As I mentioned in my last post, IU ordered my GX CS3 air compressor off Amazon and it arrived in great shape. The next day, I reread the very terse instructions in the manual and decided I better follow some basic test procedures because you don’t want surprises with high pressure air (HPA) systems – think small explosion when they do. My intent was to bring the unit up in stages.
Current Version Does Not Require Additional Water or Grease
Unlike other pumps, you do not need to add water or oil/grease to this pump. You take it out of the box and run it. I even contacted the seller just to confirm because they still include the old instruction guide that says to add grease and the Amazon listing says you do not need to do so anymore. In short, it’s ready to go out of box.
Take the time to read the very brief owner’s guide/instructions. If the Amazon listing still says you do not need grease and there is no grease supplied, that part of the guide is outdated. You can still see what they say about testing, their exploded parts diagram, etc. |
Set up and Testing
Here’s what I did and would recommend to a new owner:
1. Make sure the AC power adapter’s input voltage switch is set accordingly.
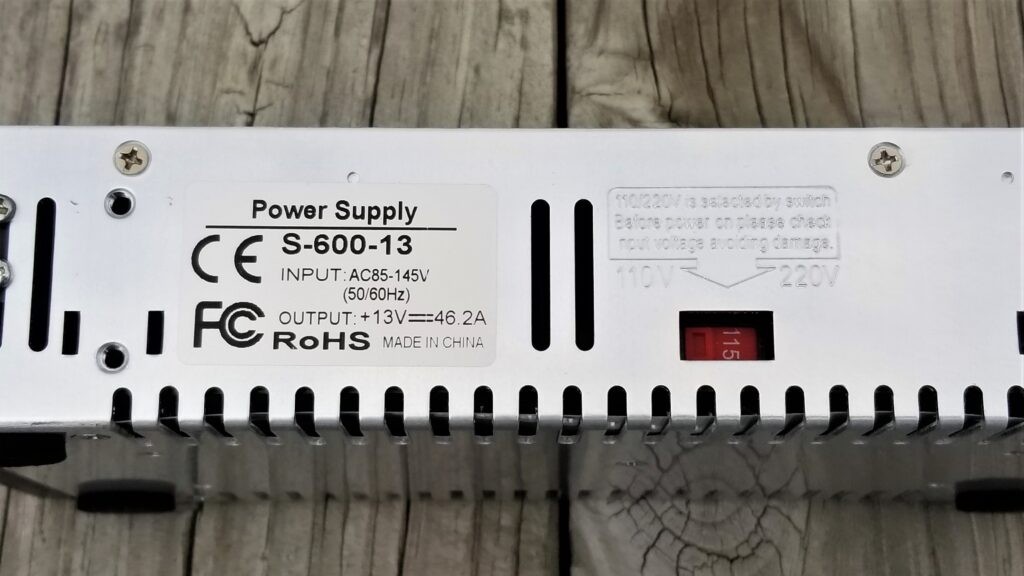
Do not plug it into the AC power yet. You need to connect the pump first.
2. Connect the pump’s power cables to the adapter.
First, I connected the power clamps to the AC adapter and then plugged the AC adapter into the wall. I debated testing the power to see if I was getting 12-13 volts but decided to just run with it. Note, there is no power switch on the adapter so connect the clamps from the pump to the compressor and then plug the power adapter into the wall.
Important: Connect the pump’s power leads to the AC adapter first before you plug it in. Also, mke absolutely sure the red power line is clamped to the red “+” terminal and the black line is to the white “-” terminal. Do not reverse the polarities. |
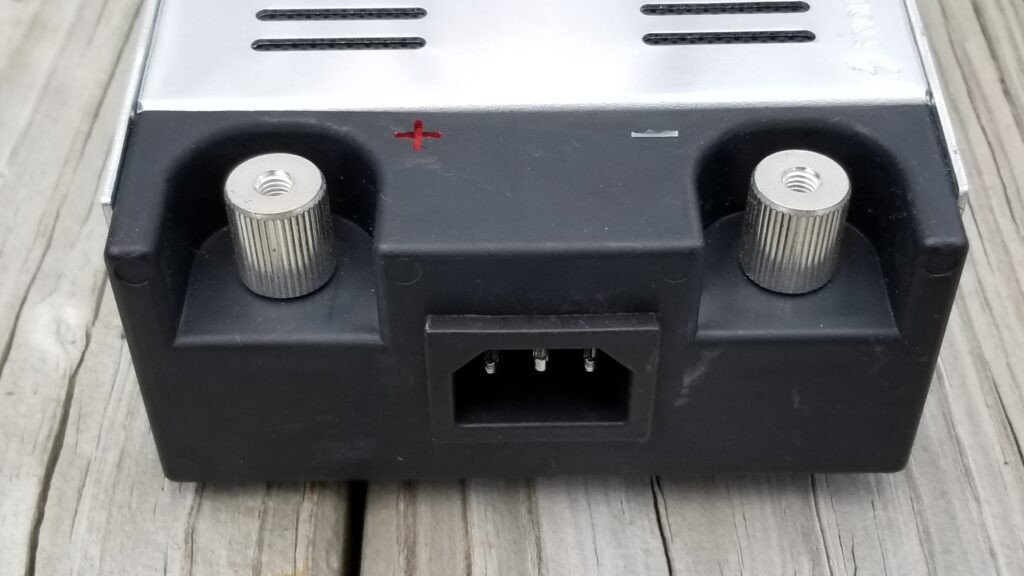
You can see the lower AC cord socket. This is your normal office plug so you have tons of cord options if you need to replace the cord down the road. There are also lots of AC adapters on the market with a very similar set up – just make sure they output 13V and and least 46.2 amps to support the compressor.
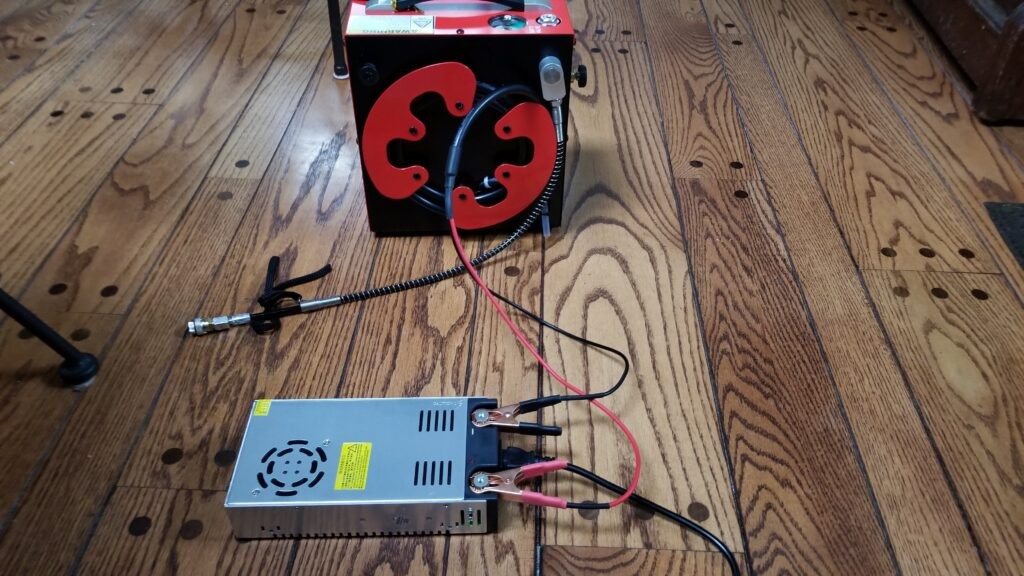
With the power adapter plugged into the wall, the cooling fan on top should start right away and that is how you know it is running. If it does not, use a test meter to check the AC power cord for 110-120 volts. If the cord is good then see if you have 12-13 volts at the terminals. You will need to contact the vendor as the fan is critical for cooling even if you do have power. If there is no output power then the vendor needs to replace the power adapter.
If the fan is running, let’s go to the next step.
3. Testing the pump and line
Set up really is that easy. At this point, it was time to turn on the pump and pressure test the line. To do this, the maker supplies a test Foster plug that goes into to supplied female Foster fitting.
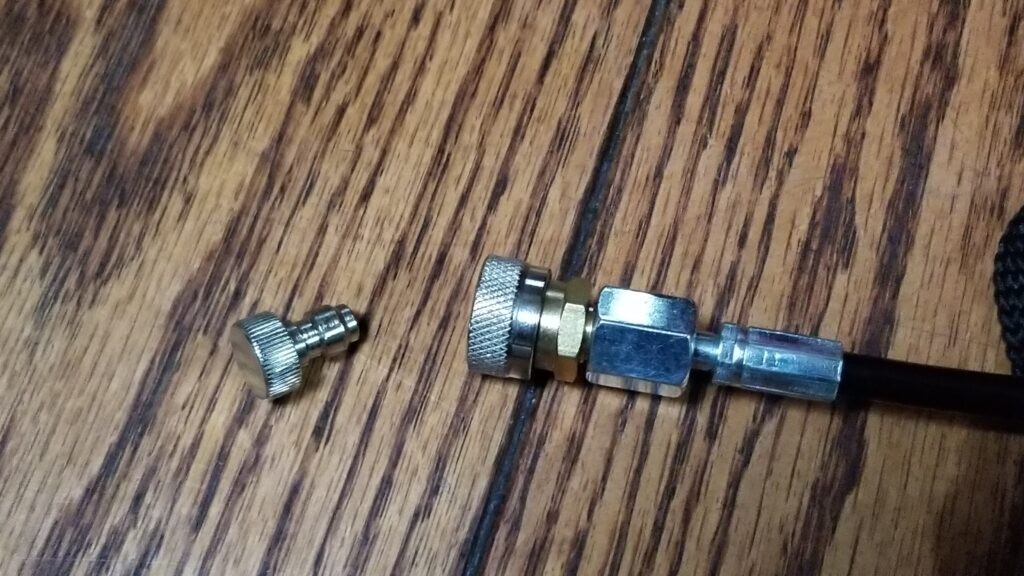
Note, my test plug came already installed in the end of those. In general, I like the idea of keeping the test plug inserted when the pump is not in use to help keep the fitting clean.
Two things, the quick connect fittings on HPA lines, tanks and guns is known as “Foster” fittings and you have the make plugs and female couplers with a locking ring you slide back to release the male plug. They are a really handy means to switch between filling different things – tanks, guns, certain types of fill probes, etc. Just make sure you get fittings that are rated for the pressure you need. For example, I’ll be filling tanks up to 4,500 PSI so my fittings are all rated for 5,000 PSI.
If you mix fittings between vendors, there’s a risk of a leak due to tolerances stacking the wrong way. In other words, vendor X and vendor Y might have slightly different allowances during machining and when you combine them, there is enough of a gap for air to leak out. With this in mind, I try to stick with Air Venturi brand fittings and if I have a problem, I swap out the fitting in question with one from that brand and I keep spares on hand just in case. Note, they can also wear out from repeated use as well – another good reason to have a few spares.
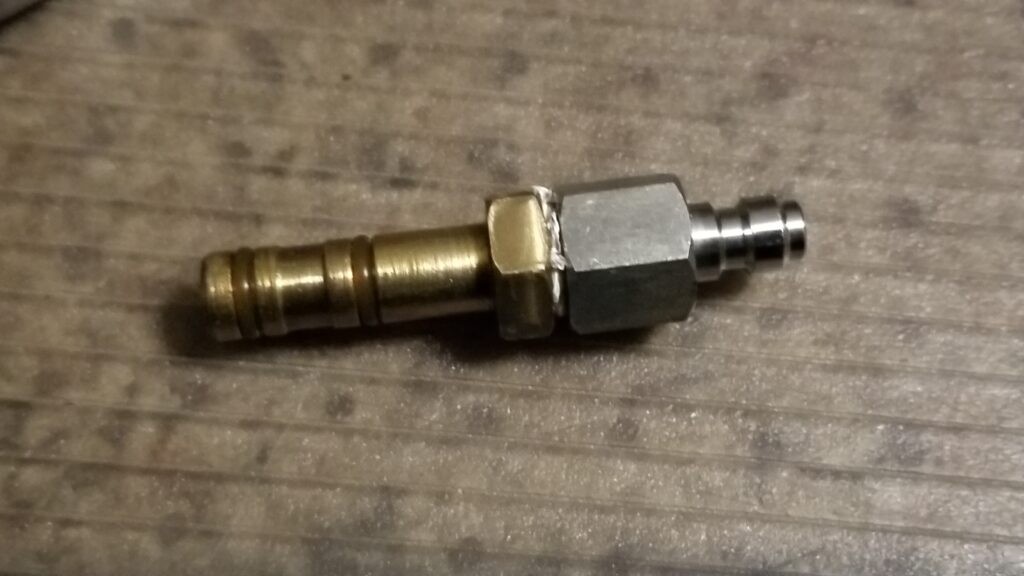
My Testing Procedure
I am paranoid. If something is going to break, I want it to happen with the lowest air pressure and volume of air behind it that I can get. Right now, we need to test the pump itself, the air line and fittings that came with tank.
WARNING: Never run your hand over a charged high pressure air line and fittings in search of leaks. You run the risk of injecting high pressure air into your blood and having an embolism. Either spray soapy water on the suspect and look for bubbles or even dip the area in soapy water. |
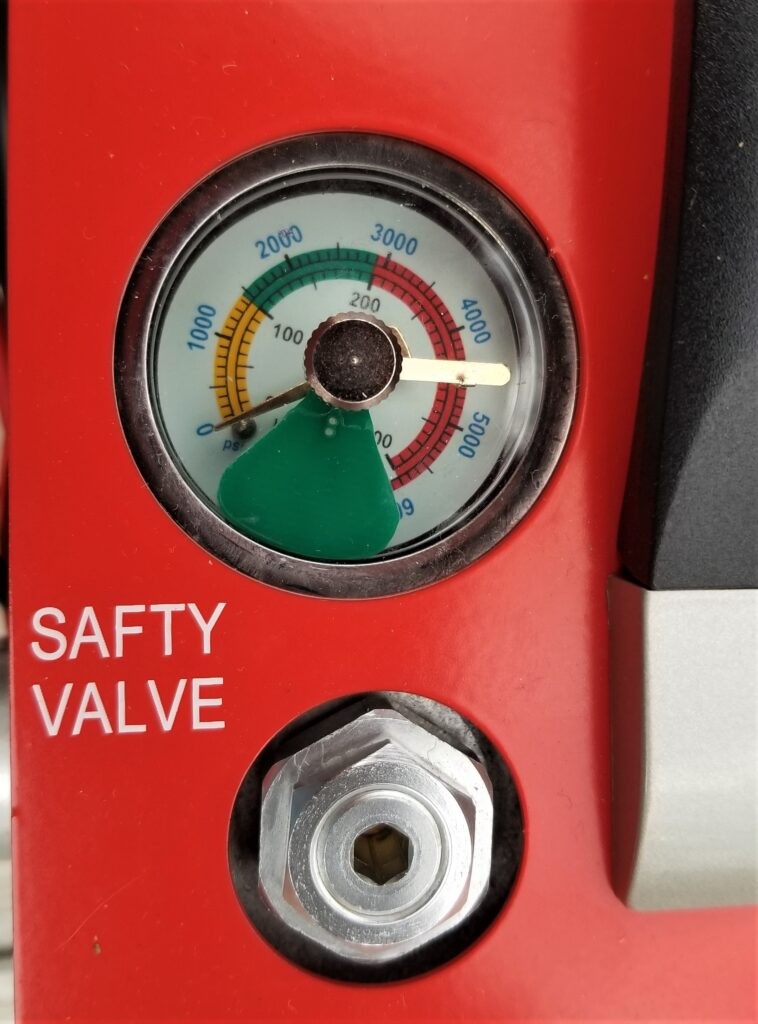
Here is what I did to test my pump and fittings and if you are not comfortable with any of it, please do not do it (safety first):
- Ensure the test fitting is installed in the end of the Foster fitting of the pump’s air line.
- Set the air pressure limit on top to 1,000 pounds.
- Flip the toggle switch as the base of the pump to On.
- Push the start button on the front of the pump. If it does not turn on, double check the power connections. You should also hear the relatively loud cooling fan turn on in the pump at the same time. If it will not turn on or you don’t hear the cooling fan once it does, you will need to contact your vendor. My fan turned on when I pushed the silver start button on the unit.
- The pump should start and in a few seconds pressurize the line to 1,000 PSI. If not, then contact the vendor.
- By the way, the pump better shut off at the assigned 1,000 PSI limit. If not then this is a serious safety concern and you should contact the vendor.
- With the pump off and the line charged, watch the pressure gauge for 30-60 seconds. If the pressure falls then that means there is a leak somewhere and you should contact the vendor. If it stays steady, go to the next step. If you want to wait for longer, you certainly can.
- Open the bleed valve and release the air pressure. Water from condensation may come out the drain tube on the side and that is fine. It may, it may not.
- Next, turn the dial up to 2,000 PSI and repeat the above test. We are increasing the pressure in steps testing the unit. You do not need to go higher than you plan to use the unit — stop where you want. For me, I am going up to 4,500 PSI for my carbon fiber tank so I drained and filled the line several times.
- Also, none of these incremental tests should take more than 10-15 seconds to complete.
- Do it again at 3,000 PSI.
- Do it again at 4,000 PSI.
- Do it one last time at 4,500 PSI.
I’m happy to say that my new pump system passed all the tests!
If you run into any problems with the above, contact the vendor. You do not want to void your warranty or get hurt so don’t go taking things apart – talk to the vendor first. I can’t stress that enough. HPA systems require knowledge to service safely and you will probably be far better off exchanging for a whole new pump vs. taking things apart.
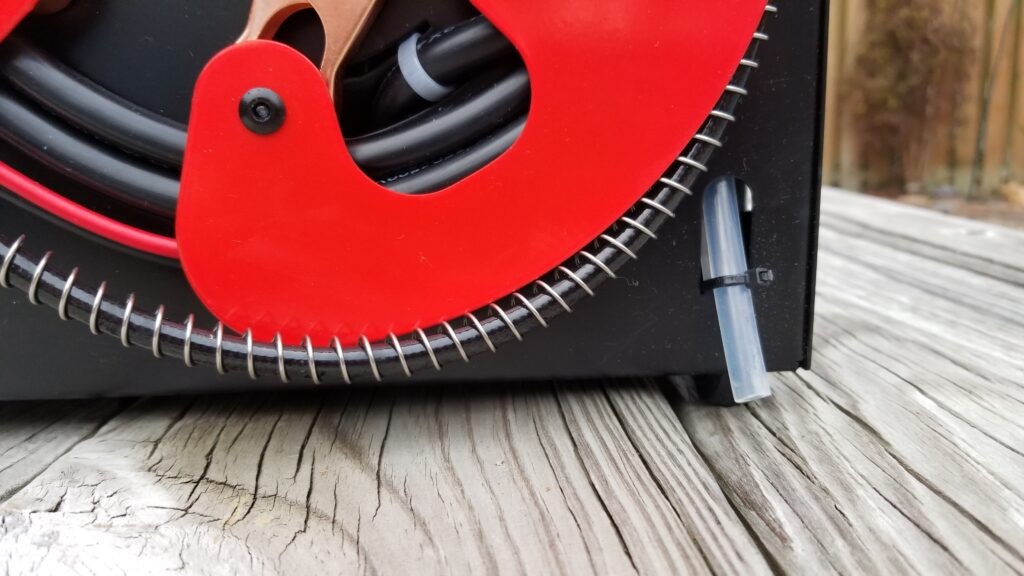
Duty Cycle
Please note that this compressor has a duty cycle that you must keep in mind. It is designed to run for up to 30 minutes straight and then it needs to cool for 20 minutes. Leave the unit powered on so the fan can help cool it off. So, if you have a big tank to fill, keep this in mind. You can fill it but do so in however many steps you need to honor this duty cycle.
Video Of It Running
I’m going to put this video both here and in the introductory blog post. Today, I recorded a quick video as I topped off my tank today – January 7, 2022. It ran for about 20 minutes as I took that tank from about 3,000 to 4,500 PSI.
When done, I let the unit’s fan run for about 10 minutes until the air coming out was cool again. Since the unit is air cooled, give it time for the fan to do just that. I also bled off the unit to replace air pressure and get rid of any condensation.
Note the odd double filter rig I am running in the video – that’s just because the double-male Foster fitting will not seat all the way in the big filter’s female fitting. I need to replace it with an Air Venturi brand fitting some day when I have time.
Safety comment: Never try to force fittings apart after a fill. Most likely there is high pressure air that needs to be bled out of the lines. With that big inline filter, the output side from it to the tank stays under pressure so I need to bleed down both the compressor and tank sides before I can safely disconnect the various fittings. Just remember to think things through carefully before you force a fitting off – high pressure air dangerous.
Conclusion
Hopefully your system passed the tests and you are now ready to fill your tank or device. If you had problems, be sure to reach out to the vendor and ask questions. I found them both helpful and responsive.
I hope you found this post useful.
Here are the GX compressors from the CS4 down to the CS1
- GX CS4 – 6.8L tanks, fluid cooled, longer run time, 5800 PSI/40Mpa – External 12 volt power supply [My current compressor]
- GX CS3 – 1 liter tanks, air cooled, 4500 PSI/30Mpa – External 12 volt power supply [I used this and now my friend has it]
- GX CS3-I – 1 liter tanks, air cooled, 4500 PSI/30Mpa – Internal power supply [I used the regular CS3 but they are the same other than the power supply]
- GX CS2 – .5 liter tanks, air cooled, 4500PSI/30Mpa – 12 volt or 110 AC [I have not used this one]
- GX CS1-I – .5 liter tank, air cooled, , 4500PSI/30Mpa, 12 volt or 110AC internal power supply [I have not used this one]
- FastToBuy 30Mpa Oil Water Filter – Not a GX product but I recommend this filter and you need one between the compressor and your tank or PCP airgun. You will need an extra hose from it to your tank or airgun plus the proper fittings.
2/2/2021 Update: The compressor is still working great. No problems at all!
Note, I have to buy all of my parts – nothing here was paid for by sponsors, etc. I do make a small amount if you click on an ad and buy something but that is it. You’re getting my real opinion on stuff.
If you find this post useful, please share the link on Facebook, with your friends, etc. Your support is much appreciated and if you have any feedback, please email me at in**@*********ps.com. Please note that for links to other websites, we are only paid if there is an affiliate program such as Avantlink, Impact, Amazon and eBay and only if you purchase something. If you’d like to directly donate to help fund our continued report, please visit our donations page.