Everyone needs a hobby. I guess mine is creating or fixing things in my own way. Back in 2014, I bought an absolutely massive beat to hell 24-1/2″ hog splitter off eBay. This thing was absolutely a diamond in the rough. Clearly it had been used very heavily – probably for decades – yet there was an amazing design in that beat up cleaver as well. First off, the blade was almost a half inch thick and it weighed about five pounds. Back in the days before machinery, you need mass to butcher big animals and this was (and still is) the most massive cleaver I have personally worked with – imagine a baseball bat with one hell of a heavy end is what it boils down to.
In the eBay listing, the seller was up front – this thing was on its last leg. The wood was all busted up, dirty as heck and the blade was loose. Of course, I had to buy it! Here’s what it looked like when it arrived. Why I did not get an overall photo at the start, I do not know.
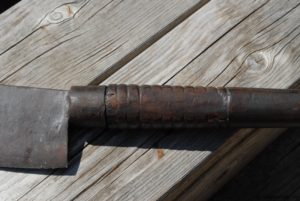
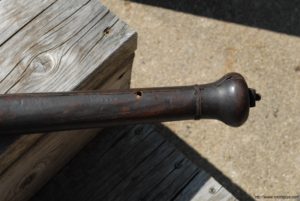
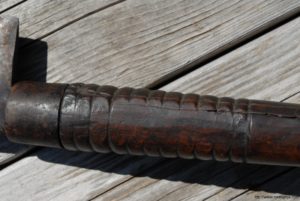

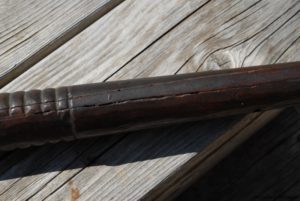
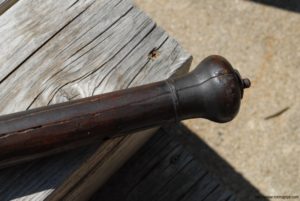
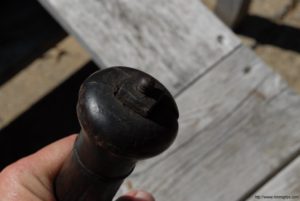
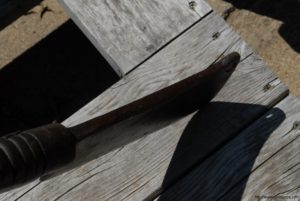
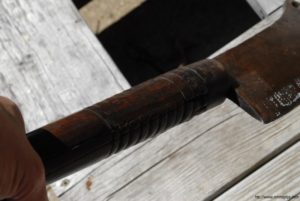
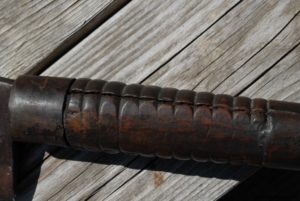
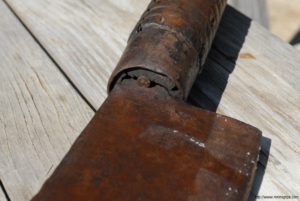
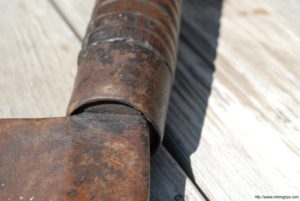
There were no maker’s marks anywhere but it was too professionally done to have been a village blacksmith. I still wonder who made this as I would love to track down more of them. If you have one, or find one, and are interested in potentially parting with it, let me know. I’d even be happy with just the giant blade.
Getting back to the story, I had to look it over and take stock. This thing was stunningly heavy and the wood was busted up because it was thin and hollow.
There had to be more than what I was seeing so I broke the frozen on nut and pulled the handle off. Wow. There was the largest rat tail tang I had ever seen – and still haven’t seen one bigger!! That’s how they spread the load. What an interesting design.
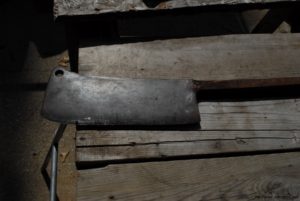
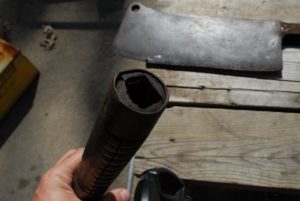
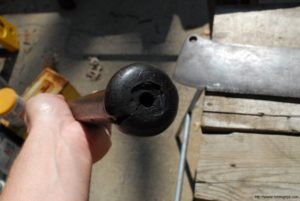
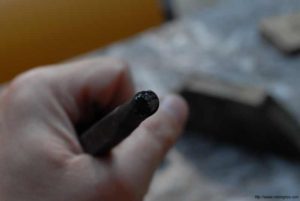
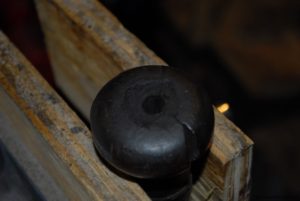
Now, the wood totally intrigued me. There was something about the color that caught my eye so I decided to fill it with glass reinforced epoxy. Now not all epoxies are equal. When you do structural work like this, you need an excellent shock resistant epoxy. My go to epoxy for stuff like this is Acraglas liquid epoxy from Brownells.
I but it in quart bulk containers and meter it out using syringes or a digital scale. I use 5/32nds milled glass fibers and black dye to color it. Fortunately, it’s the same dye I use for my plastics but you can either buy from Brownells or elsewhere. So, over the course of several days, I mixed, poured and let it sit overnight as it takes Acraglas 24 hours to cure so this work is done in steps.
I used wood stripper to try and get all the grease and oils out of the handle plus I drilled open the end to fill it easier. By the way, if you heat epoxy with a heat gun, it will get thinner and flow more readily until it cools. Gentle warmth also accelerates curing of the epoxy but remember that just because epoxy feels dry to the touch does not mean it has fully cured – read the instructions for whatever brand you go with.
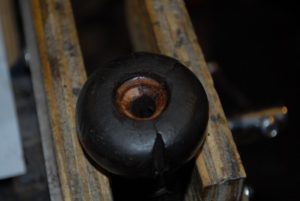
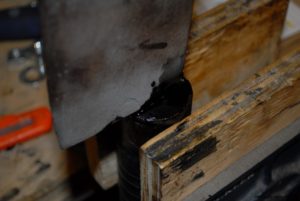
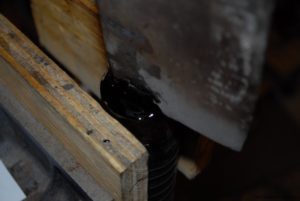
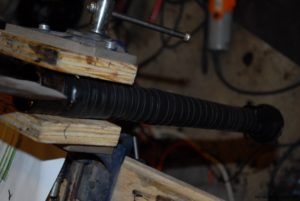
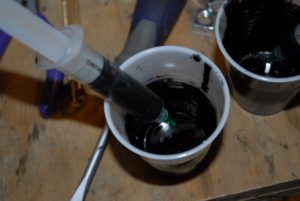
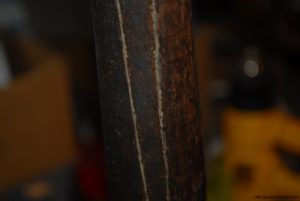
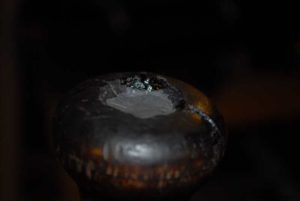
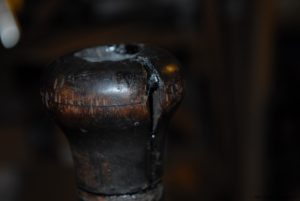

Next, I sanded, sanded and sanded. The wood was very interesting – maybe a cherry or mahogany. I’m not really sure.
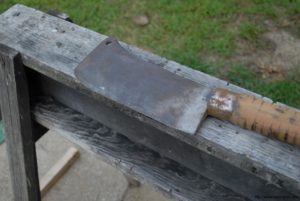
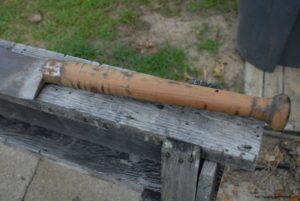
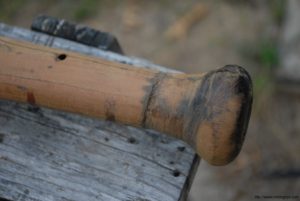
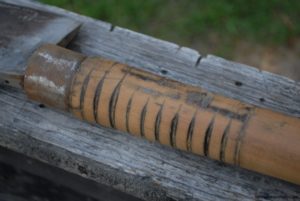
The rat tang was HUGE. I carefully marked where it was at and drilled holes for two brass pins just to play it safe. I’ve never had Acraglas let go from a clean prepped surface but never say never. The pins are a cheap insurance for a giant blade like this. I inserted the 3/16″ pins with epoxy and then added epoxy to all the imperfections followed by more sanding. Notice how I blasted the pins before gluing? Epoxy always, always, always does better on a rough surface. Do not epoxy two shiny metal surfaces together and expect them to last – they probably will not.
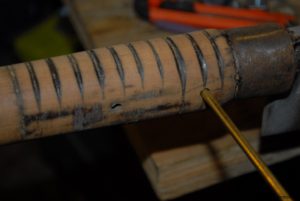
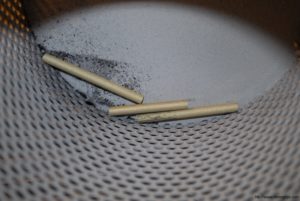
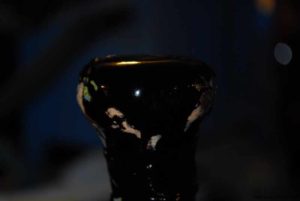
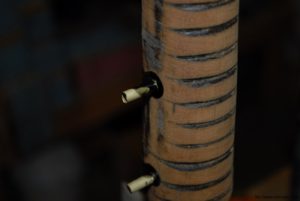
Now this took my breath away. I used a 50/50 combination of turpentine and boiled linseed oil (BLO), put it in a tank I have just for these big cleavers and let it sit for a few hours before I pulled it out. The color blew me away. Wow!! I wiped it down and then applied additional coats of BLO to seal it.
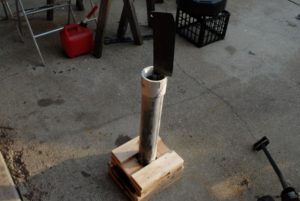
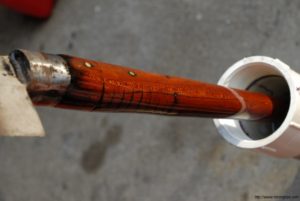
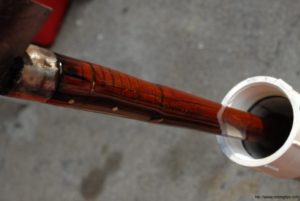
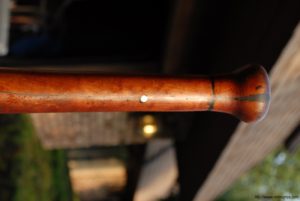
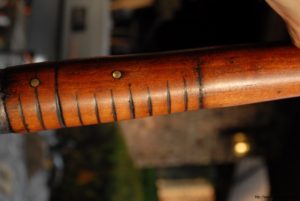
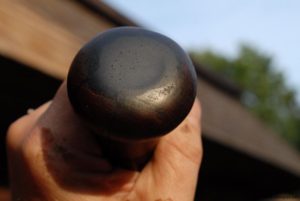
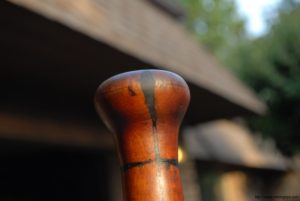
My last steps were to acid etch the blade (click here for our guide to acid etching), seal everything with BLO and then make a blade guard. Mission accomplished.
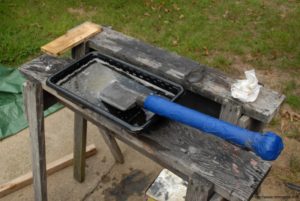
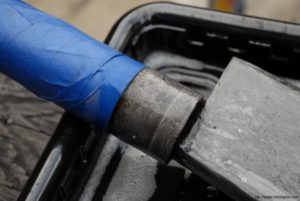
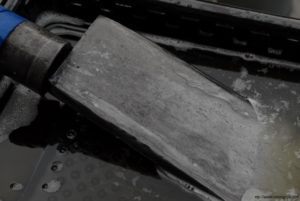
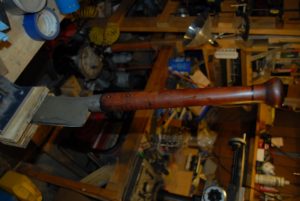
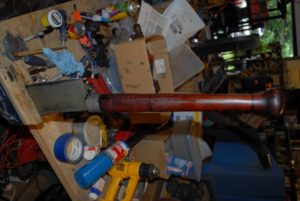
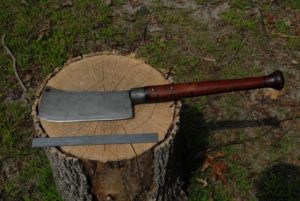
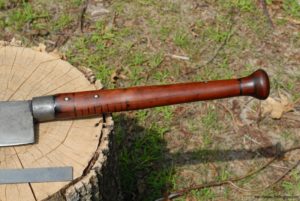
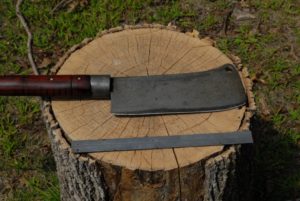
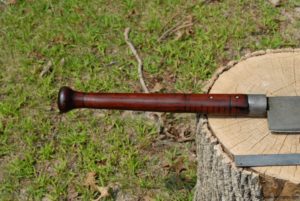
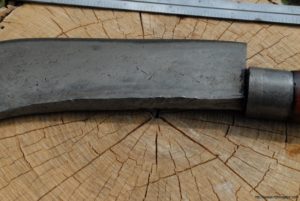
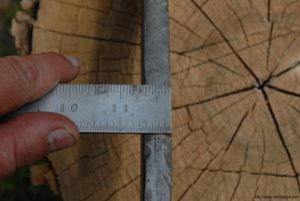
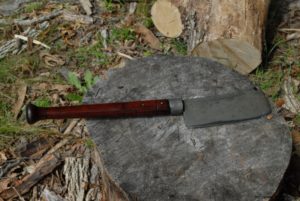
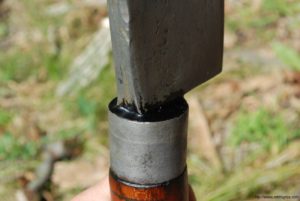
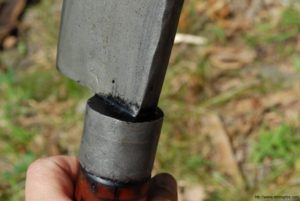
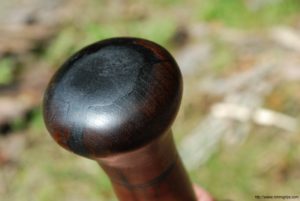

To protect the blade edge, not to mention protect other things from the edge, I made a protective cover out of 0.093 Kydex and 3/8″ shock (bungee) cord.
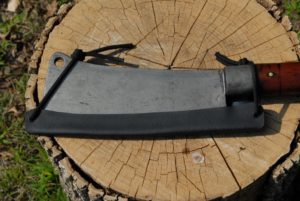
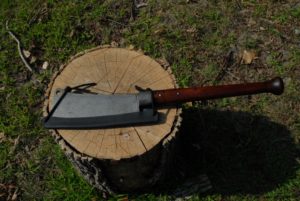
That bad boy weighed 5-1/4 pounds and was solid as a rock. I keep looking for another one like it. I never did find out where it was made but it sure was a stunner. This is another project that part of me wishes I had kept it but it went to a very happy new owner shortly after I finished it.
3/4/2020 Update: This is still the most wicked restored cleaver I have done. The wood was simply gorgeous.
If you find this post useful, please share the link on Facebook, with your friends, etc. Your support is much appreciated and if you have any feedback, please email me at in**@*********ps.com. Please note that for links to other websites, we are only paid if there is an affiliate program such as Avantlink, Impact, Amazon and eBay and only if you purchase something.
The following is a real-time search of eBay using keywords that have worked for me in the past and I hope they help you find something (note a few odd items might show up just like any other search does):