The defacto standard rear connector for braces and stocks on large format pistols is the 1913 Picatinny Rail adapter. The concept was pioneered by Justin McMillion and his firm JMAC. The idea exploded and now tons of companies offer adapters, stocks and braces to do just that. So, when I started planning my VMAC9 builds (they are basically MAC-11 9mm firearms), I knew I wanted a 1913 rear rail for flexibility.
Vendors of Adapters
A3 Tactical, Practical Solutions and Stormwerkz were all contenders because I used different products of their’s in the past. The A3 Tactical and Stormwerkz designs are similar – the are aluminum and cradle the rear to limit movement. The Practical Solutions model is a thick chunk of carbon steel welded at a right angle but does not cradle the rear.
I went with the Practical Solutions model because it is steel and I figured I could compensate if there was movement. Any design with a single mounting point is at risk of moving/working loose over time.
My Problem
Now, I did run into a challenge. The Practical Solution’s adapter needs to sit flat against the back of the receiver and that assumes the rear is at a right angle from the bottom. For whatever reason, none of my receivers had a rear at a right angle — all were slightly off.
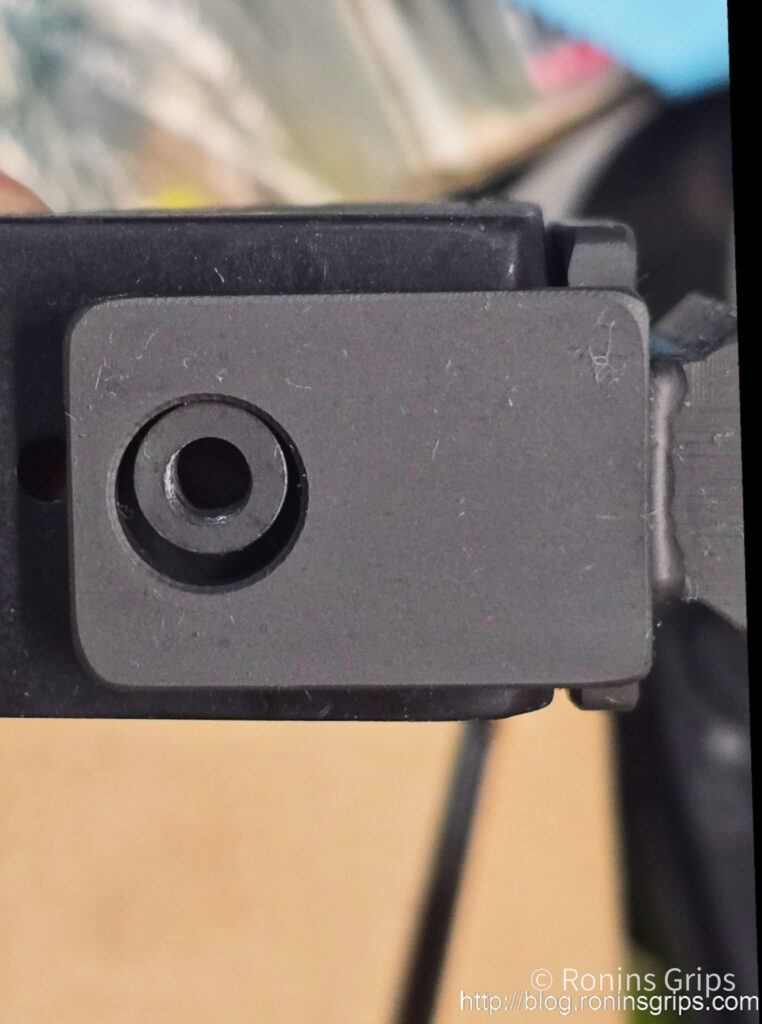
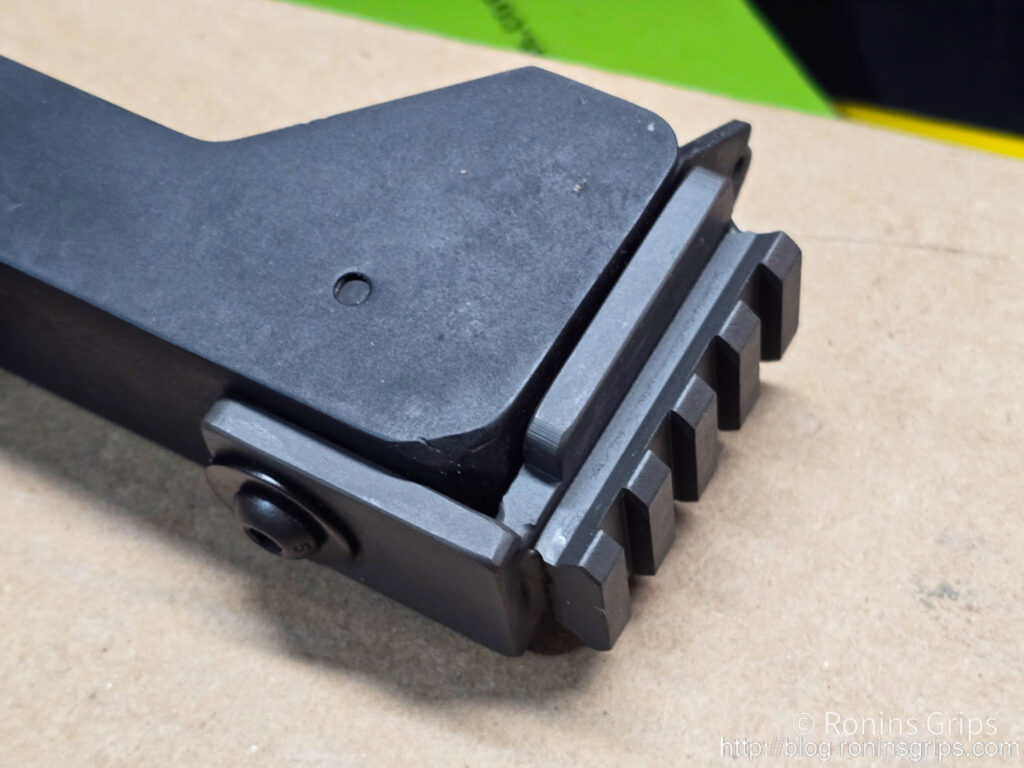
Now, I did experiment and had two braces on each of the pistols and one stock on the carbine. They all acted like lever arms and I could easily get their mounts to turn. Let me show you what they looked like:
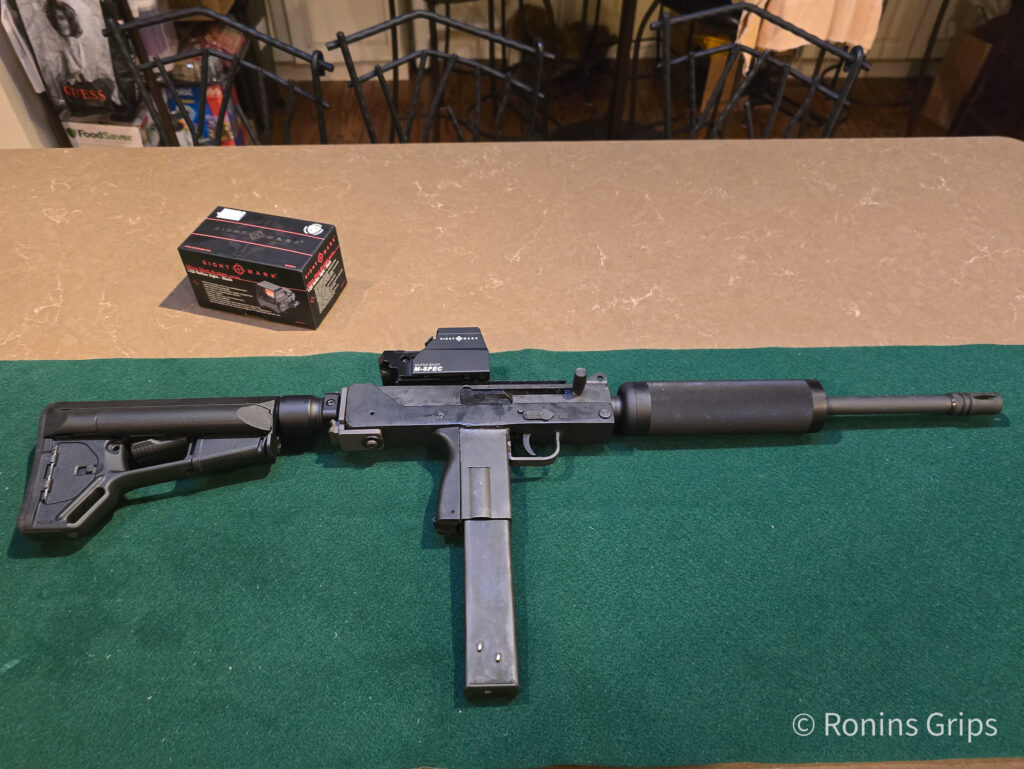
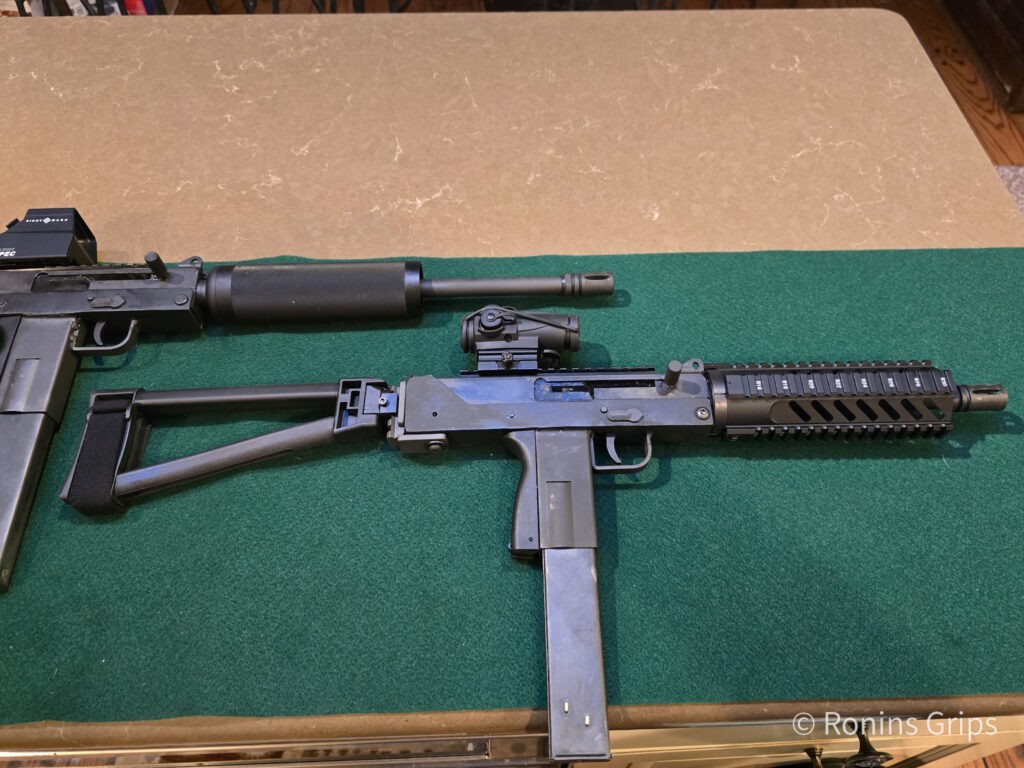
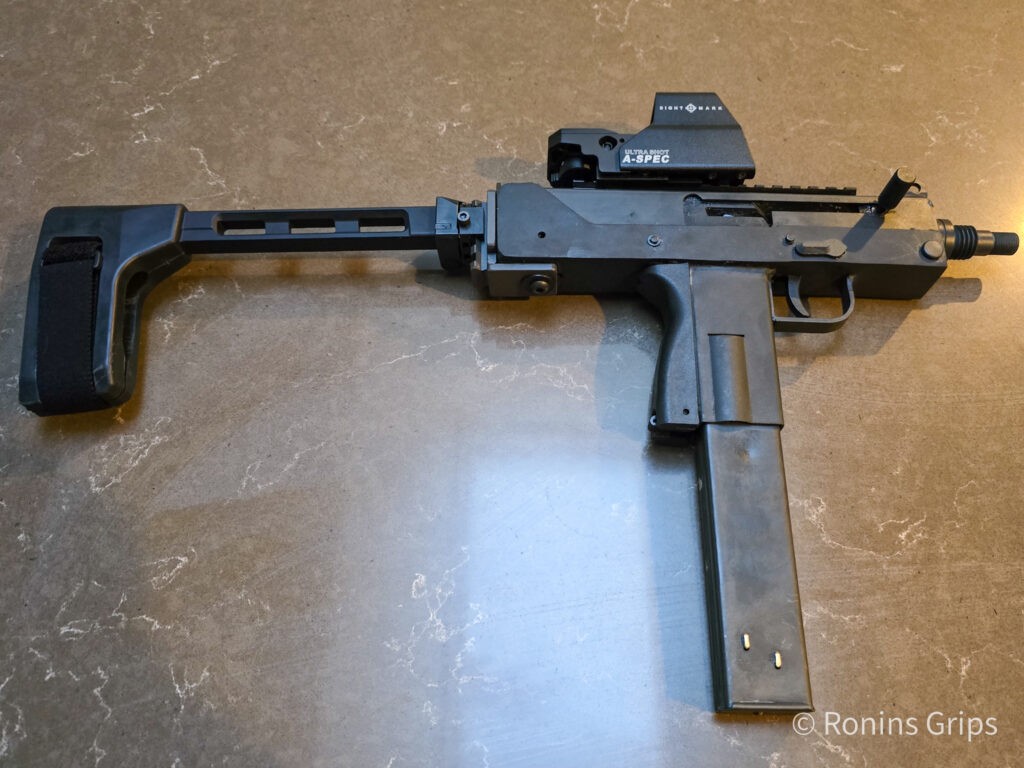
The Solution
I knew the primary issue as the irregularly shaped receiver back. The way to fix it was to mix up glass reinforced epoxy and “bed” the adapter so it could sit flat.
A second decision was whether to make this nearly permanent by epoxing the adapter directly to the receiver. I decided against that – at least for now – in case I decide to change or repair something. This decision to make what would more or less be a gasket between the two meant that I would spray release agent on the surfaces so the epoxy would cure but not adhere to the parkerizing.
Purely FYI – parkerizing makes an ideal surface for weapons finishes and epoxy due to all of the “nooks and crannies” it creates. If you don’t use some form of release agent, the bond is stunningly good and will only come off with heat.
For general epoxy work lately, I’ve been using PC Products’ Super Epoxy translucent model 502 dispensed from a 50ml cartridge. Cartridge dispensers are a bit more expensive but boy are they convenient. To use a cartridge, you need a gun and then tips – you can get everything off Amazon very cost effectively.
They do sell a black epoxy but I’ve been using the translucent epoxy and can dye it the color I want. Despite the gimmicky sounding name, I’ve been using it for a little over a year now. The working time before it hardens is 15 minutes and mostly cures in 3-4 hours with a complete cure of 4-7 days. This stuff has proven itself for me for general use.
By the way, In general, I would recommend you stick with a known brand of epoxy and the longer it takes to cure, the better it tends to hold up over time. Fast 5-15 minute cure epoxies tend the break down over time when exposed to repeated shocks – sometimes called “sugaring” where you can see the epoxy breaking down into small pieces.
The Steps
- Apply the release agent to the receiver and adapter and let it dry. I use Mann’s Ease Release 200 – that’s what I use with the molds for my furniture also. If you read about release agents guys use when bedding rifle actions in stocks, you can see guys have used various forms of wax, etc.
- To make the bedding compound, I put the epoxy and 1/32″ milled glass fibers in a cup and sti. The glass fibers help to reinforce the epoxy. You don’t need a lot of glass fibers – maybe 25% of the volume. As you increase the volume of glass fibers, the thicker the material is. In this case, I really just want the fibers to reinforce the epoxy so I went with about 25%.
- To make it look decent, I added in black dye so it would blend in and not be so obvious.
- I thoroughly mixed everything.
- I apply the material using nitrile gloves and a plastic knife.
- Acetone can be used to clean up any extra exposed epoxy until it cures.
- Once everything is position correctly, I tightened down the screw on the bottom and let it cure. made sure everything stayed positioned correctly and checked for any runs or drips. Again, stuff like that can be cleaned up with a rag with acetone on it until it sets up.
- Once the material has hardened, I put the part in a 150F degree oven to cure faster. With epoxy, hard to the touch does not mean fully cured.
The results seemed perfectly acceptable. If they loosen up again, then I’ll consider next steps. For now, they seem solid.
Summary
I like the Practical Solutions adapters. Bedding them made for solid connection points for braces of stocks.
Note, I have to buy all of my parts – nothing here was paid for by sponsors, etc. I do make a small amount if you click on an ad and buy something but that is it. You’re getting my real opinion on stuff.
If you find this post useful, please share the link on Facebook, with your friends, etc. Your support is much appreciated and if you have any feedback, please email me at in**@*********ps.com. Please note that for links to other websites, we are only paid if there is an affiliate program such as Avantlink, Impact, Amazon and eBay and only if you purchase something.