain tough and ductile to absorb the shock of firing and bolt carrier impact without fracturing. A material that is uniformly hardened to an extreme degree will be brittle and prone to catastrophic failure. The method for achieving this critical balance of a hard, wear-resistant case and a tough, shock-resistant core is heat treatment.
Subsection 4.2: Analysis of GOST-Specified Heat Treatment Protocols
Both GOST standards provide detailed protocols for heat treatment.14 The process for a component like a trunnion would involve two key stages:
- Hardening (Закалка, Zakalka): The machined forging is heated to a specific austenitizing temperature, where its internal crystal structure transforms. For Steel 45, this is 820–860°C; for 45X, it is 840°C.14 Once uniformly heated, it is rapidly cooled (quenched) in a medium like water or oil. This rapid cooling traps the carbon in a very hard, brittle, needle-like crystal structure known as martensite.
- Tempering (Отпуск, Otpusk): The now-hardened but brittle part is reheated to a much lower temperature (for Steel 45, 550–600°C; for 45X, 520°C) and held for a period.14 This process allows some carbon to precipitate out of the martensite, relieving internal stresses and transforming the microstructure into tempered martensite. This crucial step reduces brittleness and restores a significant amount of toughness, sacrificing some of the peak hardness for a much more durable final product.
The precise control of these parameters allows the engineer to dial in the final properties of the component. For a trunnion, a target hardness in the range of 40-45 on the Rockwell C scale (HRC) is considered ideal, providing excellent surface durability while ensuring the core remains tough enough to prevent fracture. Both families of candidate steels are capable of achieving this hardness range. Data within GOST 1050-88 shows that Steel 45 can achieve a hardness of 49-58 HRC after quenching, which is then reduced during tempering to the desired final hardness.
Section 5: A Comparative Framework: Soviet Steels vs. Modern International Equivalents
Subsection 5.1: An Examination of Modern Materials for AK-Pattern Trunnions
To contextualize the Soviet material choice, it is useful to examine the steels used in high-quality modern commercial and military production of AK-pattern rifles. These materials represent the current state-of-the-art and serve as a valuable performance benchmark. Across the industry, the most commonly specified and respected materials for forged AK trunnions are chromium-molybdenum (chromoly) alloy steels.
The two most prominent grades are:
- AISI 4140 Steel: A medium-carbon chromoly steel renowned for its excellent balance of toughness, fatigue strength, and wear resistance after heat treatment. It is a go-to material for high-stress applications from firearm components to automotive axles.
- AISI 4150 Steel: Similar to 4140 but with a higher carbon content, allowing it to achieve greater hardness. It is often specified for military-grade barrels and other components requiring maximum durability.
These modern choices validate the fundamental engineering requirements for a trunnion: a forgeable, medium-carbon alloy steel that responds exceptionally well to heat treatment.
Subsection 5.2: Drawing Parallels: How Modern Material Choices Validate Historical Soviet Engineering
When the chemical and mechanical properties of the Soviet candidates are placed alongside their modern counterparts, a clear picture of parallel technological development emerges. The Soviet engineers, working with the materials available to their massive industrial base, arrived at solutions that were functionally equivalent to the more complex alloys used today.
The steels from GOST 1050-88 (Steel 45, Steel 50) achieve their properties through a medium carbon content and an elevated manganese content. The steels from GOST 4543-71 (40X, 45X) achieve their properties through a similar medium carbon content but with a significant addition of chromium. This makes them the direct chemical and functional analogues of modern AISI 4140 and 4150 steels. The choice between the two Soviet standards represents a choice between a simpler manganese alloy and a higher-performance chromium alloy to achieve the same engineering goal.
Table 3: Comparative Analysis of Soviet GOST Steels and US AISI 4140/4150 Steels
Specification | Steel Grade | Carbon (C) % | Manganese (Mn) % | Chromium (Cr) % | Molybdenum (Mo) % | Functional Analogy |
GOST 1050-88 | Steel 45 | 0.42 – 0.50 | 0.50 – 0.80 | ≤0.25 | – | Economical, high-volume |
GOST 4543-71 | 40X | 0.36 – 0.44 | 0.50 – 0.80 | 0.80 – 1.10 | – | Direct analogue to 4140 |
GOST 4543-71 | 45X | 0.41 – 0.49 | 0.50 – 0.80 | 0.80 – 1.10 | – | Direct analogue to 4140/4150 |
AISI/SAE | 4140 | 0.38 – 0.43 | 0.75 – 1.00 | 0.80 – 1.10 | 0.15 – 0.25 | Modern benchmark |
AISI/SAE | 4150 | 0.48 – 0.53 | 0.75 – 1.00 | 0.80 – 1.10 | 0.15 – 0.25 | Modern high-hardness benchmark |
This table serves as a “Rosetta Stone,” translating the Soviet specifications into a familiar modern context. It demonstrates that the Soviet choices were not inferior, but rather different and highly effective paths to the same engineering destination.
Conclusion: A Definitive Finding on the Soviet AKM Trunnion Steel
The evidence, drawn from Russian technical descriptions, analysis of Soviet-era state standards, and comparison with modern engineering materials, converges on a clear conclusion. The manufacturing process for the Soviet AKM front trunnion began with the die forging of a steel billet, a method chosen to impart maximum toughness and fatigue resistance to this critical, high-stress component.7 The material itself was an “alloy structural steel” that was subsequently heat-treated to achieve a precise balance of surface hardness and core toughness.
While the exact technical package for the AKM remains classified, the available evidence points to two highly plausible material specifications, representing two distinct but valid Soviet engineering philosophies:
- The “Mass Production” Candidate (GOST 1050-88): It is possible the trunnion was made from Steel 45 or Steel 50. These are economical, manganese-alloyed structural steels that, while officially designated as “carbon steels,” contain sufficient manganese to be considered low-alloy. This choice would prioritize logistical simplicity and the use of a common, versatile material for the widest possible production, a hallmark of Soviet military doctrine.
- The “High Performance” Candidate (GOST 4543-71): It is equally, if not more, plausible that the trunnion was made from a dedicated chromium-alloyed steel such as 40X or 45X. The description “alloy structural steel” is a direct match for the title of the GOST 4543-71 standard. Furthermore, these steels are the direct Soviet-era analogues to the modern AISI 4140 and 4150 steels universally favored for high-quality AK trunnions today. This choice would reflect a decision to use a specialized, superior-performance material for the single most critical component of the rifle.
In conclusion, while absolute certainty is elusive without the original blueprints, the evidence strongly supports that the AKM front trunnion was forged from a medium-carbon alloy steel. The choice was between a common manganese-alloyed steel like Steel 45 (under GOST 1050-88) or a higher-performance chromium-alloyed steel like 40X or 45X (under GOST 4543-71). Both pathways would result in a component possessing the extraordinary durability required for a service rifle intended to function reliably through decades of use in the harshest environments on Earth.
Works cited
- AK-47 – Survival, accessed July 14, 2025, http://landsurvival.com/schools-wikipedia/wp/a/AK-47.htm
- AKM – Wikipedia, accessed July 14, 2025, https://en.wikipedia.org/wiki/AKM
- Kalashnikov and Molot made AK trunnions – AK Operators Union, Local 47-74, accessed July 14, 2025, https://www.akoperatorsunionlocal4774.com/2017/03/kalashnikov-made-ak-trunnions/
- AK47 Rifles for Sale | Nampa Idaho – Northwest Gun Supply, accessed July 14, 2025, https://www.northwestgunsupply.com/ak-47
- AK-47 – Wikipedia, accessed July 14, 2025, https://en.wikipedia.org/wiki/AK-47
- Beginners Guide To AK-47 Parts And Function, accessed July 14, 2025, https://blog.primaryarms.com/guide/guide-to-ak47-parts/
- Gunsmith Viktor Kalashnikov passes away – MercoPress, accessed July 14, 2025, https://en.mercopress.com/2018/03/28/gunsmith-viktor-kalashnikov-passes-away
- Manufacturing process of parts on the AK – Page 2 – AK-47 / AK-74 – Palmetto State Armory, accessed July 14, 2025, https://palmettostatearmory.com/forum/t/manufacturing-process-of-parts-on-the-ak/742?page=2
- SIZED BARS MADE OF HIGH-QUALITY STRUCTURAL CARBON …, accessed July 14, 2025, https://www.tubemfg.com/files/GOST/GOST%201050-88.pdf
- Technical Properties of 30khgsa Steel Rods (Gost 4543-71 / 2590-88) | PDF – Scribd, accessed July 25, 2025, https://www.scribd.com/document/482194656/30KhGSA1
- 5.45×39mm – Wikipedia, accessed July 14, 2025, https://en.wikipedia.org/wiki/5.45%C3%9739mm
- Steel 40X: characteristics, properties, analogues – Metinvest, accessed July 25, 2025, https://metinvestholding.com/en/products/steel-grades/40x
- ГОСТ 4543-71 Прокат из легированной конструкционной стали (технические у, accessed July 25, 2025, https://uaz74.ru/files/gost/gost-4543-71.pdf
Сталь 45Х: характеристики и наличие – Металлопрокат, accessed July 25, 2025, https://msk-metall.com/marki-stali/konstruktsionnye-stali/legirovannye-stali/45h